Materials engineering explores the fundamental chemical and physical principles behind the controlled combination of atoms to create new compounds, phases, and microstructures. It also involves the characterization of the resulting structures and properties.
The primary objective is to optimize the performance of a material for a specific design application by adjusting the structure, processing, and property relationship.
Materials Engineering (MATE) Department at California Polytechnic State University (Cal Poly), San Luis Obispo, is driving this effort. MATE is the only predominantly undergraduate materials engineering program among the 53 Materials Science and Engineering departments in the United States.
The MATE curriculum provides flexibility by offering a wide range of electives and allowing specialization in technical electives. MATE ensures its students gain extensive hands-on experience using cutting-edge materials characterization and testing methods.
These include dynamic mechanical analysis, optical microscopy and image analysis, hardness testing, thermogravimetric analysis, tensile testing, X-Ray fluorescence, metallographic image analysis, environmental scanning electron microscopy, Fourier-transform infrared spectroscopy (FTIR), and differential scanning calorimetry.
High-Resolution Microbalancing
These precision methods and technologies at MATE are supported by the need for high-resolution microbalancing. A microbalance is a tool designed to accurately measure the weight of small-mass objects on the scale of a million parts of a gram.
“We are conducting experiments on a wide variety of materials at MATE that require the use of high-resolution microbalancing,” says Trevor Harding, professor and chair of the Materials Engineering Department at Cal Poly.
“For example, right now we have researchers that are looking at magnesium oxide nanoparticles for carbon dioxide sequestration. They think they are synthesizing magnesium oxide, and they think they are sequestering carbon dioxide, but they really do not know that because they cannot see the particles, because these are nano-particles.
They are using a technique called FTIR to try to pick up magnesium carbonate signals in their samples, to determine if they are getting what they think they are getting from their synthesis.”
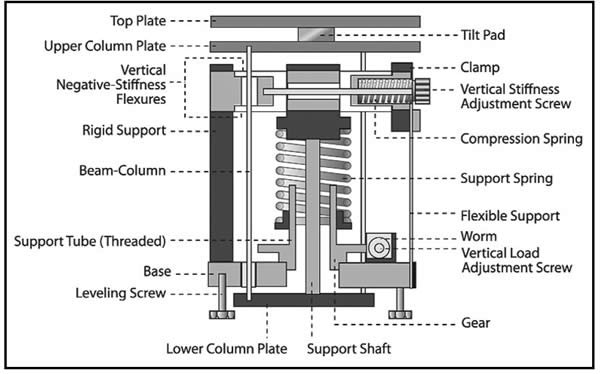
Schematic of a negative-stiffness vibration isolator. Image Credit: Minus K Technology
FTIR is a method employed to obtain an infrared spectrum of absorption or emission of a solid, gas, or liquid. An FTIR spectrometer concurrently gathers data with high spectral resolution across a broad spectral range.
When a sample is exposed to IR radiation, the sample absorbs some of the radiation, and some of the radiation is transmitted through. The subsequent signal at the detector forms a spectrum that serves as a molecular fingerprint of the sample.
Infrared spectroscopy is useful because various chemical structures (molecules) generate unique spectral fingerprints. FTIR excels in evaluating the compositions and chemistry of polymeric molecules, along with the molecular interactions of nanocomposites.
“To conduct this experiment looking for magnesium carbonate signals with FTIR you have to carefully measure out milligrams, and even micrograms of powder samples,” says Harding. “This is where high-resolution microbalancing is absolutely critical in making these very-high-resolution measurements of the mass for the samples, prior to doing the characterizations.”
The high-resolution microbalance holds significant importance as an accessory instrument for Cal Poly’s Material Engineering Department. It is also relatively sensitive and can be impacted by environmental vibrations, reducing the accuracy of its performance.
“Our whole department and most of our labs are on the second floor of the building,” adds Harding. “The heating and air conditioning system is on the roof directly above our floor, so there is much mechanical vibration coming through the floor, and within the surrounding structure.”
Negative-Stiffness Vibration Isolation
MATE opted for Negative-Stiffness vibration isolation, developed by Minus K Technology. Minus K Technology is an original equipment manufacturer (OEM) supplier of scanning probe microscopes, micro-hardness testers, and other vibration-sensitive instruments. The company’s isolators are employed by over 300 universities.
Negative-stiffness vibration isolators are compact and do not need electricity or compressed air. This enables sensitive instruments to be placed in various settings, such as a production facility, laboratory, or observatory. This extends to locations like basements, vibration-compromised upper floors of buildings, or rooftops.
These isolators do not contain motors, pumps, or chambers. No maintenance is needed because there is nothing to wear out. They operate solely in a passive mechanical mode.
Negative-Stiffness isolators are particularly advantageous because they achieve a high level of isolation in multiple directions. These isolators offer the flexibility to customize resonant frequencies to 0.5 Hz both vertically and horizontally, with some versions achieving 1.5 Hz horizontally.
Vertical-motion isolation is provided by a stiff spring supporting a weight load, coupled with a Negative-Stiffness mechanism. This results in a very low net vertical stiffness without compromising the static load-supporting capability of the spring.
Horizontal motion isolation is provided by beam columns connected in series with the vertical motion isolator. A beam column acts as a spring combined with a Negative-Stiffness mechanism.
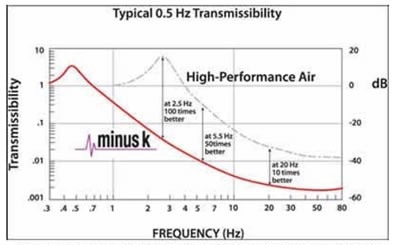
Transmissibility - Negative-stiffness isolator vs. air table. Image Credit: Minus K Technology
The outcome is a compact passive isolator with extremely low vertical and horizontal natural frequencies and very high internal structural frequencies.
Negative-Stiffness isolators exhibit outstanding performance, as indicated by a transmissibility curve. Vibration transmissibility is a measure of the vibrations that are transmitted through the isolator relative to the input vibrations.
Negative-Stiffness isolators, when configured to 0.5 Hz, demonstrate around 93 % isolation efficiency at 2 Hz; 99 % at 5 Hz; and 99.7 % t at 10 Hz.
“These vibration isolators have helped to ensure we are getting as exact results as possible from our microbalancing measurements,” concludes Harding. “We are very pleased with the resolution, and no longer are we concerned with vibration.”
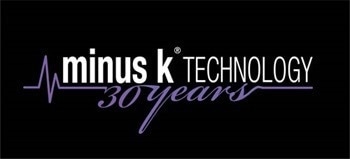
This information has been sourced, reviewed, and adapted from materials provided by Minus K Technology.
For more information on this source, please visit Minus K Technology.