The group of alloys which today make up the family of stainless steels had their beginning in 1913 in Sheffield, England; Harry Brearley was trying a number of alloys as possible gun barrel steels, and noticed that samples cut from one of these trial heats did not rust and were in fact difficult to etch. When he investigated this curious material, it contained about 13% chromium. This lead to the development of the stainless cutlery steels for which Sheffield became famous. Coincidentally development work was also being carried out in France at about the same time which culminated in the production of the first austenitic stainless steels.
The worldwide consumption of stainless steel is increasing. There is growing demand from the building and construction industry where stainless steel is used for its attractive appearance, corrosion resistance, low maintenance and strength. Many other industries are adopting stainless steel for similar reasons as well as the fact that it does not need to be treated, coated or painted when put into service, despite the fact that it is more expensive than plain carbon steels. Evidence to support this comes from the household appliances manufacturers, where there are an ever increasing number of items, traditionally known as ‘whitegoods’, being manufactured in stainless steel.
The Families Of Stainless Steels
Stainless steels are iron-based alloys containing a minimum of about 10.5% chromium; this forms a protective self-healing oxide film, which is the reason why this group of steels has their characteristic "stainlessness" or corrosion resistance. The ability of the oxide layer to heal itself means that the steel is corrosion resistant, no matter how much of the surface is removed. This is not the case when carbon or low alloy steels are protected from corrosion by metallic coatings such as zinc or cadmium or by organic coatings such as paint.
Although all stainless steels depend on the presence of chromium, other alloying elements are often added to enhance their properties. The categorisation of stainless steels is unusual amongst metals in that it is based upon the nature of their metallurgical structure - the terms used denote the arrangement of the atoms which make up the grains of the steel, and which can be observed when a polished section through a piece of the material is viewed at high magnification through a microscope. Depending upon the exact chemical composition of the steel the microstructure may be made up of the stable phases austenite or ferrite, a "duplex" mix of these two, the phase martensite created when some steels are rapidly quenched from a high temperature, or a structure hardened by precipitated micro-constituents.
The relationship between the different families is as shown in Figure 1. A broad brush comparison of the properties of the different families is given in Table 1.
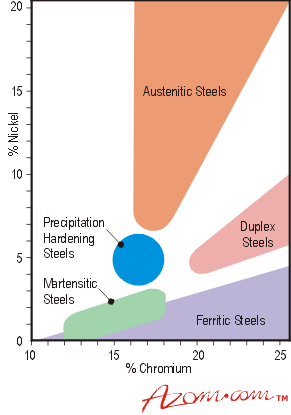
|
Figure 1. Families of stainless steels.
|
Austenitic Stainless Steels
This group contains at least 16% chromium and 6% nickel (the basic grade 304 is referred to as 18/8) and range through to the high alloy or "super austenitics" such as 904L and 6% molybdenum grades.
Additional elements can be added such as molybdenum, titanium or copper, to modify or improve their properties, making them suitable for many critical applications involving high temperature as well as corrosion resistance. This group of steels is also suitable for cryogenic applications because the effect of the nickel content in making the steel austenitic avoids the problems of brittleness at low temperatures, which is a characteristic of other types of steel.
The relationship between the various austenitic grades is shown in Figures 2.
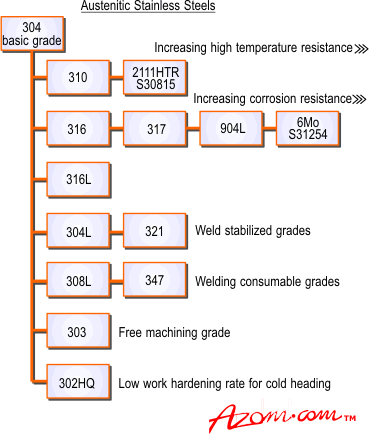
|
Figure 2. The Austenitic Stainless Steels
|
Ferritic Stainless Steels
These are plain chromium (10.5 to 18%) grades such as Grade 430 and 409. Their moderate corrosion resistance and poor fabrication properties are improved in the higher alloyed grades such as Grades 434 and 444 and in the proprietary grade 3CR12.
The relationship between the various ferritic grades is shown in Figure 3.
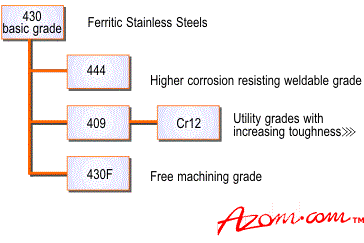
|
Figure 3. Families of ferritic stainless steels.
|
Martensitic Stainless Steels
Martensitic stainless steels are also based on the addition of chromium as the major alloying element but with a higher carbon and generally lower chromium content (e.g. 12% in Grade 410 and 416) than the ferritic types; Grade 431 has a chromium content of about 16%, but the microstructure is still martensite despite this high chromium level because this grade also contains 2% nickel.
