A hospital, a police station, a treatment plant, and a remote mine all have assets demanding uninterruptible power, commonly powered by an engine generator as primary or back up power. Engine generators, or also known as “gen sets,” are a combination of an electrical generator and an engine. They provide electrical power to areas where normal utility power is unstable or is not readily available.
Engine generators are used for temporary power demands and are often mounted on transportable skids or trailers. Portable, handheld oil analysis tools are now commonly available and can be employed to extend oil drain intervals and lower routine costs.
The recently amended US EPA NESHAP rules for emergency backup gen sets provide further boost to these tools, allowing condition-based oil drain intervals, so asset owners can realize the advantages of oil analysis. This article discusses the challenges and solutions available to portable/emergency gen set owners who have incurred the cost of time based oil changes.
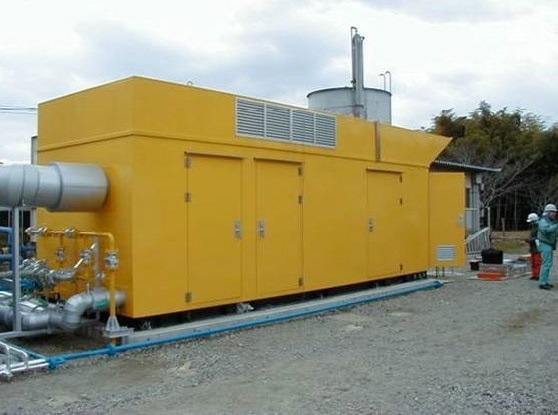
Figure 1. Typical Generator engine enclosure located adjacent to a customer site (Ref: Jenbacher)
Why Change Oil?
It is important to change engine oil before it can no longer adequately perform its intended functions within an engine. Oil in Rotating Internal Combustion Engines (RICE) becomes increasingly contaminated, and the contamination rate can differ based on duty cycle, load factor, environment, age, and fuel types.
Additives deplete to the point that the combination of oil and additives can no longer provide satisfactory protection to the engine. The type of contaminant in the oil needs to be known as this data provides symptoms of the engine condition and enables a direct remedy to rectify the problem.
Top Oil Contaminants
During normal engine operation, a wide variety of contaminants are introduced into the lubricating oil. The following are the most common types of contaminants:
Combustion By-Products
These are exhaust gases (blowby gases) that leak past the piston rings, turbocharger seals, and valve guides into the crankcase. These gases consist of particles of carbon, acids, water, varnish, partially burned fuels, and lacquers. The oil is contaminated by all of these particles.
Sulfur oxides (SOx) are commonly gases with sulfurous fuels (diesel, heavy fuel oil, and liquid fuel distillates). Nitrous oxides (NOx) are more common gases with natural gas (LNG, CNG, propane) fueled engines. Hydrocarbon oxidation (HCOx) can be found in varying amounts.
Acids, Varnish, and Sludge
When the lubricating oil is exposed to hot engine components, or when hot oil is exposed to entrapped air, contaminants such as acids, sludge, and varnish are created due to oxidation and decomposition.
Fuel
These contaminants are usually associated with engine malfunction. However, excessive engine idling or stop-and-go operation can also cause fuel dilution. Viscosity loss is the result of fuel dilution of the oil, causing severe wear and potential seizure if left unchecked. Fuel pump failure, clogged air filters, and faulty injectors are common sources for fuel dilution, although in some cases, fuel lines can rupture and contaminate the oil.
Water
Water vapor is introduced into the oil as a byproduct of combustion. Low load engines and backup generators do not let the oil get hot enough to boil off the water rapidly. Water in combination with blowby gases generate acids, which degrade the oil and corrode the engine surfaces. Ingressed water sourced from the environment or broken cooling lines will lead to rapid oil degradation and in some cases cause severe wear and engine failure.
Coolant
Glycol-based engine coolants are widely used. Head gasket seal rupture, improper cooling line fittings, or cooling system corrosion can all cause coolant mixing with the oil. Glycol is particularly corrosive to non-ferrous bearing surfaces. Excessive coolant results in the telltale sheen or mayonnaise oil emulsion, causing engine seizure.
Soot
Soot is formed by retarded injection timing and burning fuel mixing with oil on the cylinder liner(s). Excessive soot leads to abnormal valve and injector train wear and overloads the emissions control systems, resulting in air quality fines.
Oil analysis, a method designed to assess the engine health through fluid analysis, can monitor all of these contaminants.
