EMAG Automation’s ELC 250 DUO is a compact laser welding system that is designed for use on gear components. The ELC laser welding system is built as a DUO alternative with twin spindles. The system’s two-station operation makes it feasible to load and unload the spindles synchronously with the cycle time.
Turn-key welding system for the laser welding of differential gear housings
The ELC 250 DUO laser welding system has a dependable focus on productivity. The dual-spindle structure of the laser welding system, integrated with the characteristic EMAG pick-up principle of self-loading spindles, allows for completely automated use of the laser welding machine both as a standalone machine and in a production line.
The application of pick-up spindles offers numerous benefits: Firstly, this principle allows for the employment of fixed lenses as it is the workpiece that moves, not the tool. Moreover, it allows for a parallel cycle time for loading and unloading, decreasing idle times. The safety benefits owing to the fixed lenses are not to be undervalued. The lasers are at all times directed toward the inside of the machine, which ensures optimal protection for the user. The optimal beam guidance ensuing from this and the selective extraction prevents contamination of the lenses during the welding process.
The ELC 250 DUO laser welding system can be fitted with the modern laser technology based on the requirements of the component and the customer's stipulations. It should be taken into consideration that although the process happens at two stations in the ELC 250 DUO, only one laser source is needed. The laser beam is just switched back and forth between both welding stations. The laser's switching between the focusing optics is regulated by a beam switch. The occupancy rate for the laser is consequently optimized, boosting productivity during laser welding.
Advantages
- Wide-ranging integration of workhandling and laser-welding decreases the number of machining operations in the production process
- A CNC mating press joins synchro and gearwheel
- High productivity because of short idle times and rapid, safe set-ups
- The joining process is observed by an integrated force/stroke monitor
- Magnetic preheating of difficult components (without adverse effect on the cycle time)
- Enhanced workholding technology decreases distortion of the synchro
- All quality-defining parameters are NC-controlled and can be replicated at any time
- To safeguard production, actual values are monitored
- The use of high-tech CO2 lasers with the best beam quality results in flawless welding seams
- The space-saving, compact design decreases the installation effort and boosts reliability
- Can be combined with any automation system
Workpieces / Technologies
Workpieces
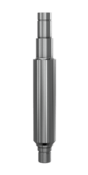
Rotor shaft (electric motor)
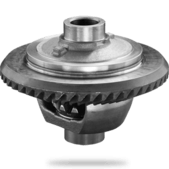
Differential housing
Technologies
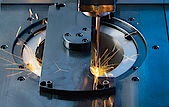
Laser welding
Laser Welding System for Powertrain Components – ELC 250 DUO