The fabrication of titanium product forms into complex shapes is routine for many fabricators. These shops recognized long ago that titanium is not an exotic material requiring elaborate fabrication techniques. This article will discuss the creation of good welds and effective heat treatments of titanium.
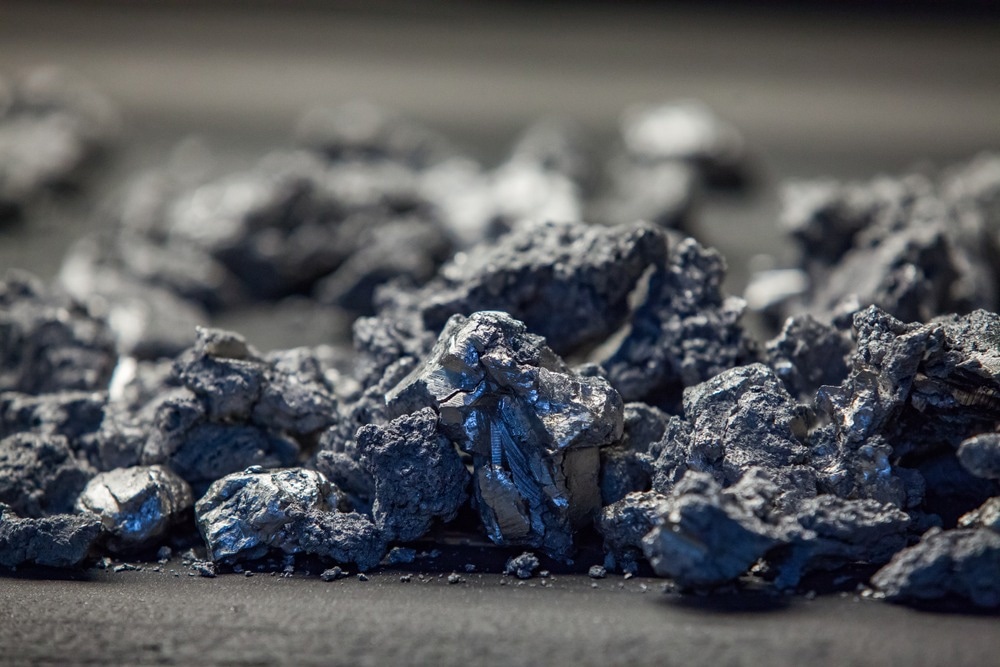
Image Credit: rezoff/Shutterstock.com
Important differences between titanium and steel or nickel-base alloys need to be recognized. These are:
• Titanium’s lower density
• Titanium’s lower modulus of elasticity
• Titanium’s higher melting point
• Titanium’s lower ductility
• Titanium’s propensity to gall
• Titanium’s sensitivity toward contamination during welding
Compensation for these differences allows titanium to be fabricated using techniques similar to those with stainless steel or nickel-based alloys. This article deals with common operations used in fabricating titanium.
Work Area
The fabrication of titanium demands attention to cleanliness. It is not uncommon for shops that handle several metals to isolate an area to be used especially for titanium. The area set aside for titanium should be free of air drafts, moisture, dust, grease, and other contaminants which might find their way into or onto the metal.
Welding Titanium
Titanium and most titanium alloys are readily weldable, using several welding processes. Properly made welds in the as-welded condition are ductile and, in most environments, are as corrosion resistant as the base metal. Bad welds, on the other hand, might be embrittled and less corrosion-resistant compared to a base metal.
The techniques and equipment used in welding titanium are similar to those required for other high-performance materials, such as stainless steel or nickel-base alloys. Titanium, however, demands greater attention to cleanliness and to the use of auxiliary inert gas shielding than these materials. Molten titanium weld metal must be totally protected from contamination by air. Also, hot heat-affected zones and the root side of titanium welds must be shielded until temperatures drop below 800°F (427°C).
