Virgin pet resin competes directly with recycled PET for many applications. Unfortunately, virgin PET can undercut reclaimed resin in price (under certain circumstances), has higher quality over its recycled counterpart, and is not subject to FDA restrictions on its usage. These disadvantages create quite an uphill battle for recycled PET use. However, many companies have found new ways to let competition further benefit them.
Alternatives for PET Recyclers
Today’s PET recyclers work to add value to their product through vertical integration into fibres, thermoformable sheet, and compounding into alloyed products, fig 1. This not only creates a stronger combined product, but also significantly increases the value of the resin, and avoids direct competition with virgin PET. By integrating the recovery of PET into downstream manufacturing processes, market stability, product quality, and profits have increased greatly. With the addition of these processes to the PET recycling industry, competition with the powerful virgin resin producers will decrease and prosperity in the industry will increase.

|
Figure 1. A prototype fender produced from an alloy of recycled PET and polycarbonate.
|
The Recycled PET Market
In the sports world, competing against those who have better skills than you is said to greatly help your play. As you continue to be knocked around, you gain better skill and knowledge of the game. In the PET recycling industry, however, this competition has not been as beneficial to all the players involved. Because of large oversupply of virgin PET, today's PET recyclers have lost three quarters of their industry and have been forced to limit collection of PET bottles.
Plastic Container Recovery
According to the National Association for Plastic Container Recovery (Charlotte, North Carolina), the US recovered 572 million pounds of PET in 1996. These levels were down by 50 million from 1995 collection totals (figure 2). The PET recycling industry was hit hard in 1996 by an oversupply of PET virgin material that pushed prices for all PET material down, including recycled PET. More than three quarters of the PET recyclers processing in 1995 were forced to shutdown in 1996 because of these difficult market conditions.
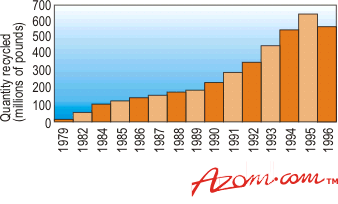
|
Figure 2. PET recycling trends.
|
Price Fluctuations
In 1995, prices for virgin PET hit record highs because of shortages of PET resins. Domestic prices for virgin PET resins increased from US$0.73 per pound at the end of 1994 to more than US$0.85 per pound by mid 1995. This increased prices of recycled PET to new record highs. These strong market conditions encouraged a number of new facilities to open that were capable of producing virgin PET.
At the same time that scrap reclaimers were getting settled into their current situations, prices entered a downslide, falling steadily during the first four months of 1996 before larger drops in April and May. This led to lows in August of US$0.05 per pound for delivered curbside bales and a FOB price of US$0.02-3 per pound. Deposit bottles receive a price premium of an additional US$0.02-3.5 per pound. The main cause of this decline was the increased virgin PET resin supply. North American and worldwide virgin PET production capacity flooded the plastics market in 1996 as new plants came on line and virgin resin in inventory had to be sold at distressed prices. With these low prices, many users of recycled PET switched to wide specification virgin PET, based on the economic advantages.
Effects on Industry
The price drop and the struggle to find markets for the recycled PET have forced many PET recyclers to close. With the excitement felt in the recycled PET industry in 1995, 10 new PET reclaimers burst onto the scene making the industry more than 30 strong. With the downturn in 1996, this was reversed and the industry is left with 8-12 reclaimers processing PET. Of the approximately 25 reclaimers that have left the industry, only 20% were vertically integrated or involved in adding product value through compounding and alloying. The remaining reclaimers now have the ability to process and sell about 600 million pounds of recycled PET.
Vertical Integration
One of the characteristics which many of the remaining successful processors of PET feature is vertical integration into product manufacturing, and the use of compounding to add product value. The two largest PET reclaimers, Image Industries (Summersville, South Carolina) and Wellman Inc (Johnsonville, South Carolina), are both product integrated into the fibre market. In addition, Wellman, and its subsidiaries Day Products and Creative Forming, as well as PETCO Plastics (Montreal, Quebec) are producing PET sheet from their recycled PET. Products from polyester carpet to thermoformed sheet to T-shirts to car parts are all made by companies which manufacture products using the PET they have recovered. Approximately 290 million pounds of the 572 million pounds (51%) of PET recycled in 1996 was used for internal manufacturing of products, fig 3. What all these companies have shown is that integration of some form can increase profits and decrease direct competition with virgin resin producers.
