Evaluating tribological properties such as friction coefficients, friction forces, and torques for arbitrary material pairs, with high precision is crucial for multiple areas of research and industry. Laboratory experimentation and testing are the only viable methods to generate a quantitative evaluation of tribological properties.
Despite the many available tribotesting options, ranging from commercial tribometers to self-developed systems, acquiring accurate and repeatable tribological property measurements is still a challenge. This is due to the interdependency of the material, surface, environment, and the equipment used to conduct measurements.
Bruker’s UMT TriboLab™ makes use of the most innovative developments in sensor technology with the new 6D Force-Torque Sensor. This state-of-the-art sensor can simultaneously measure up to six tensor components (three forces and three torques in the x, y, and z axes, respectively).
The six-axis load sensor promotes high measurement sensitivity and isotropy, while preserving low interference between measurement axes over an extensive force range (up to 1160 Newtons in a normal direction and a maximum torque of 20 Newton meters).
Synchronous measurements of these extra variables, along with variances in lateral forces, facilitate a greater understanding of the dynamics being assessed. The specific features and measurement advantages of TriboLab’s 6D Force-Torque Sensor are outlined in this article.
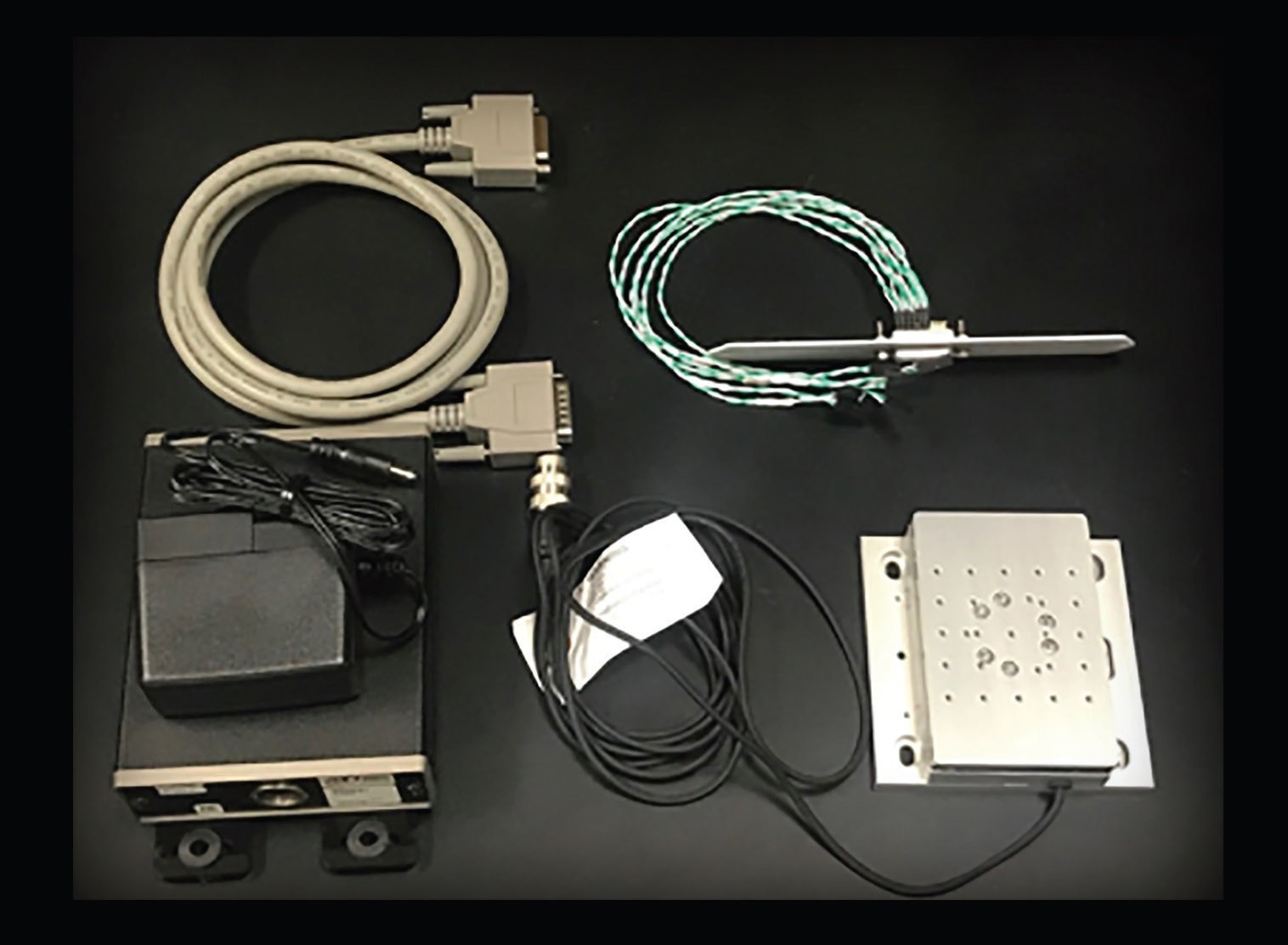
Figure 1. UMT TriboLab 6D Force-Torque Load Cell Kit. Image Credit: Bruker Nano Surfaces
High-Performance Sensor Design
The force-torque sensor’s architecture is founded on the principle of mechanical deformation of the structure using silicon strain gauges. The strain gauges are positioned on a compliant structure that generates six channels of strain gauge voltage output. These devices are digitized and transformed into forces and torques via matrix calculations.
