Ceramics, and in particular, engineering ceramics, are becoming increasingly important in today's society. They offer a huge array of mechanical, thermal and electrical properties. These range from low thermal conduction in ceramics such as alumina, to high thermal conduction, e.g. diamond, and from low density electrical insulators to superconducting ceramics. Piezo-ceramics offer the almost unique ability to convert electrical energy into mechanical movement and vice versa, and materials such as beta-alumina and zirconia, which exhibit ionic conduction, are used as sensors. These materials have found application in a wide range of industries, but their exploitation has been concentrated mainly in the automotive, power generation and electronics sectors. The Advanced Ceramics Market in the USA A recent study of the advanced ceramic market in the USA shows that the use of advanced ceramic materials is increasing, and will continue to increase. The dominant market sector is electronics, with 65% of the market. This segment, which contains mature technologies such as integrated circuits and capacitors, alongside relatively new areas such as piezo-ceramics and superconductivity, is forecast to continue to grow steadily well into the next century. The second highest growth rate is in structural ceramics, where materials such as silicon carbide, silicon nitride, zirconia, diamond and ceramic matrix composites are being exploited as cutting tools, wear parts, sensors and biomaterials. Ceramics in Application It should be remembered that, in general, ceramics should be used only where their specific properties are required. A common thread amongst all of the above applications is that, at some point, the ceramic component interfaces with something else - another part of the machine/device made from another material, or perhaps a casing. At this point some kind of attachment or joint is required. Ceramic Joining Techniques Ceramics are inherently difficult to join either to themselves or metal structures - a consequence of their strong ionic and covalent bonding. However, there are several well-established technologies available, including mechanical attachment, adhesives, soldering/brazing and glass-metal sealing. These are often chosen on the basis of temperature requirement of the joint, ease of implementation, functionality etc. There are also other more unusual or application-specific processes, such as microwave bonding, ultrasonic welding and friction welding. Of the many joining processes available, probably the main and most adaptable technique used to join ceramics is brazing. Ceramic Brazing Brazing is a liquid phase process that is particularly well suited to preparing joints and seals, and is an established technique for the joining of ceramics. The brazing process can be readily adapted to the mass production of components, such as those used in the electronics and automotive industries. Brazing The dictionary definition of brazing is stated a ‘the joining of two pieces of metal by fusing layer of brass or spelter between the adjoining surfaces’, and is probably a derivation of a 16th century French word meaning ‘to burn’. The process basically involves a braze melting and flowing between the two pieces of material. This is commonly referred to as ‘wetting’ and is absolutely critical - particularly when brazing ceramics. Nowadays there are many materials that can be fused to produce joints between materials - those that melt above ~450 °C are classed a, brazes, materials melting below ~450 °C are called solders. Wetting If a braze alloy is melted between two ceramics, a poor joint is likely to result, because of poor wetting. Wetting is measured in terms of the con tact angle between the braze and substrate after melting. For good wetting, the contact angle (θ) is less than 90°; for poor wetting, the angle is greater than 90°. Examples of good and bad we ting are shown in figure 1. 