Routine Maintenance and Oil Condition
Some of the main operating costs of running and maintaining large engine generators are the material and labor costs associated with changing oil based on a fixed operating time interval. This process is usually recommended by engine manufacturers and increasingly by local regulations aimed at curbing emissions (EPA NESHAP rules).
Oil changes are recommended based on operating hours or calendar based intervals, irrespective of whether the generator has operated at full load or is idle for most of the time. Until now, this task was non-negotiable, especially if the gen set was under warranty. In fact, the US EPA mandates oil changes for stationary engines used for emergency backup power.
There are problems with scheduled oil changes that trouble engine owners:
- Good oil is changed unnecessarily. Not all generators are operated at the same load amount, so it is perhaps unnecessary to change oil for particular generators at the recommended change interval. This leads to increased operating cost and waste, including material, labor, service engineer utilization efficiency as well as recycling cost. A significant cost saving can be achieved if it is possible to extend an oil change interval for even a fraction of the generators
- An ongoing contamination problem cannot be resolved by scheduled oil changes. Engine damage caused by contamination of the lubricant can continue, usually increasing in severity.
- Catastrophic failures can still occur and the cost of repair and downtime is not insignificant, even though it may be infrequent
The Role of Oil Analysis
Forward thinking gen set owners and service providers have been aware of these problems for some time, and use onsite or offsite oil analysis to identify the condition of lubricants and equipment. Using this information, they can determine whether the oil can be extended or if it needs an overhaul.
The US EPA acknowledged the benefits of condition-based changes due to oil analysis. Recently, the agency amended its regulations for stationary generators in backup or emergency mode to enable extended changes if oil condition condemnation limits are not exceeded (Figure 2).
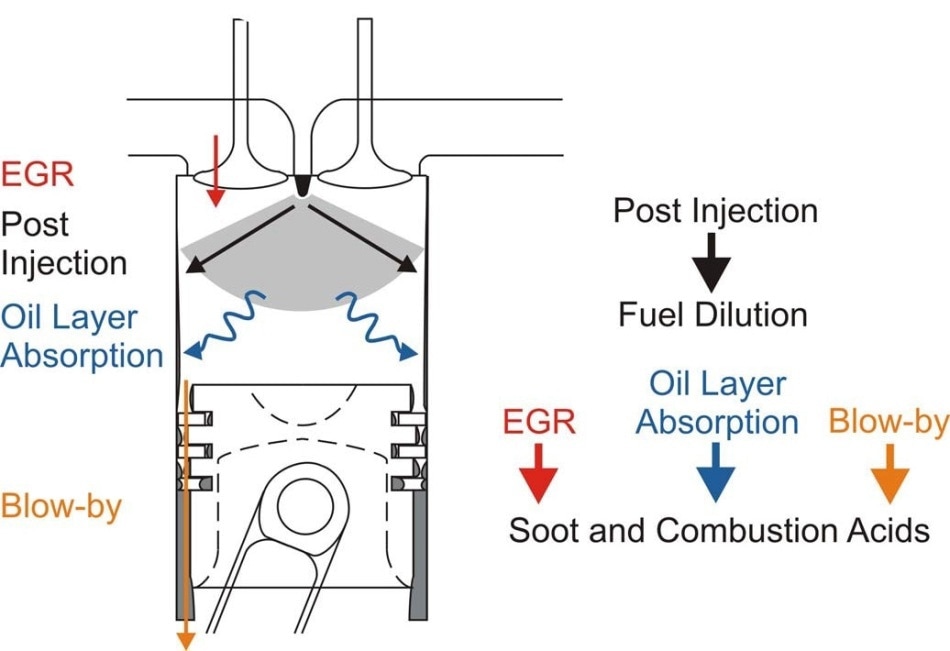
Figure 2. Oil is contaminated by a number of contaminants from the combustion chamber (Ref: MIT)
The rule is specific that condemned oil must be changed within two days of the engine owner receiving this information. If oil condition is analyzed at the time of scheduled service, a decision can be taken immediately as to whether the oil needs to be changed or if minor repairs are required.
It not only lowers the operation and maintenance costs, but also makes the engine run longer. A similar scenario can occur in managing an automotive fleet. Time-based oil change has been proven to produce waste because of unnecessary oil changes.
Although the cost savings are real and the market is starting to support them, why condition-based oil changes have not yet become a popular practice is an intriguing question. Two good reasons are as follows:
1. Investment in a dedicated laboratory is not always practical. Large power generation plants and mining operations often have central oil analysis labs located onsite for continuous monitoring of the machine and oil condition of an equipment population. Based on the recommendation of experienced laboratory data analysts, decisions about oil change and other maintenance activities are taken. Although this is the best industrial practice, applying this practice is difficult in the case of engine generator fleets due to the large, upfront capital investment and the requirement of hiring laboratory technicians and data analysts. Even after establishing a central laboratory, the distributed or temporary nature of the gen sets prevents service engineers from taking immediate decisions because of the delay in receiving results from the central lab. This is the issue with relying on contract laboratories to execute this task.
