Pyrometric cones are used worldwide to keep an eye on ceramic firings in small hobby kilns, industrial kilns, and pottery kilns, where maintaining a constant temperature is crucial to the quality of the finished product. Pyrometric cones quantify temperature, time effect, and heat work.
Even when "nothing has changed," kilns occasionally deviate from their setpoint over time. Pyrometric cones can detect minute changes in a kiln or reveal when ceramic firing is under control, enabling the user to make corrections before they affect ware.
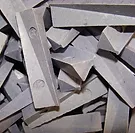
Image Credit: Orton Ceramic Foundation
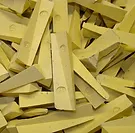
Image Credit: Orton Ceramic Foundation
All Users Need to Know About Cones
Orton pyrometric cones were created in the late 1800s to give ceramicists a way to gauge the firing of their creations. However, despite this, the cones have withstood the test of time and are still used today to confirm the combined effects of temperature and time (also known as heat-work) on ceramic products worldwide.
Though the controllers cannot detect heat work, the introduction of electronic controllers in conjunction with thermocouples has undoubtedly been beneficial in controlling the firing cycle of ceramic kilns.
Cone development began with the idea that a mixture of ceramic elements mixed to precise ratios should behave similarly to the ceramic objects fired in the kiln. After much effort, the initial hypothesis was verified, and several mixes with very consistent temperature deformation and high reproducibility emerged.
After more research, it was discovered that a thin, triangular pyramid shape was the most effective cone shape. The variables that affected the cone's accuracy were also found, and techniques were created to let the ceramist account for processing variables.
Cones are useful for verifying the reproducibility and thermal homogeneity of the heat work produced by a particular heating profile. The heating rate during the last 100 °C (180 °F) of the firing profile and the final temperature determine the final degree of cone bending.
It is crucial to remember that the cone bends over a very narrow range of temperatures; in other words, even while the cone's degree of bending seems large, it might only represent a few degrees. Since many ceramic goods share the same materials, their temperature sensitivity is no greater than that of a cone.
Cones are useful for verifying that the kiln produces the desired amount of heat work each time a specific heating profile is applied and for confirming that, when many cones are put within the load setting, the heat work is being supplied uniformly inside the kiln ware load.
Selecting the Proper Cones
The Orton Cone Temperature Equivalents Chart determines which cone number is required, The use of Orton's self-supporting cones will take care of the problem of the appropriate mounting height and angle.
Example: Firing to 1147 °C with a final 100 °C heating rate of 75 °C/hr, choose the closest heating rate column, such as 60 °C. Scan down to 1147 °C, falling between the temperature equivalents for cone 2 and cone 3. Consequently, the target cone is cone 3. For profiles involving a maximum temperature soak, consider raising the target cone by one to two cones for a one-hour soak and two to three cones for a two-hour soak.
Initially, users should choose one cone number above and one cone number below the target cone once they have determined the cone number they need for the kiln's firing profile. To find the precise match for the firing profile, fire a test burning of all three cones in the kiln. Using the Orton cone measurement template, calculate the distortion of the target cone.
If the final position of the target cone after firing falls within the range of 25 to 75 ºC, users have chosen the appropriate cone for the kiln's profile. Templates for this purpose are accessible from Orton.
Now it is time to leverage the cones for assessment. To evaluate the uniformity of heat-work in the kiln, position the three-cone series at the top, middle, and bottom, as well as on the right, center, and left. Assess the degree of bending in each cone at these locations to pinpoint any hot or cold spots within the kiln.
The second application of the cone is for quality assurance in the firing process. Regularly run the three cones at predetermined locations - top, middle, and bottom in the center of the ware.
A periodic check of these cones will confirm consistent heat-work delivery to the ware and serve as an early indicator of any changes in the firing profile. Maintaining a written log or digital photos of cone positions after each firing establishes a reference for future kiln performance, aiding in the prompt identification of changes in the firing profile before they escalate into significant issues.
Pyometric Cones Chart