Apr 13 2017
Optimal chemical processing relies on accurate and timely measurements of chemical processes, including impurities and emissions. Process control involving hydrocarbons and other volatile organics plays a significant role in many fields of chemistry.
There is a need for fully automated instruments that have the potential to differentiate and quantify process chemistry in real time. There is still a lack of instruments versatile enough to analyze a variety of organic compounds, despite the emergence of a number of field screening instruments such as GCs.
Although GCs are an effective tool, their usefulness as a process instrument is limited by retention times of several minutes or more, even for relatively simple separations1,2.
The limits of detection (LOD) and quantification (LOQ) may not be sufficient for many applications as there is frequently no pre-concentration of the sample. GC analysis speed can be significantly improved, according to on-going research. It has been shown that detection of inorganic and organic compounds can be improved with the use of a Surface Acoustic Wave (SAW) sensor. However, until recently, no significant breakthroughs in GC design had resulted in subminute analysis of VOCs.
This article details the development and application of a novel GC system equipped with a SAW detector for process measurement applications. Performance results are provided for a SAW analyzer subjected to a number of tests in the laboratory and field conditions. These results highlight the possibility to differentiate and quantify a variety of chemicals in near real time (< 1 minute) with good accuracy and precision in measuring chemical processes.
Description of Technology
High speed (< 1 minute) chromatography has been obtained by combining innovations in preconcentrator, injector, column and sensor technologies into a chemical vapor analyzer system, known as zNose® 3,4. Figure 1 depicts the major elements of a multi-port vapor analysis system.
.jpg)
Figure 1. Multi-port process control system containing one section with helium flowing through a self-heated capillary column and the other for sampling up to 16 different vapor sources
In this method, self-heating of the GC column is attained by allowing electrical current to pass directly through a metal column. The low thermal mass of the metal capillary column allows resistive heating of the column at rates as high as 20 °C/second. Maximum resolving power is provided by isothermal analysis but temperature ramping enables the system to analyze both heavy and light compounds at the same time.
Chemical vapors to be analyzed are pumped through a small loop trap (0.5 milliliter/second). The trap comprises of a metal capillary filled with approximately 1 mg of tenax® absorbent. The trap is cooled during sampling and organic compounds are preconcentrated in the trap absorbent. The trap is switched into the helium flow by a 6-port rotary valve after preconcentrating, and it then becomes an injector. Preconcentrated organics are injected by rapidly heating the trap to 250 °C in 10 milliseconds.
Such instant column heating produces very short analysis times and causes effluent peak widths to be measured in milliseconds rather than in minutes or seconds as is done with a traditional gas chromatograph 5,6. Conventional GC detectors like electron capture or flame ionization are designed to measure column flux and often contain considerable ‘dead’ volume which makes them inappropriate for measuring millisecond wide peaks in chemical processes.
The SAW technology was initially developed to produce miniature frequency control elements for communications and radar equipment. A quartz crystal SAW resonator has been transformed into an integrating GC detector, as shown in Figure 2.
Surface waves or elastic vibrations bound to the surface of the crystal are generated by electrical signals in the piezoelectric crystal. The frequency of the resonator is changed by material interacting with the crystal surface by slowing down the surface waves. The change in frequency is a direct measure of the amount of material on the crystal surface. The stability of the acoustic resonance allows the detector to achieve picogram sensitivity.
.jpg)
Figure 2. Design details of surface acoustic wave (SAW) detector.
The total change in frequency, measured in hertz (Hz), gives accurate quantification of the analytes as they leave the column. Variable sensitivity is attained by controlling the temperature of the crystal with a thermoelectric heating and cooling element.
Helium flowing from the GC column is directed onto the surface of the SAW crystal using a nozzle (Figure 3). A thermoelectric cooling element allows the crystal to be at a temperature cool enough (typically 10-20 °C) to promote adsorption of SVOC or VOC vapors entrained in the column effluent. Also, the thermoelectric element is used to heat and remove organic films from the crystal by reversing the driving voltage. A short, 15 second, 150 °C ‘cleaning’ step is used at the end of each chromatogram to clean the crystal before the start of the next measurement cycle.
