Introduction Slip casting [1-4] is an essential technique to produce traditional and/or advanced ceramics. A major disadvantage of slip casting is the time required to form a body of the desired thickness and the additional time needed to dry the cast body. To reduce the drying period a significant enhancement of manufacturing speed and improvement of productivity of ceramic fabrication are needed. However, rapid drying would increase defects, such as warpage, crack, and density distribution, besides, these defects affect the characteristics of the sintered body [5]. Conventional drying of green ceramic parts has been studied for years and has recently become more important due to the use of ultrafine powders in colloidal processes [5, 6]. The capillary size of the porosity in the green state reduces considerably as the particle size of the packing powder decreases. The transport of water through capillaries in sizes less than 1/5 of the particle diameter exerts a strong drying stress on the wet piece. Therefore, the drying must be conducted in an extremely slow rate so as to preserve an intact piece [6]. On the other hand, advances in the drying technology of ceramics have been increasingly stimulated over the past years, so that, in contrast to the traditional convective drying with warm air, other drying methods are becoming more and more important. In this context, the possibility of applying high frequency drying in the drying process of ceramics has become a centre of interest [7-9]. Some of the studies deal with the possibility of predicting the rate of heating up the material exposed to microwaves [10, 11]. Other studies are concerned with the specific drying acceleration by means of microwaves [12]. Previously, we examined rapid microwave drying in ZnO ceramic for slip cast bodies and also compared the characteristics of such bodies with those of cast bodies dried by conventional drying techniques [13]. This work showed that microwave heating has merits in terms of both the rapid drying and structural uniformity of dried bodies [13]. In this report, we discuss why by microwave heating it was possible to obtain the structural uniformity of dried bodies showed in the previous work, and also examined the difference of drying behavior under microwave heating and conventional heating based on our results. Experimental Procedure Slurry Preparation A commercially available sub micron ZnO powder (JIS 1, Hakusuitech Co., Ltd.) with an average diameter of d50=0.5 μm, was used for the preparation of slurries which contained 40 vol% of solid phase and 0.32 mass% of commercially available NH4+ salt of poly acrylic acid (PAA) (Aron A-6114, Toagosei Co., Ltd.) as dispersant. After being mixed for 2 minutes with an electric mixer (AR-250, THINKY Corp.), the suspension was ball-milled for 12 hours using high-grade Al2O3 balls (diameter 5 mm) to prepare the ZnO slurry. Drying Conditions The slip was cast on a gypsum mold to form green bodies (20×70×t3). Before their removal from the mold, they were dried by various drying methods. In oven drying, the green body was dried at 80±3°C (RH 40%) in an oven for at least 24 hours. This drying period appeared to be sufficient to evaporate all free water and most bound water. In air-drying, the green body was dried at room temperature (25±3°C, RH 40%) in an incubator for at least 48 hours. Air-drying required a longer period to reduce water content to an almost constant value. A microwave oven (MW-Master, 2.45 GHz, Mino Ceramic Co. LTD.) was used for microwave drying. The drying temperature was controlled by a proportional integral differential (PID) controller. The green body was heated to 80±3°C at a constant heating rate of 2 K/min, and kept at this temperature for 30 min. All free water and most bound water evaporated rapidly in the microwave furnace. After drying, the green bodies were sintered by a conventional method. The sintering temperature was 1000°C, the heating rate was 10 K/min and the holding time was 2 hours. Evaluation Methods The densities of green and sintered bodies were measured by the Archimedes method. The warpage of green bodies was evaluated using a laser confocal displacement meter (LT-9010M, Keyence Corp.). The microstructures of these bodies were observed on polished surfaces by scanning electron microscopy (SEM, JSM-5600N, JEOL Ltd.). Results and Discussion Figure 1, reprinted from our previous study [13], shows the extent of warpage of the dried bodies examined on their bottom face using the laser confocal displacement meter. The extent of warpage of the dried body is smaller when dried by microwave than by the other conventional drying methods. Figure 2, reprinted from our previous study [13], shows a SEM image of the polished surface of the sintered bodies. The bottom part of the air-dried sample, Figure 2(a), shows many large pores. Local differences in water content arise during the long drying period of the air-dried green body, forming many pores at its the bottom part. In oven drying, many large pores occurred in the upper part of the green body particularly at the surface as seen in Figure 2(b). In this case, the green body is heated from outside generating a temperature difference in the green body, and rapid evaporation of free water to occur from its upper surface, producing many large pores. With the microwave drying, the pores are smaller in number and size than those obtained with other drying methods. Moreover, the pores were distributed uniformly. 