Titanium reacts readily with air, moisture, grease, dirt, refractories, and most other metals to form brittle compounds. The reaction of titanium with gases and fluxes makes common welding processes such as gas welding, shielded metal arc, flux cored arc, and submerged arc welding unsuitable. Likewise, welding titanium to most dissimilar metals is not feasible, because titanium forms brittle compounds with most other metals; however, titanium can be welded to zirconium, tantalum, and niobium.
In spite of the precautions, many fabricators are routinely and economically welding titanium, making sound, ductile welds at comparable rates to many other high-performance materials. One of the important benefits of welding the commercially pure grades of titanium is that they are over 99% pure titanium and there is no concern for segregation. The same is true of weld wire or rod in commercially pure grades.
Welding Processes
Titanium and its alloys are most often welded with the gas tungsten-arc (GTA or TIG) and gas metal-arc (GMA or MIG) welding processes. Resistance, plasma arc, electron beam and friction welding are also used on titanium to a limited extent. All of these processes offer advantages for specific situations. However, the following discussion will be concerned primarily with GTA and GMA welding. Many of the principles discussed are applicable to all processes.
Types of Welding: Gas Tungsten-Arc (GTA) and Gas Metal-Arc (GMA)
The GTA process can be used to make butt joints without filler metal in titanium base sheet of up to about 1/8-inch thickness. Heavier sections generally require the use of filler metal and grooved joints. Either the GTA or GMA welding process can be used, although GMA welding is more economical for sections heavier than about one-half inch. If the GTA process is used, care should be exercised to prevent contact of the tungsten electrode with the molten puddle, thereby preventing tungsten pickup.
Power Supply
A conventional power supply, connected to D.C. straight polarity (DCSP), is used for GTA welding of titanium. Reverse polarity (DCRP) is used for GMA welding of titanium. A remote-controlled contactor allows the arc to be broken without removal of the torch from the cooling weld metal, thereby maintaining inert gas shielding. Foot-operated current and contactor control, high-frequency arc starting, and shielding gas timers are other desirable features.
Welding Torch
A water-cooled welding torch, equipped with a 3/4-inch ceramic cup and a gas lens, is recommended for GTA welding of titanium. A one-inch cup may be required for GMA welding. Thoriated tungsten electrodes (usually 2% thoria) are recommended for GTA welding of titanium. Pointed electrodes (end blunted) help to control arc characteristics. The smallest diameter electrode which can carry the required current should be used.
Inert Gas Shielding
Protection needs to be provided to titanium weldments on cooling down to about 800°F (427°C) as well as to the molten weld puddle in order to prevent contamination by air. During GTA and GMA welding, argon or helium shielding gases of welding grade with dewpoint of -50°F (-46°C) or lower are used to provide the necessary protection. Separate gas supplies are needed for:
• Primary shielding of the molten weld puddle.
• Secondary shielding of cooling weld deposit and associated heat-affected zones.
• Backup shielding of the backside of weld and associated heat-affected zones.
Primary Shielding
Primary shielding of the molten weld puddle is provided by proper selection of the welding torch. Standard water-cooled welding torches equipped with large (3/4 or 1-inch) ceramic cups and gas lenses are suitable for titanium. The large cup is necessary to provide adequate shielding for the entire molten weld puddle. The gas lens provides uniform, nonturbulent inert gas flow.
Argon is generally used in preference to helium for primary shielding at the torch because of better arc stability characteristics. Argon-helium mixtures can be used if a higher voltage, hotter arc, and greater penetration are desired. The manufacturer’s recommended gas flow rates to the torch should be used.
Flow rates in the vicinity of 20 cfh have proven satisfactory in practice. Excess flow to the torch may cause turbulence and loss of shielding. The effectiveness of primary shielding should be evaluated prior to production welding. An arc can be struck on a scrap piece of titanium with the torch held still and with shielding gas only on the torch. The shielding gas should be continued after a molten puddle forms and the arc is extinguished until the weld cools. Uncontaminated, i.e., properly shielded, welds will be bright and silvery in appearance.
