It is extremely important to understand all aspects of thermal fluids before selecting your chosen one. In this interview, Ryan Ritz, Global Director of Technology at Paratherm, talks to AZoM about what makes heat transfer fluids unique, and why not all fluids are created equally.
What are heat transfer fluids, and what are there key uses in industry?
Heat transfer fluids are also known as thermal fluids or thermal oils. They can also be referred to as heating or cooling fluids, but the two most common terms are thermal fluid and heat transfer fluid today.
The key point behind heat transfer fluid technology is the ability to generate high temperatures at low system pressures. Heat transfer fluid technology offers safety, low maintenance, and extending operating lifetimes when compared to traditional technologies such as steam heating or direct fire heating. This technology offers highly efficient non-corrosive heating and cooling and allows for accurate temperature regulation and uniformity across the entire system.
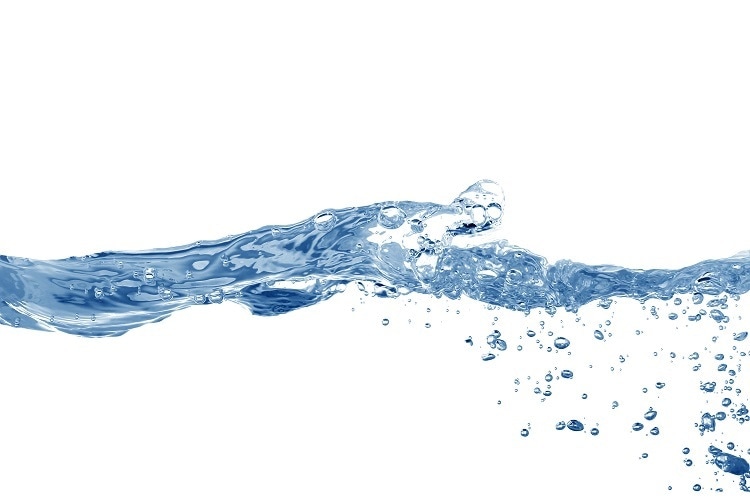
Why is selecting the right fluid so critical to a smooth operation?
Selecting the wrong fluids are likely going to lead to accelerated degradation, equipment failures that are associated with those degradation products, fouling of the fluid on the surface elements in the equipment, increased maintenance activities, and decreased efficiency on both the heat transfer and total system operation. When run properly with the correct fluid, heat transfer systems are safe and low maintenance by design. The inherent dangers of any high-temperature operation will increase exponentially if these factors are taken for granted. Therefore, fluid selection is so important. One thing that's often overlooked at the end of this is the partnership that you should have with the supplier of that thermal fluid.
You talk about the seven fluid C’s: classification, capabilities, conditions, compatibility, cost considerations, competitive benchmarking, and credibility. Starting with classification, could you give us a run through about how each of these criteria are analyzed when choosing a heat transfer fluid?
At the bottom of the scale there are three different general classifications. There are aqueous-based fluids that use water as the heat transfer medium. Water is the most efficient and the highest-quality best product that you can get for heat transfer in general by theory. The problem with water is it freezes, and it boils, so you have a very limited range where you can use water for your heat transfer fluid.
Moving up the temperature scale you have something that could be based on a type or general classification as a mineral oil. Then at the top of the capability list for classification temperature capabilities, you get into silicone-based fluids and aromatic blends. Aromatic and silicone blends also bring you back down to the bottom of the scale and allow for extreme low-temperature cooling as well.
There are also hydrocarbon-based heat transfer fluids that form two categories. We have natural organic hydrocarbons. This is base chemistry that consists of a selected mixture of molecules generated during the crude oil process, the refining process. Mineral oils are featured for their non-toxic, efficient, and cost-effective performance. Budget-minded and capability-minded, they're very good at a range from moderate to high temperatures.
The other category is the synthetic organic hydrocarbons, referred to more commonly as aromatic-based fluids. They display a very high thermal stability at higher temperatures, and then also offer lower start-up temperatures than the natural mineral oils.
In a perfect world, you would be able to have something that's the most stable that gives you the best range of temperatures. However, there are several other considerations that must be taken into account.
