Strongwell fabricated fiberglass pultrusions for Weber Aircraft of Burbank, California, marking the first manufacture of fiberglass pultrusions for use in a commercial aircraft application. The aircraft components have unusually intricate and angular design. These 18 different shapes are door framing and panel joiners for modular lavatories deployed aboard Boeing 737 commercial aircraft.
.jpg)
Design Challenges
Some of the challenges in designing the components were the ultra thin wall of some portions in the range of 0.060-0.090", and varying wall thicknesses in a single component. Fabricating these thin wall sections without compromising structural integrity was the most challenging task for Weber Aircraft.
Advantages of Fiberglass Aircraft Components
The lavatory unit installed is a homogeneous all-fiberglass system. Fiberglass framers and joiners are attached to honeycomb fiberglass panels to create the all-fiberglass lavatory unit. The selection of fiberglass is attributable to its lightweight and resistance to the corrosive chemicals utilized in the lavatory cleaning and toilet operation.
Technical Data
Product: |
Fiberglass Aircraft Parts |
Process: |
Pultrusion |
Materials: |
Fiberglass reinforced vinyl ester, fire retardant |
Sizes: |
18 different shapes ranging in size from the smallest: 1.125" wide x 0.38" high x 0.06" thick channel to the largest: an irregular pentagon having four external flanges and a smaller irregular hollow pentagon with overall dimensions of 4-1/2" wide x 2-3/4" high x varying thicknesses in the same shape of 0.125" to 0.070" |
For: |
Weber Aircraft |
User: |
Boeing |
Conclusion
To reduce cost, the system was fabricated as a modular preassembly which could be installed as a single unit. Hence, the components were fabricated with very high accuracy. According to Bob Witt, Weber Aircraft Manufacturing Engineering Specialist, Strongwell’s expertise in the fabrication of thin wall, intricate angular shapes was the reason behind its selection. This needed properly detailed tool design and an appropriate material preformer operation in production.
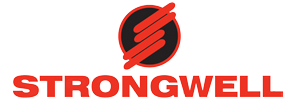
This information has been sourced, reviewed and adapted from materials provided by Strongwell Corporation.
For more information on this source, please visit Strongwell Corporation.