Key Issues
- Optimization of reaction conditions for product formation
- Chemically reactive environment
- Replaces slower on-line chromatography method
Introduction
Methyl chlorosilanes are essential raw materials, used in the production of polyalkylsiloxanes - the basic ingredient of silicone rubbers and silicone oils. One of the primary methods used in the commercial production of methyl chlorosilanes, (referred to as the direct process) involves a reaction between methyl chloride and elemental silicon.
This particular reaction generates a mixture containing a wide range of compounds, including simple methyl chlorosilane compounds, a selection of Si–H– containing compounds (for example, Me2HSiCl, MeHSiCl2 and HSiCl3), and simple chlorinated compounds (for example SiCl4 and MeCl4).
The main product in this mixture is dimethylchlorosilane, which is utilized in the formation of polydimethylsiloxanes. While other methylchlorosilanes can be used as raw materials, reaction conditions will normally be optimized in order to maximize the dimethylchlorosilane yield.
The reaction mixture and compound are separated via distillation. All the materials present are liquids which boil in the range of 26–71 °C, other than methyl chloride, which is a gas.
The reaction products must be monitored during the reaction itself and throughout the distillation process to guarantee optimal dimethylchlorosilane formation.
The conventional approach to this monitoring involves the use of gas chromatography, however, this method does have its weaknesses. It is not fast enough for optimum control, taking between 20 and 60 minutes per analysis. The instrumentation also needs a high level of maintenance, due to the prevalence of material corrosivity.
Raman spectroscopy offers a practical solution for the provision of feedback, often delivering results in under five minutes. It is able to provide spectral differentiation of the key ingredients, offering a wide dynamic range while delivering the necessary sensitivity, as low as 100 ppm for key components.
Reaction Summary
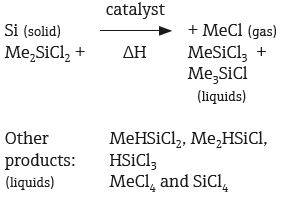
Experiment
A key benefit of employing Raman spectroscopy in chemical process reaction monitoring is that fiber optics can be used to separate the spectrometer and the point of measurement.
As such, the spectrometer can be situated in a non-classified area, for example, within the control room or within a purged analyzer house. In the example outlined here, the spectrometer was located in a standard NEMA-4 enclosure which had been rated for use in a NFPA Class 1, Division 2 environment.
The Kaiser Raman Analyzer functions with a frequency doubled 532 nm Nd:YAG laser. Gas chromatography (GC) data was used to calculate the response factors for the specific Raman bands. In instances where the total number of components is known, the band intensities are normalized and the composition is calculated from the sum of the components, assuming there is a constant response.
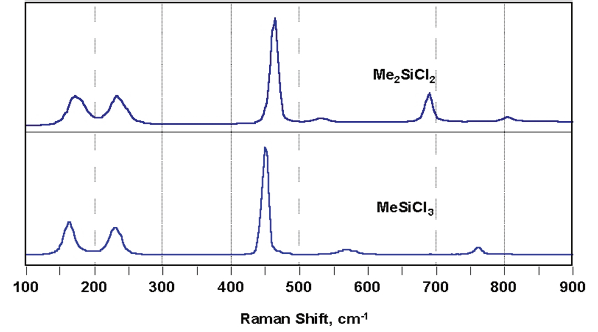
Figure 1. Example spectra of chlorosilanes. Image Credit: Kaiser Optical Systems, Inc.
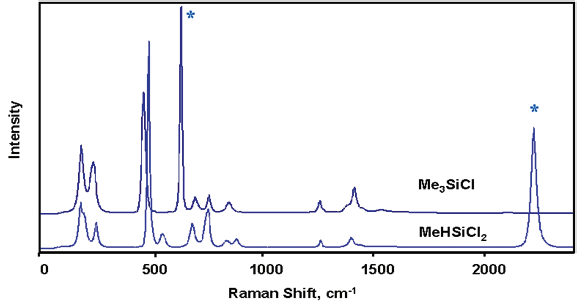
Figure 2. Comparison of chlorosilanes with and without Si-H. Image Credit: Kaiser Optical Systems, Inc.
Results
Figures 1 and 2 display example spectra for a selection of key reaction components. The spectra of the chlorosilanes, while similar in terms of their general appearance, are adequately differentiated to allow measurement of each component with no need to use additional multivariate modeling (chemometrics).
These compounds provided an exceptionally strong Raman signal, allowing the spectra presented to be acquired within a few seconds. The Si–H–containing compounds are characterized by the hydride band near 2200 cm–1.
Using fiber optic probe coupling meant that it was possible to switch monitoring locations within the process. Three of the streams investigated in this example showed some sort of abnormal behavior, and this was reflected in the measured composition of either major and/or minor components.
A five-minute data sampling rate was chosen, and this gave the users information on relatively short-term fluctuations taking place in all three streams. These perturbations are most likely linked to instability in the distillation column during start-up, or another event occurring taking place during the distillation or reaction.
As outlined above, GC’s longer measurement time does not provide the temporal resolution necessary to adequately monitor these changes. Figure 3 presents an example of a monitored variation, along with a a stream containing effectively two components: MeHSiCl2 and Me3SiCl.
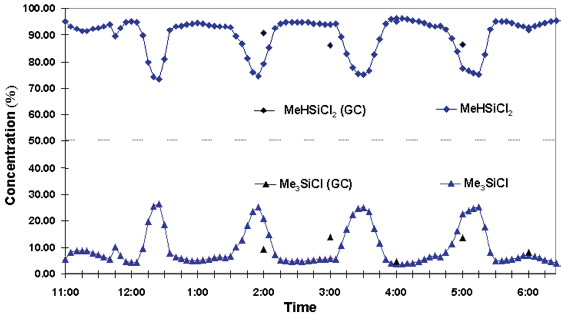
Figure 3. Process anomalies monitored by Raman. Image Credit: Kaiser Optical Systems, Inc.
These components exhibit a cyclic change in relative composition throughout a seven-hour period. This took place during a recycle phase of the process, during which material from the bottom streams and column overhead was sent back to the distillation column.
This is a genuine phenomenon of the process as shown by the exact mirroring of concentration profiles. It should be noted that the chromatographic method of measurement would be too slow to identify these events.
Conclusions
Raman reaction monitoring offers distinct advantages which are clearly demonstrated with the examples above. Here, the key issues were the remote monitoring of a corrosive and chemically reactive environment, the need to acquire rapid measurements, and the opportunity to monitor various streams in the process.1
In the latter instance, the Kaiser Raman Analyzer’s ability to offer convenient multiplexing is a considerable advantage. Raman monitoring was able to provide information on changes in the distillation and/or reaction process as they happened, offering sensitivities in the 100–1000 ppm range.
References
- Lipp, E.D. and Grosse, R.L, “On-line Monitoring of Chlorosilane Streams by Raman Spectroscopy,” Applied Spectroscopy, Vol. 52, No. 1, January 1998.
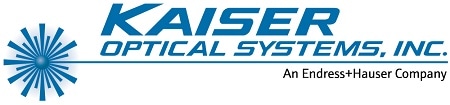
This information has been sourced, reviewed and adapted from materials provided by Kaiser Optical Systems, Inc..
For more information on this source, please visit Kaiser Optical Systems, Inc..