The increasing trend towards the usage of natural gas could lead to economic and performance benefits under certain conditions, when incorporated in the design of a carbon fiber manufacturing facility. Although electricity is considered to be dependable and consistent, in many regions of the world it is an expensive option when it comes to industrial use.
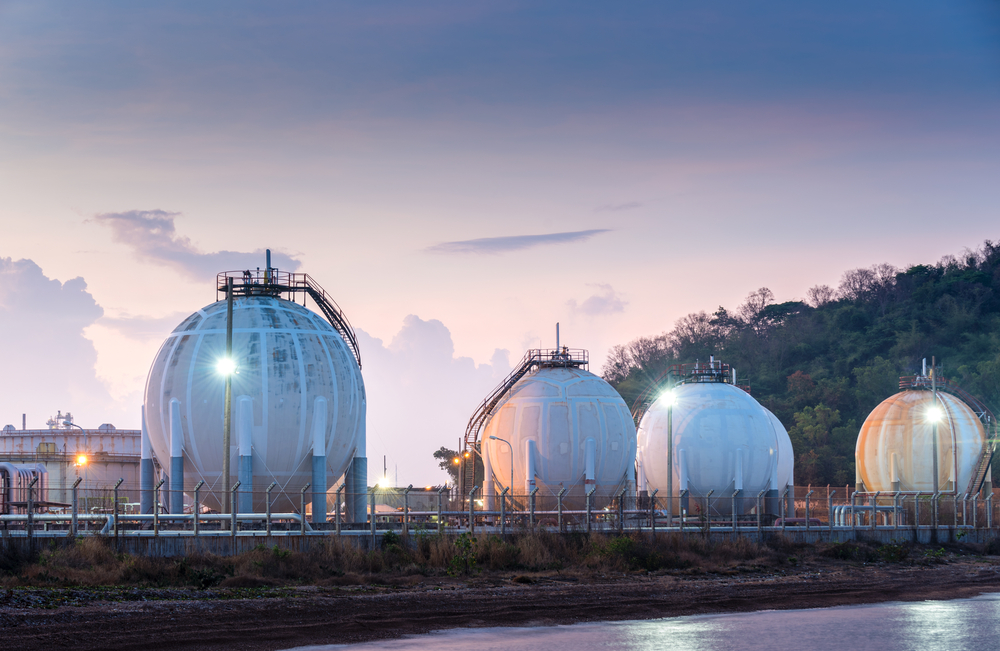
Image Credit: Shutterstock/ tonton
In order to develop economical carbon fiber materials, the industry is working towards solutions considering all phases of the manufacturing process. The usage of natural gas can play a vital role in solving the economics challenge.
This article looks at advancements which will aid in shifting to gas-fired units and hybrid gas / electric designs with thermal uniformity and better control, and with an aim to reduce utilities consumed in the thermal conversion method. Examples to illustrate the benefits are also mentioned.
Universal Plant Concept
Carbon fiber facilities in the future will have to be planned from scratch in order to operate at minimum possible cost. The industry has been focusing mainly on decreasing overall utility consumption, but energy still accounts for 5% to 10% of the overall costs relating to carbon fiber manufacture.
Depending on whether natural gas or electric power is cheaper in a particular region, carbon fiber plants will have to be adapted to utilize one of the two options, thereby realizing the lowest operating costs possible.
However over the years, fluctuating energy markets will complicate matters. Therefore, the best possible solution is a universal plant with a hybrid design, where the same equipment can run on either natural gas or electricity.
The hybrid technology will have to be focused on the oxidation ovens used in the carbon fiber line, as these ovens consume the most energy by a factor of nearly 4 to 1. The reason for this is the extended fiber residence time and high process atmosphere makeup flow rates, compared with the carbonization steps, needed by the Polyacrylonitrile (PAN) oxidation procedure.
The energy consumed for heating the oxidation oven is 32% to 40% of the total energy used in a carbon fiber line. Therefore, any cutback in power cost at this stage will translate to a key reduction in the general operating expense of the carbon fiber line.
