Superplasticity is an ability of a material to deform plastically by many hundreds or thousands of percent. Contrast this with the ductility normally found in metals and alloys, which is less than 100%. The phenomenon is strain rate sensitive, which means that the strain rate at which sheet material is formed is crucial to its ability to adapt to a die surface, rather than perforate prematurely. The flow stress of the material is also dependent on strain rate, and usually increases with increasing strain rate. The current world record for superplastic ductility is 8000%, observed in a commercial bronze alloy. Dental Implants The idea to use superplastic forming started when a dental practitioner was looking for a method of producing dental implant superstructures with passive fit. Implant superstructures are usually made by the lost-wax casting method, and are gold alloy beams that fit directly onto metallic components called abutments that protrude through the soft tissues of the mouth and which are themselves attached to machined titanium components known as dental implants. The dental implants are sited in the hard bone tissues where intimate contact occurs between the metallic component and the natural tissues. The superstructure is screwed to the abutments and teeth are then placed along the beam in an aesthetic fashion, figure 1. Patients prefer this form of fixed bridgework as it is more reminiscent of their natural teeth than a denture. For the whole prosthesis to have the optimal chance of success, there must be no misfit between the beam and the abutments due to its screw fit. Any such discrepancy is likely to strain the prosthesis, leading to loosening or fracture of retaining screws or even the demise of an implant. However, 25% of castings do not have this passive fit, and sectioning and re-soldering of the casting is not uncommon in an attempt to correct this problem. 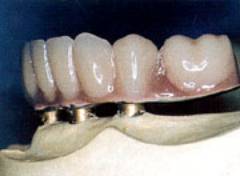 | Figure 1. A typical dental implant superstructure. | Superplastic Forming Advantages of Superplastic Forming Superplastic forming was seen as a means of producing superstructures with consistent passive fit without the need for sectioning and re-soldering. What was more, we could produce the superstructure in a titanium alloy that was similar in nature to the implant material and abutment components (commercially pure titanium), thus reducing potential galvanic effects. The titanium alloy had the added advantages that it was extremely lightweight in comparison with the gold alloy and very strong. Other advantages to using superplastic forming included the fact that superplastically formed material would only need to be heated to 0.6 Tm (K), so that problems associated with thermal mismatch of the investment material, casting shrinkage and porosity would be avoided. In addition, the slow strain rates of between 5 x 10-4s-1 and 1 x 10-4s-1 used for forming the components would reduce the likelihood of internal stresses leading to dimensional changes on cooling. Equipment Requirements Work described herein utilises a 20-ton superplastic forming press designed and built by Fielding and Platt International, Chester Hydraulics Division, with major work on the induction coil and control system being completed by IPW. Possible Problems with Superplastic Forming In fact, the only concerns for forming components were associated with the hypothesis that low-cost tooling in the form of dental casting investments could be used for the superplastic forming tools. The demands on such a material would be three-fold. Firstly, did the material had sufficient hot strength and dimensional stability to withstand variable forming loads for periods of up to three hours without fracture or distortion at forming temperatures around 900°C? Secondly, could the thermal expansion of the investment materials be matched to those of the titanium alloy to achieve passive fit, and thirdly, would the handling of the investment material to produce dies be cost effective and relatively straight forward to comply with patient treatment schedules? When is such an Implant Required? In order to produce an appliance by this method the dentist first identifies the need for a specific device - reasons for using a metal-based appliance as opposed to acrylic include sensitivity to constituents of the acrylic, usually unreacted monomer; the lack of space for opposing teeth, particularly on the molar regions, where there is a need for thin sections of material covering the ridges, but also a requirement for strength; and overall strength because the patient is prone to fracturing the more traditional appliance made solely in acrylic. The Process The dentist takes an impression and passes this on the dental technician who prepares a master model in stone. This model is modified as necessary for the production process and then duplicated in investment material to produce the core of the die for superplastic forming. The investment model is placed in a Perspex chamber and surrounded by more investment to determine the orientation of the model with respect to the forming sheet. This completed die can then be placed directly into the press where an induction coil is used to heat it to 900°C in 90 minutes. Once a disk of titanium alloy of 140 mm diameter has been inserted into the press, figure 2, and clamped above the die, argon gas is used to ‘blow’ the metal sheet onto the die surface. A predetermined pressure-time profile will be used to achieve complete adaptation of the metal sheet to the die surface. It is extremely important that as much detail as possible is transferred to the metal sheet for adequate retention of the appliance in the mouth. Forming times can be as long as three hours for the more complex shapes and argon gas pressures can reach approximately 600psi. At this stage the titanium sheet is removed from the die surface with relative ease. 