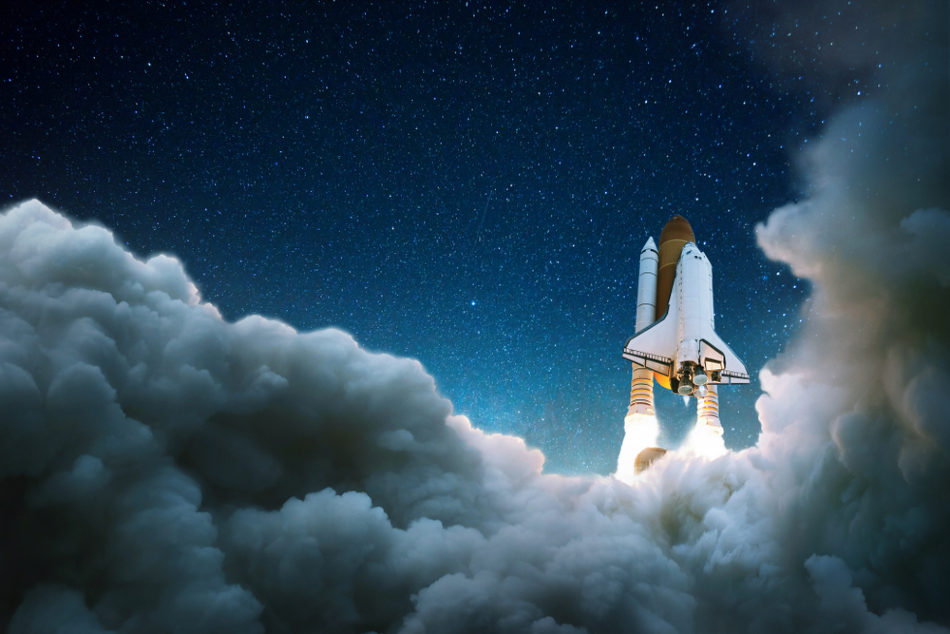
Image Credit: Alones/Shutterstock.com
There have been many recent advancements in space exploration, such as SpaceX being the first privately owned company to transport astronauts to the International Space Station (Wattles, 2020). These advancements increase the need for safer, more durable materials for space exploration and general vehicle design.
Spacecraft are typically coated with advanced polymer composites to increase flexibility, ease of processing, as well as mechanical and thermal stability. Although these factors prove valuable in achieving mission goals, polymer composites become damaged when exposed to harsh environmental elements. These include constant exposure to intense UV radiation, atomic oxygen, and collisions with space debris causing cracks in the coating (Zhu, Cao, Chen, and Wu, 2019). These factors threaten the flight safety of the spacecraft.
How can Flight Safety be Improved with the Use of Self-Healing Materials?
Flight safety is drastically improved when self-healing materials are used in spacecraft.
Self-healing materials repair damage to themselves without human intervention and mimic the properties of biological systems.
Biological systems intrinsically possess a healing ability, replenishing tissue by clotting damaged areas to prevent the loss of further material and then carrying out the healing process.
Self-healing systems are split into intrinsic and extrinsic methods. The intrinsic methods are based on dynamic covalent non-covalent bond interaction (Xu, 2012).
The extrinsic self-healing method follows two main design outlines:
- The hollow tube approach or the use of vascular systems: This involves running a network of hollow channels called vascules through the material to reinforce the tensile strength of the material. The process involves filling the channels with highly attractive bonding monomers or hardening agent. When the material is damaged, the cracks are propagated through the material, causing the hollow tubes to open and release the monomers. The monomers mix and create a bond with the damaged sections. The hardening agent solidifies the mixture and rebuilds the material. The monomers and the hardening agent can continually be replenished from external sources, making it suitable for static structural purposes. This design outline makes it possible for healing to occur repeatedly as more reacting agents can always be introduced. The hollow tubes can also be used to monitor the structural health of the material (Xu, 2012).
- The capsule-based system: This process involves the use of microcapsules distributed across the material. The healing agent is encapsulated in a substance that ruptures under a specified threshold when damage occurs. Once a capsule is broken, the previously encapsulated monomers mix with the catalyst, and the healing compound is distributed around the damaged area. This allows for the polymerization reaction to occur without the need for external heat. Researchers have proposed a UV -responsive micro-capsule based system to self-repair cracks on spacecraft coatings (Zhu, Cao, Chen and Wu, 2019). It uses UV-responsive microcapsules and Tio2 nanoparticles, and a polymeric shell.
The microcapsules are ruptured when damaged, releasing the healing agents. The unbroken bonds around a damaged area are broken down by the UV radiation in space. The healing agent made up of epoxy silicon and cationic photoinitiator is first released due to the rapid degradation rate of the polymeric shell (Zhu, Cao, Chen and Wu, 2019). In this case, the reaction is activated by stimuli from an external force and UV radiation.
How Has Our Understanding of Self-Healing Polymers Developed Over Time?
How can Self-Healing be Applied to Different Industries?
The uses of self-healing materials vary across different fields. It is most commonly used as a protective coating on products to enhance durability when micro-cracks in products result in mechanical degradation.
The potential for future uses of self-healing materials can be observed in the commercial aviation field, with several companies pushing for commercial supersonic flight.
As an aircraft approaches the speed of sound, the effects of air friction and the formation of shockwaves become more prevalent. The use of self-healing materials on these aircraft will improve its structural integrity during flight.
Its applications also go beyond functionality purposes. Many companies use self-healing materials such as anti-scratch coatings for aesthetic purposes.
The first self-healable anti-smudge coating has been developed, with an estimated 80% reduction in production cost by the City University of Hong Kong.
These anti-smudge coatings are capable of rapid self-healing and liquid repulsion. They work based on the use of oligomers capable of dynamic cross-linking and assembly assisted by hydrogen bonds (Network, 2020). The mechanical property of the polymer can be tuned via the aggregation of H-bonds, while the molecular weight can be also be modified.
References and Further Reading
Network, Q. (2020) World’S First Self-Healable, Coating Developed By Cityu Can Enhance Medical And Aerospace Equipment - QS WOWNEWS. [Online] QS WOWNEWS.
Xu, T. (2012) The Advance in Self-healing Scheme of Polymeric Materials. Journal of Material Science & Engineering, 01(02). Available at: https://www.hilarispublisher.com/open-access/the-advance-in-self-healing-scheme-of-polymeric-materials-2169-0022.1000e101.pdf
Zhu, Y., Cao, K., Chen, M., and Wu, L. (2019) Synthesis of UV-Responsive Self-Healing Microcapsules and Their Potential Application in Aerospace Coatings. ACS Applied Materials & Interfaces, 11(36), pp.33314-33322. Available at: https://doi.org/10.1021/acsami.9b10737
Wattles, C. (2020) Live Updates: SpaceX Attempts To Launch Its First Manned Spaceflight. [Online] CNN. Available at: https://edition.cnn.com/business/live-news/spacex-launch-today/index.html [Accessed 28 May 2020].
Disclaimer: The views expressed here are those of the author expressed in their private capacity and do not necessarily represent the views of AZoM.com Limited T/A AZoNetwork the owner and operator of this website. This disclaimer forms part of the Terms and conditions of use of this website.