Extensive testing of products before distribution is a primary task of pharmaceutical companies. Raw materials, excipients, and final products are tested as part of the process. Conventional methods need a large of operator interference and therefore erroneous. The Phoenix™ Microwave Ashing System is a reliable and safe solution, satisfying all muffle furnace specifications for Europe, Japan, British, the United States, and other Pharmacopeias.
.jpg)
Figure 1. The Phoenix™ Microwave Ashing System
Conventional Methods
In conventional methods, hot plates, heat lamps, and Bunsen burners are used, and muffle furnaces are constantly maintained at elevated temperatures. As a result, they are vulnerable to safety risks, exposing operators to open flames and hot surfaces. In addition, they are more susceptible to error due to the manual interference in the measurement, handling, and calculation of weights. Although other furnace systems are available, they also have problems in temperature measurement and temperature uniformity in addition to safety risks.
Microwave Ashing
The Phoenix™ Microwave Ashing System (Figure 1) satisfies all standard and microwave muffle furnace specifications outlined in ASTM, DIN, ISO, FDA, AOAC, USP (<281 > ROI & <733> LOI), ASTM D1506-94b, and ASTM D5630-94. The microwave furnace can be programmed with up to 20 techniques and is capable of ashing up to 15 samples simultaneously.
The furnace is rapidly heated with microwave energy and temperature uniformity is maintained throughout the cavity owing to the design of the continuous silicon carbide heating element. The presence of the element within the furnace wells will not cause damage to metallic crucibles, allowing their usage in the Phoenix™ Microwave Ashing System.
NIST-traceable thermocouples are used to perform all temperature measurements. The air temperature measurement in the middle of the furnace ensures accurate measurement. The temperature of the furnace exterior is nearly at hand-touchable temperature even though the interior is at a high temperature. The operator is prevented from being exposed to hot surfaces of the system while accessing the furnace interior since the furnace door is placed in a holder. Cool-down is quick upon completion of the method.
It is possible to perform all sulfated ashing steps in the Phoenix™ using the Sulfated Ashing Option (SAO), thus avoiding the requirement for additional equipment. Adding acid to the sample in the crucible is also possible. The sample then can be fed directly into the Phoenix. This is followed by a lower temperature sulfating/ashing step, and the resulting organic sample is then subjected to the high-temperature dry ashing.
A pause step can be used to program the system to remove and weigh the sulfated crucible before the dry ashing step. Evacuation and neutralization of the toxic acid vapor is possible, thanks to the Phoenix™ SAO. This allows a laboratory to meet the ISO 14000 Environmental Management requirements pertaining to the elimination of greenhouse gases. The optional workstation facilitates measurement for document control and identifies %LOI, %ROI, or %Ash automatically.
After generation, it is not possible to modify sample information, helping to meet 21 CFR Part 11 requirements. The data file can include all weighing and method data, as well as the user-entered sample ID, final result, and a date/time stamp showing when the sample ashing was carried out. All methods are saved automatically and the system reduces the chance of erroneous method modification by providing the security of a password lock.
Experimental Results
The Phoenix™ meets all the prerequisites of both USP <733> and <281>. It can identify the LOI for any type of powder and is capable of ashing samples rapidly to identify the ROI for trace metal or other analyses. The accuracy and repeatability of the Phoenix™ have been demonstrated by testing a number of pharmaceutical compounds. The corresponding results are summarized in Table 1.
Table 1. Trace metal analysis using Phoenix with Sulfated Ashing Option
|
Conventional Muffle Furnace |
Microwave Muffle Furnace |
Temperature (°C) |
Time (min) |
ROI (%) |
Temperature (°C) |
Time (min) |
ROI (%) |
Mycostatin |
800 |
60 |
3.5 |
800 |
40 |
3.09 |
Amoxicillin Trihydrate (antibacterial) |
800 |
540 |
0.1-0.2 |
800 |
30 |
0.12 |
Nicotinamide (feed grade) |
800 |
60 |
1.10 |
800 |
10 |
1.08 |
Dextromethorphan |
800 |
60 |
<0.1 |
800 |
30 |
0.04 |
The results obtained from the Phoenix™ are in good agreement with the expected results for the individual compounds and took half the time required for a conventional muffle furnace. Time taken for additional operator actions, such as the application of a hot plate or Bunsen burner, is not included in the time for the traditional muffle furnace.
Since leaving an open flame as such is not possible, constant operator attention is required for this step. Conversely, it is possible to perform the sulfating/ashing step using sulfuric acid with the help of the Phoenix™ SAO, thus minimizing the amount of operator attention as well as providing a safer lab environment.
Conclusions
The Phoenix™ complies with the prerequisites of USP <281> and <733>. In addition, it provides a convenient analysis approach with a high level of accuracy. Furthermore, the system is operator-friendly, thanks to its safety and automated nature.
About CEM Corporation
CEM is a company based on innovation that touches many different industries and scientific disciplines. It helped pioneer the field of microwave chemistry and has long been recognized for its expertise on the subject through publications and awards.
For more than 35 years, CEM has been designing and developing laboratory instruments and scientific methods (both microwave-based and non- microwave technologies) that are used by major companies, prestigious research institutes, and universities around the world.
CEM is the largest provider of microwave laboratory systems worldwide and has sold over 35,000 systems. The company also has the largest portfolio of microwave technology patents worldwide with over 300 patents. It has subsidiaries in the UK, France, Germany, Italy, and Japan and distributors in over 50 countries.
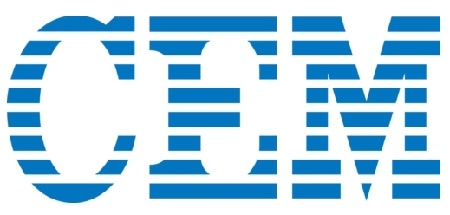
This information has been sourced, reviewed and adapted from materials provided by CEM Corporation.
For more information on this source, please visit CEM Corporation.