A number of potential sources can cause chronic flare and stack sampling issues. These issues in petrochemical and refining operations (Figure 1) are caused by poorly or inaccurate specified sampling equipment, restricted funds, or lack of maintenance. Perhaps the most complicated sampling issue to solve may not even be linked to the equipment.
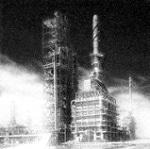
Figure 1. Refining and petrochemical operations experience process and stack sampling issues
A culture locked into traditional techniques and concepts that led to successful outcomes in the past can prevent the sampling team from accepting new techniques that will help to obtain improved sample reliability and lower detection limits. What was employed in the past may not be useful in the "new reality" of a digit part-per-million or even part-per-billion sampling requirements, stipulated by regulations like Tier 3 and more demanding customers. Discussed below are five misconceptions that contribute to the process and stack sampling issues.
I Can Prime the System and Get Good Sample Results
Currently, extremely low sulfur detection limits are dictated by regulations. It will take almost days to weeks to organize and passivate millions of active sites in stainless steel sampling flowpaths with part-per-million level sulfur process streams. In addition to this issue, subsequent desorption will lead to random sulfur spikes, complicating the measurement process (Figure 2).
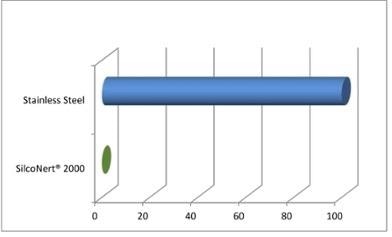
Figure 2. Sulfur adsorption rate
This issue can be solved by coating the sample flowpath with an inert coating like Dursan® or SilcoNert®. Adsorption is almost eliminated by inert coatings that help to stop the interaction between the user’s reactive sulfur sample and adsorptive stainless steel, guaranteeing an inert flowpath.
We Don't Have to Coat All the Parts In the System
Saving money by not coating filters or fittings is not a good decision. Sulfur sticks to uncoated surfaces and delivers useless test results. Even a single uncoated sintered metal filter will almost adsorb the entire sample, leading to contaminated products, angry customers or compliance issues (Figure 3).
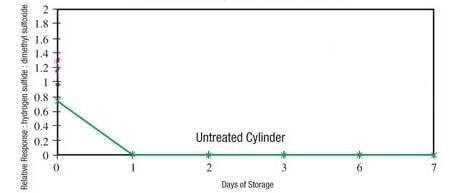
Figure 3. H2S is completely lost within hours.
We Don't Have to Worry About Moisture
Small amounts of water stagnated in sample cylinders, fittings or tubing can adsorb sulfurs and increase corrosion, considerably corrupting low level sample readings. The use of inert/hydrophobic like Dursan®, and a powerful system design enable rapid purging of moisture from sampling systems, eventually reducing sulfur adsorption and permitting the sampling team to control moisture (Figure 4).
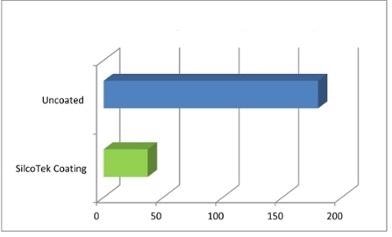
Figure 4. Moisture purge time (minutes)
Internal Surface Rust Isn't a Problem, I Can Keep Using That Sample Cylinder
Corroded sampling components are capable of absorbing almost the entire H2S sample, making the consistent sampling process a futile exercise (Figure 5).
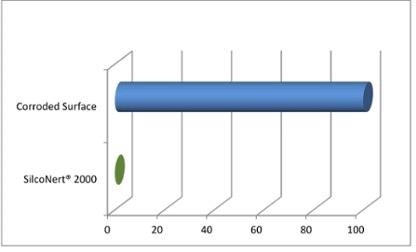
Figure 5. H2S loss
It is necessary to regularly inspect the interior of sample cylinders in order to make sure that the interior surface is free of rust particulates and corrosion. Sulfur can be rapidly adsorbed by rust particles, leading to unnaturally low readings that may result in delivering contaminated products to customers.
We Don't Need to Have Fast Response in Our System. We Can Save a Few Dollars and Go With Stainless Steel
Waiting hours for H2S readings to stabilize can be both costly and dangerous. Refiners do not want to work for days or hours in an upset condition or deliver feed stock to a downstream processor only to understand that the supply was polluted. SilcoTek® coatings enhance the response of a system by orders of magnitude, compared to stainless steel that is not coated (Figure 6). The transfer of sulfur can be considerably delayed and this would lead to potential refinery upset conditions for several days or hours.
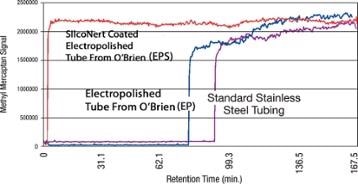
Figure 6. SilcoTek® coatings improve system response by orders of magnitude compared to uncoated stainless steel.
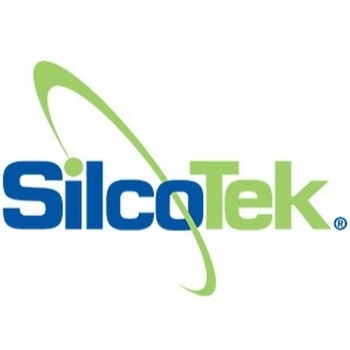
This information has been sourced, reviewed and adapted from materials provided by SilcoTek.
For more information on this source, please visit SilcoTek.