What is Mechanochemistry, and why is it advantageous over solvent-based alternatives?
Chemical reactions are typically classified based on the way the energy for the reaction is supplied. The most common types of reactions are thermal (energy supplied by heating), electrochemical (energy supplied by electrical current) and photochemical (energy supplied by optical waves).
A less known form is mechanochemistry, where the energy is supplied by impact and shearing forces, typically produced by ball mills that are used to conduct those reactions.
With mechanochemistry, it soon became clear that some reactions are conducted faster and thus are energy-saving compared to the classic solvent-based chemistry.
Furthermore, problems like poor solubility of the educts can be overcome by mechanochemistry, even reactions can be forced, which is simply not possible in solvents, or intermediate substances can be stabilized and purified, which is not possible in solvent-based reactions.
What are the environmental and sustainability advantages of this field?
A major benefit of mechanochemistry is that the reactions are conducted solvent-free. This makes the process environmentally friendly and safer to handle. The final product is automatically free of residual solvents. Research to find the most suitable solvent for a certain reaction is also not required.
In some cases, mechanochemistry enables comparably simple processes to produce new materials – whereas the synthesis of the same products with solvent-based processes is complicated and time- and energy-consuming.
Furthermore, higher yields in the reactions can be achieved with mechanochemical processes – which also influence the total energy consumption.
What are some of the challenges associated with Mechanochemistry?
Scientists had to re-evaluate parameters of “classical” chemical reactions, like concentration and temperature, when transferred to a ball mill, as these are different in a solvent-free environment. They were confronted with new parameters such as milling time and volume ratio.
The different influences are still under investigation, as it is not yet clear what really drives the mechanochemical reactions.
Is it the energy supplied by the impacts – and is more energy input always beneficial? Is it creating fresh surfaces by the balls, which can react simultaneously, with mixing effects? Or is it also the comparably high concentration of educts in contrast to soluble systems? High temperatures between the balls when they collide? Or a mixture of all?
How is Retsch addressing these challenges?
To gain more insight into these questions, Retsch partnered up with scientists from the Ruhr University Bochum and the Technical University Braunschweig and started a DFG (German Research Foundation) project in 2020 called “What drives reactions in ball mills? Qualification and Quantification of the forces in mechanochemical reactions”.
Here Retsch is involved in ongoing discussions about the current state of mechanochemistry, supports scientists with equipment, and picks up ideas for the development of machines and accessories.
Retsch has entered into various international partnerships to address the questions in the field and to find the most suitable as well as user-friendly solutions to put the possibilities of mechanochemistry to full use.
What are planetary ball mills, and how are these used in Mechanochemistry?
In planetary ball mills, the grinding jars are arranged eccentrically on a so-called sun wheel. The direction of movement of the sun wheel is opposite to that of the grinding jars (ratio 1:-2 or 1:-2.5 or 1:-3 in special versions for mechanochemistry, generating higher energy input).
Additionally, the grinding balls inside the grinding jars are subjected to superimposed rotational movements. The difference in speeds between the balls and grinding jars produces an interaction between frictional and impact forces, which releases high dynamic energies.
The interplay between these forces results in a high and very effective degree of size reduction. Conventional ball mills use the gravitation field for accelerating the balls whereas Planetary Ball Mills use the centrifugal field of a rotating sun wheel to achieve typically 40 times of the gravitation field.
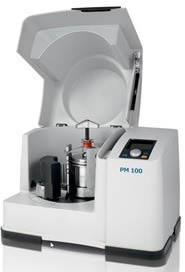
Figure 1. Planetary Ball Mill PM 100. Image Credit: RETSCH GmbH
Ball mills allow for precise control of the reaction conditions, variable energy input, and the possibility of conducting reactions in sealed vessels. In contrast to mixer mills, planetary ball mills work predominantly with many grinding balls per jar and thus with increased frictional forces.
The local energy input between the balls is less than with impact forces. Nonetheless, the high friction results in good mixing and the creation of fresh surfaces of the particles – which in turn, is one factor to drive some chemical reactions.
For research questions, it is easier to address systems with one single ball inside the jar (e.g., for the calculation in predictive simulation models). Mixer mills are beneficial in this case.
What are the benefits of Mixer Mills for mechanochemical applications?
Mixer mills work mainly by impact and are originally designed for quick, uncomplicated size reduction of small sample amounts of up to 20 ml but are also commonly used in mechanochemistry.
