The use of plastics to produce wood-like products is a familiar part of many component industries. UK car manufacturers may be the only ones left who can boast that, their wood trim is actually made of wood! However, creating wood-like products from recycled plastics and using them for a wide variety of purposes in the construction industry and related sectors, such as furniture, is relatively new. Recycled and virgin polystyrene is being used by Extrudawood Ltd to create a material with almost the same characteristics as wood. As well as matching look and feel, the new material replicates wood in terms of density and structural characteristics, making it suitable for use as a replacement material in all areas of house building and furniture production. Windows systems, roof trusses, flooring and other construction components have been employed in a small chalet made entirely of the extruded polystyrene material (figure 1). 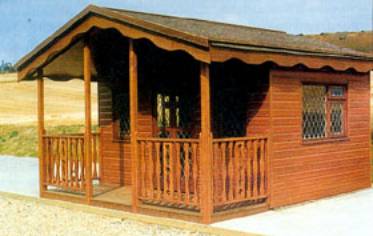 | Figure1. The all-polystyrene chalet. | Economics of Using Plastics Price is a very important issue when considering the economics of replacing wood with wood-like plastics. The major petrochemical companies first began to investigate wood-effect substitutes as long ago as the early 1970s, but two major oil price hikes made the exercise uneconomic. More recently the rising price and declining availability of wood has turned the economics back in favour of plastics. Although Extrudawood’s material cannot compete with timber on the basic level of cost per mass, the products themselves become very competitive when other factors such as machining, treatment costs, and material wastage are taken into account. The window support system, figure 2, is an example of a product ready to go on the market. The prices of the polystyrene-based products will be the same as those for softwood window frames, and the lower maintenance cost means that the system proves more economical over time. Door frames and fascias are other strong areas for the new material, due to the properties of polystyrene. 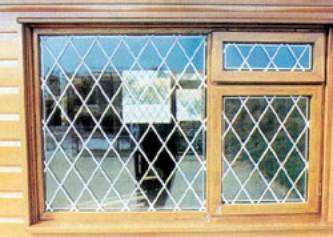 | Figure 2. The patented polystyrene (wood-like) window system. | Advantage of using Synthetic Wood Products One major advantage of Extrudawood's products is that they can all be recycled at the end of their lives by simple regrinding and reprocessing. However, the ambition is to produce wood-effect products from alternative sources of recycled polystyrene. The environmental priorities of an increasing number of companies include making use either of sustainable resources (such as timbers from plantations) or recycled and recyclable products. Recycling The second important issue is therefore the ability to recover polystyrene and reprocess it economically. European legislation has come to the aid of the recycler. All packagers (as of 1 July 1996) are obliged to recover 50% of their packaging waste, and in every European country there will be additional fees for land filling packaging waste. On 1 October 1996, new taxes came into effect for land filling in Britain, which greatly increased the cost of disposal of waste, and swung the economic balance towards recycling the materials instead. The current cost of land filling expanded polystyrene is of the order of £1000 per tonne, with more cost to come as taxes increase on petrol and diesel, and as new environmental standards are set for transportation. However, despite the impact of these factors, plastics recovery and recycling itself must be made inherently more economical. Polystyrene Recycling Solvent One economic way of recovering polystyrene is via a new product being developed in the USA. The product uses a biodegradable solvent derived from citrus fruits that eliminate all air from the polystyrene, making it economic to transport. Plastics waste is chewed up and then sprayed with the biodegradable solvent. This dissolves all the polystyrene, turning it into a jelly-like substance with a much greater density than squashed polystyrene waste. It is this high density, and the consequent ability to transport much larger quantities of material per truck, that makes the recovery process economic. At this stage, the material can also be land filled economically, or it can be reprocessed by precipitating the polystyrene from the suspension. Because the solvent reduces only polystyrene to a liquid form, it is possible to force the solution through screen filters that remove most of the contaminants, such as waste made from other plastics. This also means that for the first time it will be economic to reprocess polystyrene from food and horticultural uses. Other sources of recyclable polystyrene are of course the white and brown goods industries and fisheries. From the packagers point of view there is now a legal requirement to do this and the new solvent can reduce the economic impact of large-scale recovery. Following the filtration stage, another solvent is added to the mixture that precipitates out the polystyrene. Centrifuging separates the three components, allowing the solvents to be recovered for re-use, and the polystyrene to be used for subsequent processing. Extruding Wood-Like Plastic Components Extrudawood has been working on extruding recycled polystyrene and wood-effect compounds for the past two years. The process is relatively straightforward. Polystyrene, either virgin or recycled, is mixed with a range of additives and the compound is then extruded to shape in the colour and grain effect of any wood the customer chooses. In general the density is kept at approximately 0.56, though it has been successfully