Feb 4 2002
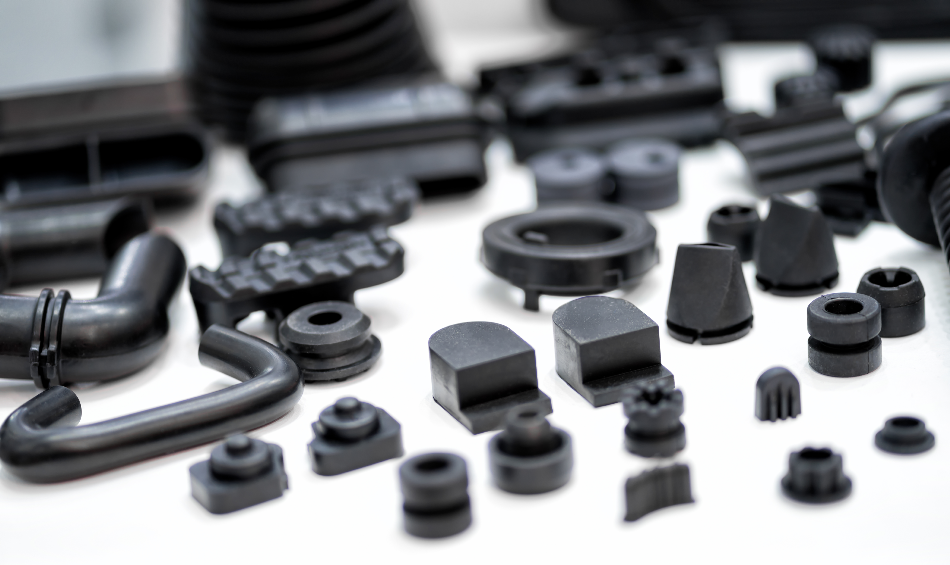
oYOo / Shutterstock
Rubber and plastics have become an integral part of modern life, without which humans cannot live. These materials are used in shoe soles, garden chairs, all types of films, DVDs, CDs, tubes, hoses, tires, packaging, and a host of many other products.
Keeping track of advanced plastics technology means individuals would need to be familiar with names—like polyoxymethylene, polypropylene, nitrile rubber, polyurethane, etc.—that can leave them considerably confused. However, in a majority of the cases, the excellent properties of valuable plastics utilized in all these effective applications are not exclusively tied to the polymers themselves.
Just like a brilliant student who achieves good grades at school, plastics also reached the top of their class with a slight amount of extra help. And that help usually means merely combining unique additives to make polymers that are soft, flexible, and resistant to impact and weather. Mostly, additives are the ones that make the plastic what it is.
Plasticizers
Plasticizers are unique types of additives. For instance, without plasticizers, PVC would have been extremely fragile and brittle, and would not have conquered the huge market as seen today. Without plasticizers, a majority of the injection molding compounds would have been completely unfit for that purpose, and certain blends of rubber would not have been produced at all.
Plasticizers make plastics elastic, extensible, flexible, and plastic at low temperatures. In a majority of the cases, polymer products can be produced only on a commercial basis by integrating a plasticizer.
As a matter of fact, the invention of plasticizers was mainly responsible for the development of the plastics industry. If it were not for this, the industry may not have developed much beyond the stage it was in the earlier days. This is because the first plastics, as well as modified natural polymers like Galalith or nitrocellulose, were brittle and hard, and hence they could not be used for daily applications.
Most certainly, it does not exactly increase the marketability of a novel material, if, for instance, people have to look after their combs as if they were made of Meissen porcelain.
Camphor
However, plasticizers changed all that. Camphor was the first one to be utilized in real plastics. It is a colorless substance, whose fragrance is reminiscent of many a cold remedy, and contains tiny crystals obtained from the wood of a Chinese laurel bush called Cinnamomum camphora.
Then, in 1869, an inventor called John Wesley Hyatt and his brother made nitrocellulose more malleable, by mixing camphor with nitrocellulose.
Other Oils
Hyatt was not the first person who tried to make the early brittle products of an evolving plastics sector easier to handle via the use of additives. An equally ambitious inventor named Alexander Parkes had already attempted to get the same effect using vegetable oils or wood tar, for instance.
However, he did face difficulties in obtaining the right recipe—his “Parkesin” was moderately easy to process, but after only a few weeks, items like ladies’ bracelets, combs, and earrings that had been produced from this specific product would warp to such as extent that they could not be used any longer. This was probably because oils used by Parkes evaporated too rapidly.