Secondary Shielding
Secondary shielding is most commonly provided by trailing shields. The function of the trailing shield is to protect the solidified titanium weld metal and associated heat-affected zones until the temperature reaches 800°F (427°C) or lower. Trailing shields are generally custom-made to fit a particular torch and a particular welding operation.
Design of the trailing shield should be compact and allow for uniform distribution of inert gas within the device. The possible need for water-cooling should also be considered, particularly for large shields. Porous bronze diffusers have provided an even and nonturbulent flow of inert gas from the shield to the weld.
Backup Shielding
The prime purpose of backup devices is to provide inert gas shielding to the root side of welds and their heat-affected zones. Such devices often look much like trailing shields and may be hand-held, clamped, or taped into position. Water-cooled copper backup bars (or massive metal bars) may also be used as heat sinks to chill the welds. These bars are grooved, with the groove located directly below (or above) the weld joint. About 10 cfh of inert gas flow per linear foot of groove is required for adequate shielding.
Makeshift shielding devices are often employed very effectively with titanium welds under shop or field conditions. These include the use of plastic to completely enclose the workpiece and flood it with inert gas. Likewise, aluminum or stainless steel foil “tents,” taped over welds and flooded with inert gas, are used as backup shields. When such techniques are used, it is important that all air, which will contaminate welds, be purged from the system. An inert gas purge equal to ten times the volume of the air removed is a good rule of thumb for irregular spaces. A moderate rate of inert gas should be maintained until the weld is completed.
Argon is generally selected in preference to helium for use in trailing shields and backup devices, primarily because of cost but also because it is denser. Helium, with its lower density, is sometimes used for trailing or backup shielding when the weld is above the device. It is important that separate flow controls are available for primary, secondary, and backup shielding devices. Timer-controlled pre-purge and post-purge torch shielding, and solenoid valves with manual switches interlocked with the welding current for secondary and backup shielding are also useful.
Joint Design and Preparation
Weld joint designs for titanium are similar to those for other metals. The joint design selected for titanium, however, must permit proper inert gas shielding of both root and face during welding as well as post-weld inspection of both sides of the weld. The joint surfaces must be smooth, clean, and completely free of contamination. All burn marks produced by grinding or mechanical filing should be removed by filing. Likewise, burrs and sharp edges should be removed with a sharp file.
The use of sandpaper or steel wool, which leave particles behind, can be a source of contamination. Good joint fit-up is important for titanium. Uniform fit-up minimizes burn-through and controls underbead contour. Poor fit-up may increase the possibility of contamination from air trapped in the joint, particularly with butt joints on light gauge material.
Maintenance of joint opening during welding is important. Clamping to prevent joint movement during welding is recommended. If tack welds are used, the same care in cleaning and inert gas shielding must be exercised, as with any and all titanium welds, to prevent contamination. Any cracked or contaminated tack welds must be removed before final welding.
Cleaning
Before welding titanium, it is important that weld joints and weld wire be free of mill scale, dirt, dust, grease, oil, moisture, and other potential contaminants. Inclusion of these foreign substances in titanium weld metal could degrade properties and corrosion resistance. Weld wire is clean as packaged by the manufacturer. If wire appears to be dirty, wiping with a non-chlorinated solvent, prior to use, is good practice. In severe cases, acid cleaning may be required.
All joint surfaces and surfaces of the base plate for a distance of at least an inch back from the joint need to be cleaned. Normal pickled mill surfaces generally require only scrubbing with household cleaners or detergents, followed by thorough rinsing with hot water and air drying. Alternatively, wiping weld joints and adjacent areas with nonchlorinated solvents such as acetone, toluene, or methyl ethyl ketone (MEK), using clean lint-free cloths or cellulose sponges, is acceptable, provided no residue remains.
