Introduction Since the discovery of detonation synthesis for ultradispersed diamonds in the 1960s, the full potential of nanodiamonds remains to be explored. Detonation synthesis produces nanosized carbon particles with average diameters of ~5 nm, featuring a diamond core covered by graphitic layers and amorphous carbon. The surface of nanodiamond particles is rich in various functional groups and can be further functionalized. The superior properties of the diamond core combined with a large and chemically tunable surface allow them to be used in a wide variety of ways: initial research performed primarily in the former Soviet Union suggests a broad range of industrial applications. Such uses include chemical and electrochemical co-deposition with metals, ultradispersed diamond-polymer composites, polishing, lubrication, and biomedical applications. Commercially, electroplating and lubricant additives currently show the highest potential. Still there is no accepted opinion concerning the mechanism by which coating properties are improved upon the addition of nanodiamond particles to the deposition bath. Two alternatives are currently under consideration. One explains the improvement by inclusion of nanodiamond into the structure of coatings; the other suggests that nanodiamond improves the deposition conditions resulting in decreased columnar structure and porosity of the coating. Addition of nanodiamond to plated coatings is especially important for Ni-based coatings which are expected to replace the Cr-containing coatings currently in use, which require toxic chemicals for their production. Ni-B coatings have been shown to act particularly well. When coated with Ni-B, residual pores in stainless steel or other metals become filled, which results in improved mechanical properties of the interface. The coatings also decrease corrosion and increase wear resistance compared to the steel substrate. However, when compared to the Cr coatings, Ni-B coatings feature lower mechanical properties and wear resistance, both due to their columnar structure. Previous results have shown that nanodiamond additives can increase hardness of Ni-based coatings by a factor of 2-3. Dispersed nanodiamonds added into the deposition bath have been empirically shown to further increase the tribological properties of Ni-B coatings. But still, the role of nanodiamond in the observed phenomena remains unclear. The aim of this study is to investigate the structure and mechanical properties of Ni-B coatings plated with and without nanodiamond additives to the deposition bath to obtain better insight into the role of nanodiamond in the Ni-B deposition process. Experimental Ni-B coatings were deposited on four steel plates via electroless deposition with bath containing diamond nanoparticles supplied by NanoBlox Inc. (USA) and without diamond additives (Table 1). The structure of diamond nanoparticles which form a colloidal solution in the deposition bath, is described elsewhere. For further studies cross-sectional specimen were cut from plates, mounted in thermal-setting plastic and ground using silicon carbide paper and polished using 0.05μm alumina powder dispersed in a polishing cloth. Table 1. A description of the samples used in this study and their mechanical properties determined by nanoindentation. | AP | As-plated without ND** | 120 ± 29* | 7 ± 2 | AP-ND | As-plated with ND | 164 ± 7 | 9 ± 0.5 | HT | Sample AP heat treated at 385°C for 90 min | 133 ± 14 | 11 ± 0.7 | HT-ND | Sample AP-ND heat treated at 385°C for 90 min | 254 ± 6 | 10 ± 1.6 | * - Standard deviation ** - ND stands for nanodiamond