The grinding jars of mixer mills perform radial oscillations in a horizontal position. The inertia of the grinding balls causes them to impact with high energy on the sample material at the rounded ends of the jars and pulverize it. The movement of the jars, combined with the movement of the balls, results in the intensive mixing of the sample.
As previously mentioned, some chemical reactions require the frictional forces of a planetary ball mill, whereas other reaction types need energy input by impact – this is where mixer mills come into the picture. Another benefit is the ease of use of these mills, together with the option to work with small sample volumes in the R&D field.
Mixer mills also offer some unique benefits over planetary ball mills: The use of transparent jars together with the typical horizontal jar movement allows the use of in-situ RAMAN spectroscopy.
Here, the reaction process can be observed in time, for example, to determine the processing time where a maximum yield is achieved. This avoids unnecessarily long process times.
The most interesting benefit of mixer mills is the option to cool or heat the jars and, thus, control the chemical reaction.
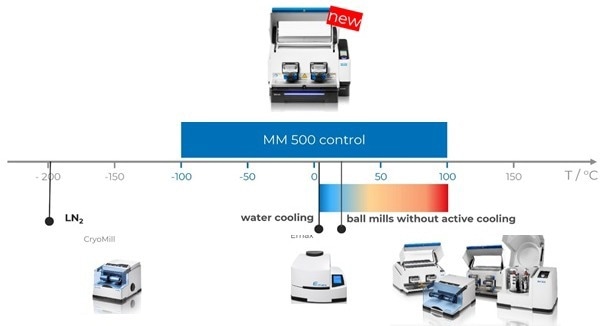
Figure 2. Retsch Ball Mills: The CryoMill is used for constant cooling at very low temperatures of -196 °C, the High Energy Ball Mill Emax offers some cooling options. Planetary Ball Mills and Mixer Mills do not provide any active cooling or heating options. The MM 500 control can be operated in a range -100 °C to + 100 °C with exceptional options to control and influence the temperature. Image Credit: RETSCH GmbH
How has Retsch further developed the benefits of mixer mills, like cooling and heating options?
Retsch has developed a series of mixer mills with different specializations, among them the CryoMill, which constantly cools the sample inside the jar to -196 °C, which is useful if temperature influences the reaction process.
For mechanochemical applications, the new MM 500 control is the most interesting mixer mill. It offers the option to operate in a temperature range from -100 °C to +100 °C.
By cooling the sample throughout a mechanochemical process, the formation of undesired derivatives can be prevented. It is also possible to apply heating, for example, to initiate chemical reactions and increase product yields.
Mixer Mill MM 500 control - Introduction #RETSCH #mixermill #laboratoryinstruments
Video of Mixer Mill MM 500 control. Video Credit: RETSCH GmbH
How could mechanochemistry technology improve in the future?
Today, scientists in this field work on understanding the factors influencing chemical reactions in small reaction vessels. The more options that are available to control the reaction (e.g., temperature regulation or energy input), the clearer the picture of how it really works in a specific case will be.
The use of grinding balls as a catalyst to enhance the reaction is also a topic of research. The next steps will therefore address improved control options like a wider range of temperature control, new accessories and enhanced techniques to supervise the reactions.
Once the processes are understood and the yields are optimized, the key will then be to upscale the process so that it can produce larger amounts of materials to replace classic solvent-based, non-eco-friendly processes.
The reactions driven in a Ball Mills can be transferred to a larger drum mill for upscaling reasons with some adaptations, of course. Here new questions have to be solved.
About Dr. Tanja Butt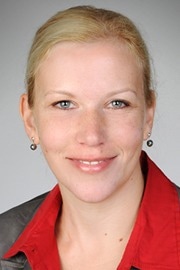
Dr. Tanja Butt studied Biology at the University of Duesseldorf, Germany, and graduated with a Diploma in Biology. After that, she earned her Ph.D. in biotechnology at the Forschungszentrum Juelich, Germany. Later, she worked in R&D and project management for different institutions. She joined Retsch in 2013 as Product Manager for the whole milling and sieving product range.
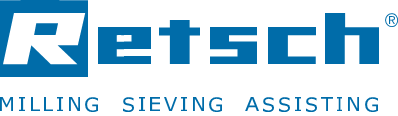
This information has been sourced, reviewed and adapted from materials provided by RETSCH GmbH.
For more information on this source, please visit RETSCH GmbH.
Disclaimer: The views expressed here are those of the interviewee and do not necessarily represent the views of AZoM.com Limited (T/A) AZoNetwork, the owner and operator of this website. This disclaimer forms part of the Terms and Conditions of use of this website.