The solvents are particularly effective in removing traces of grease and oil. Solvent cleaning should be followed by wire brushing, using a new stainless steel brush. Under no circumstances should steel brushes or steel wool be used on titanium because of the dangers to corrosion resistance that embedded iron particles pose.
Light oxide films, as might result from heating in the range 600°-800°F (316-427°) for forming operations, can be removed by brushing with a new stainless steel wire brush. Light grinding, draw filing and acid pickling are also effective. An acceptable pickle bath for titanium is 35 vol.% nitric (70% concentration), and 5 vol.% hydrofluoric acid (48% concentration) used at room temperature. Dipping of weld joint areas for 1 to 15 minutes (depending on the activity of the bath) should be sufficient.
A cold water rinse to remove acid, followed by a hot water rinse to facilitate drying, completes the cleaning. Heavy scale and oxygen-contaminated surfaces, such as might be present after a high-temperature heat treatment, are best removed by mechanical means. Grinding, and sand or grit blasting are commonly used. Molten caustic baths, although useful, require care to minimize the possibility of hydrogen pickup. After scale removal, an acid pickle should be used to remove all residue and improve surface appearance.
Once cleaned, joints should be carefully preserved. Handling should be minimized and welding should commence as soon after cleaning as possible. When not being worked on, weld joints should be kept covered with paper or plastic to avoid the accumulation of contaminants.
Filler Metal Selection
Titanium welding wire is covered by AWS A5.16-70 Specification (“Titanium and Titanium-Alloy Bare Welding Rods and Electrodes”). It is generally good practice to select a filler metal matching the properties and composition of the titanium base metal grade. However, for both commercially pure grades and alloys, selecting a welded wire one strength level below the base metal is also done. Special situations may require a different grade of filler wire to give the desired combination of joint properties.
Welding Technique
In addition to clean joints and weld wire, proper parameters, and proper inert gas shielding, the welder technique requires attention when titanium is being welded. Improper techniques can be a source of weld contamination. Before starting an arc in welding titanium, it is good practice to pre-purge the torch, trailing shield and backup shield to be sure all air is removed.
Whenever possible, high-frequency arc starting should be used. Scratch starting with tungsten electrodes is a source of tungsten inclusions in titanium welds. On extinguishing the arc, the use of current downslope and a contactor, controlled by a single foot pedal, is encouraged. Torch shielding should be continued until the weld metal cools below 800°F (427°C).
More from AZoM: Titanium and Titanium Alloys - Forming and Formability of Titanium and Titanium Alloys
Secondary and backup shielding should also be continued. A straw or blue color on the weld is indicative of premature removal of shielding gas. Preheating is not generally needed for titanium shop welds. However, if the presence of moisture is suspected, due to low temperature, high humidity, or a wet work area, preheating may be necessary. Gas torch heating (slightly oxidizing flame) of weld surfaces to about 150°F (66°) is generally sufficient to remove moisture.
The arc length for welding titanium without filler metal should be about equal to the electrode diameter. If filler metal is added, the maximum arc length should be about 1-1/2 times the electrode diameter. Filler wire should be fed into the weld zone at the junction of the weld joint and arc cone.
The wire should be fed smoothly and continuously into the puddle. An intermittent dipping technique causes turbulence and may result in contamination of the hot end of the wire on removal from the shield. The contaminants are then transferred to the weld puddle on the next dip. Whenever the welding wire is removed from the inert gas shielding, the end should be clipped back about 1/2-inch to remove contaminated metal. Interpass temperatures should be kept low enough, such that additional shielding is not required.
Cleaning between passes is not necessary if the weld bead remains bright and silvery. Straw or light blue weld discoloration can be removed by wire brushing with a clean stainless steel wire brush. Contaminated weld beads, as evidenced by a dark blue, grey, or white powdery color, must be completely removed by grinding. The joint must then be carefully prepared and cleaned before welding again.