.jpg)
Figure 3. Surface acoustic wave GC sensor with nozzle details
The SAW detector response is nonspecific and universal. Sensitivity can be controlled as it relies only on the analyte vapor pressure and crystal temperature. No ionization source or high voltages are needed to obtain picogram sensitivity. The integrating SAW detector has zero dead volume which enables it to record short duration (millisecond) GC peaks in an accurate manner.
zNOSE® FAST GC Analyzer
Shown in Figure 4, the analyzer comprises of a system controller and a Fast GC enclosure. The Fast GC enclosure contains the GC subsection which includes the preconcentrating trap, sample valve, column and detector, and the support subsection which consists of the carrier gas bottle and power supply. The system controller is based on a laptop computer that checks the data and provides a user interface.
After sequentially exiting the column, the materials interact with the surface of the SAW detector. The oscillating frequency of the SAW crystal is lowered by the added mass of the material on the SAW surface. The crystal frequency is combined with a fixed reference frequency, which leads to a difference frequency called the intermediate frequency (IF).
This IF is counted by the system electronics and the information is sent to the system controller. The detector response is interpreted by the system controller, which then attempts to identify and quantify each material it has been programmed to recognize. The frequency shift caused by an analyte is proportional to the mass of material deposited on the detector.
The retention time (RT), which tags the compound by comparison with previously stored information, refers to the time required for the material to exit the column. The columns used in the SAW/GC are 1 m in length and can be ramped at up to 2 °C/sec, unlike conventional GC columns that measure many meters in length and ramp at degree per minute rates. This allows the GC portion of the system to generate repeatable, 10-second duration chromatograms with peak widths measured in milliseconds.
.jpg)
.jpg)
.jpg)
Figure 4. The zNose® ultra-fast GC design (A) reconfigured as fully automatic chemical process controller (B & C) with a selectable multi-port inlet for measuring and controlling up to 16 multiple vapor sources.
The GC/SAW is considered to be a useful tool for quantifying the organic chemistry of a diverse number of chemicals because of its picogram sensitivity. Using an uncoated solid state mass-sensitive detector, electronically variable sensitivity, universal non-polar selectivity, and picogram sensitivity is achieved. An integrated vapor preconcentrator coupled with the electronically variable detector allows the instrument to measure vapor concentrations spanning 6+ orders of magnitude.
The zNose® system, shown in Figure 1, consists of two parts. One section or part uses helium gas, a solid-state detector and capillary tube (GC column), while the other section consists of a heated inlet and a pump, which draws process air into the instrument at a fixed flow rate, typically 0.5 milliliter/second. Connecting the two sections is a “loop” trap, which acts as an injector when placed in the helium section (inject position) and as a preconcentrator when placed in the air section (sample position).
Operation involves two steps. First, process air is sampled and organic compounds within the air are collected (preconcentrated) on the trap. After the sampling process, the trap is switched into the helium section where the collected organic compounds are injected into the helium flow. The organic compounds are separated as they travel through a temperature programmed GC column. Each compound typically has a different velocity and exits the column at a characteristic retention time. Identification or differentiation is based upon the unique retention time of each compound.
As each compound (analyte) leaves the column, it is detected and quantified by a SAW crystal detector. Detector sensitivity (physical absorption onto the quartz surface) refers to a function of crystal temperature. A thermoelectric element fixed to the backside of the crystal enables achieving electronic temperature control.
A high-speed gate-array microprocessor controls the processing of samples and includes electronic injection, timing, electronic flow control, and temperature control for the column, detector, inlet, and other parts of the instrument. The user interface is responsible for sending macro instructions to the microprocessor and showing measurement results.
This interface can be a laptop computer or a remote computer using a wireless modem (1 mile range). A software program permits users to select suitable measurement methods and to identify particular organic compounds in process air from a library of Kovats indices.
