Fouling, coking or simply “sticking” is a costly surface problem that occurs in most industrial applications. Surface fouling causes contamination, promotes corrosion, reduces flow, increases maintenance, and ultimately inflates costs while worsening performance. Surface treatments and coatings can substantially increase system uptime and output by reducing unwanted accumulation on critical surfaces.
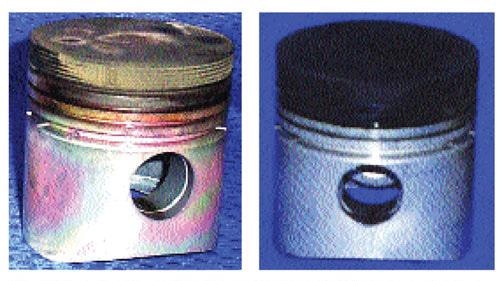
Four Applications Where Surface Fouling and Coking are an Issue
1. Automotive & Aerospace — Improve Fuel Efficiency by Preventing Carbon Coking
A key contributor to high maintenance costs is a buildup of carbon-based deposits on combustion-related components or process systems known as carbon fouling, or coking. Coking has been responsible for engine failures, shortened maintenance cycles, and unplanned repairs. For example, diesel engine manufacturers have determined that coking on pistons is a contributor to shortened engine life and costly rebuilds.1 Aircraft maintenance personnel are discovering significant coking in fuel lines, oil lines, and nozzles.
Studies have shown that coking occurs when fuels or oils are exposed to temperatures over 200 C, and increases significantly at temperatures over 400 C. Frequently, exposure to high temperature occurs after the engine or process is shut down, when there is no coolant flow to carry away excess heat.2 This stagnant-flow situation, coupled with high heat on surfaces that can catalytically form carbon deposits will significantly contribute to coke accumulation and performance issues.
Chemical vapor-deposited (CVD) coatings are applied in the gas phase and therefore ideal to treat the often complex and/or narrow flow paths of fuel delivery equipment. Specifically, functionalized amorphous silicon (a-Si) coatings applied by CVD can reduce coking by eight times or more by preventing catalysis between the metal substrate and the hot fuel or oil that is passing through the system. These coatings will flex with metal surfaces and form leak-free seals while maintaining extremely high dimensional tolerances. Most silicon CVD coatings are less than 1 µm in thickness and can be applied to existing components, ultimately extending maintenance cycles without significant re-engineering.
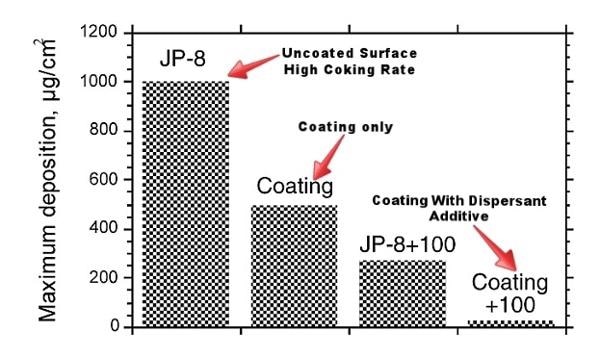
Silicon coatings improve the coking resistance of stainless steel surfaces in the presence of JP-8 fuel. When a dispersant additive is used on a coated surface, nearly 100% of carbon coke deposits can be prevented.
2. Power — Increase Performance by Preventing Scaling and Fouling on Heat Exchanger Surfaces
It has been estimated that 50 percent of maintenance costs in power applications are caused by unwanted deposits that are fouled on the interior surfaces of heat exchangers. This translates into billions of dollars in costs from process downtime and maintenance because a fouled surface simply cannot transfer heat as efficiently as a clean surface.
Keeping heat exchangers free of buildup caused by fouling or scaling is critical in keeping power generation processes up and running. Non-wetting coatings offer low surface energy and prevent media from sticking and building up on the surface. Fluoropolymers such as PTFE are often called upon in these applications, but their poor temperature stability and propensity to flake can quickly become problematic. Alternatively, CVD coatings impart a similarly low energy to the surface, but are molecularly bound to the metal surface of the heat exchanger, providing enhanced adhesion and durability compared to fluoropolymers.
3. Petrochemical & Plastics — Increase Plant Uptime by Reducing Maintenance
Refineries and other petrochemical plants must also spend considerable resources to combat coking and fouling. For example, refinery preheat train (PHT) networks experience downtime caused by fouling that can cost upwards of 66 million barrels of refined crude oil per year.3 Fouled equipment reduces production efficiency and can increase the likelihood for corrosion. This is a recipe for disaster when every second of uptime counts towards the operation’s bottom line.
Because materials that are used to produce plastics and other petrochemical products are often sticky and corrosive themselves, it’s important that production equipment is equipped to withstand them. However, common materials of construction such as stainless and carbon steels are not designed to do so. Therefore, it’s imperative that anti-fouling coatings are applied to maximize equipment uptime. Common coatings in refineries are purchased in bulk and applied on-site, but these barriers are rarely suited for the advanced performance properties that are required to prevent surface fouling. Instead, consider more functional coatings that are designed specifically to reduce wetting, such as amorphous silicon coatings. These coatings can be applied to existing equipment to minimize front-end costs.
