Equipment for thermal processing of high-purity and advanced materials needs to reliably balance high-quality product output, economic production, and safety. In the current market, companies need to balance various product lines, each requiring the same standards.
Harper International understands that each product needs its own customized processing solution. In order to utilize one thermal system for a variety of material developments and advanced material product lines, advancements in Harper’s rotary furnaces allow the interchange of process tube shapes or materials (Figure 1).
.jpg)
Figure 1. Rotary furnace system.
Image Credit: Harper
In a continuous thermal system such as an indirectly fired rotary furnace, heat is applied to the incoming process material over several thermal control zones. The system includes feeding, heating, cooling, and gas handling, and provides an efficient method for processing powders. Rotary tube furnaces are primarily used due to their efficiency in heat and mass transfer for powders and low material handling requirements.
A rotary tube furnace transfers heat from the heat chamber to a rotating tube. The process materials are present in the tube that has the required special atmosphere. The heat from the tube wall is transferred by the furnace to the bed of material being processed.
The material is continuously conveyed through heating and cooling sections as the process tube is maintained at a small angle and rotated. In comparison with other types of equipment, rotary furnaces have one of the lowest operating costs and highest thermal efficiencies.
This article presents two cases in which Harper International designed unique combination furnaces to suit the specialized needs for advanced material development.
Case study 1: Alloy/Ceramic Tube Rotary Furnace Combination System
Advanced ceramic materials for applications requiring high thermal conductivity, such as high-power LED lighting products and other heat-sink substrates are being developed by ECRIM, a leading ceramic microelectronic materials company.
Without proper research and development before the production process can lead to wasting time and raw materials that are usually sparce for a new project, and result in low-quality and inconsistent products. As a first step, ECRIM develops the required processing for its new materials in a process development mode.
Various parameters such as residence time, tube inclination angle, tube rotation rate, atmosphere flow-rate, temperature profile, feed rate, and powder bed depth are optimized, and then the parameters are used to scale up production while the precise product requirements are maintained.
The company’s development of new products and processes necessitates that its equipment can easily vary the processing parameters. The company required a rotary furnace for obtaining better gas–solid contact, controlled atmosphere with gas-tight rotary seals, material mixing, and continuous production of its products.
Tube Material Selection
Rotary furnaces use a variety of tube materials, including graphite, alloys, aluminum oxide, and silicon carbide. The tube material in a rotary furnace is carefully selected so that it withstands the process atmosphere and temperature. Selecting the incorrect tube material can have several undesirable consequences such as product contamination.
Consequences can also be serious if hazardous materials and/or gases are processed in the interior of the tube, as it is the only object separating the process environment from the ambient atmosphere.
Ceramic tubes can shatter if subjected to too much stress under improper conditions, which can cause significant damage in the furnace interior. Alloy tubes can crack if they are highly stressed or when they react with the process environment. Thermal shock, cost, and creep stress also are critical in tube selection. The correlation between process tube material type, maximum allowed stress, and temperature, for many stainless steel alloys is shown in Figure 2.
.jpg)
Figure 2. Temperature versus allowable creep stress of stainless steel alloy process tubes.
Image Credit: Harper
Maximum allowed stress depends on the amount of creep (deformation) a tube can tolerate before rupture. Usually, furnace tubes are designed so that the tube deformation due to creep stress is less than 1%, after 10,000 hours of operation at maximum process temperature. Stress on the tube can vary depending on the rotational speed and amount of material inside the tube, suspended length of the tube, and diameter and thickness of the tube.
Cast and wrought alloys are used by manufacturers for high-temperature applications. As shown in Figure 2, cast alloys usually have higher allowable creep stress. In addition, some materials are available only in cast form as they do not have enough ductility to be worked into a wrought tube, such as high chromium-content alloys.
For rotary thermal systems requiring diameters greater than ~9 - 12 inches, users show strong preference to alloy tubes as they are substantially less expensive, possess shorter lead times, and do not suffer disastrous brittle failure.
Thermal stress increases in proportion to tube diameter, and for brittle ceramic this means an increased probability of tube failure. Costly large-diameter tubes with long lead times are not generally practical or economical, as random defects can cause ceramic tubes to fail at any time.
If a product requires high purity and is being treated or the metals in the alloy tube have potential to react with the product or off-gases formed during production, then ceramic tubes should be considered. Ceramic tubes are useful in high-temperature applications and resist corrosion. Some of the commonly used ceramic tubes are quartz, aluminum oxide, silicon carbide, and, in some cases, graphite.