The convenient location of sensing elements on a highly stressed area of the spokes, allows for an almost constant strain distribution on the spoke surface. The constant strain distribution compensates for the negative effects the strain gauge positioning errors cause, thereby improving the sensor's accuracy in evaluating the standard six force and torque components (Fx, Fy, Fz, Tx, Ty, Tz).
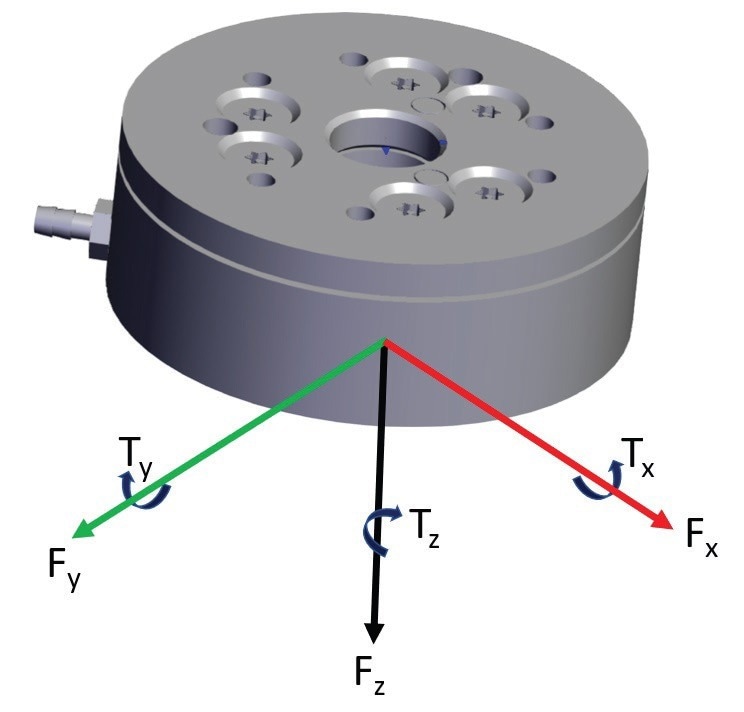
Figure 2. Structure of force-torque sensor and its position indicator. Image Credit: Bruker Nano Surfaces
Widest Range of Measurement Benefits
Integrated Load Sensor for Multiple Measurements
The 6D Force-Torque Sensor’s unique design incorporates the strain gauge transducer to deliver optimal simultaneous force-torque measurement across an extensive range of forces and torques.
The practicality of delivering simultaneous measurements of forces and torques in the x, y and z axes is exceptionally useful for calculating macroscopic friction coefficients to track the distribution of friction forces along an interface. It also helps to assess external torques of the interface that are vital for local stress evaluations.
The 6D Force-Torque Sensor is available in three specifications for different types of applications (see Table 1).
