In this article, several example case studies are provided which highlight the benefits of continuous process analysis in a wide range of applications.
Engineers at the Universidade Federal de Itajuba (UNIFEI)(Brazil) innovate practical solutions that improve the efficiency of crude oil processing. One research area is the evaluation and improvement of separators for oil-in-water emulsions. The main success of this project is the generation of feed emulsions, which are representative of those encountered in oil processing. The group includes a pilot scale unit that produces emulsions at a flow rate of up to 18 m3/h.
Results of a Trial Run
Figure 1 shows data from a trial, testing the ability of a laser diffraction on-line analyzer to monitor emulsion droplet size as test bed conditions are altered. The oil concentration in the system is increased in tests 1 to 3. This has a minimal impact on volume moment mean of the particles D[4,3] and on the Dv90 (the size below which 90% of the particle population lies), but increases obscuration (red line).

Figure 1. Experiments investigating the impact of oil concentration and production pressure on the droplet size of an oil-in-water emulsion.
In tests 5 to 7 the pressure applied during emulsion production is gradually increased, driving down Dv50, and indeed the other size parameters Dv10 (the size below which 10% of the particle population lies and Dv90 ). In test 8, a further increase in oil concentration is made, pushing obscuration up to 97.5%. In the final test 9, pressure is raised further to 12 bar to produce an emulsion with highly fine droplets, a Dv90 of 26.63 microns.
It can be observed from the time axis on the screen shot that all these trials were completed in just one hour. In this example, the on-line analyzer enables the experimenter to very quickly find, set and control the conditions required to produce a suitable emulsion.
Case Study: Innovative Equipment Design
In a comprehensive assessment of a range of mill types for producing a new marble powder, Ferrari Granulati engineers selected a vertical roller mill as the choice option. This selection was made based on energy efficiency and equipment footprint, but it also presented a challenge.
Ferrari Granulati collaborated with mill manufacturer STM to develop an innovative milling circuit based on a VRM that will deliver in-spec material. The circuit was completed with a classifier for final product separation.
Modification of the mill towards acceptable performance for the application will rely on comprehensive investigation of factors controlling particle size and intelligent modification of the hardware. A simple mechanical transducer was installed on the arm of the compaction roller as in Figure 2 and Ferrari Granulati can automatically control the powder depth on the table to increase the impact of the rollers. The transducer measures powder depth continuously, so in case the powder layer trends below 15 mm, the rotational speed of the table automatically comes down, retaining more powder on the table and re-building depth. Normally the table rotates at low speeds of around 25 to 30 rpm.
A challenge with very fine powders is their tendency to agglomerate. In this specific circuit, agglomerates are classified by the separator as over-sized and recycled back into the mill for further grinding, setting up an energy consuming internal recycle.
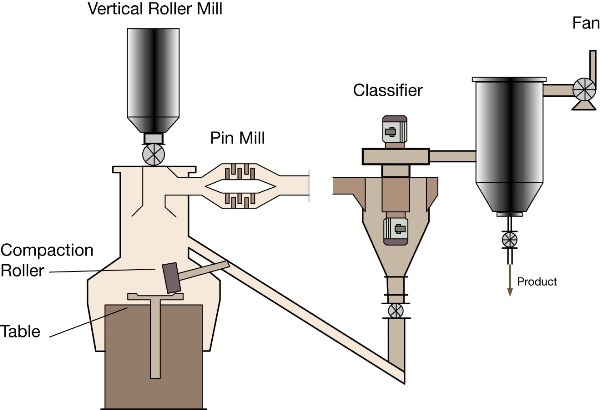
Figure 2. Schematic of a milling circuit, with vertical roller mill, for the production of marble powders.
This issue was addressed by installing an in-line pin mill immediately upstream of the classifier. The rotation is comparatively slow for a pin mill at 300 - 400 rpm (the external diameter of the mill is 500 mm) and this unit provides sufficient energy to break-up most agglomerates before they reach the classifier, enhancing energy efficiency, optimizing the mill throughput and avoiding excessive wear.
The team had to finally consider how to set the air flow rate through the circuit. There are two roles for this air flow - within the mill fallen powder is lifted back onto the table for further milling and material is also transported from the mill through to the classifier. The selected solution was to operate with an air flow sufficient only for classifier operation.
Hence, a screw auger was installed to transport material mechanically that falls from the table to the inlet of the pin mill, enabling its classification along with other milled material. The developed milling circuit proved to be a great success, one that Ferrari Granulati substantially attributes to the availability of real-time data throughout the development process.
Case Study: Developing a Generic Processing Solution
Pharmaceutical manufacturers, encouraged by the FDA's Process Analytical Technology (PAT) initiative, are actively looking for analytical techniques that will underpin the development of more effective processing strategies.
Milling is a common unit operation for pharmaceuticals and a global pharmaceutical manufacturer has recently commercialized an automated milling solution with widespread applicability.
The solution makes use of a comminutor mill, wherein material entering the mill via the throat is broken up by rotating blades, which simultaneously apply cutting and impacting actions. Particles in a specific size range exit through screen, while oversized material is retained for further comminution. Even though screen specification and blade profile impact the size of the exiting particles, rotor speed is the key control variable.
Pilot scale trials with an Insitec on-line particle size analyzer provided significant evidence that this system could efficiently and continuously monitor, in real-time, material exiting the mill. Steps were then taken to integrate the mill and analyzer in a way that the particle size data is used for controlling mill speed automatically. For automation of mill operation a closed control loop was implemented.
The operator and the automated mill interact through the mill human machine interface that runs on a dedicated PC. From here one can input particle size set points for the control loop, remotely start and stop the analyzer and mill, perform background tests, and receive particle size results. The tuning of the loop was done using proportional (P) control. The chosen feedback parameter was an average Dv50 with a 30s rolling average. In tests, the set point was reduced from an initial value of 58µm down to 50µm and then back up to the original value. At the first set point, the mill stabilized after about a minute, reached the second around 30s after the change had been made, and completed the final transition in less than 2 minutes. This performance signifies the effectiveness of the control system.
This automated solution, established at the pilot scale and presently commercialized, is applicable to any number of manually operated mills. In this study, pilot studies were used to prove the on-line technology and the feasibility of automation, generating the confidence necessary to commercialise an efficient processing solution.
Conclusion
Real-time process analysis supports the manufacture of a better quality product at a competitive cost.
Continuous process analysis enables more controlled pilot plant operation and enhances investigative research. The result is a faster, more confident transition to profitable manufacture.
About Malvern Panalytical
Malvern Panalytical provides the materials and biophysical characterization technology and expertise that enables scientists and engineers to investigate, understand and control the properties of dispersed systems.
These systems range from proteins and polymers in solution, particle and nanoparticle suspensions and emulsions, through to sprays and aerosols, industrial bulk powders and high concentration slurries.
Used at all stages of research, development and manufacturing, Malvern Panalytical’s instruments provide critical information that helps accelerate research and product development, enhance and maintain product quality and optimize process efficiency.
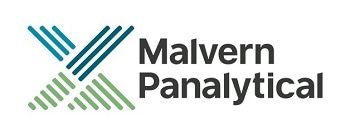
This information has been sourced, reviewed and adapted from materials provided by Malvern Panalytical.
For more information on this source, please visit Malvern Panalytical.