An increasingly vital component to customer satisfaction in the automobile industry is Squeak and Rattle performance. Usually Squeak and Rattle performance in a new car is tested throughout the validation phase before production begins. A robust design is needed to decrease the amount of Squeak and Rattle issues during validation.
A comprehensive Squeak and Rattle simulation tool was utilized to obtain ‘right the first time’ designs for GM projects and avoid unnecessary development loops. The correct representation of a part’s dynamic behavior must be known before the simulation tool can be effectively employed. So, a 3-D Scanning Vibrometer was utilized to measure the dynamic behavior of each interior car part in order to enhance the modal correlation.
The combination of the simulation tool and 3-D vibrometer data has helped engineers gain a better understanding of how to assemble automotive interior parts correctly to avoid disturbing squeaks and rattles.
Introduction
The production of squeaks and rattles (S&R) in the vehicle is an extremely complicated noise phenomenon. A large scope of factors, including surface finishing, tolerances, road load, material pairs, assembling, manufacturing, and relative displacement between parts, can impact the amount of S&R. Only one of these factors, the relative displacement, can always be connected to S&R issues.
When trying to simulate the S&R phenomenon, it is important to focus on the relative displacement. In a normal vehicle, the instrument panel has the highest complexity of interior assemblies because of the number of different parts and instruments which are mounted together. The relative displacement between all of these parts has to be controlled to circumvent S&R problems.
Parameter Definition
A detailed examination of the instrument panel identifies numerous crucial factors which must be represented in the simulation model in order to measure the relative displacement (Figure 1). These parameters are valid for all interior assemblies regarding the S&R simulation.
The global stiffness has a huge influence on the relative displacement. This impact is strongly related to the position and amount of internal mounting points. The local stiffness together with the clips and snap stiffness is also vital for the relative displacement.
The local geometry in the area where two parts can come in contact has to be considered in the simulation in addition to the stiffness. Furthermore, the applied load has a decisive effect on the S&R performance.
A load level which is too low is not likely to cause any S&R issue, but a load level which is too high will always cause issues. So, it is crucial to define a realistic load. The relative displacement is the output of the simulation, which is processed both in local and global coordinate systems.
.jpg)
Figure 1: Parameter definition for S&R simulation model.
During the development process, different types of analyses are applied. The output of these analyses is adapted to the detail level of the interior assembly:
- The modal analysis starts with a focus on the main structural parts.
- The transient analysis allows the study of relative displacement between the global structural parts due to a pulse load as the structure becomes more detailed.
- Lastly, the Squeak and Rattle simulation is carried out on the finished detailed model, utilizing a frequency response analysis in conjunction with the EdWare software from EDAG. Measured acceleration data is employed as the load and the “SAR line” technique is utilized to account for the local contact geometry when post-processing the relative displacement.
Modal Analysis and Modal Correlation
The Opel Insignia instrument panel is a complex structure which is made up of a lot of plastic parts. Both the material data (e.g. Young’s modulus) and the Finite Element (FE) representation of these plastic parts are not well-defined as compared to a steel body-in-white structure.
The data from the material suppliers cannot be used for the simulation since the foil and foam together with the carrier structure are acting as a composite. So, modal correlation work and direct measurements must be carried out in order to enhance the simulation capability.
Multiple accelerometers were employed to capture the global deformation of the structure. The key result of the correlation was that only the lowest modes were represented correctly while higher modes did not correlate, revealing that the data for the plastic material must be altered considerably.
Modal Correlation with the Aid of a 3-D Scanning Vibrometer
A Polytec 3-D Scanning Vibrometer was utilized for structural measurements to optimize the modal correlation on a local and global level (Figure 2). There are two key benefits to this approach. The first benefit is the elimination of employing relatively heavy accelerometers and the resulting mass loading. Retro-reflection tape can be utilized with the vibrometer, permitting the measurement of lightweight trim parts.
The second benefit concerns the higher amount of points which can be measured compared to measurements employing individual accelerometers where the number of channels is limited. The initial results of this correlation work clearly demonstrated that there is room to improve the linear simulation models on a local level.
The improvement concerns a better understanding of exactly the best way to connect the parts to each other in the simulation model. The model permits the user to carry out side studies at an early stage to give input to the design engineers on how the stiffness can be altered in the most effective way, for example by using different mounting point locations or different materials (e.g. glass fiber reinforced).
The design criteria include the mode shape continuity and the modal frequencies. The locations for additional ribs and reinforcements can be easily identified by examining the mode shapes. There is enough time to implement most of these reinforcements as the modal analysis can begin very early in the design project.
.jpg)
Figure 2: Operational deflection shapes of the instrument panel taken with the 3-D Scanning Vibrometer for modal correlation.
The Vibrometer Uniquely Enables Measurement of Lightweight Parts
The Scanning Vibrometer makes precision vibration measurements on lightweight trim parts possible. Traditional approaches, which utilize contact accelerometers, adulterate the dynamic response with extra stiffness and mass. The simulation model and the test setup for the Insignia’s floor console trim part is shown in Figure 3.
The results from the scanning vibrometer show the first time that a displacement measurement on this part has ever been performed. In order to extract the Eigen modes, the data measured by the 3-D Scanning Vibrometer were exported in the UNV format and then imported into LMS Test. Both measured and calculated modes entered LMS Vlab to carry out a modal correlation analysis.
This relatively simple FE model demonstrated the dynamic behavior of the part with excellent accuracy. Even when taking all measurement points into consideration (see Table and Figure 4), the first 10 Eigen modes had very good MAC values (Modal Assurance Criterion) better than 0.8.
.jpg)
Figure 3: Simulation model and the trim part of the floor console held in a jig for vibrometer testing.
.jpg)
.jpg)
Figure 4: Plot of the MAC values of the modal correlation.
Conclusions
The intention of the S&R simulation is to show the dynamic behavior of the interior structure as accurately as possible to be able to relate the relative displacement to the actual S&R phenomenon. The results of the modal correlation exhibit that the linear simulation model can calculate the lowest global modes accurately utilizing better plastic material data (unsatisfactory correlation for higher order modes persists).
This capability also makes the modal analysis a powerful tool for supporting the interior design process at a preliminary stage. A 3-D Scanning Vibrometer is used for measuring the dynamic behavior of the interior parts in order to optimize the modal correlation on a local level. This correlation results in a better understanding of how to assemble the interior parts to minimize S&R issues.
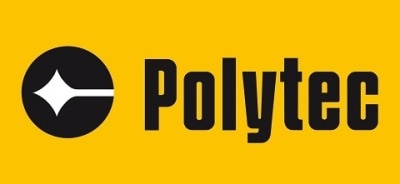
This information has been sourced, reviewed and adapted from materials provided by Polytec.
For more information on this source, please visit Polytec.