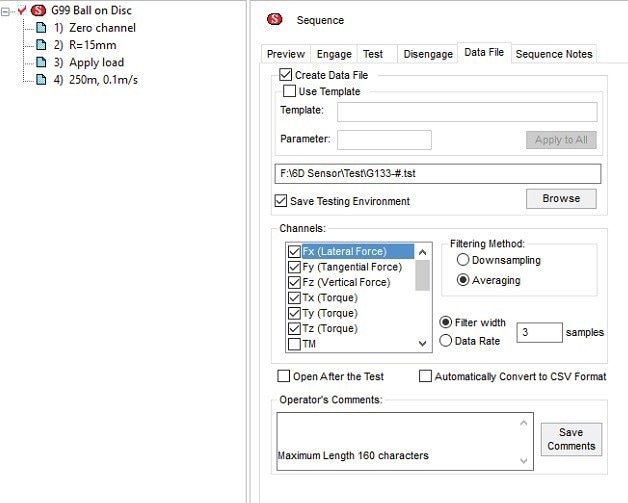
Figure 3. Structure of force-torque sensor and its position indicator. Image Credit: Bruker Nano Surfaces
Table 1. Technical specifications of UMT TriboLab 6D Force-Torque Sensors. Source: Bruker Nano Surfaces
Models/Specs |
6D-Low |
6D-Mid |
6D-High |
Friction/Lateral Force (Fx, Fy) |
Range |
0 – 145 N |
0 – 290 N |
0 – 580 N |
Resolution |
62.5 mN |
125 mN |
0.25 N |
Load (Fz) |
Range |
0 – 290 N |
0 – 580 N |
0 – 1160 N |
Resolution |
62.5 mN |
125 mN |
0.25 N |
Torque (Tx, Ty) |
Range |
5 Nm |
10 Nm |
10 Nm |
Resolution |
1 Nm |
2.6 Nm |
5.3 Nm |
Torque (Tz) |
Range |
5 Nm |
10 Nm |
10 Nm |
Resolution |
0.06 Nm |
1.3 Nm |
2.6 Nm |
Superior Accuracy and Sensitivity
Premium quality of raw output signals is key when trying to reduce any uncertainty of friction and torque coefficient measurements. A recent study reported enhanced measurement accuracy when positioning the force sensors as close as possible to the contact surface.1
The TriboLab and the 6D Force-Torque Sensor configuration synergize the forces generated on the contact surface, limiting the torques experienced by the sensors and significantly reducing measurement uncertainties. Table 2 shows that the average full-scale error was below 2% measured on the 6D Force-Torque Sensors.
Table 2. Precision measurement (95% confidence level, percent of full-scale load) for the 6D-Low, 6D-Medium and 6D-High Force-Torque Load Cells tested at ambient conditions. Source: Bruker Nano Surfaces
Models/Specs |
Fx |
Fy |
Fz |
Tx |
Ty |
Tz |
6D-Low |
1.25% |
1.00% |
0.75% |
1.25% |
1.50% |
1.25% |
6D-Medium |
1.00% |
0.75% |
0.75% |
1.00% |
1.25% |
1.25% |
6D-High |
1.75% |
1.25% |
1.00% |
1.25% |
1.75% |
1.00% |
The measurements shown in Table 2 are indicative of the maximum amount of error defined as a percentage of the full-scale load for each axis. In addition to the negligible precision uncertainty measurement, the 6D Force-Torque Sensor demonstrates excellent stability over prolonged periods of time (see stable vertical load in Figure 4) and during temperature-controlled experiments (see Figure 5). Such qualities are essential to calibrate sensor targeting for accurate tribological data.
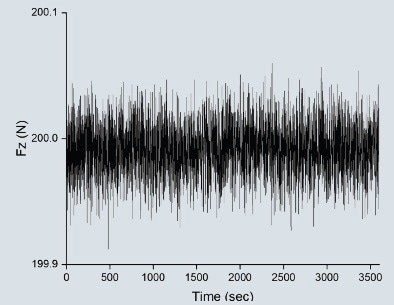
Figure 4. A force of 200 N was applied to a steel specimen for 1 hour. The recorded noise level of the 6D Force-Torque Sensor was less than 0.05% of full-scale values. Image Credit: Bruker Nano Surfaces
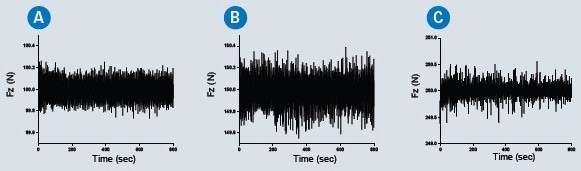
Figure 5. The 6D Force-Torque Sensor experiences minimum thermal drift effect with applied force of (a) 100 N, (b) 150 N, and (c) 250 N, at 200 °C, respectively. Image Credit: Bruker Nano Surfaces
Eliminating Artifacts with High-Precision Measurements
The kinetic friction ratio of the typical (Fz) and tangential (Fx, Fy) forces, as well as its torque (Tx, Ty and Tz) restrictions, are essential to the fundamental investigations in tribology applications.
