Introduction Inhomogeneous packing structure in green body causes large defects in a sintered body, which govern the mechanical properties of ceramics products [1, 2]. The internal microstructure in powder compacts needs to be fully understood for the improvement of ceramics. Liquid immersion method (LIM) is a unique evaluation method of internal structure in the processing of ceramics. In this method, a green compact is made transparent with an adequate immersion liquid [3-7]. Internal structure in the alumina compact (Refractive Index, R.I. = 1.76) was observed by this method with diiodomethane as an immersion liquid (R.I. = 1.74). However, the LIM technique was believed to be inapplicable to ceramics with high refractive index, because no immersion liquid was available for those materials [8]. Recently, the limitation of the LIM technique was removed by using an infrared (IR) light microscope with wavelength 1.3 µm for Si3N4 (R.I. = 2.04) [9, 10]. IR microscope with the LIM technique (IR-LIM) is a powerful tool for the examination of internal microstructure composed from powders with high refractive index. The long wave light may also increase the transmittance through the powder compact, when the particle size in the compact is much smaller than the wavelength [9, 11]. The IR-LIM technique would be an effective tool for examining the internal structure of green compacts consisting of nano- powders with high refractive index. The object in this study is to examine the internal microstructure for a nano-powders compact with the IR-LIM technique. The material used in the present study is the system of yttria stabilized zirconia, whose ceramics have excellent mechanical properties including superplastic deformation [12, 13], and a high refractive index, n = 2.14. Experimental Procedure The raw material used in this study was commercial zirconia (TZ-3Y-S, Tosoh Co., Ltd., Tokyo, Japan, specific surface; 8 m2/g) of nanometer size particles. Compact were formed by die pressing at pressures of 10, 30 and 100 MPa and heated at a temperature of 900ºC for 1hr, for binder removal and also for enhancement of strength needed for handling. A thin sample with 70 µm thickness was prepared by grinding a small piece of specimen with fine sandpaper (No.1000) for observation. The immersion liquid used was a saturated solution of sulfur in diiodomethane, with the refractive index 1.79. This is a non-toxic liquid. The thin specimen was immersed in the immersion liquid and was evacuated for 5 min. The transmittance of the light for thinned zirconia sample was measured with UV-VIS-NIR Spectrophotometer (UV-3150, SHIMADZU Co., Kyoto Japan). The wave length was changed from 0.5 µm to 2.0 µm. The commercial IR microscope (Model BX50-IR, OLMPUS Co., Tokyo Japan) with IR camera (Model C2741, Hamamatsu Photonics K.K., Hamamatsu Japan) was used for observation. The maximum operating wavelength of IR camera was 1.8 µm. A filter was used to remove light with λ < 1.3 µm. The structures of the green compact were also observed with SEM. Results and Discussion Figure 1 shows SEM micrographs of the nano-powders of yttria stabilized zirconia. The primary particle size was about 100 nm or less. The particles have near equi-axed shapes. The primary particles appear to form secondary particles of the size a few tenth of micrometer. 