Imagine going for a picnic at the beach and taking some beers. Idyllic, you might think, unless you either (a) have to carry the heavy load of bottles or (b) drop the bottles and leave bits of glass all over the place. Which is why new safe and light PET bottles for beer could prove doubly attractive to outdoors drinkers, as well as for serving at music festivals and in clubs. With the rise in both indoor and outdoor leisure activities, such as music festivals and sporting events, and the growth of the club scene, traditional glass drinks containers that may break, or be broken can increasingly be seen as a safety hazard. On top of this consideration, our hectic modern lifestyles favour clean and safe packaging concepts with ‘grab and go’ and ‘consume on the move’ qualities. The resealable PET single serving container is suited to these needs, on top of which it weighs us down less when we're rushing around. Advantages The development of a clear, plastic, cost effective consumer package for oxygen-sensitive beverages has long been a technical and manufacturing goal of the packaging industry. PET bottles are typically one seventh the weight of an equivalent glass container, do not break or smash, and are already well established for carbonated soft drinks, particularly in the larger two and three litre sizes. PET has also, over recent years, taken a significant market share from glass and metal containers in the single serving size. Disadvantages The principal obstacle to the introduction of a PET container for beer is that PET is a bit of a gas ‘sieve’ when it comes to the permeation of oxygen and carbon dioxide. The shelf life of a beer depends on how long it keeps its flavour, which is limited by exposure to oxygen, particularly for light beers with subtle flavour characteristics. These delicate flavours are also adversely affected as levels of carbonation decrease. The focus of recent materials developments has therefore been to improve the barrier properties of PET to these two gases, to achieve the longer shelf life needed to meet both consumer and retail requirements. Technical Considerations As with all packaging, the PET container has to deliver its contents to the consumer in a user-friendly way, while maintaining the freshness and distinguishing characteristics of the product. Ultimately the performance of a filled container is judged on the basis of what the product tastes like after a certain period of time, and the point at which this becomes unacceptable is generally taken as the shelf life of the product. Commercially viable shelf lives are not difficult to achieve for PET containers carrying products that are not particularly oxygen-sensitive. Such products include water and carbonated soft drinks, and even some beers and ciders, whose shelf lives are typically three to four months. After that time carbonation loss together with increasing taste (organoleptic) degradation due to oxygen ‘staling’, results in a tired a degraded product. Plastic Beer Bottles The approaches to PET barrier improvement fall in two main categories, either the blown PET bottle coated (inside or out) with a barrier material (figure 1), or a multilayer plastic bottle is blown containing barrier or oxygen scavenging layers. 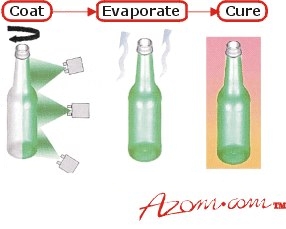 | Figure 1. Spray coating of external PET bottles. | |
Plastic Beer Bottles with Barrier Coatings Coating technologies can be broadly divided into two categories, those that use vacuum or plasma routes to deposit very thin films of materials, such as carbon or silica, and those that rely on the atomised spraying of liquid organic materials onto the external surfaces of the bottle. Ideally all coating materials must not interfere with the economics of recycling, nor detract from the bottle's appearance, but a significant further consideration with thin film internal deposits is the need for the materials to be approved for food contact. External Organic Coatings External organic coatings have been around since the early 1980s, when PVdC was used to improve the shelf life of large two litre PET bottles, but only marginal improvements were made. In the mid 1990s, barrier coating solutions based on two component epoxyamine chemistry (Bairocade) were developed by PPG, first to lengthen the shelf life of the smaller soft drink sizes in hotter climates, and then for beer. The transparent, glossy, external spray coating provides an excellent barrier to migration of C02 and O2, and is unaffected by humidity. The low temperature thermoset cure is compatible with PET bottles and provides