Over the last five decades, X-ray fluorescence spectrometry has been used in the cement industry to determine the elemental composition of materials of interest in the cement industry. During the first decades, sample preparation by pressed powders was generally utilized, but over the last two decades borate fusion became more popular.
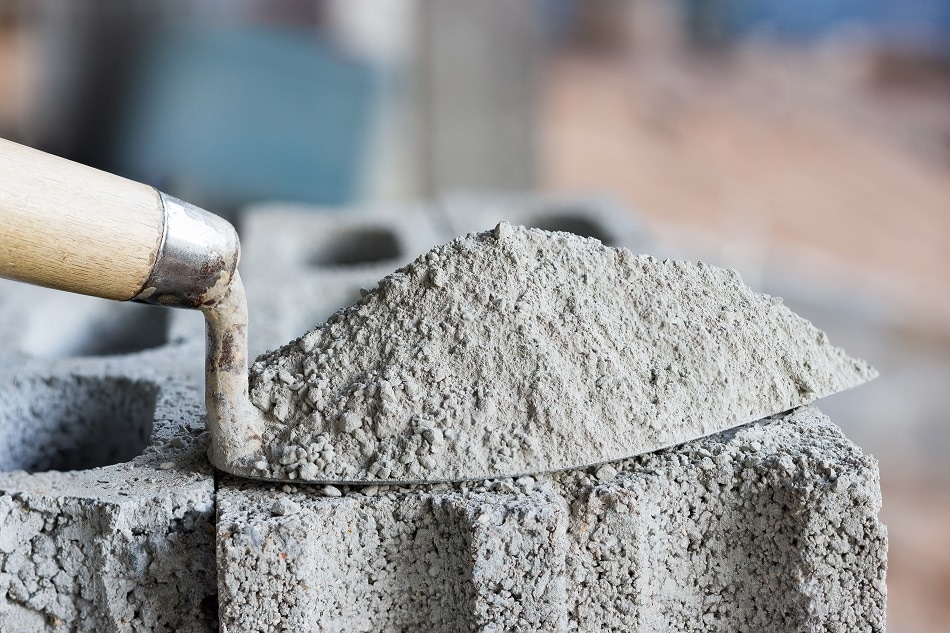
Image Credits: shutterstock.com/okcm
However, changes in the management of cement production processes such as production of cements using additives and alternative raw materials, and the use of spectrometer calibration reference materials from different sources of the world make it difficult to use the pressed powder as it is not easy to matrix match the calibration standards and the manufacturing samples from the plant.
In view of this scenario, the borate fusion preparation provides a suitable solution as it enables a more precise analysis and needs less calibration curves because this method removes mineralogy and particle size effects.
The use of a single fusion approach coupled with a wavelength-dispersive X-ray fluorescence (WDXRF) for preparation of raw materials, cements, and process materials is highly preferred. This would also ensure compliance with the ASTM-C 114 and ISO/DIS 29581-2 specifications of accuracy and precision.
To that end, a powerful analytical method using a WDXRF spectrometer as well as an automated fusion machine for sample preparation tool has been designed to measure all cement industry related elements.
Two individual sets of certified reference materials (CRMs), one from the the Japan Cement Association (JCA) and the other from the National Institute of Standards and Technology (NIST) were utilized to validate that this fusion technique enables a matrix match for cement obtained from different origins.
The assessment of accuracy and precision was carried out as per the instructions given by two international reference organizations: the International Organization for Standardization (ISO), and the American Society for Testing and Materials International (ASTM) through their respective standard methods for cement analysis by X-ray fluorescence: ISO/DIS29581-2 and ASTM-C114.
Experimental Framework
Apparatus and Instrumental Conditions
All fusion disks were produced using the Claisse®M4TM propane fired automatic fluxer (Figure 1). The fluxer comes with pre-set fusion programs and an auto-regulating gas system to enable reproducible and repeatable fusion conditions, whilst its oxidizing flames enable perfect retention of the volatile elements.
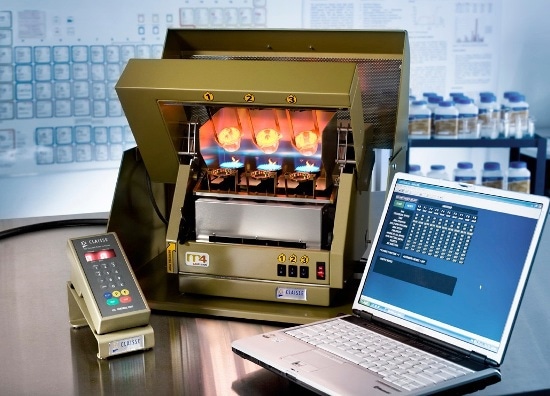
Figure 1. Claisse® M4™ Fluxer
A Fisher Scientific Isotemp® programmable muffle furnace was utilized for the preparation of ignited samples and LOI determinations. The LOI technique, which was utilized for all cement clinkers, included ignition at 950°C temperature in a platinum crucible for 1 hour.
