Feb 21 2001
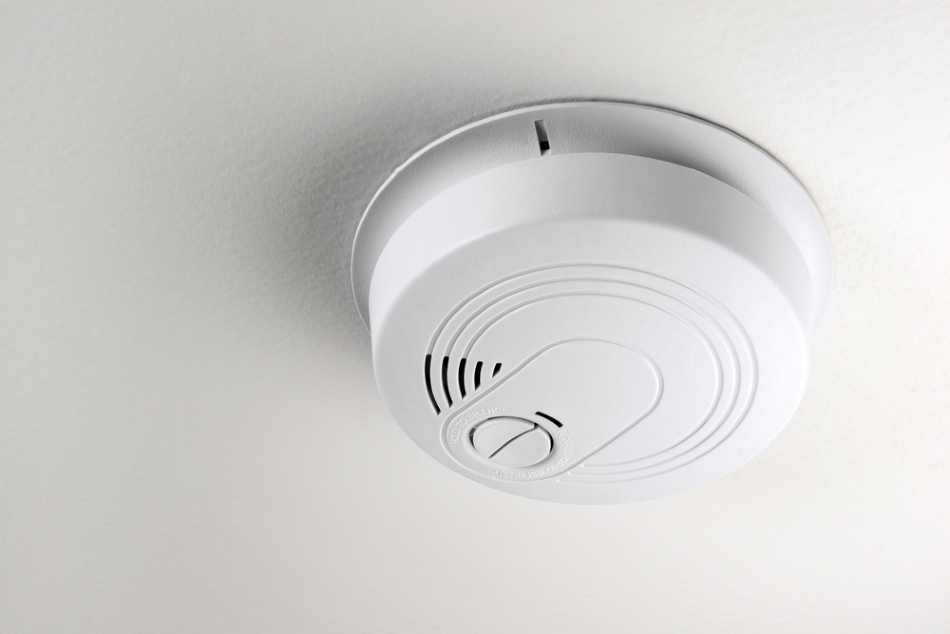
Image Credit: Chimpinski/Shutterstock.com
Article updated on 12/02/2020 by Ben Pilkington
Ceramic springs have been around as scientific novelty items since the 1970s, produced by a special processing technology. An early example, made at Imperial Chemical Industries (ICI) in the UK in the early 1980s, is the cement spring, which achieved celebrity status.
Researchers at the University of Birmingham (UK) have been carrying out speculative research work on ceramic springs and, with Applied Functional Materials Ltd., which is a spin-out company from the university, have arrived at some exciting potential applications for these devices which, until recently, were regarded merely as an interesting peculiarity. If a piezoelectric ceramic material such as lead zirconate titanate (PZT) is used to form a spring, a number of useful things start to become possible, including a revolutionary new method for making audio speakers. Such ideas and devices all rely on some clever ceramics processing and the phenomenon of piezoelectricity.
Viscous Polymer Processing (VPP)
The ICI industrial research group responsible for the cement spring also made other ceramic springs as a by-product of research into what became known as viscous polymer processing (VPP). This technique creates a highly viscous children’s modeling clay-like material, composed of fine ceramic powder particles dispersed in a polymer and solvent gel structure. The material is formed using very high shear forces to break apart any agglomerates in the powder, which are the main cause of defects in brittle materials like cement and sintered ceramics.
This results in dense, very uniform and mechanically strong ceramics. Viscous processed materials can be twice as strong as those processed conventionally. In addition, because the material is highly plastic in its ‘green’ formable state, products of all shapes can be made, all the while retaining the advantages of high strength and easy processing. Springs of various forms are ideal for demonstrating this process, as a spring structure can be highly stressed in a uniform and visible way, usually by hand. The sight of a ceramic material being elastically deformed to an apparently large degree changes many people's view of the capabilities of ceramics.
Piezoelectics
In addition to VPP, piezoelectricity is a key factor in recent work at AFM. Piezoelectricity is an electromechanical phenomenon common to many different materials, but usually only when they are in single-crystal form. This material property is related to the alignment of atoms in a crystalline lattice, which results in a net polarization and a consequent link between the electric field and material strain. The most widely known piezoelectric material is quartz, slivers of which are found in every digital watch and computer, producing very stable vibrations at high frequencies.
It is important to note that the most common piezoelectrics are based on polycrystalline ceramics. After conventional ceramic processing, these materials can be ‘poled’ to imitate the single-crystal effect – usually to a much greater degree. The poling process, which is analogous to that used in magnetic materials, uses a high electric field and an elevated temperature to align the microscopically small piezoelectric domains within the polycrystalline material. This produces a net polarization in the direction of the field. The residual polarization after removal of the field allows smaller electric fields to produce mechanical strains in the direction of poling.
Applications
Gas Igniters
Applying an electric field across a piece of piezoelectric material causes a slight corresponding strain to be developed in the direction of the field. Conversely, applying a strain causes an electric field to be set up across the material. In Figure 1, this process is illustrated for a simple cylindrical piezoelectric device. The strains involved in the operation of a typical device are very small and generally no larger than 0.1%.
Such solid blocks are the basis for piezoelectric gas igniters; in fact, a large impact on a block generates a voltage sufficient to create a spark. There are also many other applications of igniters in high-frequency applications such as ultrasonic probes, in which the displacements involved are inherently very small, or for extremely accurate micro- and nano-positioning, such as for atomic force microscopy.