a tough film, robust to filling and handling conditions. Coatings are designed to be applied to conventional bottles at thicknesses between 6µm and 10µm, and allow the use of standard resins and preforms with existing injection and blow moulding equipment. The performance improvement that barrier coatings offer for PET beer containers is significant around 19 times better than uncoated PET and translates into a retail shelf life of at least nine months. Inorganic Coatings The alternative inorganic coatings can be applied either to the inside or outside of the bottle after blowing. The latest developments are in plasma-applied coatings, using carbon or silicon, where methods have now been developed to allow the coherent coating of three-dimensional shapes, such as bottles. The Sidel Actis and Kirin DLC coating technologies produce a thin layer of amorphous carbon, typically 100 to 200nm thick, on the inside surface of the bottle. This is deposited from a high-energy plasma of acetylene gas within a high vacuum environment. The coating provides an excellent barrier to both O2 and CO2, and, because it is on the inside of the bottle, prevents the O2 dissolved in the PET matrix from migrating into the beer during the first few weeks of storage. Because the deposited layers are fundamentally brittle, they have to be extremely thin in order not to flake off under container stresses, caused by bottle expansion and creep when the bottle is filled, and under pressure from the contents. Other factors include damage and scuffing due to bottle handling, but these clearly do not affect the integrity of the coating if it is on the inside. The down side of these carbon-based coatings is their yellow-brown appearance. While this is not an issue for the typical amber-coloured beer bottle, it can detract from the appearance of clear PET bottles. The barrier performance improvements of carbon coatings are similar to those achieved by organic coatings, again giving a potential retail shelf life of nine months. Silica technologies such as Glaskin and BestPet rely on the application of a SiOX vacuum plasma coating, to give a barrier layer between 40 and 60nm thick. While the Glaskin process applies the glass clear coating to the inside of the bottle, the BestPet technique applies it to the outside. SiOX provides a better barrier than amorphous carbon, at least in principal, but is more brittle and must be applied in thinner layers than the carbon coatings, making the achievement of coherent crack-free layers difficult in a carbonated bottle. The three to four months shelf life offered by SiOX coatings is acceptable for carbonated soft drinks and certain alcoholic beverages, but does not meet the criteria of most European brewers. Plastic Beer Bottles with Multilayer Structures The alternative approach to using coatings to improve the gas permeation properties of PET is to use multilayer technologies. These rely on the production of a co-extruded or co-injected preform made from a multilayer structure of PET and other polymers, figures 2a and 2b. Final shape blowing produces a bottle with up to seven different polymer layers, which either act as a physical barrier to gas permeation, or are chemically active in scavenging oxygen from the PET and intercepting oxygen diffusing in from outside. 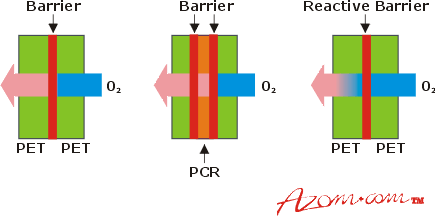 | Figure 2. Schematic of a (a) 3-layer structure, (b) 5-layer structure and (c) a multilayer structure with reactive layer. | |
In 1997 a multilayer PET bottle aimed at replacing the plastic cup at music and sports events was the first entry into the single serving beer market. The enhanced shelf life was achieved by blowing a co-extruded preform into a three-layer bottle wall, with outer skins of PET and an encapsulated inner barrier (between 5% and 10% of the bottle weight) of the high barrier polymers ethylene vinyl alcohol (EVOH) or nylon MXD6. Later developments allowed the incorporation of postconsumer recyclate (PCR) material in the inner layer of a five-layer structure, an important positive dimension to the issue of recyclability of plastic containers. Up to 25% recycled PET resin can be incorporated in this layer. This type of package gives around a six times improvement in barrier properties over a monolayer PET bottle, enabling oxygen-sensitive light beers to reach a shelf life of around four months before noticeable degradation. The Sealica process offers an alternative approach using ‘Blox’, an epoxy-based barrier material injected as an overlay on the preform, at thicknesses up to 40% of the preform. Smart