Interview conducted by Olivia FrostSep 6 2022
To become an ideal thermal fluid user, it is important to formulate a best practice guide on how to be a more effective, efficient, and responsible use of thermal fluid systems. This is not just for the operators of the system but also extends to plant managers, engineers, decision-makers, procurement folks, and anybody that is a stakeholder in the fluid system in operation.
Paratherm has compiled a ‘wishlist’ of attributes that they believe a thermal fluid user should obtain. This wishlist is essentially a source of knowledge passed down from thermal fluid experts based on the experience of decades of dealing with this specialized industry, thousands of phone calls, hundreds of site visits, hours and hours of lab research, troubleshooting, and benchmarking, and provides a summary of some of their best practices.
In this interview, Ryan Ritz, the Global Director of Technology at Paratherm Heat Transfer Fluids, talks to AZoM about how you can become an ideal thermal fluid user.
Can you provide an overview of what thermal fluids are?
In some industries, thermal fluids, or heat transfer fluids or HTF'S for short, are referred to as hot oils or thermic or thermal oils, but regardless of what they are called, the basic technology and the advantages of thermal fluids is the fact that they are able to generate high operating temperatures at low system pressures.
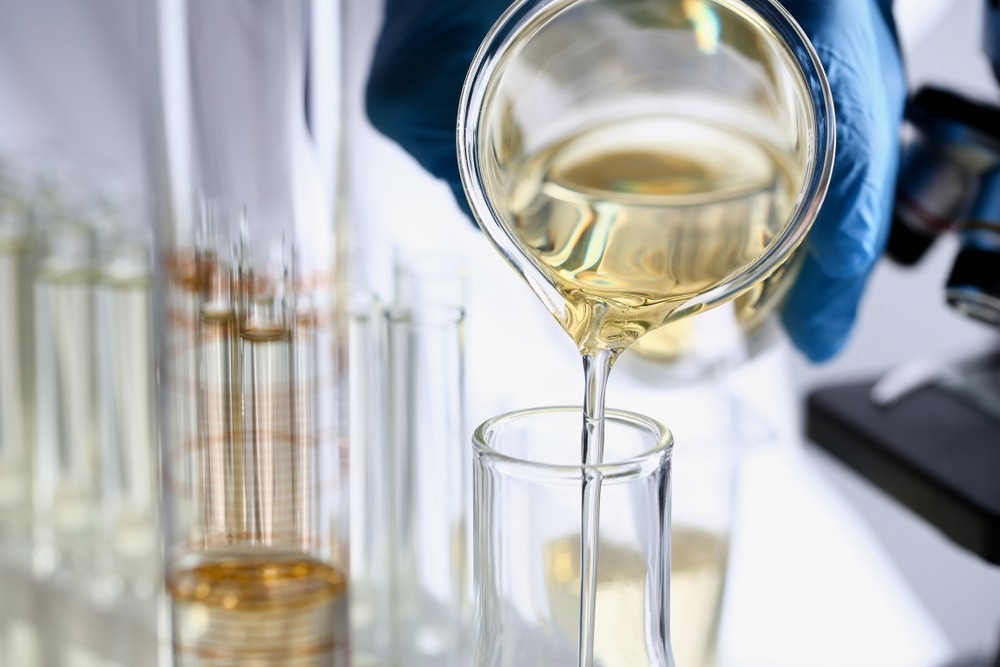
Image Credit: ShutterStock/H_Ko
High system pressures need more maintenance and have a greater number of safety issues. For example, with steam-fired systems and direct heating, there are many high-pressure points, hotspots or localized overheating. Thus, this technology was developed to create a more efficient, consistent operating temperature capability across the entire system without generating really high system pressures.
What are the main areas of focus when developing the main components of a thermal fluid system?
To answer this question, I will focus on hydrocarbon-based heat transfer fluids. By that, I am referring to natural, organic-based fluids or what you might refer to as mineral oil-based formulations, and then also synthetic-based fluids.