Banana oil or even fusel oil—that is formed during the distillation of whiskey—was also used by other inventors but without much success, if the dearth of records is anything to go by.
Soft as Chewing Gum yet Hard as Horn
The new plastic developed by Hyatt was better equipped to fulfill the challenges presented by the recently emerging plastics business. Based on the amount of camphor that he combined with collodion—a solution of gun cotton, known chemically as nitrocellulose—he successfully created a plastic. This plastic was transparent but could be colored. It was as flexible as crude rubber but was as hard as horn. This plastic was celluloid.
At a moderate temperature of between 80 °C and 90 °C, this malleable material could be produced in any required shape due to Hyatt’s fragrant formulation. One of the very first uses of this material was false teeth. However, it smelt more than a little amount of camphor and, as a result, did not always meet the complete satisfaction of their owners. However, since the material could be created in a suitable color, there was a significant enhancement on the tough rubber plates that had been used up until then. Afterward, the same material became popular as the perfect backing material for photographic films.
Origin of Modern Plastics
It is a fact that for some time, the celluloid developed by Hyatt had to overcome numerous challenges caused by its close association with gun cotton. Tiny explosions occurred when billiard balls composed of nitrocellulose crashed with each other. According to eyewitnesses, the explosions were so huge that it would make cowboys standing around the pool table to reach for their guns.
One magazine article also cited the story of a lady whose evening became even more exciting when the celluloid buttons pinned on her evening gown came very close to a fireplace and ignited. On one occasion, a whole celluloid factory exploded. However, these incidents did not conceal the fact that Hyatt had developed the first thermoplastic, and that it was a plasticizer instrumental in leading to the plastics of today.
But even after Hyatt, the history of plastics continued to be closely associated with that of its plasticizers. Then in 1946, an application for several hundred tons of a fragile cellulose triacetate plastic was being pursued. This plastic had been utilized, amongst other things, in the manufacture of aircraft windows.
The plastic was lying unused in a factory’s grounds, which was when a creative chemist had the idea of integrating the material with a plasticizer. This resulted in a novel injection molding material. In 1952, the recently plasticized Cellit was called “Cellidor” and was the perfect embodiment of versatility. In the 1950s, Cellidor was utilized to make casings for combs, dashboards, radios, spectacle frames, screwdriver handles, hair slides, etc.
Plasticizers in Rubber
The rubber industry also used plasticizers to refine its products. Extensive kneading makes unvulcanized rubber as soft as chewing gum because the kneading process breaks down the polymer’s long-chain molecules. But this means that other major characteristics of this useful material are also lost.
Due to this reason, rubber investigators made an early start by combining all types of liquid components into their black formulations—oils, pitch, coal tar, paraffin, terpenes (like camphor), and even Vaseline. This meant that the mixture of crude rubber was sufficiently sticky for various solid ingredients even when the size of the rubber molecules is not reduced considerably. Carbon black is an example of a solid ingredient that can be effortlessly kneaded together in the mixer.
These factors demonstrate the importance of these unobtrusive plasticizers with respect to polymer processing—and how they can completely transform the characteristics of what was originally a relatively unappealing polymer material. Paradoxically, this extraordinary power also demonstrates the fact that even eminent chemical historians are currently finding it difficult to acquire information regarding plasticizer technology.
The “right” plasticizers are significant to such an extent, that information gathered about the performance of plastic over the years has vanished into the vaults of firms utilizing polymers. As time passed, this meant that plasticizers became relatively anonymous utilitarian substances.
The Modern-Day Descendants of Camphor
However, it is a known fact that apart from Hyatt, others also began to use camphor. Indeed, two-thirds of all camphor synthesized across the world is used for producing celluloid even today.
A 1931 chemistry encyclopedia with the chapter titled “plasticizers” also listed terpene, in addition to glycerol esters, phthalates, and organic phosphates like tricresyl phosphate.
These compounds make plastics flexible and also improve their fire-retardant potential to such an extent that cellulose acetate, a successor to celluloid, was able to overcome one of the main drawbacks of the original plastic. For example, the plastic’s flammability was prevented after it was elastified with a combination of phosphates and camphor.
Advanced technology knows about 400 substances—that is, exotic substances and “worldbeaters”—that are utilized as plasticizers in one form or another. Around 100 of these substances have major commercial value.
Plasticizer Quantities
In the mid-1990s, over 4.2 million metric tons of plasticizers were being utilized. Today, about 90% of all plasticizers are utilized in PVC—a plastic which, in its basic form, is virtually as fragile as glass and would be completely useless for a majority of applications if plasticizers did not account for around 55% of its content. Even rigid PVC can have around 12% plasticizers that are known to enhance its processability.
