Nowadays, cutting-edge sensor technologies offer an appropriate pressure sensor for all measuring tasks. Not only do these technologies offer a choice between relative, absolute and differential pressure sensors (to work with divergent reference values), they also present a range of different measuring principles based on different physical effects.
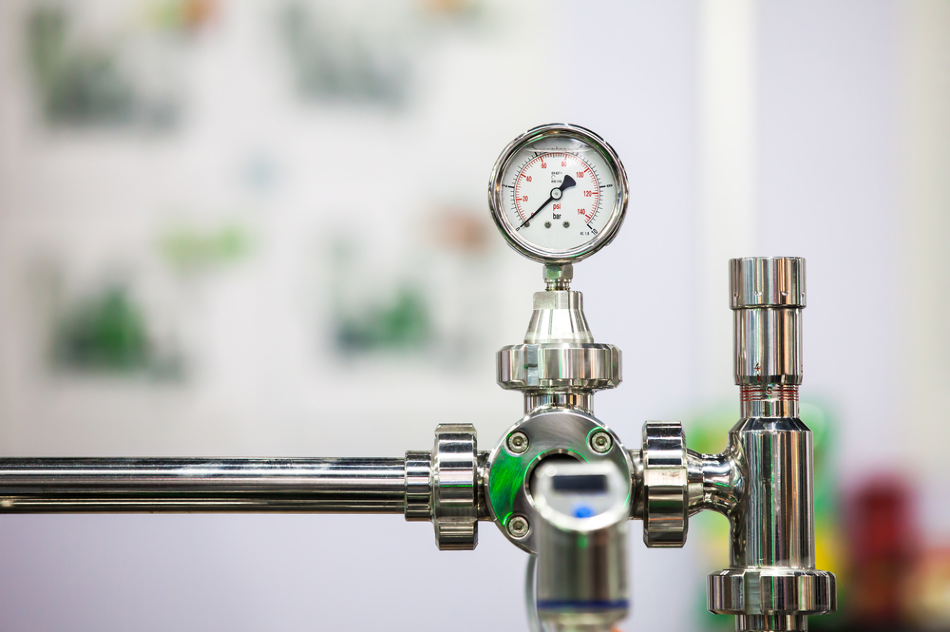
Image Credit: Shutterstock/MOLPIX
Piezoelectric and piezoresistive effects are primarily utilized among contemporary pressure sensors. This article will examine the practical advantages and special properties of a piezoresistive differential pressure sensor.
Firstly – How Does the Piezoresistive Differential Pressure Sensor Actually Work?
In contrast to relative and absolute pressure sensors, differential pressure sensors quantify the difference between any two pressures. A differential pressure sensor possesses two distinct pressure connections (hose, threaded or manifold). Moreover, depending on the calibration, it can quantify both positive (p1>p2) and negative (p1<p2) differential pressures.
The Piezoresistive Effect
Piezoresistive (diaphragm-based) differential pressure sensors based on silicon comprise a thin silicon diaphragm in which resistors (connected together in a Wheatstone bridge) are lodged. If there is any difference in pressure, the diaphragm thrusts through, causing distortion to the resistors. The inter-connected resistors in the measuring bridge react to the distortion, engendering a piezoresistive effect. This alters the resistance of the resistors and the electrical voltage. To complete the process, a pressure-proportional measuring signal is activated.
Notable Features of Diaphragm-Based Sensor Technology
- The resistor in the silicon diaphragm’s semiconductor reacts with great sensitivity to even the minutest pressure loads and changes. This allows the piezoresistive differential pressure sensor to operate with exceptional accuracy and permits measurement ranges of just a few millibars.
- Silicon embodies a monocrystalline structure, meaning that, after stretching, the diaphragm will always return to its initial state without distorting.
.jpg)
Basic design of a piezoresistive differential pressure sensors. Image Credit: First Sensor
The Comparison: How Do Piezoresistive Pressure Sensors Measure Up?
