Polymerization in a batch reactor can be easily controlled by monitoring the dielectric properties. Prior studies have demonstrated that the free-radical polymerization of methyl methacrylate can be observed by DEA.1
In this process, the change of log(ion viscosity) corresponded with fractional monomer conversion as well as physical viscosity.
While standard laboratory gravimetric techniques have to be carried out off-line, dielectric cure monitoring offers the benefit of real-time, in-process measurement of polymerization.
Resins that are processed in batch reactors usually begin with a high monomer concentration, as illustrated in Figure 1. During this stage, mobile ions can easily move through the material, leading to very low ion viscosities, or low resistivities.
.jpg)
Figure 1. Unreacted Monomers. Image Credit: Lambient Technologies.
Upon heating, the monomers react and combine to form polymer chains, as shown in Figure 2.
.jpg)
Figure 2. Early-stage polymerization. Image Credit: Lambient Technologies.
While the number of molecules decreases during this time, their molecular weight increases. There is also an increase in mechanical viscosity along with increased resistance to the flow of mobile ions in an electric field.
This electrical resistance is measured by dielectric cure monitoring, which uniquely helps in directly observing the material state in the reaction vessel.
As an increasing number of monomers are polymerized, log(ion viscosity) increases in a way that is analogous to the plot shown in Figure 3. It must be noted that only the variation in log(ion viscosity) corresponds with fractional monomer conversion — the real correlation and scaling factors should invariably be established experimentally.
.jpg)
Figure 3. Change in log(IV) versus Fractional Monomer Conversion. Image Credit: Lambient Technologies.
The value of log(ion viscosity) relies on the level of ions and impurities, and may differ from one batch to another. Consequently, log(ion viscosity) alone is not a dependable measure of resin polymerization — only the change is beneficial.
Standard Instrument Configuration
A computer equipped with data acquisition software can be connected to a dielectric cure monitor via a USB or RS-232 serial port. The instrument links to a thermocouple and a dielectric sensor, which are submerged in the batch reactor. Figure 4 shows this standard configuration.
.jpg)
Figure 4. Dielectric cure monitoring system for a batch reactor. Image Credit: Lambient Technologies.
A dielectric sensor typically includes two interdigitated electrodes on a ceramic or polyimide substrate. The process temperature — measured by a thermocouple — is significant because dielectric properties change with both the degree of conversion and temperature of the material.
Simplified Sensor for Batch Reactors
In a majority of cases, the resin present in a batch reactor has low ion viscosity during the whole process. As a result, a sensor with interdigitated electrodes is often not used. Since the electrodes take up a huge area and are in close proximity to one another, such a sensor is highly sensitive. Toward the end of cure, thermosets have very high ion viscosities, and therefore, a sensor that has correspondingly high sensitivity is required to analyze the material at this stage.
But when there is low ion viscosity, the large signal produced from interdigitated electrodes can surpass the range of the dielectric cure monitor, leading to substandard measurements. For batch reactors, it might be better to utilize a basic electrode design whose output level is more appropriate for the instrument.
Figure 5 demonstrates how two wires with exposed ends turn into a low-sensitivity dielectric sensor.
.jpg)
Figure 5. Simplified sensor for use with a batch reactor process. Image Credit: Lambient Technologies.
It is important to determine the optimum configuration by trial and error, but a sensible design can begin with 5 mm separation and 5 mm of exposed wire between the exposed ends, as shown in Figure 6.
.jpg)
Figure 6. Simplified dielectric sensor for low ion viscosity, an example configuration. Image Credit: Lambient Technologies.
A 24 AWG or thicker solid wire should be used, so that it is easily formed and stays rigid even after shaping. Teflon insulation should be used for chemical resistance and ruggedness, and the ends should be secured so that their separation does not change.
The sensor should be tested by making a measurement in the material under test at the process temperature. The sensor’s configuration should be adjusted as required by using the guidelines mentioned below:
- If the signal level is very high, the separation should be increased or the length of the exposed wire should be decreased
- If the signal is very low, the separation should be decreased or the length of the exposed wire should be increased
Hazardous Environments Around Batch Reactors
Large volumes of resin are required in batch reaction processes, and in addition to this, flammable gases are also produced.
The National Fire Protection Association (NFPA) Publication 70, the CEC, and NEC have classified hazardous environments by Class, Division, and Group as shown below:
- Class—Type of flammable substance
- Class I—Locations where flammable gases or vapors may exist
- Class II—Locations where combustible dust may exist
- Class III—Locations where easily combustible flyings or fibers may exist
- Division—Area classification
- Division 1—Flammable substances exist under the usual operating condition and/or induced by frequent equipment failure or frequent repair or maintenance work
- Division 2—Flammable substances are used or handled but usually in closed systems or containers, and they can escape only under irregular operating conditions like the breakdown of the system or rupture of the container
- Group—Gas group, or flammability
- Group A—Example: Acetylene
- Group B—Examples: Butadiene, hydrogen, propylene oxide, and ethylene oxide
- Group C—Examples: Ethyl ether, cyclopropane, and ethylene
- Group D—Examples: Ammonia, acetone, propane, butane, benzene, natural gas, methanol, gasoline, and ethanol
Preventing Ignition or Explosion in Hazardous Environments
In dangerous locations, dielectric cure monitors and similar electrical equipment usually need intrinsically safe barriers in-line with sensors to prevent the explosion or ignition of flammable gases. Intrinsically safe barriers (I.S. barriers) are essentially protective circuits developed to restrict current and voltage to electrical devices.
