Today, with the rise of global culinary innovation, flavor is more important than ever. As a result, the industry has seen a notable increase in production of differentiated, flavor-infused products.
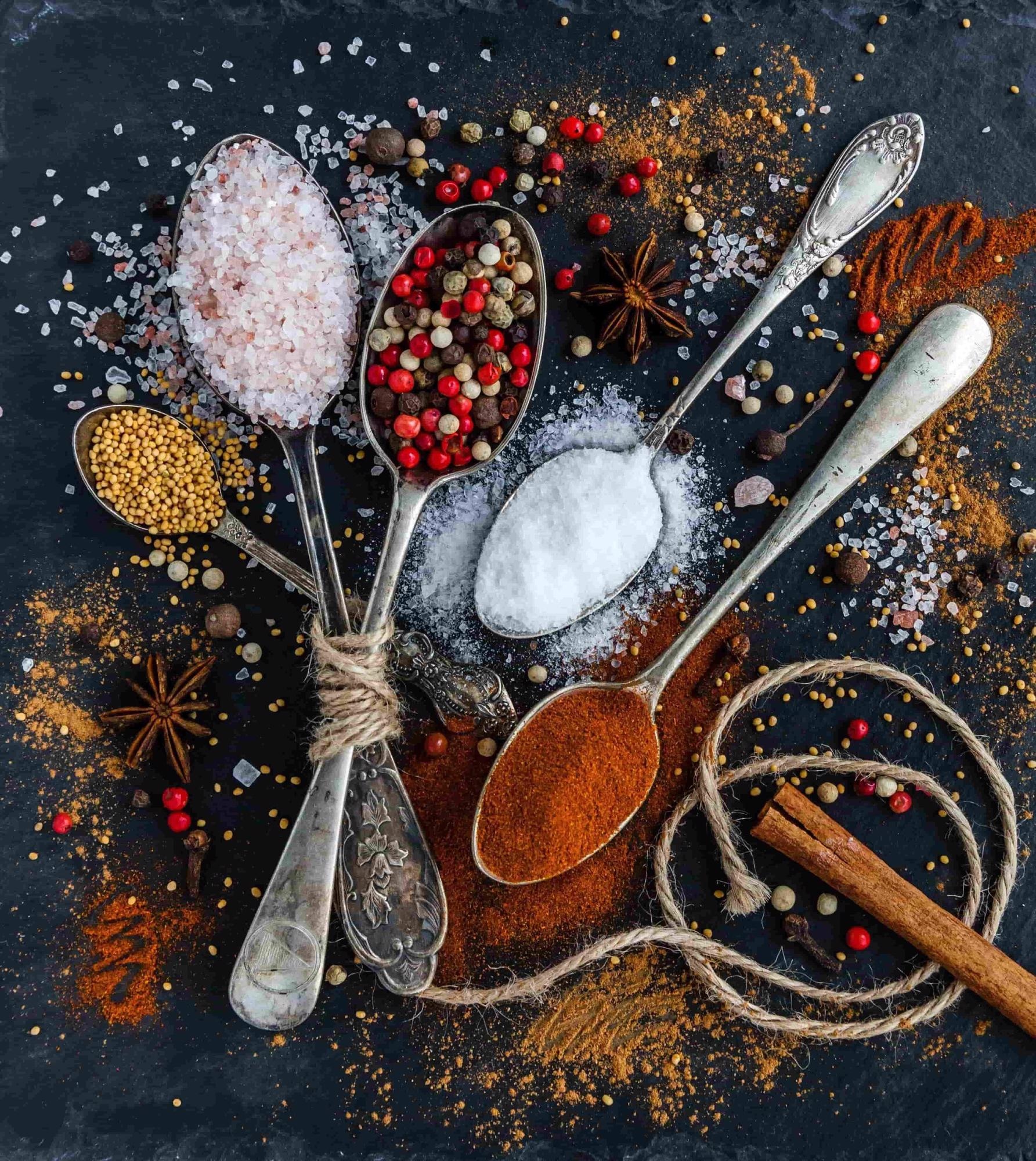
Image credit: Pall Corporation
In part driven by a younger generation’s gastronomic curiosity, flavor manufacturers are continuing to develop innovative products to meet demand in order to distinguish themselves.
Flavor houses also need to consider implementing process efficiencies that save time and prevent product loss, along with increasing the diversity of flavor profiles.
Are Traditional Filtration Methods Fit for Purpose?
In order to achieve the perfect flavor, exceptional filtration is required in order to remove particles that could risk spoiling the final taste and flavor and to ensure a clear final product. Filtration products with filter-aids are often used to accomplish this and implemented in plate and frame systems.
Diatomaceous Earth (DE) is most commonly used in sparkler filters as a filter aid. DE is comprised of ancient skeletal remnants of microscopic plants and provides an excellent filtration medium, thanks to its low resistance to flow and high pore volume. It must be noted that there are also disadvantages to using these methods.
This process can be both labor-intensive and time-consuming, resulting in drawbacks like insufficient final product quality requiring the reprocessing of the oils through to plugging of filters and the time taken to replace filters.
Naturally, this then requires manufacturers to explore options that will streamline their operations, which can, in turn, offer them numerous additional benefits.
Improving Process Time and Product Yield in Flavor Manufacturing
Filtration solutions that have high-flow capacity, and therefore a higher throughput are advantageous in cutting down processing time. A solution that has high-flow therefore increases throughput, which reduces process time.
One example of this is offered by Pall SUPRApak™ technology, which provides a unique high-area pack design called ‘edge-flow.’ Edge-flow provides a great contact time of fluids with filter media.
SUPRApak modules overcome the disadvantages of conventional sparkler filtration methods thanks to their new flow configuration known as ‘edge flow,’ which gives rise to a longer contact time of fluids with the filter media.
The edge flow technology has been reported to significantly reduce process time by an average of 87%, thanks to its excellent surface filtration and adsorption capability. This efficiency results in a productivity increase of 700%.
One-step single pass filtration removes the need for most filter aids and sparkler filters, along with rapidly speeding the process: the SUPRApak module filter changes take just three minutes, which is approximately three times faster than other methods.
SUPRA modules improve product yield in addition to helping production processes. A fully enclosed installation with low product hold-up volume, the SUPRApak system offers numerous filtration advantages.
The housing can be pressurized with gas at the end of filtration in order to empty the remaining fluid and consequently limit product losses. Any amount of material saved by leveraging SUPRA technology helps manufacturers minimize product loss, and in turn, save money, given the high cost of ingredients used in flavors.
Benefits Beyond Process Improvements and Product Yield
SUPRApak modules offer manufacturers both process time reduction and higher product yields, as well as addressing a few key challenges faced by other flavor producers. Other benefits of SUPRApak technology include:
- Thanks to the low frequency and ease of SUPRApak module change-out and cleaning, the product offers reduced labor and process downtime
- Reduction in waste and elimination of filter aids ensures sustainability improvements
- Thanks to the enclosed system, SUPRApak offers an improved product, personnel and environmental protection
Flavor houses simply must adapt in order to meet consumer demand at a moment’s notice and create unique flavors to dominate the market. Manufacturers with the right filtration solutions can not only
meet demand by accelerating the total production volume, but do so in an efficient manner.
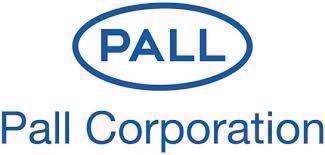
This information has been sourced, reviewed and adapted from materials provided by Pall Corporation.
For more information on this source, please visit Pall Corporation.