Mechanical properties were measured via depth-sensing indentation using a Nano Indenter XP (MTS). All indents were performed using a Berkovich tip to a depth of 2 μm. Hardness and moduli are calculated continuously throughout the loading by using the continuous stiffness measurement (CSM) option for all indents on all four Ni-B samples. Raman spectra were recorded to determine the presence of diamond in the samples. Each sample was studied at multiple points using a Renishaw 1000 Raman Spectrometer with an Ar+ laser with excitation wavelength of 514.5nm. Scanning electron microscopy using an FEI XL30 field emission SEM with an energy-dispersive X-ray spectrometer (EDS) was performed to examine the morphology of the coatings and to view residual indent impressions. A GiegerFlex D/Max-B diffractometer (Rigaku) with CuKα radiation was used to perform XRD studies to determine the phase composition of the samples. Results XRD spectra (Fig. 1) confirmed that as-plated samples AP and AP-ND (ND stands for nanodiamond) are X-ray amorphous. A single broad peak centered close to the position of major diffraction peaks of Ni2B and Ni3B, corresponds to amorphous Ni-B (Fig 1 a,b). XRD also shows that the heat treated samples HT and HT-ND are crystalline demonstrating the narrow peaks of nickel borides (Fig 1 c,d). Furthermore, the XRD patterns suggest that though both samples HT and HT-ND have been crystallized after annealing, HT-ND still contains a significant amount of amorphous material as shown by the halo and much finer grains of nickel borides denoted by broader peaks found in this sample. A higher heat treatment temperature or longer treatment time may be needed to fully crystallize the coatings produced in the presence of nanodiamond. A brief description of composition and FWHM values for the predominant Ni2B peak are summarized in Table 2. While XRD allows us to identify nickel boride phases, it does not provide information on presence of nanodiamond in the samples. An XRD spectrum of the nanodiamond powder shown in Fig. 1 e does not correspond with any of the peaks found in the other samples. This suggests that nanodiamond must be below the XRD detection limit if incorporated. 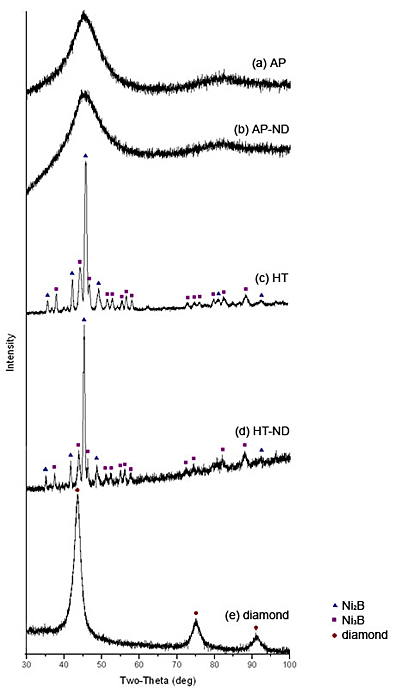 Figure 1. XRD spectra for the samples studied (see Table 1 for description of the samples). Table 2. Composition of the samples as determined by XRD. For the crystalline samples, a calculated FWHM for the (2 1 1) Ni2B peak at 45.9˚ (d = 1.9757 Å) is shown. For the amorphous samples, a calculated FWHM for the amorphous peak is shown. | AP | amorphous Ni-B | 7.5 | HT | crystalline Ni2B, and Ni3B | 0.42 | AP-ND | amorphous Ni-B | 8.4 | HT-ND | crystalline Ni2B, and Ni3B | 1.27 | The morphology and structure of the coatings was studied by SEM. An SEM image of the cross-section of sample AP-ND clearly shows dendrites which reveal the typical columnar growth mechanism of the Ni-B coatings (Fig 2 a). These columns are believed to be amorphous, as suggested by XRD. When comparing the column size of sample AP and sample AP-ND two differences are observed (Fig 2 b,c). The average width of columns is smaller for samples containing nanodiamonds than without. The average width of dendrites was found to be 0.8 ± 0.1 μm and 0.6 ± 0.05 μm for samples AP and AP-ND, respectively. Furthermore, the addition of nanodiamond leads to straighter columns with fewer branches and arms. 