Could you give our readers an introduction to Verder Scientific and MICROTRAC?
Verder Scientific has over a thousand employees in 22 locations around the world. The company sets the benchmark in terms of R&D and high-tech quality control solutions.
The company supports analytical laboratories, research organizations and innovative manufacturing businesses in a wide range of application areas such as heat treatment, particle characterization, elemental analysis, sample preparation and hardness testing.
Verder Scientific’s companies can provide considerable gains to an organization’s processes, sustainability, results and profit margins.
Verder Scientific’s individual member organizations have decades of experience in their respective fields. Their collective expertise and knowledge offer customers significant benefits.
What materials are frequently encountered in the battery industry, and how have the preparation processes for these changed over time?
Batteries can be found everywhere, from planes, tools, boats and cars to mobile phones and medical devices. The battery market is predicted to grow to over USD 80 billion in the coming years.
It is essential to initially outline the main components of batteries. Their raw materials include electrode foil and graphite powders. The electrode manufacturing process involves slurry mixing, coating, drying and calendaring.
The electrode foil containing the graphite is slit and cut before the cell assembly process. Lithium-ion batteries usually include two electrodes (the anode and the cathode) and a separator.
Pore and particle size analysis is beneficial in characterizing the battery’s raw materials and the pore structure of the anodes, cathodes and separators.
Battery materials for cathodes often include lithium nickel cobalt aluminum oxide, lithium iron phosphates, lithium nickel cobalt manganese oxide and specially enhanced lithium nickel oxides.
The anode materials often comprise activated carbons with conductive additives, natural or artificial graphite, lithium compounds such as lithium titanate, niobium-based anode materials, and surface-functionalized silicon.
The separator materials usually comprise nylon, porous polyolefin films or cellophane. Polymers possessing semi-crystalline structures are widely used in nickel batteries, for example, polypropylene and its blends.
As battery costs are decreasing, their performance continues to increase.
The UK Advanced Propulsion Centre predicts a reduction in cost from approximately $130 USD per single kilowatt-hour now to $130 USD per 50 kilowatt-hours by 2035. Average energy density is projected to grow from 700 watts to 1400 watts.
A significant development concerns the use of additive manufacturing for the production of electrodes. This permits the creation of complex structures with greater electrode efficiency.
This approach is facilitating increased battery power density, while other factors such as battery safety, temperature management, working life, recyclability and predictability are expected to improve.

Image Credit: cigem/Shutterstock.com
How does MICROTRAC's particle sizing technology support the ongoing optimization of battery materials?
MICROTRAC offers an array of different techniques appropriate for use with a range of particles sizes.
CAMSIZER instruments can analyze particles ranging from 0.8 microns up to 135 millimeters, and static image analyzing systems can work with particles from 0.5 microns to around 1500 microns.
The SYNC system is an advanced laser diffraction unit, and a range of combined laser diffraction and dynamic image analyzers are also available.
For very small particles, the NANOTRAC series can analyze particles ranging from 0.01 microns (10 nanometers) up to 4 millimeters, which is an enormous size range. These systems can measure dry and wet particles.
Different analysis algorithms are offered, including the Fraunhofer approximation for particles over ten microns and the Mie evaluation for the smaller sizes. Raleigh scattering can be utilized for the smallest particles with very weak signals where it may be required to use dynamic light scattering.
Could you provide an overview of the core features of the MICROTRAC range of particle analyzers?
MICROTRAC’s laser setup is unique. Verder’s particle analyzers utilize a three-laser system. Laser number one is always a red laser; lasers two and three can be blue or red. Despite the complex setup and powerful detectors, the system is usually small in size.
The pioneering adapted Mie scattering technique does not require access to the imaginary refractive index. It can gain access to the refractive index straight from the system’s databases, which reduces the risk of measurement errors.
The system utilizes a 5.2-megapixel camera capable of accommodating 22 to 60 frames per second, enough to visualize several particles utilizing the same cell in the same run at the same time.
Over 30 different size and shape parameters are offered, including lengths, widths, circularity, aspect and area equivalent diameter.
To successfully use light scattering, a particular amount of small particles - around 2% or more – are typically required to facilitate the detection of oversized particles. Verder systems remove this necessity and can operate with exceptionally small amounts due to their unique blended algorithm.
The sample cell - which is where the measurement takes place - is supported by both an off-axis and on-axis detector.
The detectors deliver a wide range and can detect 151 channels, covering a huge detection angle. The systems’ docking station can facilitate dry and wet delivery systems, as the strobe light supports the camera. All these features are built into a single analyzer.
The TurboSync dry dispersion system features trays where the sample can be placed before being sucked into the system by a vacuum. The system also uses compressed air for dispersion.
The FlowSync dispersal unit delivers wet dispersion via a dispersion bath. The bath has an ultrasonication probe that can pump and circulate the material.
Traditional analysis via laser diffraction does not always permit oversized particles detection where a small tail – around 100 microns – is present. Such oversized particles can lead to shorts inside the electrodes, having a negative impact on their efficiency.
Verder Scientific’s unique blended algorithm can address this as it can combine diffraction and imaging, decreasing the possibility of false peaks, permitting a precise determination of particle size.
How does Mercury Intrusion Porosimetry work as a measurement tool for pore size and pore volume?
Mercury intrusion porosimetry is perfect for measuring the pore size and volume of porous bodies.
The measurable pore size for this technique ranges from about 3.6 nanometers to 1 millimeter. Despite this wide range of pore sizes, it is feasible to carry out a precise measurement in about 45 minutes and less than that for quality control applications.