4. Medical diagnostics & Pharmaceuticals — Ensure Accurate Results and Equipment Uptime by Preventing Surface Activity
Preventing adsorption of proteins and other media onto medical device and clinical instrumentation is highly desirable. In addition to sanitary concerns, surface fouling can cause false positive or negative results, which lead to unwanted stress for both doctors and patients. From a financial perspective, these tests are extremely costly to run, so needing to repeat them is a problem that should be avoided as much as possible.
Few coatings offer the combination of purity, durability, and non-stick properties that is critical in medical device and diagnostic applications. Amorphous silicon coatings applied by CVD provide a robust, low energy surface that prevents proteins and other media from sticking to flow path surfaces. When compared to common solutions like fluoropolymers, silicon-coated stainless steel offers both better protein resistance, as well as ruggedness to withstand common cleaning and maintenance procedures.
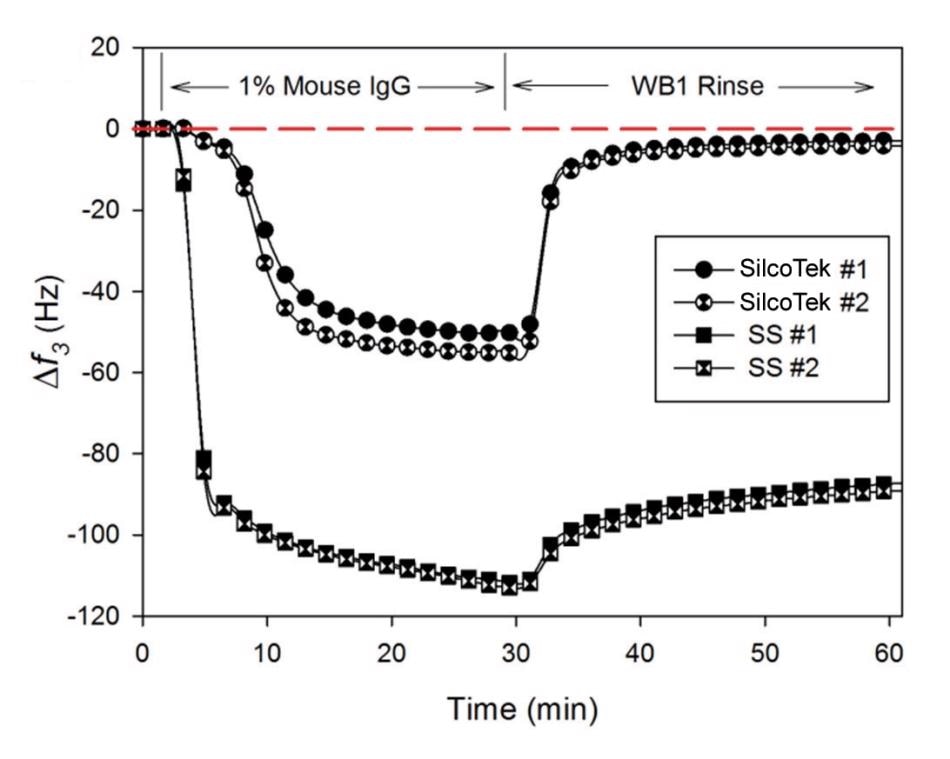
Stainless steel surfaces coated with functionalized amorphous silicon oxide (top) are cleaned significantly more easily than fluoropolymer surfaces (bottom), which retain more proteins and are easier to damage.4
Conclusion
Amorphous silicon-based coatings applied by chemical vapor deposition (CVD) provide high-performance surface properties that are critical for preventing problems associated with surface fouling and coking in key industrial applications. SilcoTek® is the world’s leading provider of CVD coating services and can apply anti-fouling, chemically inert, corrosion resistant, and other coatings to critical parts and components.
References
- Perez, J., A. Boehman. Penn State Multi-Discipline Tribology Group and Energy Institute Studies, The Pennsylvania State University, University Park, PA (1998).
- Jones, E.G., W. Balster, W. Rubey. Fouling of Stainless Steel and Silcosteel Surfaces During Aviation-Fuel Autoxidation Systems. Research Laboratories, Inc., Dayton, Ohio; University of Dayton Research Institute, Dayton, OH (1995).
- Pugh, Simon, Ishiyama, Edward; IHS Energy. Managing Fouling in Refinery Networks. July 2015. http://www.digitalrefining.com/article/1001191,Managing_fouling_in_refinery_networks.html
- Vaidya, S.V.; Yuan, M.; Narvaez, A.R.; Daghfal, D.; Mattzela, J.; Smith, D. Appl. Surf. Sci. 2016, 364, 896-908.
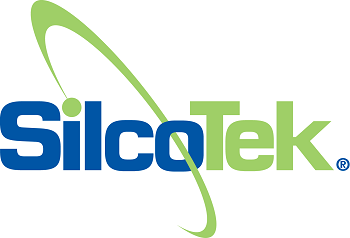
This information has been sourced, reviewed and adapted from materials provided by SilcoTek.
For more information on this source, please visit SilcoTek.