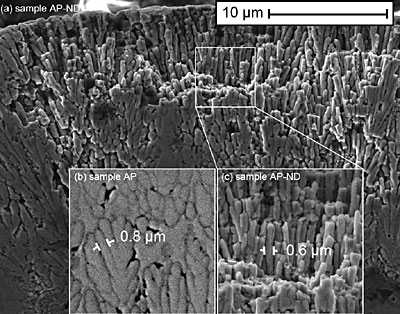 Figure 2. (a) Columnar microstructure of as-plated, AP-ND, sample deposited from the diamond-containing bath. Insets show the microstructure for both samples: (b) the sample deposited without nanodiamond additive, AP, and (c) the sample deposited with nanodiamond, AP-ND. Backscattered SEM images of the samples HT and HT-ND show that the well developed columnar structure significantly decreases as the amorphous material is converted into crystalline grains after heat treatment (Fig. 3). In the case of sample HT, some regions remain columnar or amorphous while other areas, particularly those near the surface transform into crystalline equiaxial grains. This is not the case for sample HT-ND, suggesting that the addition of nanodiamond inhibited grain nucleation and growth. 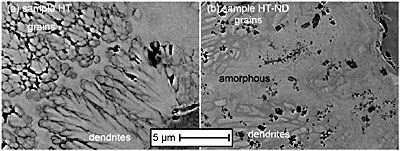 Figure 3. Comparison of the microstructure of the heat treated samples. (a) the sample deposited with no nanodiamond additive, HT, and (b) the sample deposited with nanodiamond, HT-ND. Indentation results for the samples studied are shown in Table 1. Load vs. displacement curves for all samples are shown in Fig. 4. Heat treatment of Ni-B coatings raises hardness. This can be explained by the transformation from the amorphous as-deposited coatings to harder crystalline Ni3B and Ni2B phases as confirmed by XRD (Fig. 1). The addition of nanodiamond also raises hardness by a factor similar to that achieved by annealing and causes a small increase in modulus. Heat treatment of the samples deposited with nanodiamond additives to the bath does not further increase the hardness but does increase the modulus by a factor of two. These measured properties are in agreement with the load vs. displacement curves (Fig. 4) which show an increase in the required load with heat treatment or the addition of nanodiamond. Therefore, such coatings are suitable for raising modulus and hardness or raising hardness without requiring heat treatment. Combination of heat treatment and addition of nanodiamond did not lead to a further increase in hardness as compared to sample HT or sample AP-ND. This can be explained by the fact that the microstructure of sample HT-ND still contained amorphous material (Fig. 1 d). If the sample could be processed in such a way to form small crystalline grains in the presence of nanodiamonds, additional hardening may be achievable. 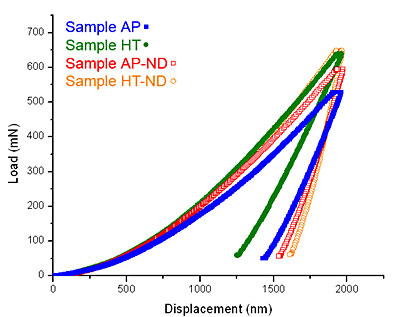 Figure 4. Representative load vs. displacement indentation curves for the tested samples. Close-up images of a typical indent for each sample are shown in Fig. 5. The cracks seen in sample HT were found on many indents in that sample and are indicative of brittle failure. Because no pop-in events can be found in the load vs. displacement curves for this sample, one can presume this small cracking did not interfere with the accuracy of indentation measurements. Though nanoindentation provides no quantitative information about a material’s toughness, this image suggests the sample is likely more brittle, which would imply that the addition of nanodiamond may have also increased the coating’s toughness. This would agree with the Hall-Petch relationship, considering the addition of nanodiamond was shown to decrease the mean dendrite size of sample AP-ND. The shape of the indent in sample AP-ND shows somewhat more elastic recovery compared to sample AP. This elastic recovery is denoted by a more concave residual impression. Compared to sample AP more elastic recovery is also observed in sample HT-ND. This sample shows the highest amount of ductile pile-up suggesting improved ductility of the coating with the addition of nanodiamond to the bath. These findings are in agreement with the data shown in Table 1. Sample HT-ND shows a surprisingly higher modulus compared to all other coatings and it is almost twice the value of sample HT. Combination of high modulus with a high ductility is quite unique and very important for potential applications. 