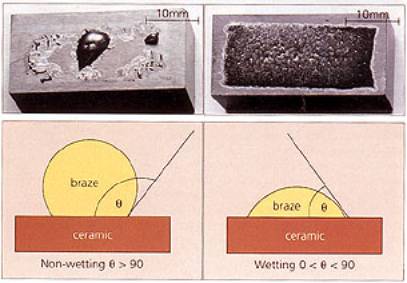 | Figure 1. Two wetting trials showing poor (left) and good (right) wetting. | Methods to Increase Wettability To encourage wetting there are two basic philosophies - apply something to the surface of the ceramics so that the braze will wet, or, put something in the braze that will induce wetting. Surface treatments include metallisation, metal coating and metal hydride treatment, while braze modification involves a process known as active metal brazing. In either case the actual brazing operation takes place either in a controlled atmosphere, such as nitrogen or argon, or a vacuum better than 10-4 N.m-2. The ‘Moly-Manganese Method’ One of the most widely used methods of metallisation is the so-called ‘moly-manganese’ process, which is particularly well suited to the brazing of alumina. It is used extensively in the electronic and electrical industries to produce ceramic-to-metal seals for ultra-high vacuum equipment, such as isolators and power semiconductor housings. In its simplest form, a powder mixture of glass, molybdenum and manganese is applied by painting or screen-printing to the alumina surface. The alumina component is then heated in a wet hydrogen atmosphere to a temperature of ~1500°C. Prior to brazing, the metallised surface is nickel coated to improve wetting. The component is brazed using a conventional braze, such as 72wt%Ag-28%Cu eutectic alloy, chosen for its moderate melting temperature (780°C) and good ductility. Other higher melting temperature braze alloys can be used, such as 82Au-18Ni, and for even higher temperature requirements, Ni-Cr-based and palladium-based alloys, figure 2. 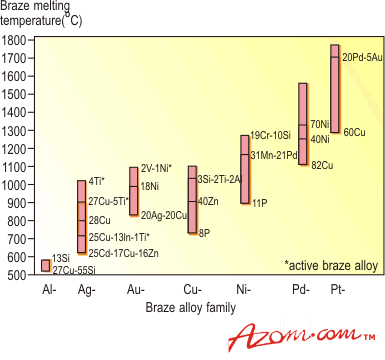 | Figure 2. Principal braze alloy families, including common active braze alloys and their melting range. | Despite the numerous steps required, the moly-manganese process can be automated. The process is dependent on the presence of an intergranular ‘glassy’ phase, which is found in several ceramics, notably alumina and silicon nitride, where the glass acts as a binding agent. Where such glass is not present, i.e. zirconia and silicon carbide, a different approach to metallisation is required. Metallising Ceramic Surfaces A number of approaches can be used to directly metallise a ceramic surface. The simplest method is by electroplating the ceramic surface to be brazed with Ni or Cu. However, this is not always possible as not all ceramics are electrically conductive. Other methods include vapour deposition and sputter coating, allowing the deposition of a metal which adheres to the ceramic and is wetted by the molten braze. A third approach is to use an ‘active’ metal hydride to form a reaction layer between the ceramic and braze alloy. Metal Hydrides Certain metal hydrides possess the ability to wet ceramic surfaces that have not been previously metallised. The hydrides - usually of Ti, or sometimes Zr - are reduced, and brazed simultaneously in a controlled atmosphere (vacuum or inert gas), at relatively low temperatures, permitting a fast brazing cycle. Typically Ag, Cu or Ag-Cu eutectic braze alloys are then used. The ‘Active Metal Process’ The ‘active metal’ process is similar to the metal hydride process. For both these processes to work they require an `active' element that will react with the ceramic, forming a reaction layer between the ceramic and the molten braze that will reduce the interfacial energy to such a level that wetting of the ceramic takes place. The active elements used for this process include Ti, Zr, Hf, V and Al. The best known of these active elements is Ti, which is used in many commercially available braze alloys. The active metal process has superseded the hydride process, and is a one-step operation. In comparison, the moly-manganese process typically has five steps. Brazing can be undertaken at a range of temperatures in controlled atmosphere, depending on the alloy used. Active Braze Alloys Active braze alloys are constantly undergoing changes and modification in composition to meet the increasing requirements to permit metals to be joined to ceramics without the need for metallisation of the ceramic surface. Commercial active braze alloys are mainly based on the Ag, Cu or Ag-Cu eutectic systems with added titanium. These and other available families of braze alloys are shown as a function of melting point in figure 2. How the Active Metal Process Works Many studies have been conducted to understand the wetting characteristics, reaction kinetics and joint behaviour of ceramics joined using these active metal alloys. Figure 3 shows a scanning electron microscope (SEM) image of a Ag-Cu-Ti alloy brazed to a silicon nitride substrate. 