Vacuum plasma processing is already a well-proven and widely-used technique for etching and surface modification in the electronics industry. It is being increasingly used by the aerospace, automotive, medical, military and packaging industries for cleaning and surface engineering of plastics, rubbers and natural fibres as well as for replacing CFCs for cleaning metal components. Range of Application Applications range from cleaning tiny components like ball point pen nibs, through surface engineering of reels of web and film materials, to adhesion promotion of whole automotive plastic bodies. There are only two real constraints - can the product fit into the vacuum chamber, and is it vacuum compatible? If the product is too big or if under vacuum it would continuously produce evolvements, such as moisture or gases, then it is not be suitable for plasma treatment. What is it used for? Vacuum plasmas can be used to clean surfaces and remove organic residues, or to promote adhesion before painting, lacquering, printing, electroplating or adhesive bonding. Materials can be modified or ‘surface engineered’ to change the surface properties without affecting the bulk material. Surface Engineering Surface engineering can improve properties such as frictional behaviour, lubricity, heat resistance, cohesive strength of films, surface electrical conductivity, or dielectric constant, or it can make materials hydrophilic or hydrophobic. Adhesion For good adhesion, thorough and consistent surface cleaning is essential, but is often difficult to achieve. After mechanical cleaning or surface preparation, loosely attached particles are often left on the surface. Aqueous cleaning tends to dissolve localised bulk residues but then, on evaporation, redeposit them as a thin film over the whole surface. This film can be extremely difficult to remove except by plasma or other radiation treatments. Vacuum plasma cleaning can remove all residues and leave the surface ‘atomically clean’. Adhesion Promotion Adhesion promotion can be achieved using reactive gases. These produce chemical species and free radicals, which react with or deposit onto the surface, improving the affinity to the adherent surface by forming chemical or electrical bonds. Non-reactive, noble gas plasmas with heavy ions cause topographical changes to the surface and thereby improve mechanical bonding. They can also create surface radicals through mechanical damage to the atomic structure. These radicals can then participate in surface reactions and bonding. The Process Vacuum plasma treatment is a low temperature process, typically at 40-120°C, which can thus avoid thermal damage. The process can induce non-thermally activated surface reactions, causing surface changes which cannot occur with molecular chemistries at atmospheric pressure. These unique properties can open up new opportunities for materials and products. Plasma processing is conducted in a controlled environment inside a sealed chamber, which is maintained at a medium vacuum, usually 13-65 N.m-2, by the introduction of selected gases, figure 1. The gas or mixture of gases is energised by an electrical field from DC to microwave frequencies, typically 1-5000 W at 500 V. The components to be treated are usually electrically isolated. The volatile plasma by-products are evacuated from the chamber by the vacuum pump, and if necessary can be neutralised in an exhaust scrubber. 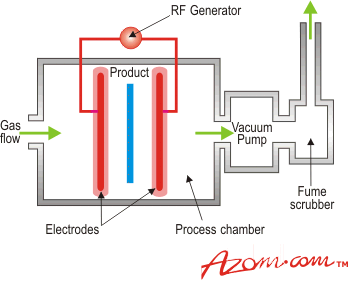 | Figure 1. Schematic of a typical vacuum plasma system. | Unlike liquid cleaners and etchants, which use only molecular chemistry, plasmas employ molecular atomic, free radical and metastable species for chemical effects, and electrons and positive ions for kinetic effects. Plasmas also generate electromagnetic radiation, in the form of vacuum UV photons, which can penetrate bulk polymers to a depth of about 10 µm. This can cause chain scissions and cross-linking. Ionisation tends to occur at higher energies than chemical dissociations. Typically, for a reactive gas, 104 in 106 molecules form free radicals whereas only 1 in 106 ionises. Hence for reactive gases, the predominant plasma effect is from free radicals, but with careful selection of process parameters using noble gases, ionic effects can predominate, figure 2. 