Universal Technology and How It Works in Practice
Oxidation generally comprises four to eight thermal zones distributed over two to four large stacks of equipment. Conversely, a carbonization furnace may have four to ten zones within one piece of equipment.
Ovens are simple and contain redundant heating devices, and they consume ten times as much energy as low or high temperature carbonization processes (Omnia, LLC, 2012), therefore carbonization processes tend to benefit the maximum from hybrid heating technology. Hybrid ovens pass a cost/benefit analysis, but with a carbonization furnace, it is not so clear.
A characteristic oxidation oven zone consists of a recirculation fan blowing air across a set of electric heating elements, thereby increasing the temperature of the recirculation air. A temperature controller controls the power supplied to those heating elements and maintains a programmed specific temperature within the fiber processing chamber. With a hybrid oven, an indirect, gas fired heat exchanger in series with the electric elements will be added.
The first temperature controller i.e., gas fired heat exchanger, set point would be manually fixed lower than the second temperature controller i.e., electric elements, as seen in Figure 1. This is so that the first heater would add a pre-defined amount of energy, and the second heater would complete the task to carry the recirculating air up to the necessary process temperature.
If gas is not required, the gas heater would be set to zero and the electric elements would perform all the tasks. If combination of heating sources is needed, when electric utility company requests a decrease in consumption during peak summer days, the load could be distributed between the two heaters. If the oven is to be heated rapidly on startup both heaters can be set to 100% output, thus realizing much faster heating than as single units.
.jpg)
Figure 1. Hybrid Heating Process.
Image Credit: Harper
Current and Future Trends in Energy Production and Consumption
The estimations made regarding the energy industry are greatly different today compared to the estimations in the past years. The current trends are influenced by surplus of supply partly caused by new supply discoveries and a reduction in demand in general.
This has changed the dynamics of energy in the marketplace around the world. Companies can strategic advantages can benefit from these geopolitical paradigm shifts in the future.
There has been an extraordinary shift in recent years in the North America utility markets. One of the shifts is seen in the increased production of natural gas deposits in the U.S. Gulf Coast, the Marcellus region in the eastern portion of the U.S. including New York, Ohio, West Virginia, Pennsylvania, and a small portion of Virginia, the Eagle Ford Shale in southern Texas, and the Haynesville Shale in Louisiana.
These recent discoveries across North America and other places have encouraged energy experts and policy makers to focus on natural gas as the main driver to pursue various goals such as reducing greenhouse gas emissions, decreasing dependence on foreign oil, easing the impact of energy-price spikes, and quickening the transition to renewable fuels.
The role of natural gas in North America’s energy infrastructure will be significant. Figure 3 illustrates that natural gas production is much higher and cost is much lower in the U.S than in other parts of the world. Policy makers in Washington, DC support profitable investment environmental standards for its continuous expansion and therefore, the industry continues to increase its investments in infrastructure. This will maintain the trend of lower gas pricing for industrial consumers, considerably lower than electricity in all categories.
Gas-fired technologies will impact investment decisions for many years as carbon fiber oxidation ovens and low temperature furnace technology remain heavy energy users. Harper International is leading the way in electric, gas-fired, and hybrid oven and furnace technologies.
Theoretical Case Study - Effects of Hybrid Oxidation Technology on Operating Expense
Here a theoretical analysis of three carbon fiber lines and the impact of various oxidation energy sources on operating expense (OpEx) will be dealt with.
Line 1-3 meter – Current industry standard production scale; Line 2-4 meter – Upcoming production scale; and Line 3-5 meter – Future production scale. Two varied ways of powering these lines will also be looked at.
- Scenario 1 – Electric oxidation
- Scenario 2 – Gas oxidation
Harper’s standard process models used these process parameters as inputs to estimate expected energy consumed by heating the oxidation systems in its three lines. Then, these energy consumption values were multiplied by industrial sector costs of both electricity and gas procured from the US Energy Information Administration’s Short Term Energy Outlook. The results are illustrated in Figure 4.
