The transportation of crude oil around the world is fundamental to the survival of most, if not all economies. Rubber plays an important role in many aspects of oil transportation, not least in its transfer offshore. This can take many forms, but perhaps the most common is loading and discharging supertankers offshore through large bore reinforced rubber hoses, in situations where access to a shore terminal is unavailable (figure 1). Reinforced rubber hoses are also used extensively in offshore oil exploration and live crude transfer systems, where demands on the product are at their extreme, with high pressures, high temperatures and sour gases. A development of the large bore oil hose is an essential product for transfer of dredging slurries offshore. 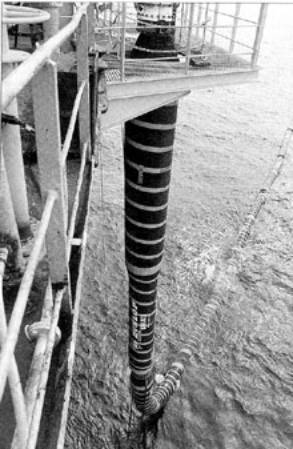 | Figure 1. Offshore oil hose floating string in use on a tandem loading application. | Definition of Large Bore Offshore Hoses The large bore offshore hose needs some explanation since associations with hose in common use can be misleading. Large bore refers to bore sizes in the range 150mm (6 in) through to 914mm (36 in), with typical individual hose lengths of 9 to 12m (30 to 40 ft). Floating dredging hose types can have an outside diameter approaching 2m (6 ft). Although rubber is an essential part of the hose construction, the strength of the hose is very much dependent upon the fabric and steel reinforcing members. Supertanker Offshore Terminals For a typical supertanker offshore terminal, the system consists of a moored buoy, with hose connections between the buoy and the seabed (submarine hose) and between the buoy and the tanker (floating hose). When not in use the floating hoses stream from the buoy turntable as dictated by the current and when in use, the tanker moors to the buoy and connects the hoses to manifolds at its midposition. There are something like 250 terminals of this type worldwide. Other systems are also in use, for example catenary systems and tandem mooring systems between storage and shuttle tankers. Large Bore Dredging Hose Large bore dredging hose is a similar product to the oil hose but requires very different properties for the rubber lining and a greater ability to withstand rough handling conditions. Dredging hose is typically used for transfer of dredging slurries from offshore dredgers and enjoying an active market stimulated by contracts such as for the extension of Hong Kong airport. Hoses for Exploration On the exploration side, high pressure hoses are used as ‘rotary drilling hoses’, to supply lubrication and spoil removal during well drilling operations, as ‘choke and kill hoses’ to control the well in emergency situations and for live crude flow lines between wellheads, pipelines and platforms. Pressures in these applications can be up to 100MPa (15,000 psi) and bore sizes from 5 to 30 cm (2 to 12 in). Operating Conditions In all the above applications loads on the hoses are significant, whether from internal pressures, external forces or combinations of both. For example, large bore oil hoses are capable of working tensile loads up to 30 tons. Structure of a Reinforced Hoses Standard Reinforced Hose Figure 2 shows a section through a typical hose wall. The hose lining is rubber, which is reinforced with multiple layers of spirally applied high tensile steel or fabric reinforcing cords, to provide pressure and external load resistance. At least one helical steel wire is then applied outside of the main reinforcement and this wire is totally embedded within a rubber matrix. The hose carcass is completed with further fabric reinforcement and a rubber cover. If the hose is a floating hose, following vulcanisation of the main hose carcass, layers of closed cell floatation sponge are applied, with a final fabric reinforced rubber or occasionally polyurethane cover. Most large bore hose is constructed in a similar manner, but many variations exist, depending on particular site requirements. 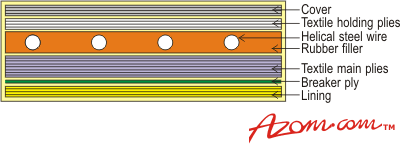 | Figure 2. Cross section through a typical hose carcass. | High Pressure Hose High pressure hoses are similar but due to the high pressures, reinforcement is usually with high tensile steel cables. Bores can be reinforced with flexible metal tubes to increase hoop load resistance and prevent explosive decompression of the lining as a result of trapped gases. Rubber for Hoses Requirements The requirements for the rubber in these products are diverse, depending on the hose type, the product carried and requirements for filler layers and covers. Any hose will have more than one rubber compound type in its construction, specially formulated to give the required properties for the layer. One essential factor in any offshore hose is to achieve very high levels of adhesion to ensure maximum resistance to fatigue. Properties for Offshore Oil Hoses The key properties for the hose bore of an offshore oil hose are oil resistance, high resistance to aromatics (up to 50%), temperature resistance, (-29 to 52°C), fatigue resistance and ozone resistance. Acrylonitrile based rubber compounds are usually selected for oil hose linings. Properties for Dredging Hoses However, with a dredging hose where high abrasion resistance is the key requirement hard wearing SBR rubber compounds are more likely to be selected. It is interesting to note that dredging hose linings will outlast steel by several times and in these hoses the steel end fittings are also lined with rubber. For live crude hoses the rubber compound must be formulated to resist oil, hydrogen sulphide and have sufficient strength to withstand explosive decompression; the rapid release of entrapped gases when bore pressures are reduced. Design of Reinforced Hoses Rubber and Steel Relationships Rubber layers within the hose are required to achieve high bond levels to reinforcing members and maintain the location of the helical steel wire. In some hose designs, particularly dredging hoses, the function of the helical steel wire is substituted by having a sandwich section of high modulus rubber. This gives the hose adequate hoop strength with the advantage that flattening and kinking can be tolerated up to a point, making the hose more tolerant to abuse. On the outside of the hose, the rubber layers need to resist seawater, ozone attack and have good abrasion resistance. Matrix Design The ability or rubber to provide a sealing function, to bond layers together, to be capable of being formulated into a wide variety of properties and to provide an overall flexible fatigue resistant structure are key factors in the selection of rubber in offshore hoses. However, the designer must be aware of the performance of the whole hose matrix and the demands made on the compounds to maximise fatigue performance. Finite element analysis of hose structures is an important element of today’s hose designs and the interaction between the engineer and rubber chemist becomes more important as some of the finer details of the complex hose matrix are fully understood. Hoses are generally very fatigue resistant and isolated problems in service will usually relate to reinforcing members or end connections and their interaction with the rubber, rather than being a feature of the rubber itself. Double Carcass Hoses Spillage of oil is obviously of major concern for offshore oil hoses and ‘double carcass’ hoses are available for those customers particularly concerned about maximising hose lives or taking out contingency plans against premature failures or damage. A double carcass hose has a reduced strength outer carcass, which will contain any leaking oil and will signal failure by various techniques used by the different hose suppliers. Summary The reinforced rubber offshore hose is well established as a proven means of providing offshore transfer of fluids in harsh environments. The finer details of this complex design are still being improved and new applications are extending the capabilities of the product. For example there is interest in the transfer of LPG products at temperatures down to -50°C, where the rubber compounds must retain flexibility at these low temperatures whilst maintaining their other properties. Also, hoses feature in proposals for offshore generation of power in renewable energy projects. We can be confident that the outstanding properties of rubber ensure that its use in offshore hose is guaranteed for the foreseeable future. |