A well-known reaction, Fischer-Tropsch Synthesis (FTS) has been receiving increased attention recently as a result of the growing interest in the microGTL process.
Compact units are required for isolated onshore gas fields (stranded gas) and associated gases in offshore platforms, in order to transform gas into liquid fuel on a substantially smaller scale than is possible using conventional GTL plants.
Fischer-Tropsch Synthesis in the microGTL Process
As a result of this renewed interest, numerous patents, books, and papers have been published over the last 10 years, both within the industry and in academia, concerning the field of microchannel reactors which include the GTL process and particularly FTS.
New possibilities are offered for FTS by microchannel technology, as it enables intrinsically safe functioning, allows for extremely compact units (process intensification), and delivers exceptional temperature control with substantial significance in control selectivity for liquid fuels (C5+ selectivity).
Developments in Adapting a Catalytic Test Unit
This application note presents developments in the adaption of a catalytic test unit (PID-Micrometrics Microactivity Reference) for testing microchannel cross-flow blocks during FTS. This development enables the same unit to be used for testing structured catalysts (monoliths), powder catalysts, and microchannel blocks.
Testing of Microchannel Cross-Flow Blocks During FTS
As displayed in Figure 1, the microchannel blocks present 100 microchannels (0.7 x 0.7 x 20 mm) which are coated with FT catalyst (20% Co to 0.5%Re/Al2O3) perpendicularly interspersed with 100 similar microchannels for the purposes of cooling.1
The ability to control reactor temperature, as well as the flow and pressure of the various gas reactants was enabled by the original unit. In order to cool the exothermic FTS with pressurized water, a second fluid line was developed.
.jpg)
Figure 1. Image of the microchannel block
.jpg)
PID-Micromeritics Microactivity Reference
.jpg)
Figure 2. A microchannel reactor.
Included in this line are a heat exchanger which permits a water-cooling loop, a high-pressure pump, pressure transducers, a motorized needle valve for controlling water pressure, and a heater and thermocouple for controlling water temperature. The liquid water’s low compressibility rendered any initial attempts to control pressure impossible.
In order to overcome this problem, a container that was partly filled with air was added. This was designed to cushion the extremely large pressure changes which are associated with the temperature fluctuations. In addition to this, the pressure set point of the cooling water was adjusted to a pressure which corresponded to a minimum of 20 bar higher than water vapor pressure at the FTS temperature.
The conditions described above made the cooling stream extremely stable. Extra modifications to the control software were also required, in order to include monitoring of the high-pressure pump and new control loops for the cooling stream (pressure and temperature).
Homogenous gas velocity at the entry point of all graphite gaskets and microchannels was assured by fitting the microchannel block with CFD-designed headers — this guaranteed exceptional sealing (<L 0.01).
The compression’s strength and the deformation of the graphite gaskets are ensured by a double housing, which includes heating cartridges for the reduction pre-treatment as shown in Figure 2.
At each gas outlet and inlet there is a tee junction. This enables thermocouples to be arranged in contact with the block face. When combined with thermocouples on the block’s lower and upper surfaces, this facilitates the total monitoring of the microchannel unit throughout the control software’s data logging facility.
Conclusion
Numerous reactions were undertaken with varying catalyst loads on the microchannel blocks. This system was shown to be extremely stable. Over a number of weeks, standard tests were carried out which allowed for changes in temperature, pressure, and flow. Displayed in Figure 3 is a methane selectivity and CO conversion microchannel test under varying conditions in a typical experiment.
.jpg)
Figure 3. CO conversion and methane selectivity in microchannel test
Several reactions were carried out with microchannel blocks that had different catalyst loads. The system proved to be highly stable. Standard tests were carried out over several weeks allowing for changes in flow, pressure, and temperature. Figure 3 shows CO conversion and methane selectivity under different conditions in a typical experiment.
References and Further Reading
- L. C. Almeida, F. J. Ehcave, O. Sanz, M. A. Centeno, G. Arzamendi, L. M. Gandia, E. F. SousaAguiar, J. A. Odeiozola, M. Montes, , “FischerTropsch Synthesis in Microchannels”, Chemical Engineering Journal 167 (2011) 536–54
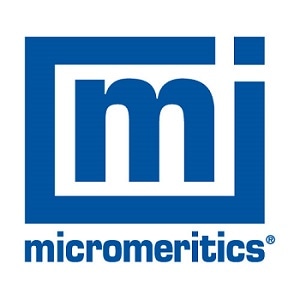
This information has been sourced, reviewed and adapted from materials provided by Micromeritics Instrument Corporation.
For more information on this source, please visit Micromeritics Instrument Corporation.