When it comes to a closed loop system and the main components of a thermal fluid system, one of the main points to consider is the heat source, which could also be a cooling source: that could be a fuel-fired heater, an electrically fired heater, or a waste heat recovery type system.
Regardless of the main heat source that is supplying the energy to the fluid, the heater, the system is going to be the main area of focus. From there, you have heat transfer fluid possibly running through a coil, and that is pumped through a pipe: the circulating pump.
You have to have a circulating system in order to get efficient heat trans fluid. So in a closed loop system, a circulating pump is what enables the fluid to move. Fluid flow is key for efficient heat transfer. In short, flow rates and temperature settings go hand in hand with the performance of the system.
Another crucial component is the expansion tank. As mentioned, heat transfer fluids are designed to achieve high operating temperatures in the system without increasing the pressure of the system too much, and the expansion tank is the reason that this is able to happen.
Essentially, the expansion tank maintains a closed loop in the system, but it is open to the atmosphere to allow pressure relief as the fluid volume increases with heat.
How do these components work together to prevent downtime, ensure safer operation, and preserve the longest possible lifetime of both the fluid and the equipment in use?
To ensure ideal performance, it is essential to consider the impact of the thermal fluid and the thermal fluid operating system on your overall operation. This is crucial as this is regarding a be high-temperature fluid that operates in an environment where it will have an impact on the safety of the people at the plant.
It will thus have an impact on equipment investments and, most importantly, on the efficiency of your overall operation.
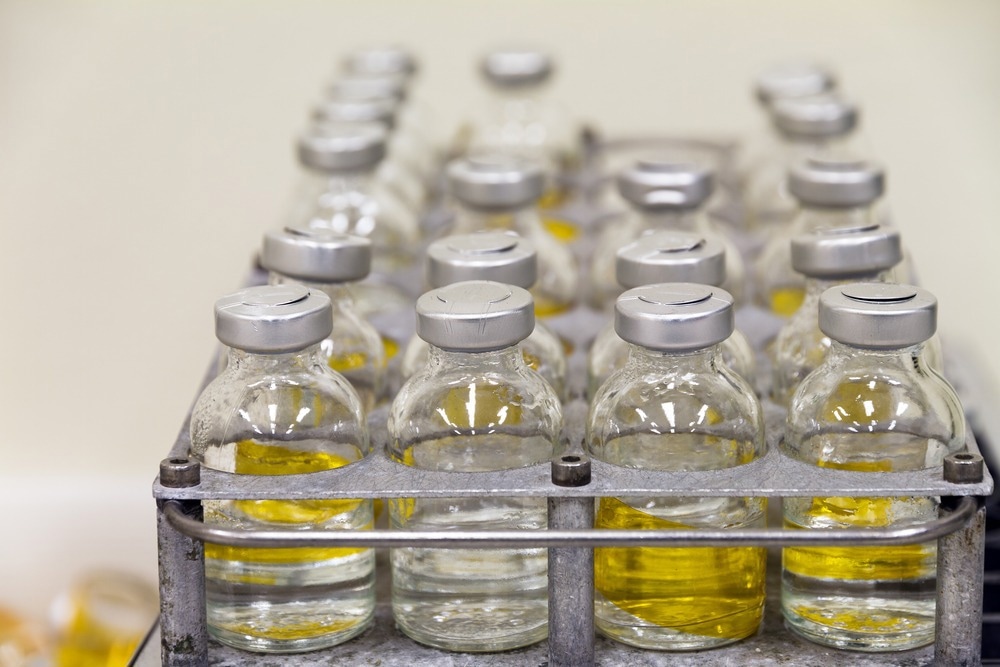
Image Credit: ShutterStock/Dennis van de Water
Therefore, if you have a heated operation that is not being run as efficiently as possible, you are not only losing out on your energy costs, but you are also going to be prematurely degrading the fluid, putting unnecessary wear and tear on the equipment, the pumps, the inside of the heater, creating a downward spiral and ultimately influencing production downtime.
One of the great things about heat transfer fluids is that they are designed to be a safer and lower maintenance alternative to other heating applications.
