The manufacturing industry has experienced a major transformation due to the emergence of additive manufacturing, commonly known as 3D printing.
This process enables the creation of metal or plastic components by building them up layer by layer, in contrast to the subtractive method that involves carving a part out of a larger material.
The ability to produce intricate shapes with tight tolerances using techniques such as direct metal laser sintering (DMLS) and electron beam melting (EBM) has opened up new design opportunities that were either not possible or prohibitively expensive using traditional subtractive methods.
Additive manufacturing also offers a cost-effective and efficient method for creating prototypes. The need for specific tools and expensive production runs is eliminated, resulting in less waste and a better cost ratio, especially for one-off or small-batch production.
However, the transition from prototyping to reliable manufacturing has presented several challenges for 3D printing, especially in the metal additive manufacturing field.
Here, powder bed fusion is utilized to manufacture complex shapes for sensitive applications such as medical devices that are implanted in the human body or aerospace components that are critical for use in flight. The failure of these components is simply not an option.
The Importance of Certification and Chemical Analysis
As with every other metal forming activity, the composition of the metal powder needs to be right for the final product to have the correct characteristics to not only meet specifications and avoid defects but also to comply with the applicable local and national statutory regulations.
However, understanding how to meet requirements, satisfy appropriate conformity assessment procedures and achieve the necessary certification is not always straightforward.
To ensure quality, each batch of raw powder should undergo rigorous testing procedures to verify chemical properties and uniform particle size distribution.
Despite extensive cleaning of the printer, the material mix may also cause products to be out of specification. Consequently, it is important to rely on the certificate of the powder purchased and verify its compliance with the specification after 3D printing.
Moreover, frequent recycling of powder through several printing runs may expose the process to external contamination, particularly when switching from one powder type to another.
Oxygen is a common source of contamination, and it can accumulate in the powder, affecting its chemical composition and material properties. The 3D metal printing process itself may also introduce defects within parts.
To prevent contamination of the finished part, it is critical to verify the raw powder before printing and check the composition of the finished product before shipping to reduce scrap rates, increase yield and fully capitalize on the benefits of additive manufacturing.
This is where Spark Optical Emission Spectroscopy (OES) can be an invaluable tool.
OES: An Established Technique for New Applications
Optical emission spectroscopy is an effective solution for measuring 3D-printed parts. This method of elemental analysis has been widely used for decades and is considered the most critical method for analyzing metals and alloys in the metallurgical industry.
Spark spectrometers, in particular, are utilized for quality control throughout the metal processing cycle, including the analysis of accompanying elements in scrap metals, incoming materials control, melting process control, and outgoing goods to fabrication.
As one of the highest turnovers and most labor-intensive industries globally, the iron and steel industry is of significant importance. The OE series, Hitachi's latest optical emission spectrometer range, is ideal for steel and ferrous material analysis.
The OE750, with its new detector technology, offers exceptional performance in metal analysis. It enables the analysis of ultra-low carbon steels, monitoring of nitrogen content in steel and iron casting processes, and determination of other trace elements.
Moreover, it provides dependable results for the most crucial alloying elements.
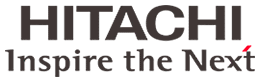
This information has been sourced, reviewed and adapted from materials provided by Hitachi High-Tech Analytical Science.
For more information on this source, please visit Hitachi High-Tech Analytical Science.