.jpg)
Figure 5. Typical n-alkane chromatogram response of a GC/SAW system
Figure 5 shows a 20-second chromatogram, indicating the GC/SAW response to n-alkanes over the range C6 to C22. A convenient headspace vapor for retention time calibration is provided by methanol containing 125 P.M. alkanes C6 to C14. Alkanes above C14 are considered semivolatile and will not pass through unheated sample needles.
Hence, it is essential for them to be directly injected into the heated inlet of the zNose®. Methanol containing 500 pg/µL n-alkanes (C16-C22) is employed as an injectable vapor standard for the higher alkanes.
Sensitivity and Detection Levels
It is essential to evaluate every GC instrument for process measurement by the sensitivity and delectability of different analytes. The GC/SAW system was subjected to a series of tests. One of the first series of tests was to measure minimum detection level (MDL) of common organics.
The MDL was based on the standard deviation of 7 replicate analyzes at a concentration that provided a signal-to-noise ratio in the range of 5 to 10. The standard deviation, σ, of the 7 replicates was determined and then MDL was calculated based on the relationship, MDL = 3.14•σ where 3.14 is the students’ t value for 7 replicates at 99% confidence level. Tables 1 and 2 and Figure 6 show the results of measurements.
Table 1. Minimum Detection levels of common volatile organic compounds (VOC).
Analyte |
MDL (ppb in Air) |
Chloroform |
45 |
Cis 1,2 Dichloroethene |
47 |
Benzene |
42 |
Carbon Tetrachloride |
130 |
Trichloroethylene |
6 |
Toluene |
10 |
Tetrachloroethylene |
6 |
Ethylbenzene |
2.5 |
o-xylene |
2.5 |
1,1,2,2 Tetrachloroethane |
3.6 |
o-xylene |
2.5 |
These measurements were obtained by sampling gas standards from a Tedlar bag for 30 seconds and using a detector temperature of 0 °C. A longer sampling time will help obtain MDL levels lower than those indicated. These MDLs are typically one to one hundredth of MDLs that can be achieved using traditional systems under similar conditions7.
Certified Scott gas was used to obtain the absolute precision and accuracy of these measurements. The accuracy varied from 90 to 97% over the measurement range7. The data clearly showed that the GC/SAW system is capable of making precise and accurate measurements.
.jpg)
Figure 6. Typical GC/SAW chromatogram of common SVOCs as shown in Table 1.
Process Monitoring Applications
The GC/SAW system was tested on several process measurements. Two such measurements are listed below.
Methyl Isocyanate Measurement
Methyl isocyanate (also methyl carbonyl amine, isocyanatomethane, MIC. C2H3NO; H3C-N=C=O) is an intermediate chemical that plays a vital role in the production of carbamate pesticides and herbicides (such as sevin, aldicarb, methomyl and carbofuran). It is also reemployed in the production of adhesives and rubbers.
Table 3 shows the standard deviation from a series of replicate measurements of MIC at relatively high concentration levels (1000 ppm), demonstrating the precision and accuracy of the GC/SAW for process control.
Table 2. Minimum detection levels for some common polyaromatic hydrocarbon (PAH) compounds
Analyte |
MDL (pg) |
Naphthalene |
1 |
Acenaphthylene |
0.1 |
Acenaphthene |
0.1 |
Fluorene |
0.5 |
Anthracene |
0.2 |
fluoranthene |
0.5 |
Pyrene |
0.3 |
Chrysene |
0.5 |
Table 3. Standard deviation of replicate measurements at high MIC concentrations ( 0-1000 ppm, 13.8 Cts/ppm)
Vapor Pressure (ppm) |
Std Deviation (ppm) |
971 |
35 |
70 |
0.6 |
55 |
2.2 |
5 |
0,25 |
Ambient air concentrations should be monitored for safety because MIC is also extremely toxic and can damage by inhalation. OSHA limits are 20 ppbv in air or 0.05 mg/m3, and therefore replicate measurements at 0-50 ppbv levels were also performed. Figure 7 shows a typical series of replicate chromatograms, offset and overlaid for viewing. Table 4 lists the standard deviations at several concentrations within this range.