However, a misalignment issue tends to arise when force and torque sensors are separately assembled to run these measurements, encouraging crosstalk between the various signal channels and infringing on the accuracy of tribological data.
With its single-cell design, Bruker’s 6D Force-Torque Sensor limits crosstalk of less than 1.5%, offering researchers relevant and precise data for each tribology experiment (see Figure 6). Moreover, the UMT software enables users to compensate and counteract noise bias when testing.
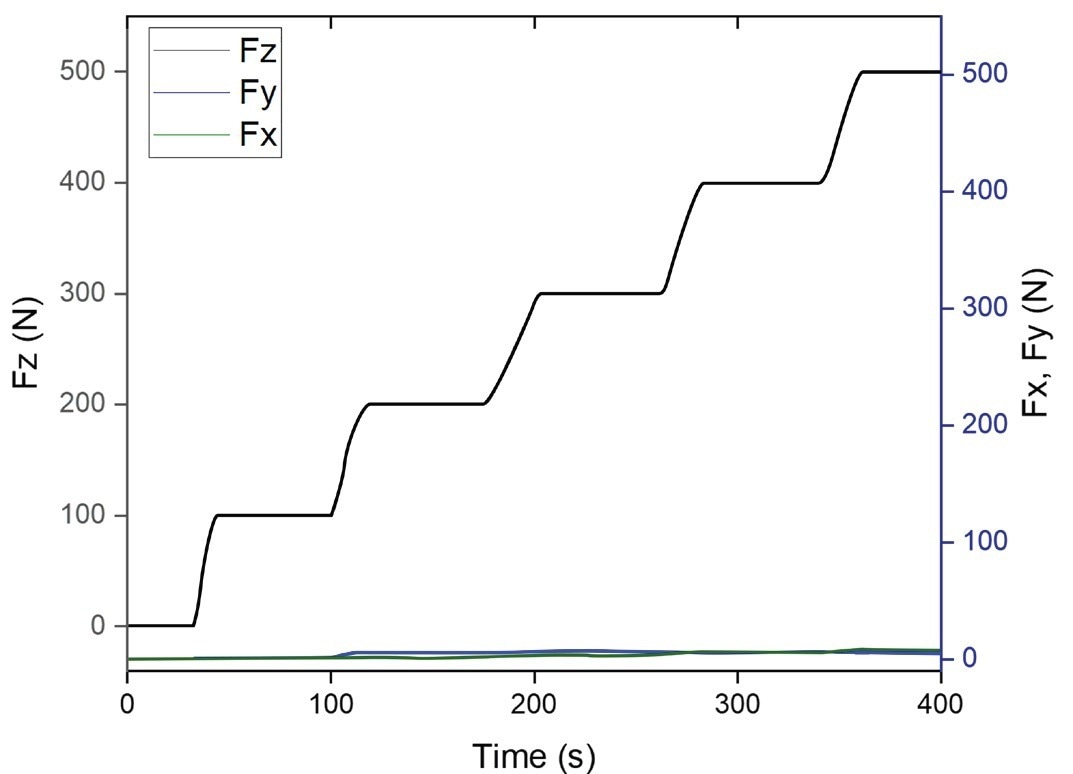
Figure 6. Minimal crosstalk between normal load Fz and lateral force sensing Fx/Fy. Image Credit: Bruker Nano Surfaces
Product Compatibility with Reduced Footprint
The 6D Force-Torque Sensor is fully compatible with the current UMT TriboLab configuration, allowing seamless integration into existing experiences. The sensor is a plug-and-play peripheral that can be used in combination with the fast exchange kit (AM30C413), fast exchange plate (M30C784), and 2-inch or 4-inch extension blocks (M30C366-1, M30C366-2).
Various upper specimens can be used with this configuration to meet an extensive range of test conditions and applications.