What challenges or issues do users typically come across during operations?
Most of the problems that end up happening at a customer site or in any operation are because the system is essentially set up and forgotten about. As the fluid is so low maintenance, it is forgotten about until problems start to arise, and then when a problem does arise, it is a very serious problem that can impact the safety of the equipment.
This, in turn, means that the entire system needs to be shut down, leading to losses in production time,
Thus, it is worth investing in the thermal fluid system to avoid those downtimes, run a more efficient operation and protect the investment and, ultimately, the people.
What impact does fluid selection have on operation?
The wrong fluid, which is not referring to a brand but rather the type of fluid, can be a catalyst for accelerated degradation, leading to equipment failures, increased maintenance, decreased efficiency, and causes safety problems.
When in operation, it is essential to follow the design specifications. A lot of time, money and effort has been put into designing this technology, so staying within those operating specs is important. If you fail to adhere to those basic maintenance practices, it can lead to some serious irreversible damage to the fluid and the equipment.
Of course, the primary concern is safety. When running a proper operation with the correct fluid within the specs, these are safe, low-maintenance operations. However, the inherent dangers increase exponentially when these factors are taken for granted.
What action needs to be taken then to ensure the correct procedures are being followed?
Design and operate with safety factors that agree with the design specifications. Make sure that you have the proper safety equipment. Identify potential hazards, look for leaks, smoke, and centralized overheating areas and make the corrections. It is better to raise a red flag, and it turns out to be nothing than do nothing, and it turns out to be something.
Appreciating and understanding the impact means that you have taken the time to understand the technology.
You really need to make sure that you understand the design features of the equipment; you need to know what the equipment does, the main aspects, know why or how a system heats up, know what the purpose of each piece of equipment is, know the features of the fluid, and what makes one fluid more advantageous to have than another.
It is also important to note what makes a good fluid versus a fluid that is going to lead to problems down the road, and part of this comes from understanding how fluids break down. If you know how the fluids degrade and what the degradation products are, that will really be an advantage for you as it will enable you to prevent the fluid from degrading as much as possible.
Additionally, it is important to make sure all responsible stakeholders, operators, maintenance, personnel, and plant engineers go through the proper training on the fluids and the equipment itself. Make sure everyone’s trained ahead of time and keep up with that training. Set a realistic budget and plan ahead.
How can users ensure they have a good fluid?
You want to make sure that the fluid you choose meets your operating specifications with a safety window. You do not want to have something that is going to be operating at the upper recommended point. Take a look at your operating specifications, and find a fluid that optimizes those specifications.
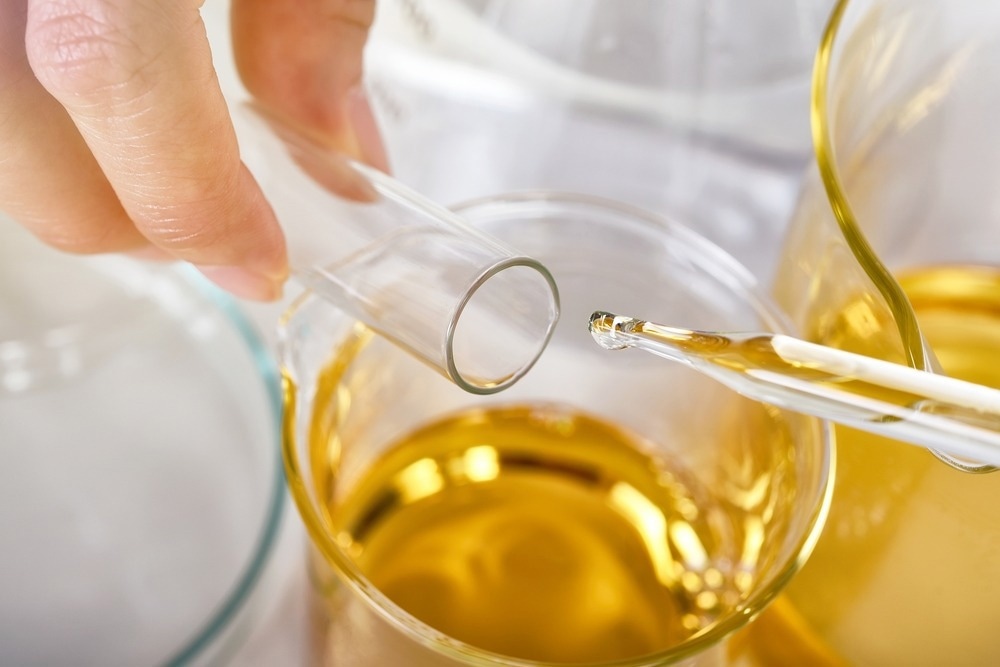
Image Credit: ShutterStock/ARTFULLY PHOTOGRAPHER
For your equipment design, certain fluids are better in certain types of equipment. You want to make sure you choose the right fluid to optimize your budget. Understandably, there are some fluids out there that are very high performing that might be out of your budget.