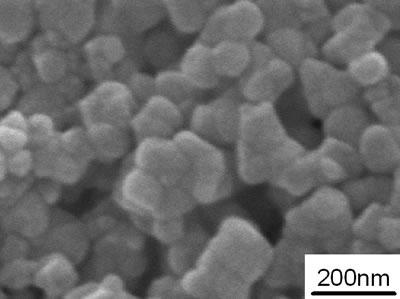 | Figure 1. SEM micrographs of the nano-powders of yttria stabilized zirconia. | Figure 2 shows SEM micrographs for granules of yttria stabilized zirconia. The granules have sizes under 100 µm and near spherical shapes. The spherical shape is often observed in granules made from flocculated slurry [11]. Each granule appears solid without a big void with the infrared light microscope. Figure 3 shows transmittance ratio as a function of the wavelength in the range of 0.5 µm to 2.0 µm. The thin sample used was pressed at 100 MPa and was prepared for the observation of internal structure. The sample was 70 µm thick and was soaked in the immersion liquid. The transmittance increased with increasing wavelength. This is understandable, for the size of the primary particles in the compact (100 nm or less) is much smaller than the wavelength, that is, the ratio of primary particle size to wavelength light is under 1/10. The high transmittance is attributed to the decreased Mie scattering. The result also indicates that infrared (IR) light penetrates easily into the zirconia sample with the immersion liquid by suppressing scattering at particle surface. In the long wavelength region, however, the transmittance did not increase much (about 10% or less), because the Rayleigh scattering starts to be dominant in the range of long wavelength (λ = 2 µm). 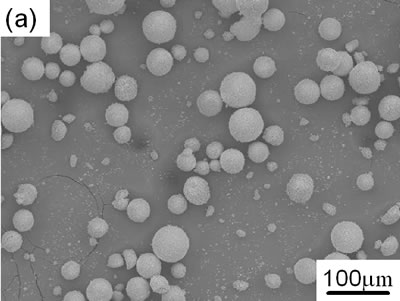 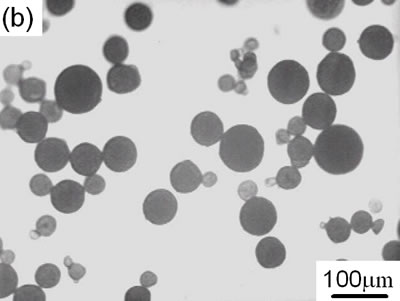 | Figure 2. SEM micrographs for granules of yttria stabilized zirconia. | 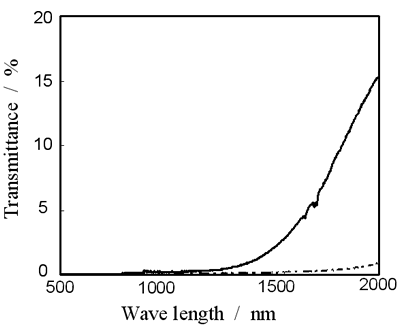 | Figure 3. Transmittance as a function of light wave length in the green compact of yttria stabilized zirconia prepared by pressing at 100 MPa. A solid line: with immersion liquid, a broken line: with no immersion liquid. | Figure 4 shows SEM and IR-LIM micrographs of the green body. These micrographs are taken from the direction perpendicular to die pressing. The fracture mode of the green body is mixed; trans- and inter- granular fracture were noted in the SEM micrograph. The structure is non-uniform; boundaries of granules are visible in some places. In the IR light micrograph, the granules are clearly visible in the green compact. The granules retain the spherical shape without being fractured at 10MPa in the compact. The inhomogeneous structure containing partially fractured granules should densify inhomogeneously in sintering, forming defects at interstices of granules. The structure in the present zirconia system was found to be similar to those observed in alumina [3, 4, 10] and silicon nitride systems [5, 9]. 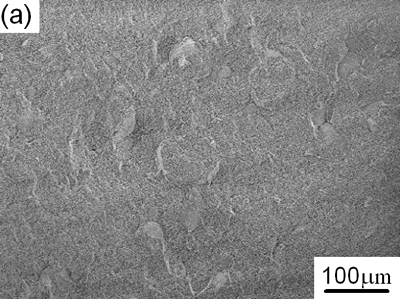 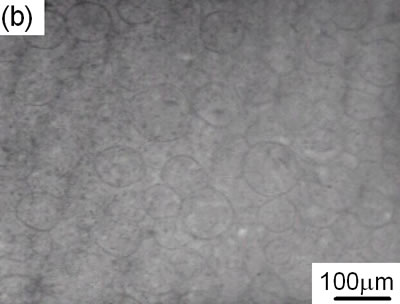 | Figure 4. Micrographs of green body made with die pressing at 10MPa. (a) SEM and (b) IR-LIM.. | Figure 5 shows the internal microstructure of the compacts pressured at 30 MPa and 100 MPa. Again, the interstices between granules remain as black lines in the sample pressed at 30 MPa. The granules have elongated shapes in the compact. The granules appear to more deformed in the green body pressed at 100 MPa. The shape of granules is still detectable and is more clearly seen than in the compact pressed at 10 MPa. 