Break through boundaries in aerospace tool design and discover new geometries with Element Six PCD round tool blanks.
.jpg)
The CFRP Revolution
Airframe weight reduction is driven by revolutionary Carbon Fibre Reinforced Polymer (CFRP) composites and stacks.
50% of Airframe Materials now made up of CFRP Composites
The 787 Boeing Dreamliner uses 50% CFRP composites by weight, for fuselage, wings, stabiliser, fin, control surfaces and nacelles. Aerospace’s overall use of CFRP is predicted to grow to 23,000 tonnes by 2020 - a 14% increase p.a.*
* Aerospace Design & Manufacturing Magazine 2014.
Transforming Aircraft Operational Economics
As airframe weight drives the aircraft operational economy, the global aerospace industry is turning towards CFRP. There are multiple benefits offered by CFRP, such as:
- Up to a 25%* improved fuel efficiency, with weight reduction for improved emissions
- High wear resistance for lessened maintenance costs
- Higher cabin pressure thanks to its strength, facilitating greater passenger comfort
- The potential of increasing payloads
* Boeing Corporation / Airbus.
Meeting the Challenge of Machining New Materials
New technology is required to machine these new durable, strong, lightweight and fibrous materials. Element Six's Aero-Dianamics™ range of Polycrystalline Diamond (PCD) round tool blanks is a revolutionary technology that allows the tool designer to attain geometries to precisely match the customers’ milling and drilling requirements, a previously impossible task.
A New Generation of PCD Tools Accelerates Production in CFRP
CFRP airframe components can be produced faster and more efficiently , thanks to the ability to mill and drill CFRP faster, at lower temperatures, more cleanly and with lower tool forces. This efficiency means that finished components can be delivered for assembly with shorter lead times, which permits airplane manufacturers to have a shorter delivery schedule for customers.
.jpg)
Tool Design Set Free
Barriers in aerospace tool design have been broken by a revolutionary PCD tool.
.jpg)
About the Aero-Dianamics™ Range
Tool designers can now break through existing obstacles of PCD tool design with these innovative PCD tool geometries, such as:
- Freedom of flute profile design
- Multiple flutes
- Unlimited flute angles and orientations (left/right/compressive)
These composite tooling solutions are next-generation, eradicating the need for coated tungsten carbide tools in fabricating composite components.
Main Product Portfolios
Milling and drilling are the two portfolios of Element Six’s Aero-Dianamics™ range. They are comprised of three production-ready product configurations.
AD-Drilling
.jpg)
Chevron
.jpg)
Planar
AD-Milling
.jpg)
Helix
Aero-Dianamics™ Revolutionary Drilling Materials
Unique Planar AD-D3 Blanks for Complex Drill Geometries
.jpg)
- Almost limitless flexibility of drill point geometry
- Vastly increased durability compared to traditional coated carbide drills
- Tool lifespan increased by over 10 times* compared with tungsten carbide drills
- Consistent tool life performance
- Increased cutting point flexibility
- PCD not brazed but instead physically bonded to substrate
- Improved work piece surface finish
- Greater rake angles possible for lower tool forces
- Can undergo multiple re-sharpenings
- Fabrication by either traditional grinding or Electro Discharge Machining (EDM)
- Ideal for drilling CFRP stacked with titanium or aluminum*
* The University of Birmingham, UK.
Premium Quality Chevron PCD Inserts for 2D Geometry Tools
.jpg)
- Disc formats both full and half round
- EDM cut available to order
- Significantly increased durability in comparison with coated carbide drills
- Lifespan of tool up to 10* times longer than that of carbide drills
*The University of Birmingham, UK.
Revolutionary Helix AD-M3 Blanks for Milling Tools
.jpg)
- A 250X* increase in durability compared with conventional tungsten carbide end mills
- Machining speeds up to 12* times faster
- Lower tool forces and better chip evacuation thanks to helical geometry
- Less heat build-up and adhesion due to high thermal conductivity and low coefficient of friction
- Fast fabrication due to EDM
- Cleanly-cut fibers thanks to sharp PCD edges
- Reconditioning of end mills possible for even greater tool life
*Modern Machine Shop Magazine.
Breaking Through Existing Barriers in PCD Tool Design
Helix Cutting Angle to Assist with all Application Needs
.jpg)
- Flexibility offers the option to optimize design in order to meet work piece application demands
Dual Angle Drill Point Geometry
.jpg)
- Necessary flexibility when determining drill cutting points
- Can achieve included angles up to 90°
Multiple Flutes
.jpg)
- Faster drilling speeds, better chip evacuations and lower forces are all results of more flutes
- No constraint for tool designers due to planar PCD shape
- Offers greater design flexibility
- Ultimate choice of Point Angle / Cutting Lips / Chisel Edge / Lip Relief geometries up to designers
- Limitations of traditional planar PCD sections removed by larger PCD layer formats
Pre-determined Flute Angle Configurations
.jpg)
- PCD processing times lessened
- Sharp PCD edges cleanly cut fibers
- Increased cuts per rotation thanks to increased number of flutes
- Lower tool forces and better chip evacuation due to helical geometry
New Tools Enable New Levels of Productivity
Exponential increases in productivity linked to these five leaps in tool performance
1. Superior Durability over Coated Tungsten Carbide
Of all materials in industrial use, PCD is the hardest man-made material, far exceeding the wear-resistance of tungsten carbide.
2. Longer Tool Life with Consistent Precision
Tool life is extended by a factor of at least 10* times with the employment of PCD, as well as maintaining maximum sharpness throughout the tool’s life.
* The University of Birmingham, UK
3. Flute Angles to Cut Fibers More Cleanly
Consistent hole and edge quality are produced by PCD drills and end mills for much longer, as compared to coated carbide tools.
4. Faster Tool Operation with Better Temperature Control
Tools may run faster with PCD, thanks to its sharper edges and subsequently reduced friction, paired with its high thermal conductivity. This means that CFRP stacks with aluminum and titanium can be drilled at twice the speed* without risking the problems linked to overheating of the work piece.
* AMRC, Sheffield, UK.
5. Reduced Re-Working and Downtime
The eradication of lengthy reworking of holes and edges, combined with longer intervals between tool changes hugely lessens machine downtime.
.jpg)
.jpg)
The Result is Exponential Increases in Productivity
Productivity is guaranteed for tool makers with these market-leading Aero-Dianamics™ tool blanks, by creating semi-finished tool materials and enabling rapid creation. Productivity is ensured for aerospace customers by significantly speeding up production of CFRP components.
Delivering an Attractive Cost of Ownership Solution
For machining the newest generation of composite materials, Aero-Dianamics™ is a proven cost-effective solution. Examples illustrating this are outlined below. Further tests are ongoing, whilst the below are taken from current testing.
Milling
Aero-Dianamics™ Helix tools significantly lessen the total time required to mill 10,000 meters when contrasted with tools of uncoated tungsten carbide and competitor flute PCD.
.jpg)
Drilling
Aero-Dianamics™ Planar and Chevron tools vastly lessen the total price of drilling 10,000 holes compared to competitor veined PCD, CVD and tungsten carbide tools.
.jpg)
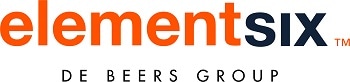
This information has been sourced, reviewed and adapted from materials provided by Element Six.
For more information on this source, please visit Element Six.