That does not mean that you need to go to the lowest possible denominator to fulfill that need. So again, the important parameters are to appreciate the impact, set a realistic budget, and use a fluid that was designed for the equipment in use – such as a fluid with high purification, a fluid that features high heat transfer efficiency, and a fluid that has high thermal stability.
What are the differences between natural hydrocarbon-based heat transfer fluids and synthetic hydrocarbon-based heat transfer fluids?
Natural organic hydrocarbons are generated from a crude oil refining process. The generic term for the base of these chemistries is mineral oil. They are usually non-toxic, efficient, and cost-effective, but the maximum operating temperature is really limited to usually somewhere between five and 600 degrees Fahrenheit.
So if you are operating at or above those limits, you will need to consider something a little bit more robust in a synthetic product.
Importantly when dealing with natural organics, quality and purification are critical. Color is really important. So when selecting a fluid, it is sometimes as simple as looking at the color of the fluid as physical appearance can be a really good initial indicator of whether the right product is being used.
Highly refined, specialized engineered products are well worth the added costs because they tend to still be within budget, and the dividends that they are going to pay down the road are going to be really high. They are also going to have higher stability and better performance.
On the other hand, synthetic organics-based chemistry is specifically formulated from chemical synthesis. These tend to have very high Thermo stability.
They can offer you temperatures above 650 degrees max operating temperature, but there are some limitations with these products because they are typically derived way down the road from some kind of benzene-based chemistry that gives them their ring structure, molecular structure, and the double bonding that gives you better stability.
The trade-off, however, is that they come at much higher costs, and sometimes there are some environmental impacts. When considering the upper operating temperatures that a synthetic product will give you, it is also important to consider the limitations that shipping, storage and the environment can have on the fluid.
As such, the cost is usually a lot higher for synthetic hydrocarbon-based heat transfer fluids.
What are some of the other fundamentals to consider when making a fluid selection?
Maximum operating temperature and minimum operating temperature are also really important considerations. The climate and the environment that you’re in also need to be considered because that is going to determine your minimum start-up temperature.
So check those boxes, and make sure that the fluid not only meets your maximum operating temperature but also what the actual process user needs and what the outlet temperature of the fluid is going to be.
The closer you are to that maximum operating temperature that the fluid supplier recommends, the less life the fluid is going to have in the long term. The user should also ensure that the fluid can be pumped and efficiently heated at whatever the minimum start-up temperature will be.
Moreover, suppose you have an existing fluid system or an existing system that you might have drained out or refilled. In that case, you want to make sure that you are not putting in an incompatible product with what was there before.
Never put water into an oil-based system, for instance, but also, you might not want to mix synthetics with mineral oil-based products. You really need to take that into account and talk to your fluid supplier before you make that decision.
As mentioned previously, the selected fluid can have an immense impact on your operation. It is not just about the fluid itself; it is also about when that fluid and inferior fluid breaks down as it can affect the equipment, causing more wear and tear on the pumps and the heater and the pipes and the integrity of the metal and the valves. Therefore it is crucial to take that total life-cycle cost analysis into account choosing the fluid.