.jpg)
Figure 7. Replicate MIC chromatogram measurements, horizontally offset, using 55 ppbv vapor standard. Sample time was 30 seconds (15 milliliter) and detector temperature 20 °C.
Table 4. Standard deviation of replicate measurements at low MIC concentrations ( 0-50 ppb , 1.76 Cts/ppb)
Vapor Pressure (ppm) |
Std Deviation (ppm) |
55 |
1.05 |
30 |
1.15 |
7.8 |
0.26 |
Monitoring Biochemical Processes
Biochemical processes are essential for a broad range of pharmaceutical and industrial products. In these processes, a healthy colony of bacteria is grown and maintained. It is necessary to monitor the health, viability, and production of chemicals by bacteria in real time.
The chemistry of headspace vapors from a liquid culture containing e. Coli bacteria was measured by the GC/SAW. Information on nutrient levels as well as the number of colony forming units present was provided by the real time chemical analysis. The concentration of compounds exclusively produced by the bacteria provides an easy quantification method (Figure 8).
Measuring the concentration of indole (produced by e. Coli) with the GC/SAW allowed real-time quantification of bacterial population. The nutrient in the culture is exhausted and the bacteria population reaches a plateau after a period of exponential growth. The population begins to decline and eventually dies without further nutrient.
.jpg)
Figure 8. Indole signal level (headspace concentration) vs time for e.Coli liquid culture in a biochemical process.
Summary
Improvement in the art of chromatography for process measurements is represented by the SAW gas chromatography sensor developed in this program. The SAW detector is considered to be the first and only known integrating detector for GC systems. The device operating in the frequency domain needs no radioactive ionization sources or high voltages. It is a true solid state chip technology with high accuracy at low cost, and can process millisecond duration peaks.
This latest technology represents a major improvement in fast chromatographic methods as demonstrated by the instruments’ ability to provide accurate and real-time measurement (< 1 minute) of many different compounds, and thus be used to enhance productivity without affecting accuracy or precision.
Acknowledgments
The authors wish to thank the support provided by Electronic Sensor Technology Corporation and
National University.
References and Further Reading
- Watson, G.W. and Staples, E.J., “SAW Resonators as Vapor Sensors,” Proceedings of Ultrasonics Symposium, 99. 311-314, 90CH2938-9 (1990).
- Watson, G.W., Horton, W., and Staples, E..J., “Gas Chromatography Utilizing SAW Sensors,” Proceedings of the of Ultrasonics Symposium, pp.305-309, IEEE No. 1051-0117/91/0000-0311 (1991).
- Einfeld, Wayne, “Environmental Technology Verification Report – Field Portable Gas Chromatographs, Electronic Sensor Technology Model 4100,” U.S. EPA Report No. DW89936700-01- 0, (1998)
- United States Patent Number 5,289,715 was issued to Amerasia Technology Inc. (ATI), Westlake Village , CA on March 1, (1994).
- Beling, S., G. Blaser, J. Bock, L. Heinert, M. Traxler and D. Kohl, “ Signal Conditioning for semiconductor Gas Sensors being used as Detectors in GasChromatographs and Similar Applications,” Sensors and Actuators B 52, pp15-22 (1998).
- Beling, S., G. Blaser, J. Bock, L. Heinert, M. Traxler and D. Kohl, “ Signal Conditioning for semiconductor Gas Sensors being used as Detectors in GasChromatographs and Similar Applications,” Sensors and Actuators B 52, pp15-22 (1998).
- Viswanathan, S., G. Watson and Staples, E.J., “Development of a Surface Acoustic Wave (SAW) Analyzer for Measurement of Volatile Organic Compounds “, Environmental Progress (2003) in Print.
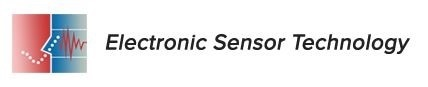
This information has been sourced, reviewed and adapted from materials provided by Electronic Sensor Technology.
For more information on this source, please visit Electronic Sensor Technology.