.jpg)
Figure 4. Calculated Annual Cost of Oxidation, 2014.
Image Credit: Harper
The benefit of natural gas is not constantly so great. Figure 5 illustrates the 6 years costs.
.jpg)
Figure 5. Calculated Annual Cost of Oxidation, 2008.
Image Credit: Harper
The cost of natural gas and electric heating is much closer in other parts of the world. Off peak times when there is low demand on the electric grid are an ideal time to cost-effectively heat the oxidation ovens with electricity rather than with natural gas.
Effects of Gas Fired Low Temperature Carbonization on Operating Expense
Here the effect of choosing a gas or electric low temperature (LT) carbonization furnace is looked at to understand the difficulty of the problem. When the process temperature rises, it causes the efficiency of gas heating to decrease.
A moderately temperature profile and basic zone count was assumed when modeling gas and electricity energy consumption. Figure 6 illustrates the cost it would take to heat the LT furnace based on 2014 utility costs. Figure 7 illustrates the results of the same calculations but based on 2008 utility costs.
.jpg)
Figure 6. Calculated Annual Cost of Low Temperature Carbonization, 2014.
Image Credit: Harper
.jpg)
Figure 7. Calculated Annual Cost of Low Temperature Carbonization, 2008.
Image Credit: Harper
In 2008, heating a low temperature carbonization furnace with electricity than with natural gas would have been cheaper. This year was an inconsistency, with market forces momentarily inflating the cost of natural gas in the U.S.
This analysis goes to indicate that even in places such as the U.S with lower cost of natural gas compared with electricity cost, the choice is not constantly obvious. Here the preference of heating source would be as follows: Good – Electric ovens, Gas LT; Better – Gas ovens, Gas LT; and Best – Hybrid ovens, Gas LT.
This good/better/best scenario of gas versus electric heating applies to areas where natural gas is constantly the lower cost energy source. In other regions around the world, it could vary. Therefore, a hybrid plant design is universally beneficial.
Other Considerations
Reliability
In a hybrid oxidation system, greater reliability can be achieved by the redundant heating sources. The electric heating elements and gas fired heat exchangers should be sized for the total heating load so that they can contain either completely electric or completely gas heating.
Therefore, simple reliability via redundancy would be accomplished. In case one heating source fails, the other can maintain operation until the end of the operation cycle when the faulty unit can be changed.
Daily Operation
Customer contracts made out by electric utility companies often place expensive penalties for increased usage during peak demand times, such as mid-day in the summer months. To avoid this, power manufacturers could reduce their production during these times.
For instance, in the summer, industrial gas plants frequently decrease the output of their cryogenic air separation units during mid-day hours. However this cannot be followed by carbon fiber lines as a decrease in output during a campaign, such as slowing the line speed, would alter the time/temperature recipe and thus damage the product fiber.
The only approach to decrease electricity usage during a campaign would be to redirect a part of the load to a secondary heating technique using natural gas during the peak hours.
High Temperature and Ultra High Temperature Furnaces
The final thermal processing steps in a carbon fiber line, namely high temperature (HT) and ultra high temperature (UHT) are not covered in this article. These techniques function between 1200°C and 2800°C.
The effectiveness of natural gas reduces as processing temperature increases, therefore natural gas can generally be used for the oxidation ovens at 250°C, and for the LT Furnace at 800°C. This is, however, not a feasible option for the HT and UHT furnaces. Electric heating is the ideal technology in these techniques.
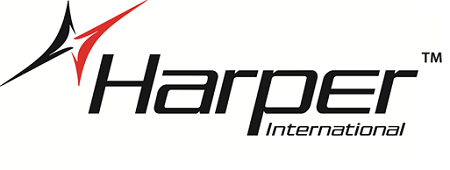
This information has been sourced, reviewed and adapted from materials provided by Harper International.
For more information on this source, please visit Harper International.