By AZoM.com Staff Writers from Original Material Supplied by Tecvac
Lowering fuel consumption, reducing carbon dioxide emissions, and achieving greater time on-wing between service outages are the objectives of every aircraft manufacturer and operator. The use of lighter but stronger materials like carbon fiber within the airframe is ever increasing to realize improved power to weight ratio.
Titanium is increasingly utilized as an alternative solution to steel and other dense metals to achieve weight reduction in aerostructures such as the undercarriage. Resistive coatings are applied to key engine parts in order to maintain optimal profile, minimize erosion, and extend intervals between services. Although these are key developments, they all bring in new technical challenges.
Solution to Problems Associated with Carbon Composite Structures
It is a challenging task to drill and cut carbon composite structures compared to their metal counterparts. The heat generated during the cutting process is dissipated through the metal by conduction, released by the swarf formed by machining or by drenching with cutting and cooling fluid. This is not possible with carbon fiber reinforced composites due to its poor heat conductivity and extreme hardness that make drench operations less effective to achieve cooling.
This results in heat build-up, which can lead to smearing of the bonding resins, while carbon fiber’s extreme hardness can cause rapid blunting of conventional cutting tools, thus demanding frequent stoppages to change tools. These issues can be alleviated by applying diamond coatings to tools. Tecvac recommends the use of coatings of diamond variants called Carbon Speed, Multi Speed, and Fibre Speed offered by its technical and logistical partners, Cemecon.
Tools with these diamond coatings exhibit the extreme hardness needed to avoid the erosion caused by the carbon fibers. They maintain their cutting edge up to eight folds longer compared to conventionally hardened tools and minimize smearing problems by generating less heat. Moreover, the requirement for tool changes is also reduced, which, in turn, reduces stoppages and so improves quality and productivity.
Addressing Titanium Problems
Although titanium exhibits high corrosion resistance, fatigue strength, and strength to weight ratio, poor coefficient of friction and the tendency for metal-to-metal adhesion under load owing to low hardness are its major drawbacks. This problem can be addressed by the PVD applied titanium or chromium nitride coating in lightly loaded situations by forming a surface with much less frictional resistance. However, this treatment is insufficient in heavy loading cases because of the instability of the substrate.
Tecvac offers a duplex coating to overcome this problem. The duplex coating involves hardening of the substrate by producing a hardened nitride diffusion zone underneath a lubricious PVD applied surface coating. Both hardening and final coating are done in a single process.
Improving Engine Performance
Components such as compressor blades need to operate in extreme conditions of high pressure, temperature and the erosive forces of airflow and impurities in the air stream. These conditions lead to increased fuel consumption and reduced service life of the aerofoils. Tecvac’s answer to these problems is Nitron Flight, a multi-layer coating based on chromium, titanium, carbon/metal carbide or chromium/aluminum.
Nitron Flight creates a surface that conforms closely to the polished substrate. This multilayering makes a low stress surface coating that exhibits more resilience to delamination compared to a single layer coating of the same thickness. A major international maintenance overhaul and repair contractor has demonstrated the benefits of the chromium based variation of this coating on compressor blades in side-by-side engine trials on the same aircraft. The Nitron Flight treated engine improves fuel usage by around $48,000 per year (based on 2010 fuel costs) and decreased carbon dioxide emissions by roughly 290 tons.
Nitron Flight surface coating retains the aerofoil profile and optimum smoothness of the blades, thereby resisting the erosive effects of harmful impurities in the airstream. This leads to improved fuel consumption and extended service intervals, which, in turn, results in greater time on the wing and improved return on engine ownership. The erosion made the untreated blades more susceptible to encrustation that was difficult to strip. Scale buildup was also there on the treated blades, but descaling was easier due to the surface coating.
PVD Processes
The PVD process involves vaporizing the coating material in a small crucible within the vacuum coating chamber by bombarding with an electron beam, while the component to be coated is rotated on a rack inside the chamber to allow the vaporized material to get condensed on its surface. This deposition is facilitated by applying a negative charge on the components within a positively charged chamber.
Tecvac produces bespoke machines for their use and supplies them to other manufacturers, research organizations and universities. Each equipment is supported with a complete manual, full training, and on-going advice, service, spares and back-up. Micro fine coatings provide several specific benefits. With multilayering, they extend service life by preventing the cracks in the surface layer from propagating beyond the boundary with the underneath layer.
Conclusion
Tecvac works closely with aerospace majors, universities, and suppliers in the aerospace industry to address the new challenges. The Tecvac team is equipped to transfer the newly developed process to the production environment to scale up and improve the process.
About TECVAC Ltd
Tecvac UK is part of the Wallwork group of companies. Tecvac Specialises in hard coatings, heat treatment, machine build, vacuum brazing and a range of other engineering services.
The Tecvac plant has facilities for thermal processing of components using vacuum Technology. The facility on the outskirts of Cambridge is split into three processing streams:
a) Vacuum Heat Treatment
b) Vacuum Brazing
c) Physical / Chemical Vapour Deposition (PVD / PECVD).
The latter involves the deposition of micro-fine coatings using specialised technologies such as Electron Beam, Magnetron Sputtering and Plasma Enhanced Chemical Vapour systems .
The Facilities include:
- Research and development with three full size PVD machines used exclusively for developing new processes and techniques.
- A dedicated carbon room where six specialised machines apply only carbon based coatings. This offers materials covering the full carbon spectrum from highly lubricious graphite to ultra-hard and resilient near diamond coating. This area also includes specialised equipment for internal pipe coating.
- A general coating area containing 6 machines where a range of PVD coatings can be applied.
- A Machine Production workshop dedicated to the design and manufacture of state of the set PVD machines
- Tecvac’s research and development department is a key driver to the company’s success. A group of experienced scientist and engineers are working on a range of external, internal and customer driven application research projects.
- Tecvac also possess a superb analytical laboratory, equipped to a level equal to or exceeding many university metallurgical departments. This enables the surface micro examination of untreated and treated surfaces and the application of tests to ensure consistency of coating and compliance to specification.
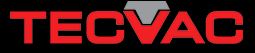
This information has been sourced, reviewed and adapted from materials provided by Composition Materials.
For more information on this source, please visit Composition Materials.