The restrictions prevent hazardous discharge of energy and rely on the classification of the unsafe environment and the device requirements.
Intrinsically safe barriers, which include a fuse, a resistor, and one or two Zener diodes, should be linked to a ground point. Intrinsically safe barriers would be able to handle negative, positive, or AC signals, with configurations illustrated in Figure 7.
.jpg)
Figure 7. Intrinsically safe barrier configurations. Image Credit: Lambient Technologies.
Explosion-Proof Enclosures
Intrinsically safe barriers make sure that the available energy is inadequate to ignite the dangerous substance that may potentially exist, and they avoid the requirement for exclusive explosion-proof enclosures around measurement circuitry.
Explosion-Proof Apparatus is defined by Article 100 of the NEC as follows:
Apparatus is enclosed in a case that is capable of withstanding an explosion of a specified gas or vapor that may occur within it and of preventing the ignition of a specified gas or vapor surrounding the enclosure by sparks, flashes, or explosion of the gas or vapor within, and which operates at such an external temperature that a surrounding flammable atmosphere will not be ignited thereby.
NEMA Type 7 enclosures are engineered to fulfill explosion-proof requirements in indoor Class I, Group A, B, C, or D locations. These enclosures can tolerate the pressures caused by an internal explosion of specified gases, and have the ability to contain the explosion and inhibit the ignition of a surrounding explosive atmosphere.
Although intrinsically safe barriers can avoid the use of explosion-proof enclosures, users must always consult with the company or local safety authority to confirm whether the equipment fulfills safety requirements.
Implementing Intrinsically Safe Barriers into a Batch Reaction Process
The first step to implement dielectric cure monitoring in a batch reaction process is to identify the category of an unsafe environment. Then, suitable intrinsically safe barriers should be selected for use with dielectric sensors and thermocouples. These barriers should be installed in an enclosure to support connectors to the sensors as well as connectors for linking to the instrumentation.
For instance, a batch reactor is in a Class I, Division 2, Group D hazardous environment. The company R. Stahl2 produces intrinsically safe barriers and the components given below can be utilized to arrange an Intrinsically Safe Interface:
- For dielectric sensors: R. Stahl 9001/02-093-390-101 I.S. barrier (Ω = 31–36, V = ±6 VAC, IMAX = 110 mA)
- For thermocouples: R. Stahl 9001/01-050-150-101 I.S. barrier (Ω = 42–49, V = 1–3 VDC, IMAX = 20–61 mA)
- Enclosure: R. Stahl 8150/5-0200-0300-150-3321 stainless steel enclosure
It must be noted that while the enclosure is not explosion-proof, it is safe and appropriate when utilized with intrinsically safe barriers for Class I, Division 2, Group D settings.
This enclosure equipped with the intrinsically safe barriers is the Intrinsically Safe Interface and has been schematically illustrated along with the dielectric cure monitoring system in Figure 8.
.jpg)
Figure 8. Apparatus for a single channel of intrinsically safe process monitoring in a batch reactor. Image Credit: Lambient Technologies.
Due to the added circuitry in the I.S. barriers, dielectric measurements may have accuracy or frequency restrictions when compared to the base instrument.
Important: For safe operation, both the Dielectric Cure Monitor and the Intrinsically Safe Interface should be linked to the same electrical ground.
Figure 9 schematically illustrates a complete, four-channel system with cabling, utilizing an LT-451C Dielectric Cure Monior.3
.jpg)
Figure 9. Four-channel dielectric cure monitoring system with intrinsically safe barriers (Computer and thermocouples not shown for clarity). Image Credit: Lambient Technologies.
A ground reference is required for the intrinsically safe barriers, and the enclosure should be grounded to guarantee their protective function. For excellent measurements, the LT-451C Dielectric Cure Monitor should have the same ground as the barriers.
The ground connection points of the LT-451C Dielectric Cure Monitor and the Intrinsically Safe Interface are shown in Figure 10. These points should be linked to the ground reference, which should be the same as the safety ground of the AC Mains supply.
.jpg)
Figure 10. Grounding points of the Intrinsically Safe Interface and LT-451C Dielectric Cure Monitor. Image Credit: Lambient Technologies.
Dielectric cure monitoring can offer real-time, on-line data about the polymerization in a batch reaction process. But batch reactors usually work in dangerous settings with combustible gases.
Intrinsically safe barriers can be used along with dielectric sensors and thermocouples to restrict energy below the ignition point of these gases and thus avoid an explosion. Valuable process control of batch reactions in large-scale production of resin can be realized using a dielectric cure monitoring system with an Intrinsically Safe Interface.
References
- Crowley, Timothy J., and Choi, Kyu Yong, In-line dielectric monitoring of monomer conversion in a batch polymerization reactor, Journal of Applied Polymer Science, Feb. 28, 1995, pp 1361-1365
- R. Stahl, Inc., Stafford, TX USA.
- LT-451C Dielectric Cure Monitor, manufactured by Lambient Technologies, Cambridge, USA. https://lambient.com
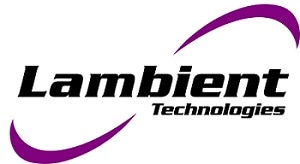
This information has been sourced, reviewed and adapted from materials provided by Lambient Technologies.
For more information on this source, please visit Lambient Technologies.