The LT-451 Dielectric Cure Monitor1 from Lambient Technologies was used to observe the curing behavior of sheet molding compound (SMC). In general, bulk molding compound (BMC) is the same type of material as SMC but has a bulk form; therefore, the overall behavior also applies to BMC.
The data obtained from dielectric cure monitoring evidently shows that:
- Cure time decreases with increasing temperature, as predicted for a thermally induced reaction.
- Critical Points detect typical features of the cure like the maximum slope of log(ion viscosity), minimum ion viscosity, and the time taken for a selected end of cure.
Definitions
This article shows and discusses the data for log(ion viscosity) as well as the slope of log(ion viscosity), indicating the cure state. The plots demonstrate typical traits like the maximum slope of log(ion viscosity), minimum ion viscosity, and the time taken for a selected end of cure.
For brevity purposes, log(ion viscosity) will be referred to as log(IV), while the slope of log(ion viscosity) will simply be known as a slope. Electrical conductivity (σ) has both frequency-dependent (σAC) and frequency-independent (σDC) components.
While σDC emerges from the flow of mobile ions in an oscillating electric field, σAC emerges from the rotation of stationary dipoles. Both these responses behave just like electrical elements in parallel and are combined together as shown below:
σ = σDC + σAC |
(ohm−1–cm−1) |
(eq. 1) |
Resistivity (ρ), which is the inverse of conductivity, can be defined as:
Based on its relationship with conductivity, resistivity also has frequency-dependent (ρAC) as well as frequency-independent (ρDC) components. The amount of crosslink density or polymerization is a measure of the state of cure. It has an impact on mechanical viscosity as well as the ion movement, and this influences ρDC. Consequently, the name Ion Viscosity was coined to highlight the correlation between ρDC and mechanical viscosity. Ion viscosity (IV) can be defined as:
IV = ρDC |
(ohm-cm) |
(eq. 3) |
Frequency-independent resistivity (ρDC) is the exact definition of ion viscosity. But for convenience purposes, ion viscosity can also be utilized to represent resistivity in general, which not only has a frequency-independent (ρDC) component but also has a frequency-dependent (ρAC) component. But it must be noted that mechanical viscosity and cure state relate best to frequency-independent resistivity, ρDC, which happens to be the true ion viscosity.
Procedure
SMC samples were placed on Mini-Varicon2 sensors, as illustrated in Figure 1, with the lay-up of Figure 2.
.jpg)
Figure 1. Mini-Varicon disposable sensor. Image Credit: Lambient Technologies.
.jpg)
Figure 2. Lay-up of SMC for cure monitoring. Image Credit: Lambient Technologies.
Sample curing was done in a laboratory press at 135 °C, 145 °C and 155 °C. Prior tests had identified that 10 Hz is an optimum excitation frequency for cure monitoring.
The dielectric properties of each sample were measured by an LT-451 Dielectric Cure Monitor at 10 Hz. The monitor was activated to begin data acquisition as soon as the press was closed. The data was acquired and stored by the CureView3 software, which also carried out presentation and post-analysis of the results.
Results
Figures 3, 4, and 5 respectively illustrate the data obtained from the SMC tests at 135 °C, 145 °C, and 155 °C, indicating how SMC cures more rapidly at more elevated process temperatures. The time of minimum ion viscosity denotes the initiation of the accelerating cure, and it takes place sooner at higher temperatures. Moreover, when cure dominates, ion viscosity increases more sharply at higher temperatures until the curve flattens as it reaches the end of cure.
.jpg)
Figure 3. 135 °C SMC cure data at 10 Hz. Image Credit: Lambient Technologies.
.jpg)
Figure 4. 145 °C SMC cure data at 10 Hz. Image Credit: Lambient Technologies.
.jpg)
Figure 5. 155 °C SMC cure data at 10 Hz. Image Credit: Lambient Technologies.
Table 1 shows the Critical Points characterizing each cure. It must be noted that the slope of 0.25 to define CP(4) — that is, the end of cure — was randomly selected. In reality, users should find out the slope to denote the end of cure based on the application requirements.
Table 1. Critical Points from SMC cure monitoring. Source: Lambient Technologies.