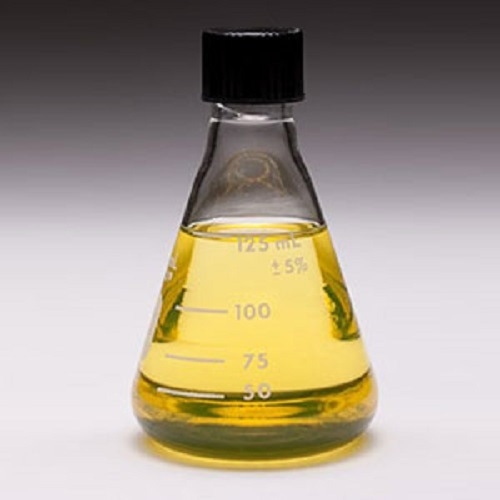
What are the fundamental capabilities of the various fluids?
The fundamental product capability that you'll have to look at right off the top of things would be your operating temperature range, and what you really should look for in this range is your minimum operating temperature. That's going to be the performance characteristic that's going to be most relevant to what you're doing.
At the other end of the scale is the maximum operating temperature. That will be defined as the temperature at which the fluid you're looking at will be able to give you efficient performance and will be able to last a reasonable amount of time in your system if you operate it correctly.
After this is the minimum start-up temperature. Your options become extremely limited at that point to what kind of technology you can have, that has that wide of a temperature range available to you.
Your climate and environment are also very important capabilities to consider. Fluid with a minimum start-up temperature above your environmental ambient temperature is going to cause problems. A fluid with a lower start-up is going to offer you much better fluid longevity and protection against premature degradation during the start-up process.
Some other fundamental considerations are looking at the fouling aspects of the impurities that you have, noting the presence of any additive packaging, and the temperature claim capabilities. If you know nothing else about the operating conditions on your process prior to this selection process, at the very least you should know the required operating temperatures.
For performance capabilities, you need to look at for the capabilities of fluid as a primary factor is a functionality based off three key features: the thermal stability, the heat transfer efficiency, and the product purity.
Some other areas where you can consider if all those things are equal, are the expansion rate of the fluid, and how that ties into the system sizing, as well as the flash and fire points.
Another area to look at is oxidation resistance. There's some inherent oxidation resistance with different chemistries, and the ability to introduce additives, antioxidant additives to help with that.
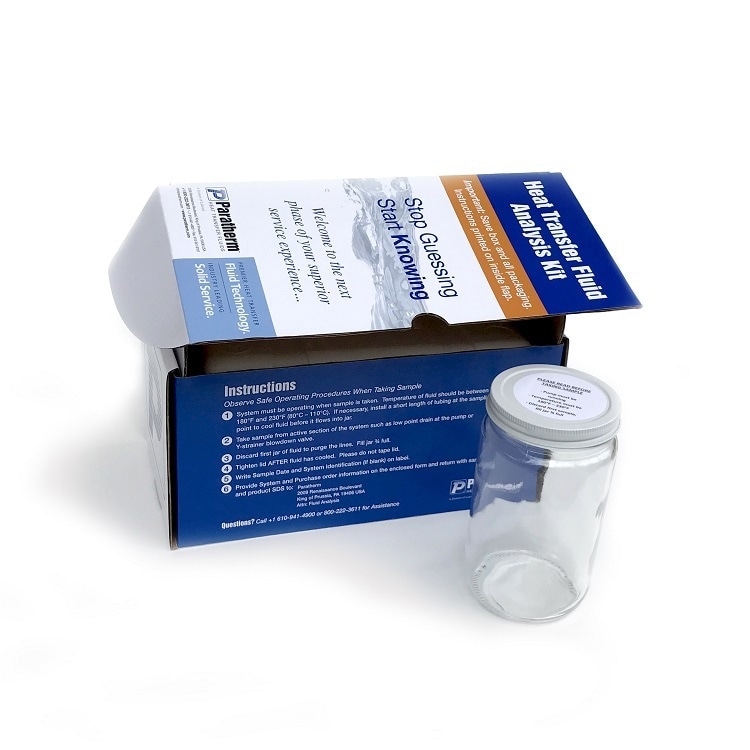
How do the conditions of your system dictate your fluid selection process?