Graphite tubes and muffles are used in furnaces that require high purity or high temperatures. They are ideal for environments in 1,000 - 3,000 °C and for inert atmospheres, such as argon or nitrogen. As carbon will oxidize at these temperatures, they are not used for oxidizing environments.
Silicon carbide tubes are available in many forms, including reaction-bonded silicon carbide, nitride-bonded silicon carbide, recrystallized silicon carbide, solid-state-sintered silicon carbide and liquid-phase-sintered silicon carbide. Depending on the grade of silicon carbide, they are ideal for processes that require air atmospheres less than 1,400 °C. Making a controlled atmosphere can be difficult as many economical grades of silicon carbide are porous.
Aluminum oxide tubes, like silicon carbide tubes, are available in many grades. Aluminum oxide tubes that can withstand some thermal stresses are highly porous, and are ideal for processes that do not need a controlled atmosphere environment. These tubes are preferred for processes needing temperatures ≤1,600 °C, depending on mass rate of the process material and tube size. However, the tubes must be heated and cooled very slowly as they cannot easily withstand thermal shock.
Quartz tubes are suitable for processing at temperatures <1,300 °C and for oxidizing, reducing, or inert atmospheres, and also many high-purity applications. The tubes are non-permeable and have a very low coefficient of thermal expansion compared to most ceramic tubes. However, the tubes are brittle and can break due to random defects.
ECRIM’s production required a quartz process tube based on strict product purity, working temperatures that reached 800 °C, and an atmosphere with a precise composition of air and nitrogen for a tightly controlled oxidation reaction. For the required tube diameter, a quartz tube is substantially more expensive than an alloy tube and could break during the company’s research and development stage. An alloy tube introduces contamination risks, even though it can withstand the high temperatures.
Therefore, ECRIM worked with Harper to design a single, continuous thermal rotary processing system that could easily function as an alloy tube and a quartz tube.
System Design
Harper’s equipment design solution uses an alloy tube for process development, followed by a quartz tube for significant quantity production of high-purity material. Other than being multifunctional, this technique avoids contamination between research and development material and production material.
Three individually-controlled temperature zones form a part of the single thermal processing system. The temperature profile can be easily optimized during process development. The furnace has a clamshell design that enables opening the top half of the furnace, exposing the furnace’s internal section.
The top half of the clamshell is pneumatically actuated and is hinged at one end, enabling easy accessibility of the furnace tube, heating elements, and insulation, and avoiding usage of a crane.
A completely sealed rotary tube system and enclosed discharge collection to maintain atmospheric integrity form a part of the rotary tube furnace. In order to allow the seal to move with the expanding tube, the exit and entrance hoods, and rotary seals are on rails. This is particularly important if an alloy tube is used, as it has a thermal expansion of ~1.35%, which much more than that of the quartz tube.
Residence time is directly influenced by tube inclination and tube rotation. Tube rotation can be regulated by a programmable logic controller system through a variable frequency drive. Thus, the rate of tube rotation and resulting material residence time during process development are easily changed by ECRIM.
Tube inclination is controlled by a pneumatic adjustable jack for easily adjusting the system without using a crane.
This furnace is unique due to its ability to use an alloy or quartz tube. A Harper rotary tube of this type is usually supported by flanges that are welded to the external surface of the tube. The flanges are bolted to tire assemblies that are set upon casters.
The casters resist heat and are designed to be gentle on the tube. Rather than using flanges welded to the exterior of the tube, this dual material rotary furnace system uses tube clamps (Figure 3). The tube clamps are secured by features provided on the exterior circumference of the tube.
The same tire can be interchanged by ECRIM between alloy and quartz tube assemblies. A variable speed drive connected to the tire through a V-belt to the reactor tube, mounted at the end fixed from expansion, rotates the tube.
.jpg)
Figure 3. Harper dual-material tube assembly uses tube clamps instead of welded-on flanges.
Image Credit: Harper
By unlocking and sliding away the feeder, on rails, ECRIM removes the tube assembly from the entrance seal assembly. The entrance seal assembly and exit hood assembly are also unlocked and slid out of the way for tube removal as they are also on rails.
After pneumatically opening the furnace clamshell, the tube can be easily removed and replaced. The company can test and develop new materials that utilize ceramic or alloy tubes for its processes.
ECRIM’s mission to make advanced ceramic materials for applications needing high thermal conductivities is duly supported by the development of this furnace. Harper’s design of this dual functionality furnace supports the requirements to work with several types of tubes, saving time, money, and facility space.