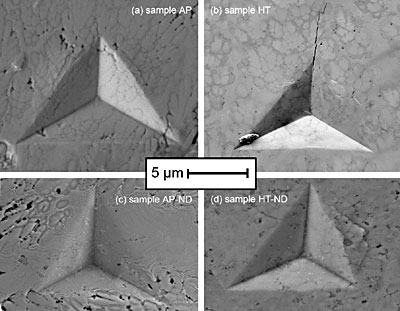 Figure 5. SEM images of indents from the samples. (a) as-plated sample AP, (b) annealed sample HT, (c) as-plated sample AP-ND, and (d) annealed sample HT-ND. EDS mapping was performed to determine if and where the diamond resides in the coating. A summary of these results is shown in Figure 6. Though some carbon was detected, no correlation between the carbon location and microstructure could be seen. Usually, the nanodiamond powders with 5 nm particles form agglomerates from tens to hundreds of nanometers in size in the deposition bath. Thus, if diamond were incorporated into the coating, we would expect to see those agglomerates. Carbon was neither found in the form of large agglomerates, nor did it seem to congregate along grain boundaries. Raman studies of the samples deposited from the bath containing nanodiamond show no nanodiamond features, therefore significant changes in mechanical properties cannot be explained by incorporation of nanodiamond in the structure of coatings. We estimate that since neither Raman spectroscopy, XRD or EDS have shown the presence of diamond, even if present it should be at a concentration less than 1 wt%. and should not significantly affect the mechanical properties. By using the rule of mixtures, we could not explain the observed difference in modulus between samples AP and AP-ND by addition of 1 wt%. or less of diamond. Incorporation in the amount of at least several percent would be required to explain the observed increased hardness and modulus after deposition and this amount of diamond could be easily detected by the techniques used. Thus, the increase in mechanical properties is not a result of composite diamond/metal coating formation. Recent work has shown that nanodiamond accumulates on the surface of the Ni coatings, influencing its growth and structure. We assume a similar behavior in our Ni-B system. This assumption agrees with the latest report where nanodiamond additives did not incorporate into the coating. Diamond also did not react with the metal matrix even when used in carbide forming metals. The fact that after adding nanodiamond the deposition bath could be used for months without replenishing and without a loss in the properties of the coating supports the fact that diamond is very slowly consumed in the deposition process. 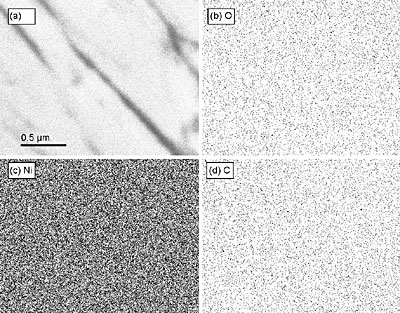 Figure 6. An X-ray map of a region of the as-plated sample, AP-ND, deposited from the diamond containing bath. (a) the original image with scale bar for all images, (b) a map of oxygen, (c) a map of nickel, and (d) a map of carbon are shown. No segregation of oxygen or carbon along grain boundaries can be seen. Conclusions • Nanodiamond additive to the deposition bath has been shown to improve the hardness, modulus, and ductility of electroless deposited Ni-B coatings. The additive has increased the hardness of the coatings, but not as effectively as annealing. • The hardening mechanism appears to be related to refinement of the dendrite size upon the addition of nanodiamond into the bath. • Heat treatment of samples deposited from the diamond-containing deposition bath did not lead to increased hardness beyond that of the heat treated diamond-less sample because the addition of nanodiamond to the bath led to an inhibition of the grain formation, and therefore led to more amorphous material and smaller grains. • Heat treatment of Ni-B coatings