You really can't change the process specifications too much. This is the area that has your rotated system; the equipment you've already selected; the application and the process that your plant is producing. All of those have inherent limitations that help you choose one way or another on fluids that you're going to specify.
The first consideration is: does it require a food grade rating? It may not be food production per se, but it may require a safe product to be used. If it's that kind of application, you need to make sure you choose a fluid that has NSF HT-1 Incidental Food Contact rating.
Some other operating conditions may be: if it is a continuous process, the local climate, and is the system open to the atmosphere.
Also, the fluid that you choose based off its ability to operate over your entire cycle may not have the inherent capabilities to transition between temperatures quickly and you're going to be cycling much slower. That's a lot of downtime and could possibly really hurt your application if you're not using a heat/cool fluid that's capable of that cycle.
What are some of the compatibility concerns you may have?
Compatibility concerns can come in the form of a few different areas. The primary one is making sure that you're looking at materials of construction that are going to be compatible with the fluid that you choose.
Another cause for concern for compatibility is the fluid/fluid compatibility. The process for replacing the existing fluid is extremely important. Make sure that whatever the degradation level is in that system isn't going to be something that's going to immediately contaminate and hurt the new fluid that you're putting in. It's virtually impossible to drain a system and get all the fluid leftover, causing fluid/fluid issues. Miscibility is one key issue. If the two fluids are not able to fully mix together, you're going to have phase separation. Phase separation can cause all kinds of problems with vaporization of one fluid over the other, pump cavitation’s, unnecessary wear on the gaskets and polymers throughout the system itself.
Reactivity isn’t common, but you should check that you're not going to have any inherent reactivity or you're not forming something new that's going to be outside of the design specification of the fluid that you're running.
The next issue is contamination. Degradation and maintenance contaminants are incompatible with most fluids and will immediately degrade the fluid that you have in there. You also need to look at all materials of construction for compatibility with water, because there's a clear line between what's compatible with aqueous fluids and what's compatible with non-aqueous fluids.
A common problem which arises when someone's changing out a degraded fluid and switching to a new one. Oftentimes that person applies a cleaner in between the refills. Be very cautious of what that cleaner is. Don’t use an aqueous-based cleaner as it's going to cause more headaches than it's worth. If it's a solvent-based cleaner you need to make sure that that solvent's not going to cause problems to your new fluid when you put it in.
What are some of key aspects that should be considered when thinking of the costs of the fluid?
When considering cost versus performance, critical analysis becomes most critical when you are near classification extremes, and the safety cushion of an extended temperature range of a synthetic comes at a cost. That cost is three to four times per gallon cost between the high-performance synthetic products and the highly engineered mineral oil products.
That's by going through a total life cost analysis, and if you're switching to a supplier who requires a 20% a year best practices top-up rate, that's also going to cost you. Synthetic aromatic products typically require you to have a waste removal service, which comes at a cost, versus a general oil recycling service that can come in and just remove the product for you and, depending on the cost of oil, may give you a credit towards that.
If you're at that extreme operating temperature range, your fluid that you're looking at is limited to 600 but your process calls for 590, rest assured that you're going to be replacing that fluid more commonly than not. The upfront capital investment or the upfront investment of putting into the aromatic fluid, three to four times the cost, well if the lifecycle of that is expected to last five or six times the life of the mineral oil, that's going to be something that you can really consider.
If you have narrowed the choice down to two products: A and B, how does competitive benchmarking help to decide the final fluid you will use?
The key competitive differentiation factors that are product based are: heat transfer efficient, high purity, and thermal stability.
Heat transfer efficiency is determined by an ideal combination of low viscosity, high density, high thermal conductivity, and high specific heat capacity. Those advantages, weighed out and ratio-ed out and designed, will give you better heat transfer efficiency at any proposed operating temperatures and flow conditions.
You need to remove the impurities that catalyze fluid degradation and foul equipment surfaces when continuously exposed to high operating temperatures. This extends the service life of the fluid, reduces maintenance activities, lowers risk of equipment failure, and gives greater consistency in performance.