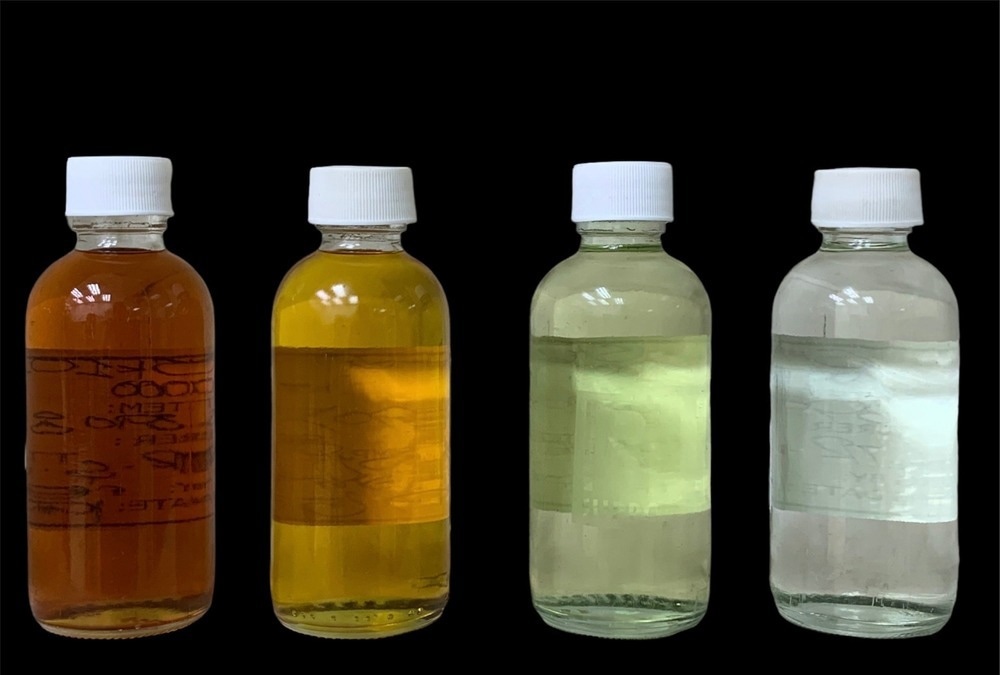
Image Credit: ShutterStock/kajeab_pongsiri
An engineered fluid, on the other hand, takes the fluid chemistry and balances the primary factors (thermal stability, key transfer efficiency, product purity).
There are three key primary performance factors to thus take into account, the first being high purity. You want to make sure that the fluid that you are using is able to stand up to the temperatures that you have and the additives or impurities left from the crude lower refining process, or if something is formulated with way too many additives, those impurities are going to fall out onto the surfaces and cause problems.
Thus, you want to make sure you are specifying a high purity product and are paying attention to the SDS.
Color is also particularly important, particularly for a mineral oil-based product. The purity level can really be indicated by color. Anything that is really tinted with color is going to show one of two things; either way, too much additive has been put into that formulation, or the fluid itself was not taken to purification levels and distilled out in its production phases.
Finally, high efficiency should be considered, and this is calculated using the thermal properties of the fluid and the operating conditions.
A more efficient heat transfer fluid or thermal fluid will feature a great mix of low viscosity, high density, high thermal conductivity, and high specific heat capacity.
What recommendations would you give our readers to ensure a good life cycle?
Suppose a fluid that you are specifying or considering does not have a great mix of low viscosity, high density, high thermal conductivity, and high specific heat capacity available across the entire temperature range that you might be considering. In that case, the odds are that fluid was not intended to be a heat transfer fluid or a thermal fluid.
For a fluid formulator or a fluid designer to actually design and create a new fluid, they would have to make sure that they test it around all of those factors to give you a more efficient fluid, so make sure you insist on that data, see if they have it, and use that as an indicator or qualifier to determine if it is a reputable supplier or not. Then check the thermal stability. This can be done with a lab test (ASTM D6743).