2. Previous onsite oil analysis technologies are insufficient. The tools used for oil condition monitoring have to satisfy the following requirements in order to implement an effective condition based oil change practice:
- Portable – Maintenance engineers can carry it from one generator to another
- Easy to use – No need to hire an experienced oil expert
- Cost effective – Return on investment in one or two years
- Fast – Allows engineers to use their time on site more efficiently
- Comprehensive – Provides the complete picture of oil condition with minimal chance of false alarms
- Repeatable and definitive – decisions can be easily made
- No waste stream and no recycling of hazmat chemicals – lowers the cost of training on handling, storage, transportation, and recycling of chemicals
This is not an easy list of requirements as most of the commercially available tools can partially fulfill these requirements. The tools may be simple and user-friendly but not definitive, or they may be expensive and accurate but not user-friendly or easy to deploy in the field.
Spectro Scientific has recently launched a comprehensive set of portable oil condition analyzers that provide a complete picture of in-service oil condition. The battery-powered tools are compact in a handheld form, and as accurate as laboratory instruments. These portable tools are currently even used at oil analysis laboratories.
Each instrument uses a small oil sample volume, measured in drops, and does not generate any waste stream. Chemicals are not needed for oil analysis, eliminating the need for hazmat materials or recycling. Without sample preparation, oil samples retrieved directly from engines can be analyzed within a few minutes.
Results can be read on the analyzer’s display and contain alarms to alert users to make informed decisions immediately. The set of tools all originate from joint development with the US Military for condition-based oil changes. These tools are used in the field to improve reliability and lower costs.
Maintenance personnel now have the power of decision making in the field and are transforming the industry. As a result, condition-based oil changes now become both affordable and practical.
Spectro Scientific Portable Oil Condition Combinations
The set of portable oil condition monitoring tools from Spectro Scientific include a temperature-controlled kinematic viscometer, a portable fuel dilution meter, and an infrared spectrometer (FluidScan). This triple combination provides a complete picture of in-service oil condition, including coolant contamination, oil degradation, fuel contamination, water contamination, and viscosity.
All three instruments are battery powered and use less than 1 ml of oil collectively. Table 1 lists in-service oil parameters that can be determined using these combination kits.
Table 1. US EPA NESHAP ZZZZ rule Amendment (Oct 2013) Condemnation limits for in-service oil
PARAMETER |
CONDEMNING LIMITS |
Total Base Number
(CI RICE only) |
<30% of the TBN of the oil when new |
Total Acid Number
(SI RICE only) |
Increases by more than 3.0 mg of potassium hydroxide per gram from TAN of the oil when new |
Viscosity |
Changed by more than 20% from the viscosity of the oil when new |
% Water Content by Volume |
>0.5 |
Table 2. Critical engine oil parameters
GENERATOR ENGINE TYPE |
LUBRICANT PARAMETERS |
Diesel, Gasoline, Bio-diesel, Propane, Bio-gas, Natural Gas |
Oxidation, Nitration, Sulfation, Anti-wear additive, TBN, Water, Glycol contamination, Soot, Fuel dilution, Viscosity |
FluidScan®
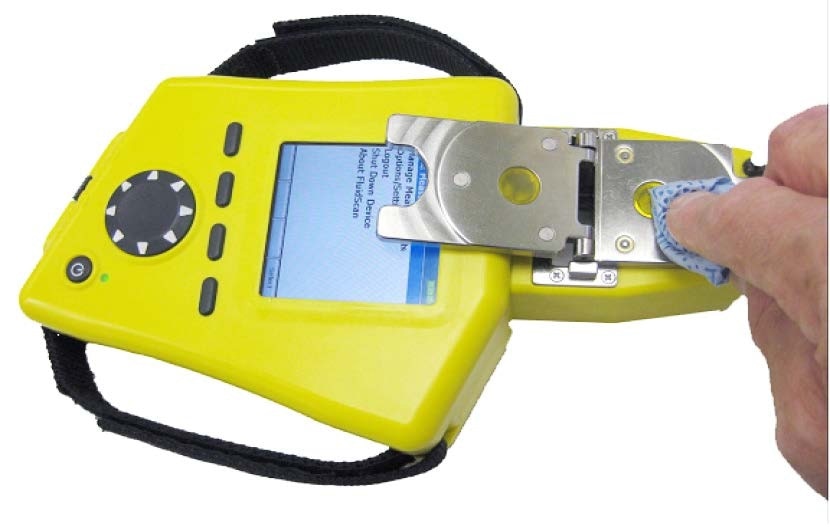
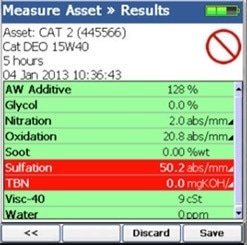
FluidScan (Q1000) handheld infrared spectrometer[1,2] measures oil absorbance spectrum in the mid IR range (2.5 mm - 12 mm). For better portability and durability, diffraction grating-based optics with detectors was used in place of FTIR technology, a commonly used method in oil analysis laboratories.
