Oct 9 2014
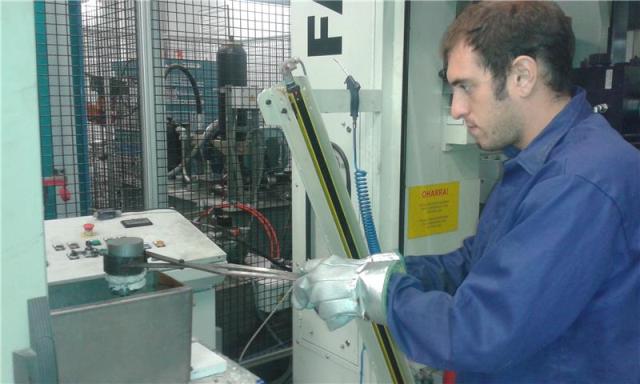
Researchers, as part of the Co-operative Research Centre into High-performance Manufacturing’s (CICmarGUNE) “InProRet” strategic research project, are collaborating to develop more effective joints with a longer life for joining hybrid and composite metals that are required for automotive applications.
This would enable production of components with greater value and also aid Basque companies in competing with others in the industry.
Automotive manufacturers have been trying to reduce the weight of their vehicles due to strict environmental regulations. To address this issue, they combine hybrid or dissimilar materials. However, as present types of joints do not address increasing demands of certain applications, new types of joints have to be developed.
If more light-weight materials are to be used for automotive applications, then more cost-effective joining processes with a longer life need to be developed. Hybrid structures hold great promise and the design and production of these structures bode well for the automotive sector. The automotive industry in Europe has increased its use of composites, magnesium, aluminium and other light materials in the chassis and framework of automotive vehicles to reduce weight.
The automotive industry has widely used aluminium and iron alloys due to their advantageous properties. Hybrid structures developed from this material possess the same wear resistance and toughness as low density aluminium alloy steels. However, intermetallic compounds rich in aluminium are formed in conventional aluminium-steel welds.
These compounds are brittle and may affect the product. Problems such as these occur when dissimilar materials are blended. Furthermore, this type of joining technology also restricts the geometry of the final structure.
Researchers are studying various technologies, such as using adhesives, laser, friction, co-casting, advanced arc welding, and thixoforming. Thixoforming technology holds great promise as it enables production of “near net shape” components in a single step. It is a robust process that is suitable for repetitive manufacturing.
This method allows a certain level of geometrical complexity and helps achieve reduction in weight by 40%. The components produced have good mechanical properties without any defects. Adoption of this technology may help automotive companies in the Basque country improve their competitiveness in the industry.