Evaluating Weld Quality
Prior to making production welds on titanium, procedures and techniques should be closely evaluated. For pressure vessel construction, the ASME Boiler and Pressure Vessel Code, Section IX (Welding Qualification), details procedure and performance tests that must be met.
Tensile and bend tests on trial welds made under conditions intended for production are the acceptance criteria. Impact or notch tensile tests may also be required, particularly for low-temperature applications. Once good procedures are established, as evidenced by tensile and bend tests, they should be strictly followed in subsequent production welding.
Bend Tests
Bend tests evaluate ductility. For this reason, the bend test made on preproduction trial welds or on extensions of production welds made for that purpose provides a good evaluation of weld quality. A bend sample in which the weld is positioned perpendicular to the bend axis assures uniform straining of weld metal and heat-affected zones, thereby giving more meaningful results. Table 1 lists weld bend radii for various titanium alloys.
Table 1 lists weld bend radii for various titanium alloys.
Table 1. Bend radii for titanium welds
|
1
|
2T
|
2
|
3T
|
3
|
4T
|
4
|
4T
|
5
|
10T
|
7
|
3T
|
16
|
3T
|
11
|
2T
|
17
|
2T
|
12
|
5T
|
Good quality welds should be capable of being bent to the indicated radii without cracking. Problems with titanium welds are generally a result of contamination due to inadequate shielding. The color of welds can be used as an indicator of shielding effectiveness and, indirectly, weld quality. Thus, any indication of the quality level of a single pass titanium weld is readily apparent to the welder and any inspector. Weld colors reflect the degree to which the weld was exposed to oxygen (air) at elevated temperatures.
A bright silvery metallic luster generally can be taken as an indication of a good weld, provided the weld joint was clean and good techniques were followed. The presence of other colors, as indicated in Table 2, represents various degrees of surface and weld contamination and requires attention.
Table 2. Irregularities in weld colour and corresponding treatments
|
Light Straw, Dark Straw, Light Blue
|
Surface oxide. Remove by wire brushing with new stainless steel wire brush.
|
Dark Blue, Grey Blue, Grey
|
Metal contamination. Welds should be removed and done over after corrections in shielding are made.
|
White (loose deposit)
|
Metal contamination. Welds should be removed and done over after corrections in shielding are made
|
Hardness measurements on weld vs. base metal are also sometimes used as an indicator of weld quality. Normally, uncontaminated weld hardness is no more than 30 points greater on the Knoop, Vickers or Brinell hardness scales (5 points Rockwell B) than the hardness of base metal of matching composition. It should be recognized that heat-to-heat variation in chemistry, within specifications, can result in hardness differentials somewhat higher than 30 Knoop or Brinell without any contamination. In any event, high weld hardness should be cause for concern because of the possibility of contamination.
The ASME Code suggests that, if titanium weld metal hardness is more than 40 BHN greater than base metal hardness, excessive contamination is possible. Substantially greater hardness differential necessitates removal of the affected weld-metal area. The Code further specifies that all titanium welds be examined by liquid penetrant. In addition, full radiography of many titanium joints is required by the Code.
Resistance Welding
Resistance spot welding, seam welding, and butt welding are performed on titanium in much the same manner as for other metals. As with arc welding, careful attention to the cleanliness of metal surfaces and to the protection of weld metal and heat-affected zones from contamination by air are important.
Preparation of titanium for resistance spot or seam welding is similar to that for other metals. The surface must be clean, free of scale, oxide, dirt, paint, grease, and oil. Cleaning of mill surfaces with commercial, nonchlorinated solvents which leave no residue is satisfactory. Light oxide scale, such as is present after elevated temperature forming has been performed, should be removed by acid pickling or by wire brushing with a clean stainless steel wire brush.
Inert gas shielding of resistance spot and seam welds is often not required. The close proximity of mating surfaces in combination with the very short duration of the resistance weld cycle and squeeze pressure all help to exclude air from the weld. If a deep blue, grey, or whitish color develops on the surface of titanium after resistance spot or seam welding, consideration must be given to altering weld parameters or providing inert gas shielding.
