In 1976, Howmet Corporation became the first company to offer hot isostatic pressing (HIP) services to the aerospace industry. The HIP process, which subjects a component to elevated temperatures and pressures to eliminate internal microshrinkage, helped engineers respond to the aerospace industry’s increasingly stringent regulations. HIP enabled engineers to design components so they could meet specifications for use in critical, highly stressed applications. The HIP’ing Process The HIP process provides a method for producing components from diverse powdered materials, including metals and ceramics. During the manufacturing process, a powder mixture of several elements is placed in a container, typically a steel can. The container is subjected to elevated temperature and a very high vacuum to remove air and moisture from the powder. The container is then sealed and HIP’ed The application of high inert gas pressures and elevated temperatures results in the removal of internal voids and creates a strong metallurgical bond throughout the material. The result is a clean homogeneous material with a uniformly fine grain size and a near 100% density. Advantages of HIP’ed Materials The reduced porosity of HIP’ed materials enables improved mechanical properties and increased workability. The HIP process eliminates internal voids and creates clean, firm bonds and fine, uniform microstructures. These characteristics are not possible with welding or casting. The virtual elimination of internal voids enhances part performance and improves fatigue strength. The process also results in significantly improved non-destructive examination ratings. HIP and Maching One of the primary advantages of the HIP process is its ability to create near-net shapes that require little machining. Conventional manufacturing methods use only 10-30% of the material purchased in the final product the rest is removed during machining. A HIP’ed near-net shape part typically uses 80-90% of the purchased material. As a result, machining time and costs are significantly reduced. The strong combination of improved raw material use and greater machining efficiency that results from the HIP process has driven the growth of HIP’ed powder metal parts manufactured from nickel-based and titanium alloys. In fact, HIP has become the standard ‘bill of material’ on virtually all powder metal components produced by Howmet’s HIP operation. What Type of Things can be Produced by HIP’ing? The HIP process enables engineers to produce materials of all shapes and sizes, including cylindrical billets, flat rectangular bar billets, solid shapes with complex external geometry, and complex shapes with internal cavities. Because powder metals do not have the directional property characteristics of forgings, the HIP process can produce materials from metallic compositions that are difficult or impossible to forge or cast. Howmet’s expertise in HIP powder compaction is displayed in the manufacture of abrasive tips, figure 1. Abrasive tips are uniquely layered compacts of ceramic and metallic powders which are used for turbine blade wear protection. 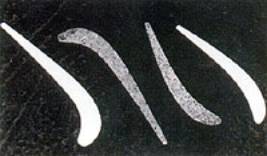 | Figure 1. Ceramic and metal sides of finish machined abrasive tips | What HIP’ing can be used for The HIP process is now not only used for densifying castings, but in many other applications such as diffusion bonding of dissimilar materials, component repair and powder metal consolidation. In the powder metal market, Howmet applies HIP technology in four separate areas: • Consolidation of powder metals (PM) • Creation of PM shapes • Production of near-net shapes • Cladding. Cladding Another fundamental application of the HIP process is cladding. Cladding is the selective bonding of hardfacing materials onto various substrate surfaces. A less expensive material is coated with a thin layer of powdered metal, creating a buffer on its wear surface. This reduces costs by placing expensive, wear resistant materials only where they are needed. As a result, wear resistant properties are improved without incurring unnecessary cost penalties. An additional benefit of cladding is that it can create bonds between otherwise incompatible materials such as metal, intermetallic, and ceramic powders. Most notably, cladding is used in the production of diesel engine valve lifters, figure 2. Here, the hardfacing material (tungsten carbide) is bonded to a lower cost material such as an alloy steel. Howmet has also used this capability in a number of other industries, such as the offshore and plastic extrusion equipment industries, where cladding is used to fortify various components including valve bodies, thick wall casings, and compound tubes, figure 2. 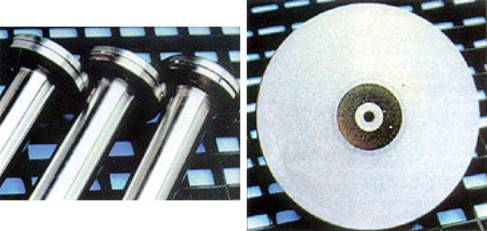 | Figure 2. Left, diesel engine valve lifters with HIP clad carbide hardfacing and right, cross section of 4140 steel extrusion barrel with HIP clad inside diameter of nickel alloy hardfacing. | Areas where HIP’ing is Utilised Today, HIP has expanded well beyond aerospace products and is finding new applications in a range of industries, including automotive (turbocharger wheels and diesel engine valve lifters), medical (prosthetic devices), petroleum (valve bodies) and chemical processing. HIP offers engineers in these industries greater design freedom than was previously possible with conventional processes such as forging and casting. Parts which cannot be made by the more conventional processes are now possible using HIP, figure 3. An example of this is the dual alloy wheel. In this the hub, which is made of a HIP consolidated powder metal, is bonded to a cast outer ring through the use of the HIP process. The resulting part has excellent tensile properties in the hub and high stress rupture properties on the outer ring. 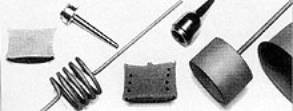 | Figure 3. A Selection of parts made by HIP’ing | HIP in the Gas Turbine Industry A rapid rise in the use of the HIP process followed the intensification of standards within the gas turbine industry. These standards required the elimination of shrinkage porosity in investment cast components, such as increasingly complex airfoils. HIP vs Conventional Foundry Technology Conventional foundry technology was not up to the task. By developing HIP, Howmet met mechanical property requirements and eliminated shrinkage porosity defects. HIP provided the means to produce the desired high density, fine grain material. Summary Since it’s inception in 1955, the use of the HIP has grown steadily in the powder metal and casting densification fields. During the last 25 years, HIP has become a proven process in the production of aerospace and industrial gas turbine parts, and the future looks bright. New markets have developed for rocket engines, satellites and aerospace airframe castings. HIP continues to be used more frequently in the production of powder metal parts and shapes. Cladding and near net shape technology are on the rise with significant growth expected in the production of sputtering targets. As with any technology, awareness by industry is the key to growth. With this in mind, a HIP council was recently formed consisting of equipment manufacturers and HIP suppliers. The inaugural meeting of the Hot Isostatic Pressing Council of the Advanced Particulate Materials Association took place on 30 August, 1999 at Bodycote IMT, Andover, Massachusettes. This council will now address the areas of safety, marketing and technology, to further enhance the capabilities of the HIP process. |