Chemometric calibration was applied on the raw IR spectrum to get oil condition information such as oxidation, sulfation, nitration, anti-wear additive, water, total base number, glycol contamination, and soot. [3,4] The technique was recently granted an ASTM D7889 standard method.
FluidScan is widely used in labs as a titration alternative, in marine vessels, in fleet management for mining trucks, in industrial plants, and in power generation plants for oil condition-based predictive maintenance. The patented flip top cell uses three drops of oil, requires one minute and does not need any chemicals solvents or chemicals for cleaning.
The instrument also has an onboard database with asset information and preset alarm limits utilizing a traffic light system, enabling maintenance engineers to make decisions immediately right after the measurement.
Portable Kinematic Viscometer
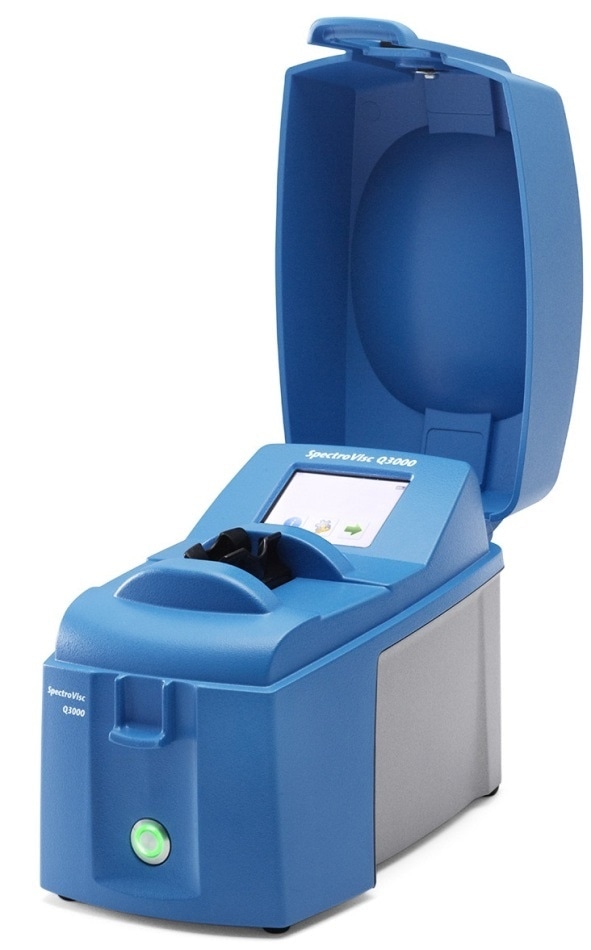
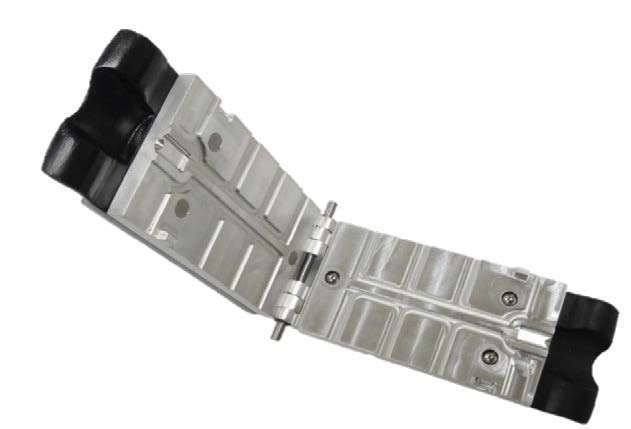
The battery powered Q3050 portable kinematic viscometer measures oil viscosity at a controlled temperature (40 °C).[5] Based on a preset viscosity index of a given oil, the tool can extrapolate viscosity at 100 °C. The patented split cell requires only two drops of oil oil (60 µL), completes the test in a couple of minutes, and does not need any solvents or chemicals for cleaning.