deposited from the bath with nanodiamond additives improves the modulus and ductility. This can be explained by the fine-grain structure of the coating produced in the presence of nanodiamond. Acknowledgements Thanks to Dr. G. Yushin, Z. G. Cambaz, P. Rossi, D. Mattia, R. Dash, S. Amini, and Dr. D. Filimonov for experimental assistance and helpful discussions. Samples were provided by NanoBlox, Inc. Research was conduced in the Materials Characterization Facility at the A.J. Drexel Nanotechnology Institute and the Laboratory for Research on the Structure of Matter (LRSM) at the University of Pennsylvania. This work was supported by Nanoblox. A.J. Gurga was supported by NSF IGERT grant DGE-0221664. References 1. Shenderova, O. & McGuire, G., Nanomaterials Handbook (ed. Gogotsi, Y.) (CRC Press, New York, 2006). 2. Yushin, G. N., Osswald, S., Padalko, V. I., Bogatyreva, G. P. & Gogotsi, Y., "Effect of sintering on structure of nanodiamond", Diamond and Related Materials, (14), 1721-1729, 2005. 3. Dolmatov, V., "Detonation Synthesis Ultradispersed Diamonds: Properties and Applications", Russian Chemical Review, (70), 607-626, 2001. 4. Wang, L., Gao, Y., Xue, Q., Liu, H., Xu, T., "Effects of Nano-diamond Particles on the Structure and Tribological Property of Ni-matix Nanocomposite Coatings", Materials Science and Engineering, (309 313-318), 2004. 5. Engel, P., Schwarz, G. & Wolf, G. K., "Characterisation of chromium nitride films prepared by ion-beam-assisted deposition", Surface and Coatings Technology, (112), 286-290, 1999. 6. Krishnaveni, K., Sankara Narayanan, T. S. N. & Seshadri, S. K., "Electrodeposited Ni-B coatings: Formation and evaluation of hardness and wear resistance", Materials Chemistry and Physics, (In Press, Corrected Proof). 7. Ozkan Gulsoy, H., "Influence of nickel boride additions on sintering behaviors of injection moulded 17-4 PH stainless steel powder", Scripta Materialia, (52), 187-192, 2005. 8. Hou, F., Wang, W. & Guo, H., "Effect of the dispersibility of ZrO2 nanoparticles in Ni-ZrO2 electroplated nanocomposite coatings on the mechanical properties of nanocomposite coatings", Applied Surface Science, (252), 3812-3817, 2006. 9. Burkat, G. K., Fujimura, T., Dolmatov, V. Y., Orlova, E. A. & Veretennikova, M. V., "Preparation of composite electrochemical nickel-diamond and iron-diamond coatings in the presence of detonation synthesis nanodiamonds", Diamond and Related Materials, (14), 1761-1764, 2005. 10. Dolmatov, V., Ultradisperse Diamonds of Detonation Synthesis: Production, Properties and Applications (St. Petersburg, State Polytechnical University (in Russian), 2003). 11. Osswald, S., Yushin, G. N., Mochalin, V., Kucheyev, S. & Gogotsi, Y., "Control of sp2/sp3 carbon ratio and surface chemistry of nanodiamond powders by selective oxidation in air", Journal of the American Chemical Society, (In Press, Corrected Proof). 12. Ibanez, A. & Fatas, E., "Mechanical and structural properties of electrodeposited copper and their relation with the electrodeposition parameters", Surface and Coatings Technology, (191), 7-16, 2005. 13. Petrov, I. et al., "Nickel Galvanic Coatings Codeposited with Fractions of Detonation Nanodiamond", Diamond and Related Materials, (In Press, Corrected Proof). 14. Aleksensky, A. E. et al., "Nanodiamonds intercalated with metals: structure and diamond-graphite phase transitions", Diamond and Related Materials, (13), 2076-2080, 2004. 15. Andreyev, M., Anishchik, V., Markova, L. & Kuznetsova, T., "Ion-beam coatings based on Ni and Cr with ultradispersed diamonds--structure and properties", Vacuum, (78), 451-454, 2005. Contact Details |