Verder’s mercury intrusion porosimetry systems range contains the BELPORE LP, MP and HP. The BELPORE LP is a mercury filling and measurement device perfect for working with macropores, and pressure ranges up to 450 KPa.
While the BELPORE MP and HP are similar, their main difference lies in the size of the sample cell. As the BELPORE MP has a larger cell volume, it can measure up to 228 MPa, and the BELPORE HP can measure up to 414 MPa.
Each system can measure up to 20,000 data points and includes advanced safety features; no gas or liquid nitrogen is required. Each system can operate out of the box and is an efficient, intuitive application that is perfect for pore characterization.
The range of common applications of mercury intrusion porosimetry includes the analysis of the separators and electrodes in batteries, as well as catalysts, resins, porous oxides, polymers and ceramics.
Mercury intrusion porosimetry is based on the fact that mercury is a liquid but is non-wetting. Pressure is applied to press the liquid mercury into the pores, and the smaller the pore, the higher the pressure needed.
Utilizing the Washburn Equation, the pressure, surface tension, contact angle and pore size can be utilized to establish the amount of mercury that was introduced into the pore, giving the pore volume.
The BELPORE LP can be used on pore sizes from around 1 millimeter down to 3.33 micrometers. The BELPORE MP can work with pores up to around 6.5 nanometers.
The application of double pressure would yield half of the smallest pore size, allowing detection down to 3.6 nanometers, while these techniques can only detect accessible pores.
A range of sample holders are available, depending on the sample type under analysis, such as powders and solid materials. The system includes an autoclave which is built to accommodate very high pressures.
A mercury siphon facilitates the recycling of mercury, helping to make the fullest use of resources.
A standard BELPORE LP workflow commences with the deployment of a vacuum pump to achieve a vacuum. This opens the proportional valve, letting a second pump introduce the mercury in this line.
Once filled, the proportional valve is shut, and pressure is applied - utilizing a simple air pump - to measure the region up to 450 KPa and to establish the size of the macropores.
The BELPORE MP and HP facilitate the transfer of the sample load to an autoclave before low pressure is applied using a hydraulic system or high pressure is applied using a pressure multiplier.
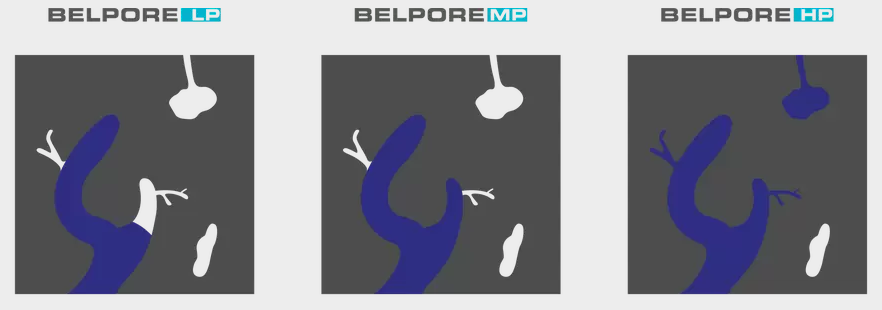
Image Credit: Microtrac
Please elaborate on how the PoreInspect software coordinates and interfaces with these systems?
The PoreInspect software includes a user-friendly interface that can operate up to four instruments via LAN: these instruments can be measured in real-time.
The mercury’s intrusion curves may need to be adjusted to account for compressible material. Utilizing this software, it is possible to adjust the intrusion curve, record compressibility and acquire values for the compressed volume and bulk models.
The software can be employed in the investigation of the pores of cathodes and anodes with smaller pore sizes in the range of hundreds of nanometers. It can also be utilized to investigate membranes and separators.
About Dr. Jürgen Adolphs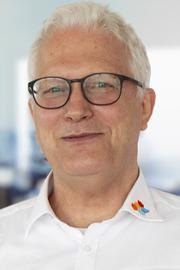
Dr. Jürgen Adolphs studied Physics and Mathematics at the University of Göttingen with a diploma thesis about engine acoustics (VW). Afterwards he changed to Building Physics and Materials Science in Civil Engineering at University Duisburg-Essen and received his PhD in Theoretical and Physical Chemistry about Sorption Modelling. Research activities followed in the USA at Northwestern University Evanston ILL., Advanced Cement Based Materials Center, Argonne ILL. Synchrotron Facility and NIST Gaithersburg SANS. In 2001 he started at Porotec GmbH, a company specialized on the equipment for the characterization of porous and particular materials. In 2010 Jürgen became co-owner and CEO until 2020 when Porotec GmbH was acquired by Verder Scientific and integrated into Microtrac. Jürgen is author of more than 60 publications and active in DIN and ISO committees. As the head of the application center in Haan and sales director for surface and porosity analysis Jürgen states: “Microtrac stands for customer focused solutions with the best equipment and optimal scientific and technical support.”
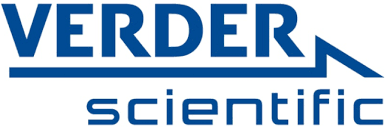
This information has been sourced, reviewed and adapted from materials provided by CARBOLITE GERO Ltd.

For more information on this source, please visit Microtrac.
Disclaimer: The views expressed here are those of the interviewee and do not necessarily represent the views of AZoM.com Limited (T/A) AZoNetwork, the owner and operator of this website. This disclaimer forms part of the Terms and Conditions of use of this website.