The relationship between the various martensitic grades is shown in Figure 4.
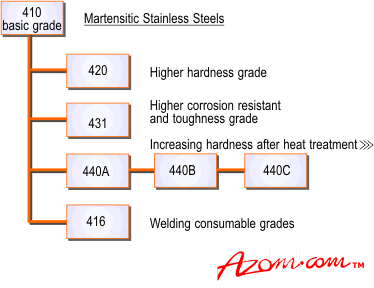
|
Figure 4. The families of martensitic stainless steels.
|
Duplex Stainless Steels
Duplex stainless steels such as 2304 and 2205 (these designations indicate compositions of 23% chromium, 4% nickel and 22% chromium, 5% nickel but both grades contain further minor alloying additions) have microstructures comprising a mixture of austenite and ferrite. Duplex ferritic - austenitic steels combine some of the features of each class: they are resistant to stress corrosion cracking, albeit not quite as resistant as the ferritic steels; their toughness is superior to that of the ferritic steels but inferior to that of the austenitic steels, and their strength is greater than that of the (annealed) austenitic steels, by a factor of about two. In addition the duplex steels have general corrosion resistances equal to or better than 304 and 316, and in general their pitting corrosion resistances are superior to 316. They suffer reduced toughness below about –50°C and after exposure above 300°C, so are only used between these temperatures.
The relationship between the various duplex grades is shown in Figures 5.
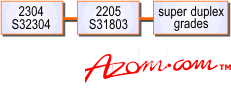
|
Figure 5. The families of duplex stainless steels.
|
Precipitation Hardening Stainless Steels
These are chromium and nickel containing steels that can develop very high tensile strengths. The most common grade in this group is "17-4 PH", also known as Grade 630, with the composition of 17% chromium, 4% nickel, 4% copper and 0.3% niobium. The great advantage of these steels is that they can be supplied in the "solution treated" condition. In this condition the steel is just machineable. Following machining, forming etc. the steel can be hardened by a single, fairly low temperature "ageing" heat treatment which causes no distortion of the component.
Characteristics Of Stainless Steels
The characteristics of the broad group of stainless steels can be viewed as compared to the more familiar plain carbon "mild" steels. As a generalisation the stainless steels have:
• Higher work hardening rate
• Higher ductility
• Higher strength and hardness
• Higher hot strength
• Higher corrosion resistance
• Higher cryogenic toughness
• Lower magnetic response (austenitic only)
• Must retain corrosion resistant surface in the finished product.
These properties apply particularly to the austenitic family and to varying degrees to other grades and families.
These properties have implications for the likely fields of application for stainless steels, but also influence the choice of fabrication methods and equipment.
Table 1 (Part A). Comparative Properties of stainless steel families.
|
Austenitic
|
Generally No
|
Very High
|
High
|
By Cold Work
|
Duplex
|
Yes
|
Medium
|
Very High
|
No
|
Ferritic
|
Yes
|
Medium
|
Medium
|
No
|
Martensitic
|
Yes
|
Medium
|
Medium
|
Quench & Temper
|
Precipitation Hardening
|
Yes
|
Medium
|
Medium
|
Age Harden
|
1 = Attraction of steel to a magnet. Note some grades can be attracted to a magnet if cold worked.
2= Varies significantly within between grades within each group e.g. free machining grades have lower corrosion resistance, those grades higher in molybdenum have higher resistance.
Table 1 (Part B). Comparative Properties of stainless steel families.
|
Austenitic
|
Very High
|
Very High
|
Very High
|
Very High
|
Duplex
|
Medium
|
Low
|
Medium
|
High
|
Ferritic
|
Medium
|
High
|
Low
|
Low
|
Martensitic
|
Low
|
Low
|
Low
|
Low
|
Precipitation Hardening
|
Medium
|
Low
|
Low
|
High
|
3= Measured by toughness or ductility at sub-zero temperatures. Austenitic grades retain ductility to cryogenic temperatures.
Standard Classifications
There are many different varieties of stainless steel and the American Iron and Steel Institute (AISI) in the past designated some as standard compositions, resulting in the commonly used three digit numbering system. This role has now been taken over by the SAE and ASTM, who allocate 1-letter + 5-digit UNS numbers to new grades. The full range of these standard stainless steels is contained in the Iron and Steel Society (ISS) "Steel Products Manual for Stainless Steels", and in the SAE/ASTM handbook of Unified Numbering System. Certain other grades do not have standard numbers, but are instead covered by other national or international specifications, or by specifications for specialised products such as standards for welding wire.
|