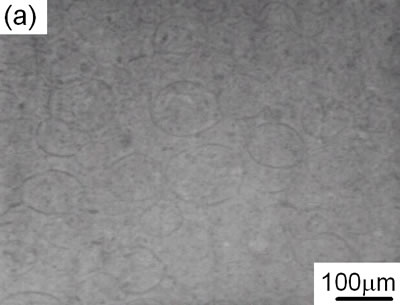 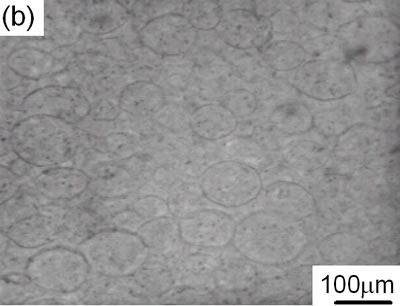 | Figure 5. IR-LIM images of the internal microstructure of the compact pressured at 30MPa and 100MPa. | Clearly, the transmittance of light through the compacts increases with increasing pressure and thus it is possible to observe the structure more clearly. This result suggests that the light is scattered by the pores at the interfaces of particles rather than the particles themselves. The suppressed pore size and/or pore volume reduces the scattering. The IR-LIM is again noted as a powerful tool for observation of internal structure in the green body consisting of nano-powder. Conclusions Infrared (IR) light microscopy with liquid immersion method (IR-LIM) has high potential to study the internal structure in the green compact with nano- powders. Even internal structure of high refractive index materials, internal structure in the green compact with nano powders was obtained by using infrared light. Change of granule deformation in the green compact with pressure is clarified with this method. This technique will be widely used to examine the internal structure of nano powder compacts. Acknowledgements This research was partly supported by a COE program Grant-in-Aid for Scientific Research from the Japan Ministry of Education, Culture, Sports, Science and Technology and Nippon Sheet Glass Foundation. References 1. W. D. Kingery, “Firing- The proof test for ceramic processing”, pp291-305 in Ceramic Processing before Firing, Ed. by G. Y. Onoda and L. L. Hench. Wiley, New York, (1978). 2. F. F. Lange, “Powder Processing Science and Technology for Increased Reliability”, J. Am. Ceram. Soc., 72 [1] (1989) 3-15. 3. K. Uematsu, M. Miyashita, M. Sekiguchi, J.Y. Kim, N. Uchida and K. Saito, “Examined with Immersion Liquid Technique”, J.Am.Ceram.Soc., 74 [9] (1991) 2170-74. 4. K. Uematsu, “Immersion Microscopy for Detailed Characterization of Defects Ceramic Powders and Green Bodies”, Powder Technology, 88 [2] (1996) 291-98. 5. H. Takahashi, N. Shinohara, M. Okumiya, K. Uematsu, J. Tsubaki, Y. Iwamoto and H. Kamiya, “Influence of Slurry Flocculation on the Character and Compaction of Spray-Dried Silicon Nitride Granules”, J. Am. Ceram. Soc., 78 [4] (1995) 903-908. 6. N. Shinohara, M. Okumiya, T. Hotta, K. Nakahira, M. Naito and K. Uematsu, “Formation Mechanism of Processing Defects and thier Relevance to the Strength in Alumina Ceramics Made by Powder Compaction Process”, J. Mater. Sci., 34 (1999) 4271-77. 7. K. Uematsu, H. Ito, S. Ohsaka, H. Takahashi. N. Shinohara and M. Okumiya, “Characterizatrion of Particle Packing in Injected Green Body”, J. Am. Ceram. Soc., 78 [11] (1995) 3107-109. 8. H. Ishikawa, Y. Zhang, N. Uchida and K. Uematsu. “Quantitative Evaluation of the Liquid Immersion Microscopy”, J. Ceram. Soc. Jpn., 104 [2] (1996) 133-36. 9. K. Uematsu, N. Uchida, Z. Kato, S. Tanaka, T. Hotta and M. Naito, “Infrared Microscopy for Examination of Structure in Spray-Dried Granules and Compacts”, J. Am. Ceram. Soc., 84 [1] (2001) 254-56. 10. K. Uematsu, Y. Saito and S. Tanaka, “Breakthrough in Evaluation for Packing of Powders”, Transactions of the Materials Research Society of Japan, 27 [2] (2002) 333-338. 11. K. Uematsu and M. Saito. “Liquid Immersion Technique Coupled with Infrared Microscopy for Direct Observation of Internal Structure of Ceramic Powder Compact, with Alumina as an Example”, J. Mater. Res., 14 [12] (1999) 4463-65. 12. F. Wakai, S. Sakaguchi and Y. Matsuno, “Superplasticity of yttria-stabilized tetragonal ZrO2 polycrystals”, Adv. Ceram. Mater., I (1986) 259-63. 13. M. J. Melendo, A. D. Rodriguez and A. B. Leon, “Superplastic flow of fine-grained yttria-stabilized zirconia polycrystals: constitutive equation and deformation mechanisms”, J. Am. Ceram. Soc., 81 (1998) 2761-76. Contact Details |