As devices become smaller, the requirement for reliable connections becomes more important. Plasma treatment is used to improve and enhance reliability.
In this interview, Dave Selestak, Senior Business Development Manager from Nordson MARCH talks to AZoM about the Evolution of Plasma Treatment.
Nordson MARCH has been around since 1986, starting as Advanced Plasma Systems and March Instruments and then becoming part of Nordson. What are the most significant changes you’ve seen in plasma treatment since then?
The use of plasma treatment, not just with MARCH’s technology, is to improve and enhance reliability. As components and devices get smaller, the requirement for reliable connections is becoming more critical.
Plasma enables this level of reliability, from mobile phones to automotive sensors to implanted medical devices to missile guidance.
Technologies like fan-out packages, flexible circuits, and lead-free solder are becoming more prevalent. Have you seen a growth in the use of plasma to enable these technologies?
I think the driver behind each technology choice is different and plasma does enable this. The decision to go with lead-free solder is more of an environmental choice. By using this type of solder, you need adhesion promoters, as well as bleed eliminators.
Plasma makes this possible, but it would not be necessary if lead wasn’t a problem. I believe there has been an increased usage of plasma for flex and fan-out, but probably not at a significant level.
Most of the plasma integration points for fan-out and flex are similar to the integration points for traditional wafer packaging and PCB manufacturing, respectively. The biggest change is probably the form factor of the product.
Nordson MARCH is using plasma polymerization to uniformly deposit thin films to change the surface characteristics of a substrate. How is that a new use of plasma?
When thinking of traditional plasma treatment, cleaning, and/or etching, plasma deposition uses a gas vapor, or heated liquid monomer vapor delivery system, along with RF plasma energy exposure to cause polymerization. This results in coatings that can reduce and in certain cases eliminate tackiness, provide a tie layer, which acts as an enhancement or inhibition agent in applications, and can change desired surfaces from hydrophobic to hydrophilic, or vice versa.
What are the benefits and implications of using Plasma Polymerization to uniformly deposit thin films to change the surface characteristics of a substrate?
Plasma processing for polymer deposition has numerous benefits for applications for medical devices, electronics, elastomers, and many more industries. Deposition is used to apply thin films uniformly to substrates that render a specific uniquely desirable surface characteristic across a broad range of end-use products not naturally occurring in the virgin substrate’s physical behavior.
Plasma polymerization (or glow discharge polymerization) uses plasma sources to generate a gas discharge that provides energy to activate or fragment gaseous or liquid monomer, often containing a vinyl group, in order to initiate polymerization. Polymers formed from this technique are generally highly branched and highly cross-linked, and adhere to solid surfaces well.
The biggest advantage to this process is that polymers can be directly attached to a desired surface while the chains are growing, which reduces steps necessary for other coating processes such as grafting. This is very useful for pinhole-free coatings of a few nanometers to many micrometers thickness with solvent insoluble polymers.
Plasma deposited polymers can exhibit similar properties to those created via standard chemical polymerization techniques. Proper control of plasma parameters can maintain the characteristics of the monomer resulting in films with desired functional properties. Functional groups, such as amines or carboxyls, can be very useful when grafting films subsequently onto or as a biologically compatible surface. Plasma polymers are useful to eliminate tack from elastomers and can be used to change surfaces from hydrophobic to hydrophilic or vice versa. Plasma polymers are quite useful as barrier layers when deposited onto other polymers.
As plasma polymers are deposited directly from the monomer, there are no waste streams due to wet chemical synthesis or solvents. Plasma deposition allows for precise control of the film thickness.
.jpg)
Figure 1. Plasma processing for polymer deposition has numerous benefits for applications for medical devices, electronics, elastomers, and many more industries. Nordson MARCH offers a range of plasma treatment systems to fit the requirements of the process.
Plasma deposition can be used for applications in a wide range of industries, such as medical, life sciences, industrial, semiconductor, MEMS, plastics, and electronics. Can you give us some examples of how plasma polymerization is being used?
Plasma processing for polymer deposition does have numerous benefits for applications in the medical device, electronics, elastomers, and many more industries.
Examples of plasma polymer deposition applications:
Catheters - Plasma deposition of polymers using an allyl amine monomer to a medical catheter creates a tie layer for application of a lubricious coating that can withstand the rigors of multiple cycles without losing their lubricious properties.
Rubber, Elastomeric, and Silicone Materials - Plasma deposition of materials to surfaces that are traditionally sticky or tacky by nature can be made smooth and slippery (lubricious). This is commonly required for medical devices that use silicone rubbers, so they do not adhere to each other, another material, or even the patient. It is also useful to reduce the stickiness of o-rings and other seals used in industrial applications, where they cannot allow components to stick to each other. Using some sort of siloxane liquid as the precursor to act as the monomer for polymerization and deposition enables enhanced performance in end uses such as reduced insertion forces, lower friction forces, enhanced singulation, and separation in handling.
Intraluminal Deposition - Plasma Deposition within a tubular structure can be accomplished via the utilization of Nordson MARCH’s Patented Intraluminal Deposition Technology. By placing tubes within a hollow cathode, the plasma is sustained and can allow for material deposition to the ID of a tubular structure. By precisely managing the process pressure and RF frequency and duration cycle, various tube diameters and lengths can achieve reactant diffusion. Nordson MARCH’s application-specific gas manifold design is utilized to optimize the deposition uniformity desired.
.jpg)
.jpg)
Figures 2 and 3. Plasma deposition inside a tubular structure can be accomplished by placing tubes inside a hollow cathode, utilizing Nordson MARCH’s Patented Intraluminal Deposition Technology.
.jpg)
Figure 4. The plasma is sustained and can allow for material deposition to the inside of a tubular structure. By precisely managing the plasma process, various tube diameters and lengths can achieve reactant diffusion inside the tubular structure.
Electronics and Surface Protection - Plasma polymer deposition is also useful for the deposition of hydrophobic films. These films can be useful as coating on electronics to prevent moisture penetration, as well as barriers to prevent liquid flowing into undesired areas. In addition, plasma can apply precise and thin coatings for anti-microbial, anti-thrombogenic, and corrosion-resistant surfaces.
What do you foresee in the future for plasma coating and treatment?
In addition to traditional plasma treatment applications for cleaning and etching, this exciting plasma deposition coating technology lends itself to providing users with alternatives to traditional coating techniques for Life Critical, Mission Critical and Personal Safety and Security applications.
Where can our readers go to find out more?
To learm more visit our Applications Content page at www.NordsonMARCH.com
About David Selestak
Dave has been with Nordson Corporation since 1980. His current responsibilities for Nordson ASYMTEK and Nordson MARCH are to develop business opportunities that involve technologies from both businesses, such as conformal coating and plasma treatment.
In previous positions within Nordson, Dave has worked in direct sales for both ASYMTEK and MARCH, and for several other Nordson product lines in several technology and manufacturing industries. He has a BS in Accounting/Finance from Baldwin-Wallace University, Berea, Ohio.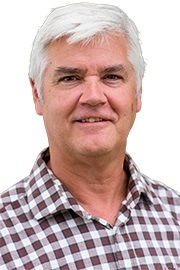
Disclaimer: The views expressed here are those of the interviewee and do not necessarily represent the views of AZoM.com Limited (T/A) AZoNetwork, the owner and operator of this website. This disclaimer forms part of the Terms and Conditions of use of this website.