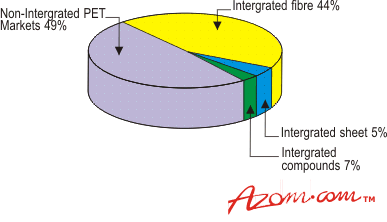
|
Figure 3. Integration of PET recycling.
|
Advantages of Vertical Integration
The main lustre behind vertical integration into product manufacture is the economic advantages it offers. Current sale prices for recovered clear PET flake material are between US$0.31-35 per pound and between US$0.42-46 cents per pound for pelletised PET material. The costs for production of this recycled PET flake or pellets is US$0.7-15 cents less than the selling price, table 1. This represents a saving of between 25‑35% over the purchase of material from another PET reclaimer. A lower raw material price translates to a saving in the price of the production, which, in turn, results in the ability to increase profits or undercut competitors’ prices.
Table 1. PET bottle recycling costs US$ per pound.
|
Raw material
|
2-6
|
Inbound freight
|
0-2
|
Processing Costs
|
13
|
Fixed costs
|
7
|
Total
|
22-28
|
|
Raw material
|
2-6
|
Inbound freight
|
0-2
|
Processing costs
|
23
|
Fixed costs
|
10.5
|
Total
|
35.5-41.5
|
Besides the obvious economic advantages, product integration also allows usage of choice material, assurances of raw materials, and lower transportation costs. In addition, sale of a product removes some of the focus from the recycling operations, allowing survival even during downturns in the economics of PET recycling such as happened in 1996.
Quality Issues
Integration isn’t the sole answer to success in the PET recycling industry. Companies such as Agra Industries (which included sheet production), Goodwill industries (purchased by RockTenn, which is a sheet producer), Plastic Recycling Alliance (sister company of Signode, which is a large PET strapping producer, both owned by ITW), and Nationwide Recyclers (sister company to Constar, which is a large PET bottle producer) were vertically integrated, but suffered problems with quality and production costs. This led each of these companies has since shut down.
Recycled PET Products
Some products that cane be manufactured from recycled PET include:
- Polyester fibre products e.g. carpets, sleeping bags, car boot linings, clothing, fibrefill and other textile applications
- Thermoformed sheet products e.g. laundry scoops, containers for fruit and berries, non-food containers and specialised food packaging
- Other applications e.g. hoses.
PET Alloying
In 1996, 20 million pounds of recycled PET was used in applications in which it was first combined with another resin. This process, known as alloying or compounding, greatly increases the chemical resistance, dimensional stability, and abrasion resistance. PET, both recycled and virgin, cannot easily be injection moulded. PET will randomly crystallise during normal thick wall moulding thus making the moulded part brittle and subject to warp. The process of adding an impact modifier to PET allows it to overcome those problems and allows it to be used in other applications.
Applications for these resins are in the industrial, lawn and garden, sports goods, electrical/electronic, and automotive areas. Product applications include:
- Car bumper bars, other panels and recreational vehicle parts
- Computer keyboards
- Boating equipment
- Protective helmets
- Lawn mower decks
- Tractor grilles
- Meter covers
- Conveyor components
- Consumer sporting goods
- Household appliances
- Telephone housings
- Industrial motor housings
- Pump components
- Lawn/garden machinery
PET/Polycarbonate Alloys
Alloys of PET and polycarbonate are common, using PET contents of 50-80%. Such alloys can be up to 25-30% less expensive than those produced using virgin material, typically acrylonitrile-butadiene-styrene (ABS). They can be produced in different colours and with or without flame retardants using processing techniques such as injection moulding, blow moulding, and sheet extrusion. PET/PC alloys are used for:
- Automotive Applications - automobile bumpers, grilles, wheel covers, and body panels, electrical and electronic components
- Power tools, and other appliances
- Consumer items - office machines and cartridges for copying machines.
Glass-Filled Compounds
Compounds have proven to be another growing market such as glass-filled compounds containing 35% glass fibre and minerals. This material is used in the automotive industry. For example, Ford uses it for grille opening reinforcing panels on its cars and trucks. Applications include:
- Headlamp brackets
- Exterior car door escutcheons
- Automotive window hardware
- Roof racks
- Pot handles
- Arms for chairs
All of these products require good dimensional stability, strength, stiffness, and paintability.
Summary
Direct competition with virgin resin has been harmful to the PET recycling industry. With the increasing use of vertical integration into product manufacturing, however, companies have been able to use their recycled PET to produce quality products. The growing use of compounding will continue to add value to the recovered PET and will open new doors for its usage in products. Competition may make one stronger, but sometimes the wiser fighter will pick a different opponent.
|