Based on the type of application, other polymers utilize plasticizers in many different quantities. Paper contains about 5% of plasticizers, thermoplastic materials up to 10%, and elastomers at times as much as 60%; certain plastics also have 95% of plasticizers.
How Plasticizers Work
Essentially, all plasticizers are based on the same principle and one that is practically self-explanatory, provided individuals can understand what plastics are composed of in the inside. “Plastic” invariably contains very long-chain molecules that appear like long threads under extremely high magnification. A plastic becomes flexible when these threads are loosely intertwined together.
However, in the case of a majority of plastics, these threads tend to lie on top of each other just like packed spaghetti. In fact, when someone casually throws spaghetti into a pan without stirring it while it cooks, and later sieves it, apart from pasta strands loosely tangled together, there will also be areas where the pasta strands are still attached together as they were in the bag. Such lumps appear slightly harder than the rest, albeit the pasta itself is completely cooked and soft.
A similar thing occurs with respect to the chain molecules of plastics. A stiff structure analogous to the strictly regular composition crystals enables the plastic to look stiff from the outer side. Both in the test tube and in the pan, the rule is as follows: the rigid structure is hard and loosely tangled is flexible.
Chemistry
This is where the plasticizers have a role to play. In most of the cases, regardless of whether mineral oil or camphor is being discussed, the molecules are relatively smaller than the chain molecules of the polymer material. They are interlaced into their spaghetti-like structure when processing the plastic.
These molecules subsequently push their way between the neighboring threads of plastic molecules and set them apart from each other. They act in the same manner as oil does on a plate of spaghetti, where it enables the pasta strands to slide past each other. This suggests that it is possible to produce a loose and freely mobile structure—the plastic turns out to be flexible and when more plasticizer is added, it becomes even more flexible. This simple correlation elucidates an entire range of products that is essential for a plastics chemist’s job.
To a great extent, the expertise of a materials developer lies in being able to identify substances that are well suited to the plastic being utilized. It is not possible to interweave hydrophilic substances into water-repellent molecules, for example, those of unvulcanized rubber, as both substances would separate just like oil and water.
It is also crucial to choose a plasticizer that offers an ideal fit with regard to its own molecular configuration and the target plastic chain molecules. Chain molecules are not as comparable to one another as the spaghetti strands—certain polymers can resemble flat pasta, while others seem like a chain of thick neon tubes linked together with thin wires, or have a zig-zag appearance. Yet others seem like necklaces made of extreme fat pearls. Nevertheless, Hyatt’s celluloid was the one that attained the success it did. This is because the camphor molecules fitted quite well between the gun cotton molecules that were molded like a pearl necklace.
However, not all plasticizers are appropriate for every polymer. Another fact is that each plasticizer has a different impact on its “host molecule.” While one plasticizer offers a greater level of flexibility at lower temperatures, another is specifically developed to prevent plastics from liquidizing at high temperatures. Meanwhile, there are other plasticizers that make plastics more flexible and also behave as a kind of integrated fire extinguisher that can put out flames in their very initial stages. The plasticizers accomplish this by decomposing in the presence of heat to create substances that are resistant to flames.
One Problem—Many Solutions
Over the years, the plastics sector’s order book for plasticizers has developed into an unorganized agglomeration of chemicals. However, it is governed by several “major families” of products.
Phthalates are employed in PVC films and cables, cellulose adhesives, and coatings. With dicarbonates, flexible PVC becomes elastic at low temperatures. Phosphates are utilized both as a hydraulic fluid and as a flame-retardant. Fatty acid esters—the distant relatives of margarine—are used for plasticizing rubber and vinyl resin floor coverings. For some applications, plastics technologists also turn to esters of tartaric acid and citric acid.
Dangers
Most certainly, it should be remembered that in spite of the beneficial effect of plasticizers on plastics technology, they also have their drawbacks. In the recent past, it was suspected that phthalates are harmful to health. While conclusive evidence is yet to be obtained, studies are now ongoing.
Luckily, regardless of the result of this discussion, by no means it implies that all plasticizers should be condemned: after all, a single plasticizer is not the same as the next, as demonstrated by camphor, which happens to be a natural product.
Alternatives
Meanwhile, some highly useful products have been created that serves as a substitute for phthalates. Products like these take the form of a series of substances whose members are called “alkyl sulfonates.” It was known for a long time that alkyl sulfonates have no adverse effects, and have been approved as being safe for food use in a majority of the countries.