Equipment and parameters for resistance spot or seam welding titanium are the same as are required for austenitic stainless steel. As with any welding procedure to be used on titanium, test resistance spot and seam welds should be made on titanium, prior to production welds. Tension-shear tests will help to determine the quality of the welds made. Once parameters and procedures are verified as producing quality welds consistently, these should be adhered to strictly during production runs.
Resistance butt welding and a variation, stud welding, are interesting techniques that are sometimes used on titanium. Clean, oxide-free abutting surfaces are a must. The flow of current through the workpiece causes arcing and resistance heating, bringing temperature close to the melting point. At the proper temperature, the workpieces are forced together, pushing molten and plastic metal out of the joint. Successful welds have been made in air. However, inert gas shielding may be required for contamination-free welds.
The resistance butt weld technique has been used to successfully join titanium to dissimilar metals such as copper alloys, steels, and stainless steel as well as other titanium alloys. Test welds should be made and carefully analyzed to establish proper parameters to be followed on production welds.
Brazing Titanium
Several brazing techniques are applicable to titanium. These include induction brazing, resistance brazing, and furnace brazing in an argon atmosphere or in a vacuum. Torch brazing is not applicable to titanium. Since brazing techniques have the potential for contaminating titanium surfaces, cleanliness is important and consideration should be given to argon or helium gas shielding. Alloys for brazing titanium to itself or other metals are titanium-base (70Ti-15Cu-15Ni), silver-base (various), or aluminum-base (various). The titanium base alloy requires temperatures in the vicinity of 1700°F (927°C), whereas the silver and aluminum-base alloys require 1650°F (899°C) and 1100°-1250°F (593°-677°C) respectively. If corrosion resistance is important, tests should be run on brazed joints in the intended environment prior to use. The titanium-base alloy reportedly offers superior resistance to atmospheric corrosion and saline environments.
Heat Treating Titanium
Heat treatment of titanium fabrications is not normally necessary. Annealing may be necessary following severe cold work if restoration of ductility or improved machinability is desired. A stress relief treatment is sometimes employed following severe forming or welding to avoid cracking or distortion due to high residual stresses, or to improve fatigue resistance. Cleanliness of titanium parts to be heat treated is important because of the sensitivity of titanium to contamination at elevated temperatures. Titanium fabrications should be cleaned carefully prior to heating, using nonchlorinated solvents or a detergent wash, followed by a thorough water rinse. Handling following cleaning should be minimized to avoid potential surface contamination.
Most titanium grades are typically stress-relieved at about 1000°F (538°C) for 45 minutes and annealed at 1300°F (704°C) for two hours. A slightly higher stress relief temperature [1100°F (593°C), 2 hrs.] and annealing temperature [1450°F (788°C), 4 hrs.] are appropriate for the Grade 5 alloy. Air cooling is generally acceptable.
Although no special furnace equipment or protective atmosphere is required for titanium, a slightly oxidizing atmosphere is recommended to prevent the pickup of hydrogen. Direct flame impingement for extended periods, leading to temperatures in excess of 1200°F (649°C), should be avoided because of the potential for contamination of the weld pool and embrittlement. Hydrogen or cracked ammonia atmospheres, also, should never be used, because their use would lead to excessive hydrogen pick-up and embrittlement.
If a scale removal treatment, following a high temperature (1200°F; 649°C) anneal is not feasible, a vacuum or inert gas (dry argon or helium) atmosphere is recommended. Superficial surface discoloration, caused by annealing below 1200°F (649°C), may be removed by acid pickling in a 35% nitric acid – 5% hydrofluoric acid bath at 125°F (52°C). However, if long heating times or temperatures above 1200°F (649°C) have been used, a molten caustic bath or mechanical descaling treatment, followed by nitrichydrofluoric acid pickling, is necessary to remove scale.
|