The piezoelectric pressure sensor represents an alternative to the piezoresistive differential pressure sensor. In contrast to diaphragm-based sensors, piezoelectric pressure sensors are formed of crystal disks. Under pressure, charge separation produces a proportional electrical voltage in the crystal, which is known as the “piezoelectric effect.” A charge amplifier is responsible for outputting the voltage difference, while a digital circuit is tasked with converting it to the physical value of pressure.
Both the piezoresistive sensor and the piezoelectric sensor possess unique advantages. The decision regarding the most appropriate measuring principle is dependent on the application being undertaken. For example, piezoelectric sensors can resist high temperatures and highly dynamic pressure processes especially well, while diaphragm-based differential pressure sensors are well suited to applications that require very good measurement precision and sensitivity.
.jpg)
Diagram of a diaphragm-based differential pressure sensor from First Sensor. Image Credit: First Sensor
The main advantages of using a piezoresistive differential pressure sensor:
+ Extremely small size
+ Exceptionally precise measurements
+ Outstanding sensitivity
+ Capacity to measure even the minutest differential pressures
+ Substantial measurement range: 1 mbar (100 Pa) to 10 bar
+ Minimal material fatigue or hysteresis
+ Excellent overpressure resistance
+ Analog and digital interfaces
+ Particularly linear signal – pressure characteristic curves (no air flow)
New: Piezoresistive Low Differential Pressure Sensor for Manifold Mounting
First Sensor produces diaphragm-based low differential pressure sensors in a novel small-scale manifold design. The extremely small, flat sensors span measurement ranges from 1 mbar to 7 bar and are perfect for space-saving installation in manifolds. The piezoresistive sensors comprise digital signal conditioning, an SPI interface and an analog output signal, rendering them ideally suited for battery-powered processes in mobile or portable devices.
Features:
- Suitable for mounting in manifolds
- Surface area 8 x 13 mm, height <7 mm
- Long-term stability and high precision
- Pressure ranges from 1 mbar to 7 bar
- Calibrated and temperature-compensated (0–70 °C)
- 3.3 V or 5 V power supply
- SPI interface with 15 bit resolution
Requirements:
- Manifold-compatible pressure ports
- Manifold-ready housing
- Straight connection, allowing the mounting point to be sealed with an O-ring
Application
When is the utilization of diaphragm-based differential pressure sensors recommended?
When pressure quantification necessitates high sensitivity, high measurement accuracy, pressure ranges from 1 mbar to 10 bar and a design that saves space, a piezoresistive differential pressure sensor is ideal.
Standard fields of application for diaphragm-based differential pressure sensors:
- Medical technology: CPAP, spirometers, ventilators, anesthesia equipment, oxygen concentrators
- Air-conditioning technology: filter monitoring, burner controls, flow regulators
- Measuring technology
- Industrial control and regulation technology
Precise Process Connections and Filters
In theory, differential pressure sensors should possess process connections which enable the sensor to be connected to the flow line (by means of hoses etc.). Many applications also rely on supplementary filters in the supply lines. These additional filters can prevent dust, moisture or bacterial contamination from reaching the sensor, for example.
And if a Standard Solution Isn’t Enough?
Greater accuracy, greater speed, greater efficiency, greater cost-effectiveness, greater application-specificity: Certain applications and market situations necessitate specialized sensor solutions. Consequently, as well as providing a broad array of diaphragm-based differential pressure sensors, predominant manufacturing companies, such as First Sensor, have also developed and implemented application-specific sensor systems.
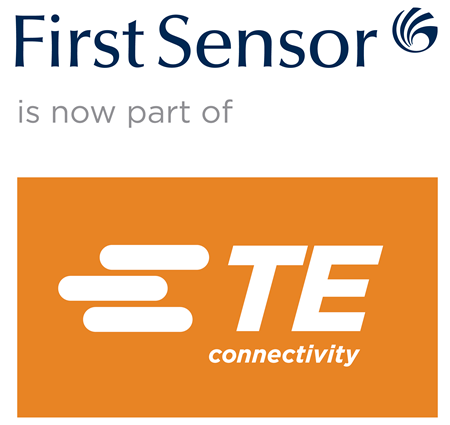
This information has been sourced, reviewed and adapted from materials provided by First Sensor AG.
For more information on this source, please visit First Sensor AG.