Alkyl sulfonates, which are already used in the place of the controversial phthalates in gloves, toy figurines, dolls, and membranes for water beds, can be found in sealants in the construction sector, and are used in wellington boots and swimming aids. In addition, the material provides a complete range of additional benefits—for instance, it is different from many other plasticizers and is not attacked by water and elements, and it also results in products that are conducive to printing. This is a significant factor when it comes to creating vividly colored children’s paddling pools produced from PVC film, among other things.
The raw form of PVC is fragile, virtually glass-like plastic that would be almost useless if it were not for plasticizers. Alkyl sulfonates make the PVC elastic and resistant to saponification and weather.
Drifting Plasticizer Molecules
Recently, industry researchers have come up with a solution to the issue of drifting plasticizer molecules. The minute particles of plasticizers held within the plastics are incredibly mobile. Under specific circumstances, the particles move around just like honey in a sponge. Within the plastic, the movement of certain plasticizer molecules comes to an end sooner or later when they reach the surface and create an unattractive greasy film.
Housewives are not the only ones who know this fact. Unique plasticizers that have been trained to stay in one place inside the polymer—for instance, by providing them long-chain molecules—can prevent rubber and plastic from developing a greasy or dulled surface.
Furthermore, researchers have created custom-made halogen-free plasticizers for electronic circuit boards, so that the fragile plastic used to produce them does not break when the boards are drilled, punched, and soldered.
Growth and Development of Industry
The plasticizer sector is largely involved with conventional products. While it is quite unusual to devote so much effort to product development, it definitely pays off.
Over the past two years, the plastics market achieved a growth of just 4%, but despite this fact, the sales of certain specialist plasticizers increased by about 15%, in the same period. This figure alone is sufficient to show that the last chapter in the long history of plasticizers has not been written yet: innovative plastics and the latest demands placed on the products that are constantly made from them need novel solutions. Here, only the collective brainpower of plastics experts can do justice to these.
Natural Plasticizers
However, coming back to plasticizers, the plasticizing chemicals emerging from crucibles and flasks of the chemical sector are not the sole ones that occur in the world at large. Since nature also partly contains polymers, it also needs substances to make sure that these polymers continue to be flexible.
Starches, DNA, proteins, wood, and even stones essentially contain long and at times spatially interconnected chain molecules. Nature uses water as the main plasticizer. Natural fibers like cotton, wool, or silk will be fragile without their water content.
Moreover, excess water keeps muscular proteins flexible. In advanced age, water content reduces, while fats more or less play the role of a plasticizer successfully. The plastics industry is not the only one that relies on plasticizers, but even mother nature cannot manage without them. Muscle fibers are composed of chain molecules similar to those found in plastics. Just like contemporary polymers, muscle fibers contain their own plasticizers in the form of fat molecules and water.
Also, water can be used to soften quartz, which is known to be a very hard material—while hard, natural quartz contains just 0.01% water, for technical reasons, artificial quartz contains about 10 times that amount. Artificial quartz can be molded similar to plaster at 400 °C—a temperature that can be easily tolerated by minerals—while “dry” natural quartz plainly remains “rock solid” up to a temperature of 1000 °C.
This is an excellent example of the fact that the use of plasticizers in technology is not necessarily limited to plastics. Individuals who think hard about the curved handle of their umbrellas would know that some kind of procedure is used to make the wood flexible.
Hot water vapor can indeed be used to soften the wood, but liquid ammonia, when mixed with organic solvents like tetrahydrofuran, dimethyl sulfoxide, or polyethylene glycol, does the job even better. A specific formulation like this even enables individuals to tie knots in walking sticks. After the evaporation of ammonia, the wood comes back to the original state—that is, its freshly cut state.
Emerging from the Plastics Middle Ages
Over a hundred years ago, plastics came to be known through Hyatt’s invention. Hence, it is not surprising that professions that have so far been associated with the preservation of antique pigments are now coming to terms with plasticizer issues. For instance, restorers are presently fighting to sustain the spacesuits that were worn by the Apollo astronauts on the moon and came to Earth undamaged.
Those spacesuits contained PVC tubes that had been plasticized with the help of a phthalate. After spending over three decades in a museum, this liquid substance has diffused out of the polymer, in a way that is typical of all drifting plasticizers. As a result, the supply tubes have become brittle. What was once believed to be the pinnacle in spacesuit technology has now become less durable when compared to knights’ harnesses that are hundreds of years old. Looking at things from this standpoint, it can thus be concluded that humans are still in the so-called Middle Ages of plastics technology.