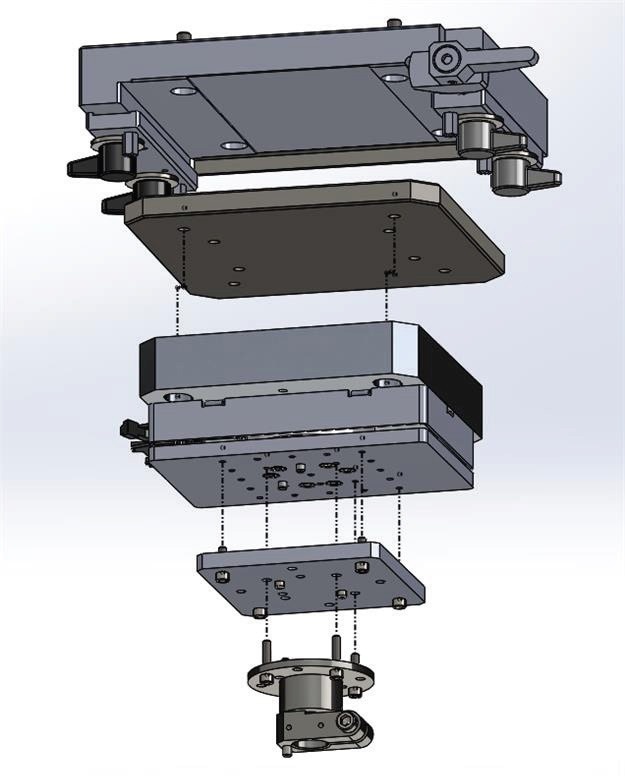
Figure 7. Assembly diagram of the 6D Force-Torque Sensor. Image Credit: Bruker Nano Surfaces
Experimental Applications
Bruker’s UMT TriboLab is an innovative modular platform with a single high-torque motor built into the system’s base to facilitate an extensive range of speed and torque tests.
Combined with the advanced 6D Force-Torque Sensor, TriboLab delivers complex motion and highly precise measurements around multiple axes, a fundamental requirement for tribology research and industrial applications.
Rotary Test
The rotary test is a frequently used friction and wear testing method in the laboratory and across industrial sectors. During this test, a ball or pin is placed under the 6D Force-Torque Sensor, and a standard disk is incorporated as the lower specimen (see Figure 8a/b).
Here, forces and torques across several axes are measured to acquire the friction coefficient and torque coefficient.
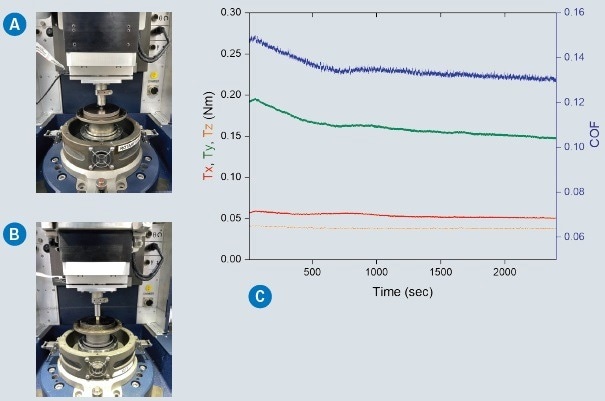
Figure 8. UMT TriboLab rotary test module with 6D Force-Torque Sensor; (a) ball-on-disc, (b) pin-on-disc tests, and (c) plot of dynamic friction coefficient and torques against time. Image Credit: Bruker Nano Surfaces
Measurements across multiple axes are extremely useful to better comprehend the friction and wear behavior of a tribosystem. The in-situ coefficient of the friction measurement considers the contributions of both Fx and Fy, represented by the mathematical equation COF=√(Fx2 + Fy2)/ Fx.
Throughout high-speed rotational tribotests, unwanted movements of the contact partners as a result of loose assembly or a breakage event would have a detrimental impact on the tests. The 6D Force-Torque Sensor allows users to easily identify such issues through real-time monitoring of the torque output along the x and y axes (see Figure 8c) so that any failures can be addressed immediately.
Brake and Clutch Materials Screening
The Brake and Clutch Material Screening Tester for UMT TriboLab has been purposely designed as a cost-effective and rapid way to screen and rank materials before moving on to evaluations at a component level.
Such methods allow the tribological performance of small friction material samples to be characterized precisely and conveniently. This appears while monitoring important parameters, such as friction, sliding speed, temperature, and wear.
The scaled-down method is generally used to replicate vehicle brake systems while consistently matching the critical physical parameters employed by dynamometers for protocols such as SAE J2522.