For data generation, a Bruker-AXS S4 Explorer sequential WDXRF spectrometer with a rhodium end-window X-ray tube was utilized. All measurements were performed using a 28mm collimator mask and vacuum.
Parameters such as spectrometer analytical conditions, background position, background measurements, peak-line, counting time, pulse-height, etc. were optimized by wavelength step-scanning of selected standard disks. In order to ensure proper operation of the spectrometer and to improve the counting time for the peaks, the ISO validation test for repeatability of the spectrometer was utilized.
Global Sample Preparation Method
For the study, 0.6000g of ignited sample was weighed with ± 0.0001g tolerance in a Claisse® Optimix™ Pt/Au crucible, and 6.0000g of Claisse® LiT/LiM/LiBr: 49.75/49.75/0.50, Pure Grade Flux was weighed with ± 0.0003g tolerance on top of the sample.
Next, a mini-vortex mixer was employed to combine the sample with the flux but care must be taken to control the speed of the mini-vortex mixer so that material is not lost as this may ultimately lead to erroneous results. Fusion temperature was maintained at 1025°C, and molten flux was poured in a Pt/Au mold.
Preparation for Calibration, Selection of Control Samples and Preparation for Validation
The aim of this study was to calibrate the WDXRF with two individual sets of CRMs from different origins and also to conform to the requirements of ISO and ASTM international standard methods for cement analysis. ASTM utilizes CRMs to validate accuracy and precision on two different days, while ISO verifies method’s repeatability by utilizing one or more CRMs as control samples.
For validation of ASTM requirements, results should comprise LOI, and for validation of ISO requirements LOI-free results are required. Table 1 displays the CRMs element concentration as oxide equivalent and control samples. Given that two CRMs were utilized for the ISO validation, the samples thus selected must cover the low and high element concentration range as specified in the standard method.
Table 1. CRMs element concentration as oxide equivalent and control samples
Compound |
Concentration Range NIST & JCA (LOI Free Base) (%) |
ISO Control Samples (LOI Free Base)(%) |
JCA XRF-03 |
JCA XRF-14 |
SiO2 |
18,907 - 29,29 |
20,67 |
25,74 |
Al2O3 |
3,40 -10,70 |
4,57 |
8,70 |
Fe2O3 |
0,154 - 4,18 |
2,43 |
2,03 |
CaO |
49,28 - 68,94 |
66,32 |
55,15 |
MgO |
0,78 - 5,12 |
1,53 |
3,98 |
SO3 |
1,91 - 4,689 |
3,18 |
N/A |
Na2O |
0,021 -1,086 |
0,30 |
0,26 |
K2O |
0,094 -1,248 |
0,45 |
0,31 |
For qualification of the Global Fusion/XRF method with ASTM Standard Test Method C-114 and for the calibration of the WDXRF instrument, two individual sets of glass disks were prepared for each CRM, one on the first day and the other on the next. For verification of the analytical method with ISO, 10 glass disks of each control samples were prepared over a course of 15 days. The glass disks with control samples were examined on the same day they were prepared.
Results and Discussion
Robustness of the Fusion Methodology
Sample ignition is an important step in the analytical process for a global fusion methodology. To demonstrate the robustness of this fusion method, over 200 different samples from 20 different types of materials were combined with the global fusion methodology. Table 2 shows the list of materials. The global fusion method was effective for preparing stable and uniform lithium borate glass disks with all of the materials, except copper slags, copper-rich iron ores, and iron ores with high magnetite content.
Table 2. List of materials used in this experiment
t# |
Material Type |
Tried |
Success |
# |
Material Type |
Tried |
Success |
1) |
Cement |
118 |
118 |
9) |
Bauxite |
4 |
4 |
2) |
Cement with AdditionsA |
15 |
15 |
10) |
Sand |
7 |
7 |
3) |
Aluminate Cement |
7 |
7 |
11) |
Silica Fume |
3 |
3 |
4) |
Clinker |
13 |
13 |
12) |
Fly Ash |
9 |
9 |
5) |
Kiln Feed/Raw Mix |
11 |
11 |
13) |
SlagB |
8 |
6 |
6) |
Limestones |
9 |
9 |
14) |
Iron OreC |
19 |
12 |
7) |
Gypsum |
7 |
7 |
15) |
Other |
5 |
5 |
8) |
Clay |
7 |
7 |
|
Overall |
242 |
233 |
A. Only the cements with known additions are listed here; the cement category probably included some cements with additions
B. The two slag samples that failed contained a higher level of copper
C. The iron ore samples that failed contained a higher level of copper
ASTM Precision and Accuracy
The ASTM precision test was used as specified in the method. The duplicates are the two glass disks prepared on two different days for each CRM. Table 3 shows results, which are the maximum absolute difference of the results of duplicate for all inspected elements. The maximum values achieved for all analysed elements fulfill the specifications and are well within the limits.