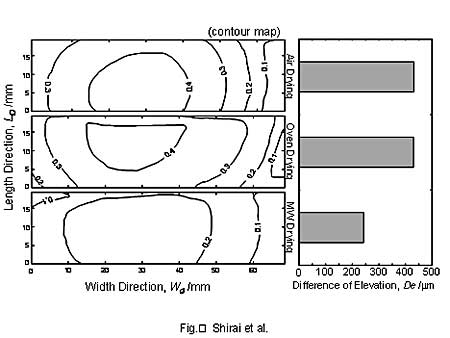 Figure 1. Extent of warpage of dried bodies dried by different drying methods [13]. 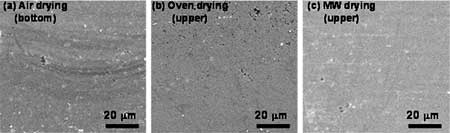 Figure 2. SEM image of polished fractured surface after sintering; (a) air drying in bottom part, (b) oven drying in upper part, and (c) microwave drying in upper part, respectively [13]. Microwave heating is fundamentally different from conventional heating. In microwave heating, heat is generated internally within the material instead of from external heating sources [8]. A material needs to have high dielectric loss for absorbing microwaves efficiently. Figure 3 shows the temperature-time curves for ZnO slurry, water with PAA, water, and ZnO powder heated by a microwave source operating at 2.45 GHz and 150 W. After MW irradiation for 6min, ZnO slurry and water with PAA reached 75°C and 71.4°C, respectively. The results of ZnO slurry and water with PAA show similar temperature-time curves. On the other hand, the temperature of ZnO powder slightly increased to 27°C. Clearly, ZnO powder did not contribute to the increase of temperature under microwave irradiation. In the case of ZnO slurry, water with PAA is heated selectively due to higher dielectric constant compared with ZnO powder. Comparing water with PAA to only water, the rate of temperature increase of water with PAA is higher than the rate of temperature increase of only water, and the temperature reached by water with PAA is almost 20°C higher than the temperature reached by water after 6 minutes. It is considered that a little addition of PAA to water has important effects on microwave absorption. From these results, the free and bound waters with PAA in a green body are selectively heated due to higher dielectric constant compared with ZnO powder, and evaporation and transport of water is done efficiently under microwave heating. The results show that due to an efficient evaporation of water, the water content inside and outside of green bodies dried by microwave heating is very small. Therefore, the extent of warpage is smaller in microwave dried bodies than for the ones dried by conventional methods and their sintered bodies are uniform. 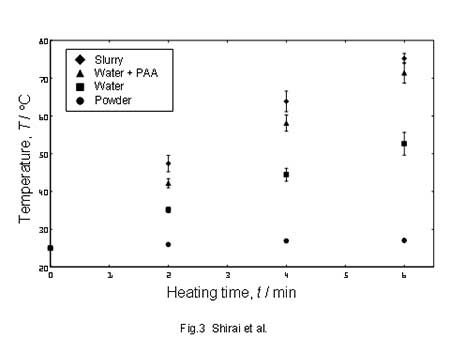 Figure 3. Temperature-time curves for ZnO slurry, water with PAA, water, and ZnO powder heated by a microwave source operating at 2.45 GHz and 150W. Conclusions ZnO slip cast bodies were dried rapidly by microwave drying comparing with those dried by conventional drying techniques. The extent of warpage of a microwave dried body is smaller than when drying by conventional methods. Furthermore, the number and size of pores are smaller for this drying technique than for other drying methods. Clearly, the selective heating by microwaves contributes to uniformities in temperature and water content in a green body during drying. The water content inside and outside of green bodies dried by microwave heating is very small, because the free and bound waters with PAA in a green body are selectively heated due to higher dielectric constant compared with ZnO powder, and evaporation and transport of water is done efficiently under microwave heating. Therefore, the extent of warpage of a dried body is smaller when microwave drying is used compared to other conventional drying methods, and their sintered bodies are uniform. References 1. Y. Hotta, T. Tsugoshi, T. Nagaoka, M. Yasuoka, K. Nakamura and K. Watari, “Effect of Oligosaccharide Alcohol Addition to Alumina Slurry and Translucent Alumina Produced by Slip Casting”, J. Am. Ceram. Soc., 86 (2003) 755-760. 2. K. S. Chou and L. J. Lee, “Effect of Dispersants on the Rheological Properties and Slip Casting of Concentrated Alumina Slurry”, J. Am. Ceram. Soc., 72 (1989) 1622-1627. 3. L. B. Garrido and E. F. Aglietti, “Pressure Filtration and Slip Casting of Mixed Alumina-Zircon Suspensions”, J. Eur. Ceram. Soc., 21 (2001) 2259-2266. 4. N. Omura, Y. Hotta, K. Sato, Y. Kinemuchi, S. Kume and K. Watari, “Slip Casting of Al2O3 Slurries Prepared by Wet Jet Milling”, J. Ceram. Soc. Japan, 113 (2005) 495-497. 5. Y. Shiraki, “Ceramic-Seizo-Process III”, Gihodo Shuppan, (1980) pp. 39-43 [in Japanese]. 6. W. C. Wei and C. L. Hsieh, “Drying Kicetics of Ultrafine Alumina Cake with Drying Control Chemical (DCC)”, J. Ceram. Soc. Japan, 107 (1999) 313-317. 7. I. W. Turner and P. G. Jolly, “Combined Microwave and Convective Drying of a Porous Material”, Drying Technol., 9 (1991) 1209-1269. 8. W. H. Sutton, “Microwave Processing of Ceramic Materials”, Am. Ceram. Soc. Bull., 68 (1989) 376-386. 9. D. Skansi and S. Tomas, “Microwave Drying Kinetics of a Clay-Plate”, Ceram. Int., 21 (1995) 207-211. 10. R. Y. Ofoli and V. Komolprasert, “On the Thermal Modeling of Foods in Electromagnetic Fields”, J. Food Processing and Preservation, 12 (1988) 219-241. 11. P. Jolly and I. W. Turner, “Non-Linear Field Solutions of One-Dimensional Microwave Heating”, J. Microwave Power and Electromagnetic Energy, 25 (1990) 3-15. 12. P. Jolly, “Temperature Controlled Combined Microwave-Convective Drying”, J. Microwave Powder, 23 (1986) 65-74. 13. T. Shirai, M. Yasuoka, Y. Hotta and K. Watari, “Rapid Microwave Drying for Slip Cast Bodies”, J. Ceram. Soc. Japan, 114 (2006) 217-219. Contact Details |