You can essentially test all the key properties of the fluid by putting a stress test on two fluids that you are trying to compare. A fluid with high stability will last longer and will require less maintenance over time.
Once the appropriate fluid has been chosen, what are the start-up procedures?
Once the proper fluid has been selected, you want to make sure you that the system is clean to start with; you want to make sure that there is no moisture in that system and that nothing water-based was introduced into it.
Starting with a clean system is really important, but once the system is filled, following the procedures from the equipment manufacturer and the fluid manufacturer, you want to make sure you start up properly.
When fluids are colder, they have a higher viscosity, which means that they are going to stick to the walls of the pipe more; thus, as the surfaces begin to heat, the fluid will break down faster on the pipe walls.
So a low temperature, more biscuit, fluid is not thermally efficient. If you put a lot of temperature and heat energy onto that cold fluid right away, you are going to shock the fluid and crack the fluid onto the heated surfaces. So you want to make sure that you start up slowly, not letting the heater go into high fire until the fluid reaches what we call turbulent flow turbulent flow.
Once the fluid has reached turbulent flow, it means that the flow rate is good enough to remove the fluid and get it moving. Turbulent flow usually happens around 180 degrees Fahrenheit.
Moreover, when shutting down the system, you need to make sure that the pump and heater are not shut off at the same time because then you have fluids sitting inside of a hot heater box baking into the fleet heater; keep the main circulating pump running after the heater is powered off.
What are some of the red flags to look for during operations?
Firstly, if you hear sounds or see gauge ratings that are off, that is something you should act on, or at least raise the issue up higher and then talk to an equipment manufacturer or talk to your fluid supplier.
Your differential pressures are going to show you the flow rate between your heater in the inlet and outlet. If that pressure changes, then there is something inhibiting the flow through the heater that can cause cracked heater tubes, which can ultimately cause problems down the road.
The exhaust stack temperature is another important consideration because the heat not going into your fluid is going out of the exhaust stack. If exhaust tax temperature starts to rise over time, that is energy that used to go in the fluid and is no longer doing that; it is going out into the atmosphere: that is also a red flag.
I would also advise users to record their readings, monitor report changes, know the signs of degradation and get their fluid analyzed.
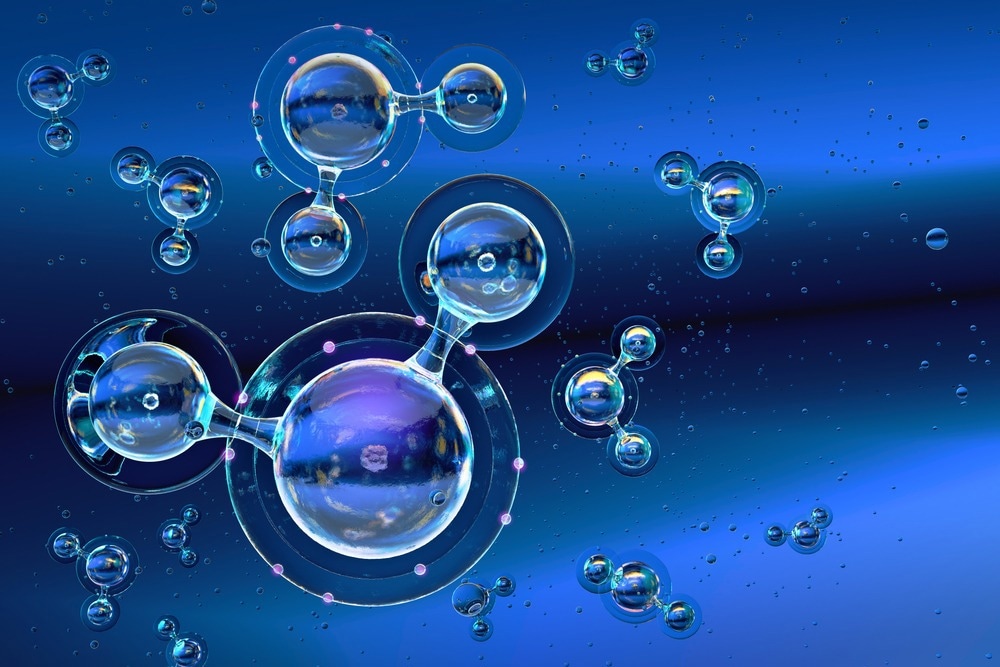
Image Credit: ShutterStock/Corona Borealis Studio
If red flags are ignored or not dealt with in the appropriate manner, issues can arise. For instance, when the design of the fluid is not working properly, you might see thermal cracking or overheating. This breaks the molecular bonds, generates low boilers, carbon solids, and reduces heat transfer. You always want to make sure you operate inside your design specs.