The 6D Force-Torque Sensor aids the screening testing process by enabling simultaneous multiple axes measurements to better comprehend the dynamic tribosystem’s behavior.
Figure 9a displays a standard setup on the TriboLab for brake material screening with the built-in 6D Force-Torque Sensor. The torque output (Tx, Ty and Tz), shown in Figure 9b, is among the new output features the sensor provides. It enables better evaluation of the mechanism of brake fade from thermal deterioration of the brake lining material.
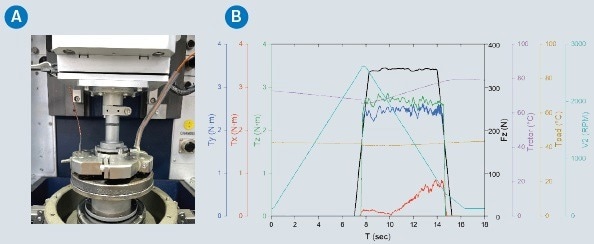
Figure 9. (a) UMT TriboLab Brake Material Screening Tester with 6D Force-Torque Sensor, and (b) simulation of snub performed by varying the speed from 2620 to 131 rpm (100 to 5 km/h vehicle speed) in 8 seconds, and under an applied force of 354 N (2 MPa contact pressure). Image Credit: Bruker Nano Surfaces
In Table 3, additional applications that can gain an advantage from having six components of forces and torques, including the four-ball test, the twist compression test, and the sliding-to-rolling ratio tests, are shown.
Table 3. The advantages of using a 6D Force-Torque Sensor to perform ASTM standard tests. Source: Bruker Nano Surfaces
ASTM# |
Description |
Advantages |
D4172-20 & D2266-01 |
Wear Preventive Characteristics of Lubricating Fluid & Greases (Four-Ball Method) |
Multidirectional torque output signals enable quick identification of balls rolling and slipping in the four-ball cup holder. |
D5183-21 |
Determination of the Coefficient of Friction of Lubricants (Four-Ball Method) |
D2596-20 & D2783-19 |
Measurement of Extreme-Pressure Properties of Lubricating Fluid & Greases (Four-Ball Method) |
G99-17 |
Wear Testing with a Pin-on-Disk Apparatus |
Stability of applied forces with minimum effects of thermal drift is suitable for extended period testing. |
G132-96(2018) |
Pin Abrasion Testing |
D3702-94(2019) |
Wear Rate and Coefficient of Friction of Materials in Self-Lubricated Rubbing Contact Using a Thrust Washer Testing Machine |
Sensitivity of the load sensor improves self-leveling of the upper sample in a thrust washer test. |
D5619-00 & D8288-19 |
Comparing Metal Removal Fluids |
Cross-threading during tapping can be easily identified and prevented. |
Summary
Bruker’s UMT TriboLab is an indispensable tribometer for force-torque measurements across an extensive range of forces and torques in research and industry, including precision for scientific instruments, actuators, automotive, robotics sensors, micro-manipulators, and lubrication applications.
With the latest 6D Force-Torque Sensor, TriboLab offers:
- High-precision measurements that resolve interference between measurement axes in multiple directions.
- Linear responses with a high natural frequency, and overload protection.
- Solutions to independent simultaneous force and torque measurements.
Ultimately, TriboLab is able to run an extensive range of friction, wear and lubrication testing that complies with various internationally recognized standards, such as the ASTM, ISO, DIN, SAE, and others.
References
- Grégoire, C., Laulagnet, B., Perret-Liaudet, J., Durand, T., Collet, M., and Scheibert, J., Design and characterization of an instrumented slider aimed at measuring local microimpact forces between dry rough solids. Sensors and Actuators A: Physical, 317, 112478, (2021).
- Ballo, F., Gobbi, M., Mastinu, G., and Previati, G., Advances in force and moments measurements by an innovative six-axis load cell. Experimental Mechanics, 54(4), 571- 592, (2014).
- Heglund, N.C., A simple design for a force-plate to measure ground reaction forces. J. exp. Biol., 93, (1981).
- SAE J2522, Dynamometer Global Brake Effectiveness, SAE International (2013).
- ASTM G09-05 (Reapproved 2010), Standard Test Method for Wear Testing with a Pin-onDisk Apparatus, ASTM International, West Conshohocken, PA, (2010).