The next key criteria, thermal stability. Greater thermal stability fluids will result in higher heat transfer efficiency over time, longer fluid life, and lower potential for system damage and safety hazards when proper operating conditions are followed.
Additional considerations: thermal expansion, oxidation resistance, fouling resistance, and vapor pressure are also key benchmarks.
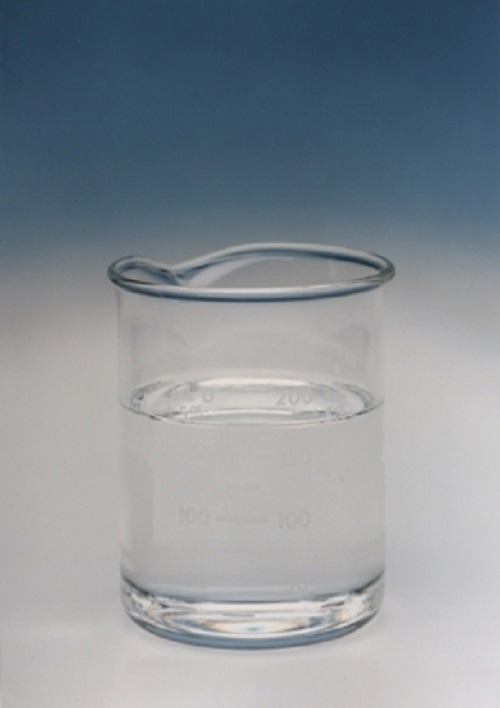
The final “C” is credibility. What do you mean when you refer to it regarding a fluid?
Credibility comes in the form of multiple things. Your thermal fluid supplier's credibility and the claims that that supplier is making. You always need to make sure you're insisting on excellence from your supplier. Talk to your equipment manufacturer. See who they recommend, not just based on the fluid but the expertise they have.
Technical support is key, as fluid degradation is going to be there no matter what. You need a supplier partner to be able to minimize the rate at which that degradation happens. Find somebody that's able to offer you that upfront and be there with you through the entire lifecycle. A fluid analysis program is the most reliable tool for keeping your system running without problems. Make sure that your supplier offers this, and whether this is in their own facility or they're doing it through third parties. That's key based on turnaround time, expertise.
Credibility of claims is important as well. You want to make sure if someone's claiming something based on their fluid, it's very oxidation resistant or it's got these additives, tell them to put that in the scope of what's important for your system itself.
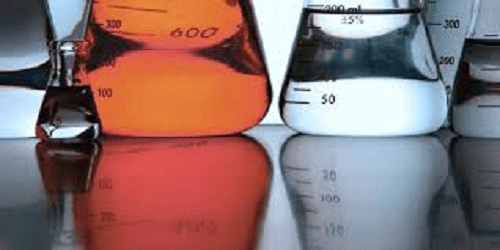
Can you summarize what is important for heat transfer fluids?
At the end of the day, all of this is here to avoid the rough waters. Using the wrong fluid will lead to accelerated degradation, failures, surface fouling, increased maintenance, and decreased efficiency. Operating outside of design specification and failing to adhere to basic preventative maintenance practices will lead to irreversible damage of the fluid and the equipment.
Choosing a reputable specialty supplier, they can work with you to select a high quality, engineered heat transfer fluid and co-develop an operation-specific preventative maintenance plan. That's going to give you a much higher return on your upfront investment, prolong your fluid life, minimize your downtime, and this critical element of your operation will run with increased safety, efficiency, and reliability, without a high demand on your personnel.
Where can our readers go to find out more?
To find out more please visit our website - https://www.paratherm.com/
About Ryan Ritz
Ryan Ritz is the Global Director of Technology - Heat Transfer at Paratherm and has worked with the company since July 2003.
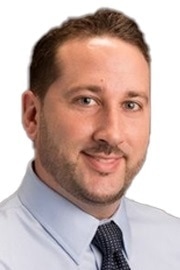
Disclaimer: The views expressed here are those of the interviewee and do not necessarily represent the views of AZoM.com Limited (T/A) AZoNetwork, the owner and operator of this website. This disclaimer forms part of the Terms and Conditions of use of this website.