Case Study 2: Rotary/Mesh Belt Rotary Furnace Combination System
To help in the design of a single, continuous thermal processing system, a national laboratory with limited available floor space, contacted Harper. The lab required a continuous thermal processing system at operating temperatures of up to 1,050 °C and in different types of atmospheres for the process development for commercial production of carbon materials.
The lab also wanted to vary carbon precursor materials in particle size, composition, moisture content, shape, and density. Two different types of furnace systems were needed for the variations in precursor materials: a mesh belt furnace and a rotary furnace.
Precursors possessing good flow properties and requiring better gas–solid contact and shorter residence time are suitable for rotary systems. As the mixing and tumbling throughout the tube would be detrimental to the product, a rotary furnace is not an option for fragile precursors.
Residence time in a rotary furnace is controlled by tube inclination and tube rotation rate. Materials that require longer and more controlled residence time are also not suitable for a rotary furnace, because long residence times need a slow tube rotation rate and a small angle of inclination, creating difficulties in controlling residence times for more than two hours.
In a continuous thermal system such as a mesh belt furnace, heat is applied to the incoming process material via several thermal control zones. The system is powered by either gas or electric heating. Atmospheres in the reaction chamber are controlled by a muffle.
If an inert atmosphere is required, the product conveyed on the belt can enter a purge chamber before entering the heated zone of the furnace. Process materials are fed non-stop and directly onto the belt or kept in crucibles for thermal processing. The process material progresses through the length of the furnace supported on the belt, since the belt moves through the heated section supported by the alloy muffle.
The belt speed controls the soak time in each temperature control zone as the belt conveys the material through each zone. After thermal processing, the material is unloaded after it travels through a cooling section and an exit purge chamber.
At the initial stage it looked as if the laboratory needed two separate furnaces to satisfy all required design aspects. Traditional rotary and mesh belt furnaces were first considered by Harper.
However, as the lab faced limitations in space and resources, two stand-alone furnaces were not optimal. Instead, the Harper team designed a multifunctional thermal processing system, where using a single thermal platform enabled a rotary tube furnace to be transformed to a mesh belt furnace (Figure 4).
.jpg)
Figure 4. Mesh belt/rotary thermal combination system designed for a national laboratory with space constraints.
Image Credit: Harper
System Design
The clamshell design of the single thermal processing system allows the top half of the furnace to open to expose the internal section. To maintain atmospheric integrity, the rotary tube furnace has a fully sealed rotary tube system and enclosed discharge collection.
Adjustments to heat-up rate, soak period, and cooling rate are made using the four control zones. By adjusting the system’s inclination angle, as well as the rotational speed of the tube and feed rate from the screw feeder system, the process capacity can be controlled.
A user can reconfigure the main parts of the system in rapid succession to transform the system between mesh belt and rotary tube systems, similar to autobots in the movie “Transformers.” If starting with the rotary tube systems, the user can remove the screw feeder, rotary tube (via clamshell access), and entrance and exit hoods.
Next, the alloy muffle, purge chambers, cooling section, and mesh belt can be installed by the user. A minimum number of subassemblies need to be reconfigured since the mesh belt drive stands and the heating chamber remain in place.
Since the purge chambers are located at entrance and exit ends of the furnace system, the mesh belt thermal system also is atmospherically controlled. Adjustments to the thermal profile are done by using the four control zones. The internal alloy muffle with many exhaust ports at important locations to remove corrosive off-gases was also designed by Harper.
Both furnace systems are gas-tight and operate under different atmospheres such as corrosive and reactive gases, and can operate in the 1,000 °C range. The thermal processing cycle varies between from 30 minutes to 10 hours.
Now, the leading national laboratory has attained the flexibility for testing and developing new carbon materials from various sources, including renewable materials, in support of its mission to further the future of materials research. The requirements to work in a limited laboratory space and to obtain the flexibility in processing various materials in rotary and mesh belt furnace systems was supported by Harper’s design of this dual functionality furnace.
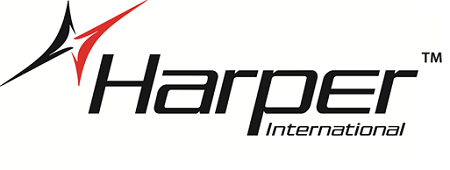
This information has been sourced, reviewed and adapted from materials provided by Harper International.
For more information on this source, please visit Harper International.