Oxidation is when a hot fluid is exposed to air - increasing fluid viscosity, sledge formation, and elevated temperatures in the expansion tank are usually the cause. Look at your hotspot inside your heated source and take a look at inside that coil. If you do not have proper flow or you have got other issues going on, you have an inferior fluid. The heat is not going to go out into the system.
Instead, the energy is going to be used to break the molecular bonds. When the molecular bonds of the fluid break, they create carbon fouling or carbon solids onto the walls of the heater. That creates an insulation layer that blocks the heat from getting to the bulk of the fluid. If you have that heat being blocked to the bulk of the fluid, it’s going to then build up more and more and more.
What course of action would you recommend when encountering these issues?
First, raise the red flag and take action against it. The next ideal thermal fluid user aspect is implementing a consistent PM program and regular housekeeping. The fluid degradation over time is going to happen no matter what fluid you are using or how great your system is. However, this does not mean that we cannot control it to a certain extent. The goal is to minimize the rate at which it happens.
So ensure that your fluid is not specked right up to what your operating temperature is going to be - leave a degree of safety there, leave room for error because if you increase the fluid 18 degrees over its max bulk temperature, you will cut the life of the fluid in half.
To prevent oxidation, keep the expansion tank below 150 and never enslave the outside of the expansion tank. You can do that by putting it in an inert gas blanket. That is another super user tip. If you cannot keep the fluid in the tank below 150 degrees, installing a gas blanket to displace the oxygen inside that tank, but without really affecting the pressure and still giving you that safety feature, will be important.
Are there any good housekeeping practices you would recommend?
Keep things labeled - this includes ensuring that when you keep your drums or containers of fluids stored in an area that is going to take on moisture, the labels on those drums are clear.
Fluid analysis is also really important. Fluid analysis should be carried out at least once a year. Fluid analysis is the most reliable tool for keeping your system running at an optimum level and avoiding unexpected problems. You should be getting this as a preventative maintenance practice annually, but also after any major changes, such as if the fluid is being added in and out.
As an ideal user, you should always be looking for red flags. If things change to the point where it is a concern, call your thermal fluid supplier - maybe getting a fluid analysis will help alleviate some of that stress or justify the fact that your red flag was actually there.
That being said, make sure that the fluid analysis that you are getting on your thermal fluid is specific to thermal fluid or heat transfer fluid. We often see people getting fluid analysis done on a lube oil provider because it is easier to send all your fluids out to the same lab.