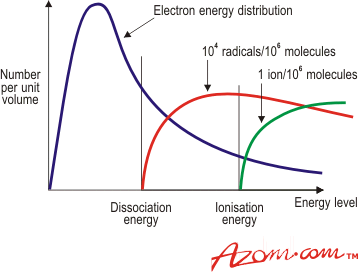 | Figure 2. Electron Energy distribution. | Because plasmas affect materials at an atomic level, it is often necessary to use surface analysis techniques such as scanning electron microscopy and X-ray photoelectron spectroscopy to identify the processes required and to judge their effects. However, as a simple indication of surface energy, and hence adhesion or wetability, a water droplet contact angle test will often suffice. The lower the contact angle, the higher the surface energy and more hydrophilic the material, figure 3. 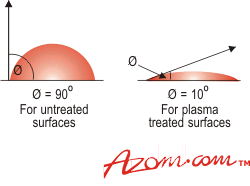 | Figure 3. Contact angle of a water droplet. | Machine Configurations Machines for plasma processing can be configured according to the product and process. Components can be mounted in trays or baskets or tumbled in a drum, and web or film material can be processed in a reel-to-reel configuration. The electrode design depends upon the product and the process. Where a planar surface is treated, parallel plate electrodes with an unidirectional plasma can be employed. For three dimensional components, electrodes providing an isotropic plasma effect are required. Disadvantages of other Plasma Processes Flame, DC corona discharge and atmospheric AC plasma processes are customarily used for surface treatments, and are well suited for continuous production. All, however, have significant limitations for stringent applications. Flame plasmas can cause damage by thermal energy. Corona discharge plasmas tend to have low energy densities and are relatively ineffective, and can cause damage by the accumulation of electrical charge. AC atmospheric plasmas need very high energies, which can damage materials. If a process is conducted in air or in an uncontrolled environment, the treated surfaces can be recontaminated by airborne contaminants or by-products of the process. These processes restrict the free radicals and chemical species available to the surfaces. Dedicated profiled tooling is usually required for simple three dimensional products and none of the processes are suitable for more complex shapes. Advantages of Vacuum Plasma Processing The vacuum plasma process avoids damage to materials as it is a controlled, low temperature process with low energy densities. The plasma energy is highly efficient because the vacuum pressure reduces recombinations, and increases the mean free path length of the particles resulting in higher ionic kinetic energies. In the controlled environment of a vacuum plasma, precise surface engineering effects can be achieved with the careful selection of the plasma gases and process parameters. Different gases can be used sequentially to achieve different effects. Applications Applications for vacuum plasma process’s are many and varied. Some include: • Polypropylene automotive components such as car bumpers, door mirror housings and dash board components are plasma treated before painting • ABS components before the application of wood grain effect transfers • PTFE surface wetability and bondability is achieved by plasma treatment,thus avoiding the use of hazardous liquid chemistries • Plasma pretreatment of polyethylene mouldings, with wax and ether inclusions, for adhesion of water-based epoxy adhesives, solvent-based adhesives and electroless copper plating has proved successful. This has replaced a chromic acid process, for health and environmental reasons • A woven wool and nylon material has been successfully plasma treated in web form for bonding to sheets of natural rubber, forming a composite that is used for waterproof rainwear. Many continuous polymer film materials have been plasma treated in reel-to-reel form for improved adhesion of ink jet printing, surface wetabllity and improved affinity to blood products • Bacterial, fungal and biological organisms can be removed from medical products using plasma treatment. The strength and reliability of the bond between the needle of a hypodermic syringe and its polypropylene holder is critical. Plasma treating the assembled components in a tumbler before the application of an epoxy adhesive greatly improves the product. Summary Plasma technology has many advantages thermodynamically unfavourable reactions can be achieved at low temperatures, surfaces can be cleaned with no residues, and it eliminates the need to use primers and pretreatments for adhesion promotion. Modification of the mechanical, electrical, chemical properties of materials is possible, and the process is environmentally friendly with negligible health and disposal hazards. Computer control of all the variables in a process ensures quality and repeatability. |