Table 3. ASTM C-114: precision test results
Compound |
Maximum ValueA (%) |
ASTM Limit (%) |
SiO2 |
0,085 |
0,16 |
Al2O3 |
0,036 |
0,20 |
Fe2O3 |
0,013 |
0,10 |
CaO |
0,131 |
0,20 |
MgO |
0,032 |
0,16 |
SO3 |
0,048 |
0,10 |
Na2O |
0,011 |
0,03 |
K2O |
0,012 |
0,03 |
A. Results of control samples are include in the calculation for Maximum Value
The ASTM accuracy test was used as specified in the method. Table 4 shows the results, which are the largest absolute difference of the average of duplicates from the CRM certified values for all inspected elements. The maximum values achieved for all analyzed elements fulfill the specifications and are well within the limits.
Table 4. ASTM C-114: accuracy test results
Compound |
Abs. Max. ErrorA,B (%) |
ASTM Limit (%) |
SiO2 |
0,096 |
0,2 |
Al2O3 |
0,060 |
0,2 |
Fe2O3 |
0,050 |
0,10 |
CaO |
0,124 |
0,3 |
MgO |
0,050 |
0,2 |
SO3 |
0,057 |
0,1 |
Na2O |
0,029 |
0,05 |
K2O |
0,005 |
0,05 |
A. Abs. Max. Error = Absolute Maximum Error
B. Results of control samples are include in the calculation for Abs. Max. Error
ISO Precision and Accuracy
The ISO limits for accuracy and precision are not a fixed limit as in ASTM C-114. The ISO precision test was used as specified in the method. Table 5 shows the maximum absolute difference for all analyzed elements and this was compared to the ISO expert precision limit. The maximum values achieved for all analyzed elements fulfill the given limits for both control samples.
Table 5. ISO: precision test results of control sample JCA XRF-03 and XRF-14
Compound |
XRF-03 (Control Sample 1) |
XRF-14 (Control Sample 2) |
Maximum Value (%) |
ISO Expert Limit (%) |
Maximum Value (%) |
ISO Expert Limit (%) |
SiO2 |
0,030 |
0,134 |
0,052 |
0,149 |
Al2O3 |
0,030 |
0,062 |
0,020 |
0,081 |
Fe2O3 |
0,017 |
0,054 |
0,011 |
0,054 |
CaO |
0,114 |
0,235 |
0,093 |
0,217 |
MgO |
0,023 |
0,044 |
0,018 |
0,054 |
SO3 |
0,020 |
0,054 |
N/A |
N/A |
Na2O |
0,006 |
0,023 |
0,011 |
0,023 |
K2O |
0,006 |
0,023 |
0,003 |
0,023 |
The ISO accuracy test was used as specified in the method, but without averaging the results of the different preparations. The accuracy values were measured as difference of the results from the 10 preparations over a 15-day period against the certified values. Table 6 shows the absolute maximum error for all analyzed elements and this was compared to the ISO expert accuracy limit. The maximum values achieved for all analyzed elements are within the specified limits for both control samples.
Table 6. ISO: accuracy test results of control sample JCA XRF-03 and XRF-14
Compound |
XRF-03 (Control Sample 1) |
XRF-14 (Control Sample 2) |
Abs. Max. Error (%) |
ISO Expert Limit (%) |
Abs. Max. Error (%) |
ISO Expert Limit (%) |
XRF-03 (Control Sample 1) |
XRF-14 (Control Sample 2) |
Compound |
Abs. Max. Error (%) |
ISO Expert Limit (%) |
Abs. Max. Error (%) |
ISO Expert Limit(%) |
SiO2 |
0,087 |
0,15 |
0,058 |
0,15 |
Al2O3 |
0,024 |
0,08 |
0,066 |
0,12 |
Fe2O3 |
0,022 |
0,08 |
0,031 |
0,08 |
CaO |
0,089 |
0,25 |
0,096 |
0,25 |
MgO |
0,019 |
0,08 |
0,027 |
0,08 |
SO3 |
0,052 |
0,08 |
N/A |
N/A |
Na2O |
0,017 |
0,02 |
0,011 |
0,02 |
K2O |
0,007 |
0,02 |
0,005 |
0,02 |
Qualification of Reference Material not included in Calibration
The final step of the study was to utilize a single set of CRMs for the calibration, followed by a different set of CRMs that were not included in the calibration for the qualification of ASTM C-114. The first test was applied to produce a calibration including only NIST CRMs, then assess JCA CRMs as unknowns and search for ASTM accuracy test results.
The second test was applied to produce a calibration including only JCA CRMs, and then examine NIST CRMs as unknowns to fulfill ASTM C-114 accuracy specifications. All results were found to be within the ASTM C-114 limits.
Conclusion
This article has demonstrated how a cement XRF application using a global borate fusion methodology was effective for determining the materials of interest in the cement industry. In spite of the flexibility of the fusion methodology, the overall method still conforms to the accuracy and precision needs of the international standard methods for analysis of cement (ISO/DIS 29581-2 and ASTM C-114).
Furthermore, qualification by ASTM C-114 of both set of reference materials, which were not included in the calibration, was realized. This is a major step in quality control of chemicals in the cement industry.
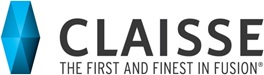
This information has been sourced, reviewed and adapted from materials provided by Claisse.
For more information on this source, please visit Claisse.