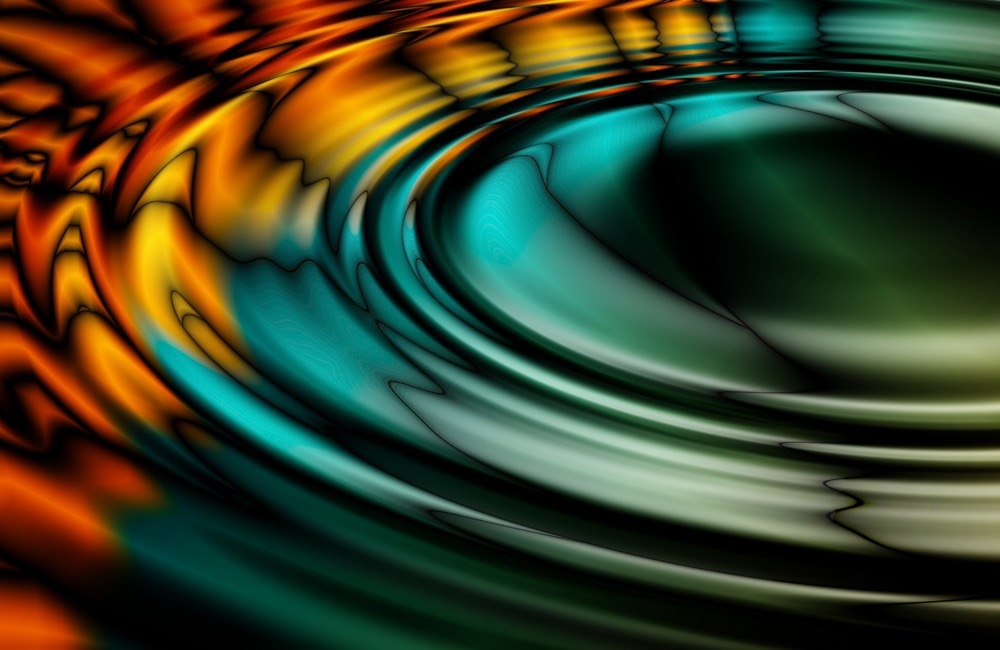
Image Credit: ShutterStock/Michael Zysman
They may be similar tests and ASTM methods, but the condemning values for a thermal fluid and any other kind of industrial oil could be very different. You want to ensure that you are dealing with somebody who is testing based on those values, specific to the thermal fluid system and not just any other industrial oil.
If you use a reputable supplier, they will be able to set you up with good testing capabilities, which is a really important thing. You want to make sure you have a full report of your condition, such as expert recommendations, not just the values and if it is condemned or not.
There are a lot of gray areas when condemning thermal fluid. It depends on the temperatures that you are running, the cycles you are running, how long the fluid has been in there, and what it looked like three years ago versus what it looked like last year to this year.
A lot of stuff can happen in that time period. So you want a verbal review of your results. You also need a plan of action, and you need to be able to work with a reputable supplier for that.
In short, some of the main things to consider should be the scheduling of regular equipment inspections with your equipment manufacturers and having them review what is going on. Follow their PM programs. Uphold that strict fuller analysis program once a year as a minimum and insist on an in-depth review of the results or recommendations.
It is also essential to maintain good records of volumes. Whatever the initial fill was, keep records of your maintenance activities and your fluid analysis reports. This goes a long way for helping us troubleshoot when problems arise, and always consult with your equipment and fluid experts on any changes, concerns, or red flags you see. Never compromise on that service support.
About Ryan Ritz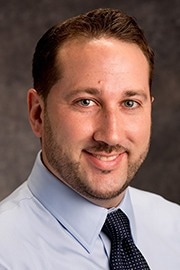
Ryan Ritz is the Global Director of Technology at The Lubrizol Corporation’s Paratherm Heat Transfer division (King of Prussia, PA). Mr. Ritz has been working with high-level technical aspects and the industrial application of heat transfer fluids since July 2003. His experience has been focused on strategic positioning, practical functionality, product formulation, R&D, used fluid testing, technical service, sustainability, sales & marketing, and laboratory management.
He formally presents his expertise on thermal fluid technology to global audiences on a frequent basis and has authored multiple technical articles that have been featured in trade publications for chemical processing and oil/gas-related industries. Ryan holds a Bachelor of Chemical Engineering degree from the University of Delaware. He resides in Havertown, PA with his wife and their two young daughters.
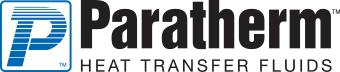
This information has been sourced, reviewed and adapted from materials provided by Paratherm.
For more information on this source, please visit Paratherm
Disclaimer: The views expressed here are those of the interviewee and do not necessarily represent the views of AZoM.com Limited (T/A) AZoNetwork, the owner and operator of this website. This disclaimer forms part of the Terms and Conditions of use of this website.