Cure Temp. (°C) |
pr(1) Crit. Visc. |
CP(2) Min. Visc. |
CP(3) Max Slope |
CP(4) Crit. Slope |
Value |
Time |
Value |
Time |
Value |
Time |
Value |
Time |
135 |
8 0 |
0.65 min
(39 s) |
7 38 |
4.17 min
(250 s) |
1.86 |
6.23 min
(374 s) |
0 25 |
7.21 min
(433 s) |
145 |
8.0 |
0.60 min
(36 s) |
7.39 |
3.42 min
(205 s) |
3.65 |
5.01 min
(301 s) |
0.25 |
6.13 min
(368 s) |
155 |
8.0 |
0.65 min
(39 s) |
7.60 |
2.48 min
(149 s) |
3.67 |
4.03 min
(242 s) |
0.25 |
5.14 min
(308 s) |
As shown in Figure 6, the time taken to reach every Critical Point is shorter for cures at elevated temperatures, which is anticipated for reactions that are thermally induced.
.jpg)
Figure 6. Critical Point time versus cure temperature for SMC. Image Credit: Lambient Technologies.
However, the time to Critical Point 1, or CP(1), is not plotted in Figure 5. It is the CP(1) that determines when the SMC’s ion viscosity has decreased to the user-defined value of 8.0. The value was selected to demote the onset of flow. The time to flow is not a measure of curing but a measure of heating time; hence, for clarity, CP(1) has not been considered.
Within the 20 °C range of the plot shown in Figure 6, the time taken to reach the ion viscosity minimum — that is, CP(2) — decreases by about 50 seconds for every 10 °C increase in processing temperature. The times to reach both CP(3) and CP(4) differ by an analogous amount with temperature.
Critical Points During Thermoset Cure
Thermoset curing occurs when monomers react to form polymer chains and subsequently a network. Most often, the reaction is exothermic — producing heat — and may further be driven by an oven or press heat. A plot of log(ion viscosity) is a simple method to define the progress of cure. Figure 7 illustrates a standard thermoset’s behavior with a single ramp and hold step in temperature.
Initially, with increasing temperature, the material melts or softens, which leads to decreased mechanical viscosity. Moreover, mobile ions experience less resistance to movement and, as a result, ion viscosity decreases. The reaction is still slow at this point.
.jpg)
Figure 7. Typical ion viscosity behavior of thermoset cure during thermal ramp and hold. Image Credit: Lambient Technologies.
As the material turns hotter, the cure rate also increases. At times, the accelerating reaction starts to take control; mechanical viscosity reaches a minimum value and the material subsequently becomes more viscous.
Electrically, the increased ion viscosity caused by polymerization overcomes the decreased ion viscosity caused by higher temperatures. Moreover, ion viscosity reaches a minimum value and subsequently increases because of the chain extension. This chain extension acts as a major barrier to the flow of ions.
Following the minimum point, a continuous increase in ion viscosity is observed until the unreacted monomer concentration reduces and the rate of reaction decreases. Accordingly, the ion viscosity slope also reduces and ultimately reaches a zero value when the cure ceases completely.
.jpg)
Figure 8. Ion viscosity curve and slope of ion viscosity of thermoset cure during thermal ramp and hold. Image Credit: Lambient Technologies.
Four Critical Points, illustrated in Figure 8, define the dielectric cure curve:
- CP(1) — A user-defined log(IV) level to detect the onset of material flow.
- CP(2) — Minimum ion viscosity closely correlates with minimum mechanical viscosity, denoting when increasing viscosity and polymerization start to govern the behavior of the material.
- CP(3) — The maximum slope detects the time of the maximum reaction rate. The CP(3) height is a relative measure of the reaction rate, and CP(3) is typically utilized as a signpost related to gelation.
- CP(4) — A user-defined slope that defines the end of cure. The decreasing slope matches the decreasing rate of reaction.
The characteristic behavior of curing thermosets, when temperature slowly increases to a hold value, is shown in Figures 7 and 8. Also, the response is somewhat different when the material under test is typically isothermal, as depicted in Figure 9.
.jpg)
Figure 9. Ion viscosity curve and slope of ion viscosity of thermoset cure during isothermal processing. Image Credit: Lambient Technologies.
In this example, CP(1) is either pointless or arises instantly when heat is applied and when the material flows and makes contact with the sensor. Minimum ion viscosity also occurs at t = 0 or soon afterwards because the cure starts instantly. For isothermal cures, both CP(3) and CP(4) are theoretically the same as for ramp and hold conditions.
References
- LT-451 Dielectric Cure Monitor, manufactured by Lambient Technologies, Cambridge, MA, USA. https://lambient.com
- Mini-Varicon sensor, manufactured by Lambient Technologies, Cambridge, MA, USA
- CureView software, manufactured by Lambient Technologies, Cambridge, MA, USA
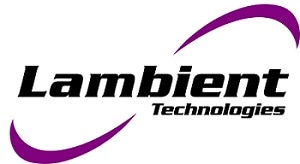
This information has been sourced, reviewed and adapted from materials provided by Lambient Technologies.
For more information on this source, please visit Lambient Technologies.