The result is 3% accuracy, which is enough to make informed maintenance decisions. It complements FluidScan well and is commonly used in marine vessel and mining truck settings.
Fuel Dilution Meter
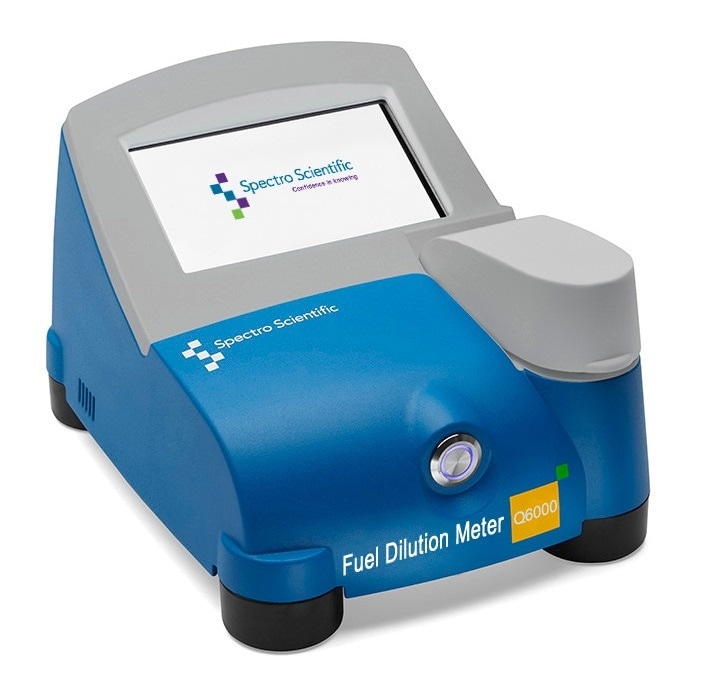
The portable Fuel Dilution Meter (Q6000) is the new member of the oil condition family. The Fuel Dilution Meter (Q600) was the predecessor, a stationary analyzer used in analytical laboratories and onsite laboratories to screen for fuel dilution in engine oil. It was jointly developed with the US Navy and is commonly used in railway, mining, and marine environments.
The measurements are based on a calibrated response of a Surface Acoustic Wave (SAW) sensor to a fuel vapor aromatic in the sample bottle headspace, which varies in proportion to the fuel content in the engine oil sample. The new fuel dilution meter inherited the SAW sensing technique but is compact, battery operated, and the patent-pending sampling system makes it user-friendly in the field and uses only 500 µL of used oil.
The three instruments complement each other and provide a complete set of oil condition information. They all feature the same set of characters, including
- Small, light, portable and battery operated
- Fast (one to two minutes each)
- Use small volumes of oil (<1 mL combined)
- Accurate (correlates to laboratory results)
- No need for chemicals or solvent to clean (requirement for onsite analysis)
- Easy to use (no need for an oil expert)
This set of features makes maintenance professional's life easier. Now, oil analysis can be performed at the generator and immediate and accurate decisions can be made with confidence.
Conclusion
Advances in oil analysis techniques make portable and accurate oil condition monitoring instruments available to maintenance professionals. Companies managing of a fleet of engine generators can now easily implement a condition-based oil change practice. As a result, operating expenses can be lowered by minimizing unnecessary oil change waste and maintenance costs, improving the reliability of the machine and eliminating catastrophic failures. These cost benefits can be achieved with the Spectro Scientific portable fluid condition monitoring combination solution.
References:
- Under the Hood – Meeting the Design Challenge of the FluidScan® Handheld Infrared Oil Analyzer – Spectro Scientific white paper
- Overview of FluidScan® Handheld Infrared Oil Analyzer – Spectro Scientific white paper
- Using Infrared Spectroscopy for the Determination of TAN and TBN in Machinery Lubrication Oils – Spectro Scientific white paper
- Measuring Water with the FluidScan® Fluid Condition Monitor
- EPA NESHAP Quad Z Requirements
- P. Henning, SpectroVisc Q3000 Series Viscometer – a Portable Oil Analysis Solution for Field Based Users
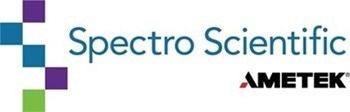
This information has been sourced, reviewed and adapted from materials provided by AMETEK Spectro Scientific.
For more information on this source, please visit AMETEK Spectro Scientific.