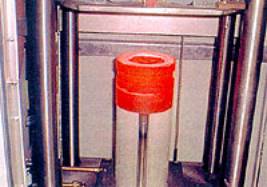 | Figure 2. A Ti-6Al-4V disk shown above the preheated tooling. | Potential of Superplastic Forming Soon after the project commenced, dentists soon became aware of the potential of titanium alloy prostheses for other applications such as upper denture bases for partial dentures, figure 3a, hollowed bulb obturators, implant overdentures, ridge augmentation membranes and complex plates for cleft palate prostheses, figure 3b. The most obvious advantages that were immediately apparent to all were the degree of adaptation of thin titanium alloy sheet (0.7 mm) to the investment die and the tremendous reduction in weight compared to cobalt-chromium alloys, the most likely alternative material. Both features would increase the comfort of wear and reduce the bulk of the titanium alloy based denture. Now regular requests are being made for titanium plates that form the basis of a patient prosthetic device for restoration of oral function. 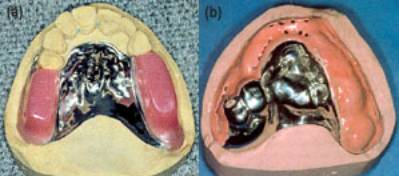 | Figure 3. (a) Upper denture base for a partial denture and (b) a complex plate for a cleft palate prosthesis. | Initial concerns with dies made from investment casting materials have been almost completely assuaged. The principal dental casting investments used for the project have been based on phosphate-bonded investments consisting of a refractory filler such as SiO2 and a binder of magnesium ammonium phosphate. There is some interaction between the surfaces of filler particles and binder that gives the material added strength. A lack of strength does not seem to be a problem during superplastic forming unless the metal sheet is too thick when increased forming pressures are required and unsupported areas of the die are subject to shear stresses. This was found to be the case in the forming of ridge augmentation membranes, so forming times were increased and the orientation of the form within the die was changed to reduce these stresses. No distortion of the dies has been observed even for forming times as long as three hours. Investment Materials The SiO2 particles in the investments are of various allotropic forms and these undergo displacive transformations on heating. These result in considerable expansion of the material to compensate for the shrinkage of the alloy on cooling during casting. By such means dental appliances can be made to fit exact replicas or models of the teeth in a person's mouth. There is also some expansion of the investment material as it sets. An investment mould is prepared by mixing the powdered material with either water or a solution of colloidal silica. If colloidal silica is used the amount of setting expansion can be controlled by diluting with water to specific ratios. These variables can also be used to control the setting and thermal expansion characteristics of the investment materials to match the thermal contraction of the titanium alloy sheet from the superplastic forming temperature. More recently new investment materials have been marketed for casting commercially pure titanium. These investments are based on alumina, spinels, zirconia and magnesia. The objective in developing these investments has been to minimise the interactions between molten titanium and the investment moulds on casting so as to lower the levels of a-case formation. In the magnesia-based investment the expansion is controlled using zirconium, which is converted to zirconia on heating. As this reaction occurs, so the investment expands. The expansion characteristics of these materials is being studied to develop suitable die materials for dental superplastic forming to achieve the passive fit required for dental implant superstructures. Clinical Results A range of dental appliances has now been produced using superplastic forming, some of which are currently in service. In Japan, more extensive studies of complete upper denture bases have been made using superplastic forming and several thousand people have been fitted with these appliances. The feedback from both study groups is very similar. Dentures are said to be comfortable to wear, are lighter and better fitting, provide more extensive tongue space and allow more distinct pronunciation, allow good taste from food without metallic taste sensations, are more sensitive to temperature changes in foodstuffs and exhibit reduced adhesion of food debris. Similar complete upper denture bases produced by superplastic forming are also now available in Russia. Applications Some applications of these plates are extremely complex and include forming over gold crowns and copings, over natural teeth, and into areas where tumours have been removed or are the result of clefting. |