extruded from 0.40 to 0.70. Having its own fabrication facilities, the company has found it possible to work the material with normal wood fabrication equipment. Extrusions have been produced in various sizes and shapes, depending on the end use of the product. Because the components are extruded directly from the raw material, and not shaped out of wood from a tree, the level of waste is minimised. Making shaped components is easier - the versatile process eliminates the need for additional shaping work, and a wide range of products can be made for structural use. To demonstrate this, the company built the on-site chalet entirely from polystyrene, and sought to establish an EU funded project to build three holiday cottages, a swimming pool cover and a community hall on the Isle of Wight. The chalet has allowed experimentation with different fixing techniques as well as ways of shaping the material. Properties of Wood-Like Plastics The performance of Extrudawood's products will theoretically far outstrip wood. One of the reasons for this, apart from the inherent properties of the material, is that the timber industry is forced to rely on an increasingly unreliable product. Force grown hardwoods are an unknown quantity. Though they may be marketed as teak or mahogany they are unlikely to match the life span and performance of natural as opposed to force grown hardwoods. The same is true of the more popular softwoods, particularly pine. Extrudawood's material has other advantages. The nail and screw retention of the material is as good as that of wood, allowing construction to be carried out as normal. It is possible to incorporate flame retardants (the material has Class 1 spread of flame certification) and UV stabilisers. The product can also be extruded in a range of non-wood colours for shop and other interiors. Despite these advantages public acceptance of the material is a marketing issue of some concern. The chemicals used in manufacturing and the fire dangers of foam furniture are both issues in the consumer’s mind. However, the toxicity of the wood-like products is no more dangerous than that of the many other synthetics in use in the home, or that of natural substances, such as the wool in carpets or curtains. The flame retardancy of the material makes it highly applicable as a building product, and its ability to resist rot and insect attack makes it a useful material in applications requiring hygienic conditions. Materials Performance The density, weight, and performance of the synthetic products are all equivalent to wood. The chalet is as sturdy as one built from wood, remaining unaffected by anything that the British weather can throw at it. There is minimal movement or effect at high temperatures, as the softening temperature for material made from prime grade polystyrene is 105°C, and approximately 96°C for the recycled material. The material is strong enough to withstand high winds, and it has good photostability, ensuring that no short-term degradation occurs from UV exposure. The excellent performance of the material is due to its microstructure, which is a dense cellular structure, similar to that found in wood. However, unlike wood, the material can be enhanced by the addition of reinforcements. Provided they are small enough to be extruded with the polystyrene, strands of fibres can be added to the mix, to give, in effect, a composite material, with the associated enhanced properties. Other materials can be included, such as high-impact modifiers, to tailor the characteristics of the material. The system is highly flexible, and properties such as elasticity can be varied to allow the material to cover a wide range of uses. The material is very easy to decorate, being a more stable base material than wood. As no physical changes occur over time, paint will not flake and peel. Extrudawood's products are compatible with acrylic paints, and to further enhance its environmental credentials, it can be decorated with water-based acrylics. Application Areas Gymnasium floors have been laid in the USA where demand is now growing for this particular product. This is perhaps the most demanding use of the material as it involves continuous use by aerobics classes. It is also applicable in areas where wood performs poorly such as in agricultural storage areas. The material has been extruded for roof beams (though this is a longer term project), roof tiles, external cladding, internal fittings such as dado and skirting board, and windows. The window system has recently been granted full patent status. In the furniture industry interest has been expressed in kitchen furniture and office furniture with demand once again strongest in the USA. Interest has also been expressed in using the material for prefabricated buildings in the third world and in the faster growing economies of Asia. The latter is particularly interesting because of the growing amounts of plastic waste available in these areas. Combined with the new recycling technology it is possible to envisage a complete package whereby local waste is recycled into local low cost homes. Of course the same scenario is possible in the UK and with many local authorities committed to recycling policies then these kinds of initiatives should be possible. The major drawback is inertia. The UK has been the slowest of the EU countries to adopt the packaging waste legislation, and to make the legislation work effectively it is imperative that the local or national authorities specify minimum recycled content levels for house building or housing renovation as is now done in the automotive industry. |