Packaging While the above technologies are effective to a greater or lesser degree, probably the most effective way to deal with the problem of permeability is to create ‘smarter’ packaging that can respond chemically to gas permeation. Oxygen scavenging materials can be incorporated into polymer layers to react with the gas before it reaches the beer, figure 2c. These active barrier bottles are generally of a three-layer composition, with the outer PET layers surrounding a ‘functional’ barrier layer. The foremost such active barrier technology is Oxbar, which employs a scavenger of MXD6 nylon with patented metal catalysed oxygen reduction chemistry. This system reacts very quickly with oxygen in the bottle system and has a high oxygen capacity, ensuring a long active life. Similar active barrier technologies use the X-312 scavenger in MXD6 nylon, or the all polyester Amosorb 3000 as the active constituent in either a five or three-layer multilayer bottle construction. With these types of active oxygen scavenging packages for beer, shelf life performance is determined solely by the rate of carbonation loss. C02 loss is reduced by the presence of the MXD6 as a physical barrier, but it still limits the bottle's performance. With MXD6 as the ‘functional’ barrier, a beer shelf life of around four months is achieved, although the oxygen ‘capacity’ of the barrier layer may be as much as 24 months for a single-serving bottle. A trained taste tester can identify changes in the characteristics of atypical light beer once the oxygen level in the product reaches around 1ppm. Over a period of six months (a typical shelf life), a conventional PET container allows the beer to exceed this value by a factor of 30. Only the amorphous carbon, organic coating and Oxbar technologies achieve the 1ppm specification, figure 3a. The specification for carbonation loss is typically defined as the shelf life at which the product has lost 10% CO2. Here coatings generally outperform multilayer structures, figure 3b, and give a barrier performance that translates as a shelf life in the order of nine months, an important target for European brewers. 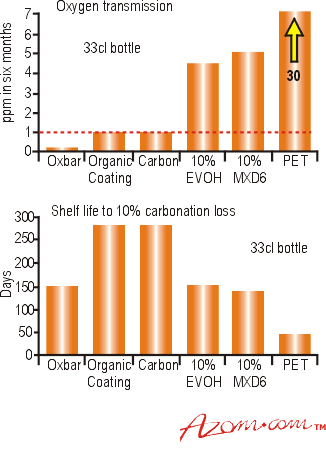 | Figure 3. (a) Relative oxygen ingress for different barrier technologies and (b) relative carbonation performance for different barrier technologies. | |
Overall then, it is clear that these developments have resulted in a number of technical solutions to a viable PET beer bottle that meets the needs of brewers and consumers alike, but that no single technology will ideally satisfy the entire spectrum of applications. Different products and markets require different solutions, with products being market rather than technology driven. Barrier coating technologies provide the longest carbonation shelf life and good oxygen barrier characteristics, whereas the active multilayer bottle offers manufacturing flexibility and outstanding oxygen barrier performance, but a shorter carbonation shelf life. In the end, the essential indicator for product shelf-life performance is taste, and a significant part of this work involves taste performance assessment, using a trained taste panel to compare the product against a control. Needless to say, membership of these panels is generally greatly oversubscribed. Public opinion on using plastic for beer bottles has been investigated, and consumer studies show that acceptance is, not surprisingly, highest in the 18 to 25 age group and lowest in the 50+ age group. The generation that has grown up with soft drinks packed in PET doesn't think twice about beer in a plastic bottle, and so it is likely that it will not be long before beer packed in PET will become commonplace in supermarkets, pubs and clubs throughout the world. However, no matter how much the technologies described here improve the barrier properties of the PET, there is still the issue of sealing the bottle. Gas permeation through the bottle closure can be significant for small bottle sizes and negate some of the barrier improvements. Available closure systems are metal crowns, plastic closures and aluminium twistoff closures. What is needed is a barrier bottle plus closure system that meets the product performance needs the development of barrier closures must proceed hand in hand with the bottle. So, as you resign yourself for now to loading up with kilos of glass containers for your next foray into al fresco eating, or clumsily knock your bottle onto the pavement, console yourself that in the near future the picnic will weigh less and your beer will bounce back. |