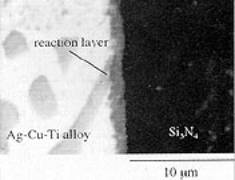 | Figure 3. Scanning electron micrograph of the reaction layer between an active metal braze and silicon nitride. | The reaction layer is clearly visible and many studies have shown that excessive growth of this reaction layer can be detrimental to the strength of the brazed joint. Although many reaction products are possible, thermodynamic analysis can determine which products are favourable. Table 1 shows that TiN, Ti5Si3 and TiSi are the main reaction products for silicon nitride. Brazing Alloys A number of brazing alloys have recently entered the market designed for specific needs, i.e. the high temperature brazing of SiC. These are based on transition metal-Si eutectic alloys, producing joints capable of surviving temperatures in excess of 1200°C. Another alloy that is of interest is a low temperature active braze (or solder) that melts at ~420 °C, which can join ceramics (and metals) in air, as opposed to a protective atmosphere. Ceramic Particulate Reinforced Braze Alloys Another innovation has a ceramic incorporated in the braze alloy, to both increase its strength and reduce its coefficient of thermal expansion (CTE). One example is the modification of a common active metal braze which on cooling forms an in-situ metal matrix composite. It has been shown that the joint strength increases with the introduction of as little as 5% by volume of ceramic particulates, when compared with the unreinforced braze alloy, figure 4. Future work on this concept will be extended to higher temperature braze alloys. 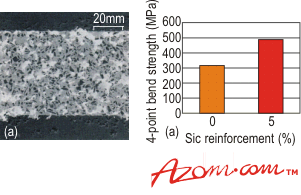 | Figure 4. Scanning electron micrograph of a 20vol% SiC reinforced active metal alloy, and a comparison of the strength of the unreinforced and 5vol% reinforced SiC brazed joints. | High temperature Active Metal Brazes The majority of the commercial active metal brazes have been developed for moderate temperature use up to ~450 °C. However, one of the many attractive properties of ceramics is their ability to survive high temperatures - for example, alumina typically has an upper use temperature of 1700°C. The braze alloys used therefore need to have higher temperature capability than is currently available. One method is to coat the ceramic with either a reactive or refractory metal (W Mo, Ta, Cr) then braze using high temperature braze alloys, such as palladium and platinium-based systems. This is similar to the method described in metal coating, and has been used successfully for joining many high temperature ceramics. An alternative that is being investigated is a range of high temperature active braze alloys, capable of extended use at temperatures in excess of 650°C. Although these alloys are not currently available commercially, they are of great interest, with the potential of being commercialised in the future. Ideally these alloys will retain their strength and ductility at temperature, as well as having good oxidation resistance. Alloys with such properties include Pt-Cu-Ti, Pd-Ni-Ti and Co-Ti. It has been shown that one active braze alloy, 60Ta-30W-Zr, can be used to join graphite, for use in excess of 2700°C. Joint Design When brazing ceramics, particularly to materials with a dissimilar CTE, careful consideration must be given to the design of the joint. Typically, the CTEs of ceramics are less than most metals (and braze alloys) which means, on cooling from the brazing temperature, the braze alloy and metal component will contract more than the ceramic component. This will introduce residual stresses into the joint. As ceramics perform better in compression, the joint should be designed, if possible, to keep the ceramic component in compression. A further factor that must be considered is the brittle nature of ceramics and the avoidance of sharp edges/changes in section in the joint. These points can act as stress concentrators, potentially acting as initiation sites for the fracture and failure of the ceramic or joint. The best practice of joint design, braze alloy choice and brazing temperature will help reduce the residual stresses that develop in the joint. Joint Modelling Modelling can be used to predict failure of brazed joints and compare many different joint designs, therefore reducing the number of brazing trials required. For simple component shapes and joint design then analytical methods may be used. However, in the majority of cases the component or joint is too complex and so numerical methods are required, such as finite element analysis (FEA). Finite Element Analysis For FEA a complex component is usually modelled by considering it as an assembly of small simple parts, called elements. The element assembly (or mesh) gives a geometric representation of the component. The use of the computer allows a ‘virtual laboratory’ to be set-up to test different joint configurations, braze alloys and brazing conditions prior to any actual brazing. This technique is very powerful and is being used more in development work, not only for brazing, but other joining technologies. |