Fast, accurate photocopying is taken for granted these days. At the press of a button we expect rapid delivery of dozens of copies identical to the original document. Yet not many people appreciate the intricate system of mirrors, drums and rollers which makes up in inner workings of a photocopier, or the materials from which the parts are made. The Fuser Roller The most important part of the photocopying system is the fuser roller, which finishes the copying process by fixing the toner to the paper. It is covered in a polymeric coating which must be heat resistant to over 200°C, wear resistant, and have the necessary surface release properties. Improvements to the process of producing this coating are making fuser rollers cheaper and ‘greener’. Fuser Roller Materials Only two types of material - silicone rubber and fluoroelastomers - have all the necessary physical properties, and these are commonly used to coat a hollow metal core to produce the fuser roller. Certain grades of silicone rubber have both the necessary heat resistance and required release, but the fluoroelastomers need to be used in conjunction with an oil-doning system to give satisfactory release. Without the right release properties the toner will stick to the fuser roller, resulting in poor copy quality. What is in a Fuser Roller? The fuser roller contains a heating element with an output of approximately 1.5kW. This cycles on and off as required and is controlled by a thermistor which is in contact with the covering on the roller. This creates significant wear and damage. In addition, the rolls are subjected to a load of approximately 100kg over the face length to create a nip approximately 5mm wide, which allows time for the fusing process to take place. Producing Fuser Rollers Producing fuser roller coatings to withstand these harsh conditions although at the same time improving quality and value for money is an extremely competitive business. With new companies entering the industry, existing suppliers need to maintain their competitive advantage by investing in, new technology and ensuring their existing processes are made as efficient as possible. Current Technology The current method of producing fuser rolls involves degreasing and priming the metal core, and then applying a thin (typically 0.25mm) elastomeric layer by spraying or moulding. The materials for both processes are expensive. The typical cost for silicone materials is presently £12 per kg, although some special compounds can cost over £60 per kg. Fluoroelastomer materials for these applications cost in the region of £30 per kg. Spraying Polymer Coatings onto Fuser Rollers To apply a coating by spraying, the polymer is mixed with a solvent in the ratio 70% polymer to 30% solvent. The mixture is then electrostatically sprayed onto the roller - with varying degrees of success. The equipment required is expensive, the process is environmentally unfriendly due to the large amount of solvent being used, the expensive materials get wasted due to overspraying, and end caps have to be fitted to the roller during spraying, which must then be cleaned or disposed of. Moulding Polymer Coatings onto Fuser Rollers By comparison, moulding is a fairly simple process - the core is assembled into a metal or cardboard tube, the material injected, and the assembly cured either in a press (typically for 5 minutes at 1500°C for high temperature LSR injection moulded articles) or in an oven (for around 1½ hours at 65°C for RTV materials). End caps are again used and need to be cleaned at the end of the process, however, thus wasting valuable material. Thin Coat Flowcoating A new system for manufacturing fuser rollers wastes very little material, is almost solvent free, is capable of coating various roller sizes, and is not overly complex in engineering terms. It is also cost effective for new products, and does not affect roller performance. The technique is known as ‘thin coat flowcoating’, and has previously been used in the poyurethane industry to apply thick coatings to rotating surfaces. It has been taken a step further, however, with an innovative process allowing very thin coatings of elastomers (down to fractions of a millimetre) to be applied to rotating cores. How Does Flowcoating Work Figure 1 shows the nozzle of the flowcoating machine applying a two part, room temperature, condensation cured liquid silicone coating to a hollow aluminium fuser roller core. The liquid silicone is blended with a selected volume of catalyst in a water-cooled dynamic mixer, where trapped air is removed before the mixture is filtered and dispensed. In this process, material flows onto the roller through a nozzle that produces a very thin bead, typically 2mm wide. The roller has to be accurately positioned in relation to the nozzle, to within 0.02mm. 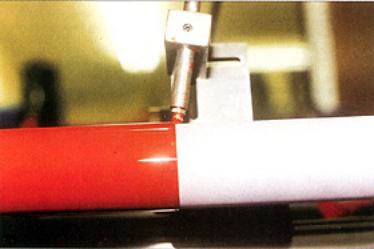 | Figure 1. Application of liquid silicone by the flowcoating process. | Processing Parameters At the same time as the coating is being applied, the roller is rotated and the nozzle is driven along its length, controlled by a computer. The roller is then rotated at a controlled speed until the material has solidified. The rotation speed of this part of the process is critical - too fast and the material migrates towards the ends of the roller, too slow and the covering will run and drip. Either way, this produces a roller with an uneven coating thickness which will not level during the grinding process, and so it will be rejected. Material viscosity is also critical during rotation, which continues for about an hour. If it is too high, the material will not flow satisfactorily. If it is too low, the material will slump and drip before it has cured. Ingredients and Advantages of Flowcoating A number of key ingredients need to be incorporated into silicone in order to improve roller performance and life. Aluminium oxide and boron nitride are typical fillers used in roller applications. The aluminium filler imparts good thermal conductivity to the material. Boron nitride, as well as giving the material good thermal conductivity, imparts lubricity and provides wear resistance. These fillers affect the viscosity of the material and its ability to be flowcoated. Additions have to be carefully monitored in order not to adversely affect processing. Depending on the viscosity required, rollers can be made fairly cheaply by flowcoating, as there is no need for moulds. Summary Flowcoating does need an extremely clean and controlled environment, however, because small particles of foreign matter on the surface of the roller can cause copying problems. Any contaminated rollers are rejected at final inspection. On the plus side, flowcoating is not restricted by roll length, fig 2, and is not limited to room temperature curing silicones either. It can also be successfully adapted to produce fluoroelastomer coated rollers. Despite the drawback of clean room conditions, flowcoating looks set to prove itself a crucial method in roller production for companies wanting to stay ahead in the photocopier market. 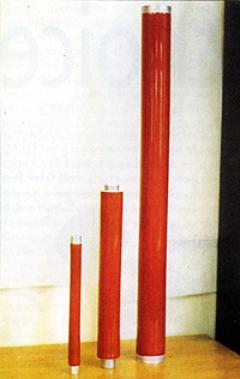 | Figure 2. Flowcoating can be used to coat rollers of various lengths and diameters (left 400m, through to right 1000mm). | |