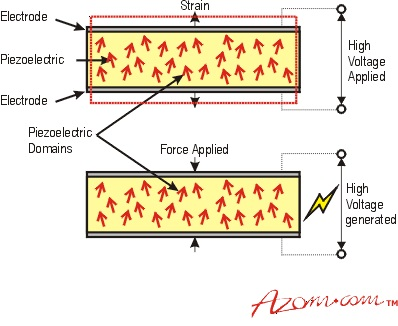
Figure 1. When a voltage is applied across a poled electrode piezoelectric device, the material expands in the direction of the field and contracts perpendicular to the field. When a force is applied to the piezoelectric material, an electric field is generated.
Piezo-Sounders in Smoke Alarms
Amplification techniques can be used to get more apparent strain out of piezoelectric materials. The most common device used to amplify the effect is the unimorph, as shown in Figure 2. The unimorph is a plate of piezoelectric material stuck to a metal disc. If the piezoelectric layer within the unimorph attempts to contract or expand under the electric field, the disc flexes, causing the center of the disc to move relative to the edge. This is the same mechanism by which the piezo-sounder, which is an extremely widely used ceramic piezoelectric device found in telephones, smoke alarms, high-frequency tweeters and many other items, works.
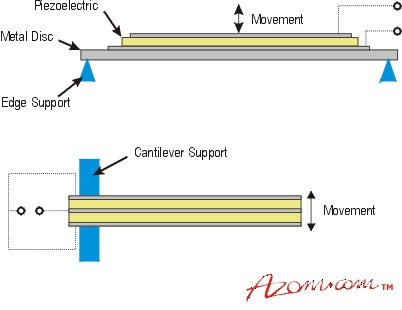
Figure 2. A unimorph bending device. When a thin disc of piezoelectric material is bonded to a metal substrate, a voltage application subsequently causes the device to bend and produce amplified movement or sound in the direction perpendicular to the plate. The lower graphic shows a bimorph bender making a sandwich structure with an internal electrode allows one half to push while the other pulls, giving twice the movement of a unimorph
Video Read Heads
For more technical applications, piezoelectric bimorphs are used, as demonstrated in Figure 2. Piezoelectric bimorphs are mirrored unimorphs, in which the electrodes are engineered so that one layer pulls while the other pushes, thereby causing an increase in bending. These devices are used in applications that require more movement with small forces. The most common application is the video read head adjuster, which eliminates interference when freeze-framing a video recording.
Piezoelectric Springs and Loudspeakers
For extra actuation, things start to get difficult with ceramic piezoelectrics. Making a longer bender device does allow for increased actuation; however, this must occur at the expense of reduced forces and increased fragility. One possible way to solve this problem is to create a more flexible structure, such as a spring.
Before considering springs as actuators, it is easier to look at a piezoelectric spring generating electrical signals, as opposed to movement. Springs like this are formed in the green ceramic state by winding an extruded tube on to a former of the required diameter and pitch. The spring is then sintered on a refractory ceramic former of a size that allows for sintering shrinkage.
Applying electrodes to the former and the outer surfaces of the tube, while also poling the material in the radial direction, produces a vibration-sensing device. As the spring is very flexible, the resonance can be tuned to frequencies as low as 10Hz, with an appropriate seismic mass. The device then becomes a competitor to the more conventional electromagnetic geophone. The actuation effect is not great, and the spring cannot provide much in the way of force or displacement, unless at resonance.
With the correct electrode configuration, displacements as large as several millimeters (mm) can be achieved from such a spring. However, while a significant improvement on the simple spring form, this type of device is also inefficient. This is because all of the material between the electrodes is not activated to the same degree, and the material underneath the electrodes simply hinders movement.
This information, therefore, warrants the question - what kind of piezoelectric spring can generate the sort of movements that may be useful? The one potentially ground-breaking device is a revolutionary new digital loudspeaker that has been proposed by UK company Cambridge Mechatronics Ltd. The Cambridge Mechatronics loudspeaker is made up of an array of small, identical, independently driven transducers, each of which has a piezoelectric spring inside, as shown in Figure 3. The active part of the transducer is in the form of a bender, which is similar to that which is found in bimorph devices but is instead coiled around an inner core containing a bearing and moveable core.
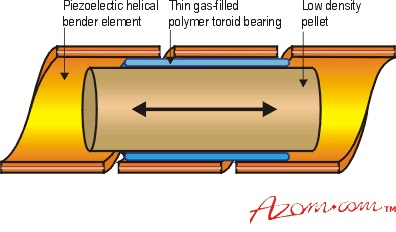
Figure 3. A cut-away diagram of the digital loudspeaker driver unit.
When actuated, the bender attempts to coil or uncoil, which affects the pressure inside the linear bearing. If this coiling is made to be greater at one end than the other, or if the internal core is tapered, the core will be forced to move along the axis of the coil in line with the applied voltage. This action is similar to that which is produced by a hand squeezing a wet bar of soap – the harder you squeeze, the faster the soap shoots out. The key is that a small movement in the ‘squeeze’ produces a much larger movement in the core. This movement generates movement in the air next to it and therefore produces noise.
Through a trick of human audio perception, an array of these devices produces a coherent sound image away from the speaker. This is in some ways analogous to a computer or smartphone display screen, made up of many tiny elements, otherwise referred to as pixels, which in themselves are meaningless, but, when put together, create an image.
From a laboratory curiosity with no apparent applications, piezoelectric ceramic springs have become an exciting new interdisciplinary research area. These structures show great potential for new types of actuators and sensors, and these springs, in their various forms, could greatly expand the realm of piezoelectric materials and make them an even more integral part of modern technology.