Nanotechnology, which revolutionizes industries such as semiconductor technology, materials science, pigments, food, and pharmaceutics, is one of the most innovative developments today. It deals with particles ranging from 1 to 100 nm. These particles have special properties because of their size, as their surface is very much enlarged in relation to their volume, the so-called “size-induced functionalities”. For instance, ultrafine particles are harder and more break-resistant compared to larger particles. Nanotechnology brings effects that occur in nature to a commercial level, such as, for instance, the lotus effect: nanocoated fabrics or paints are dirt- and water-repellent just like the lotus flower.
Application examples for the use of nanoparticles
Industry |
Application |
Alternative Fuels |
Improved cleaning of solar cells |
Automobile |
Densification of tyre material, improved color properties of paint |
Cosmetics |
Protection against UV radiation |
Textiles |
Protection against water or dirt (lotus effect) |
Medicine |
Controlled release of drugs, for example in tumor cells |
Food |
Non-stick coating of food packaging |
Sports |
Reinforcing materials, for example for tennis rackets |
How are nanoparticles generated? The “Bottom-Up” technique synthesizes particles from molecules or atoms. The “Top-Down” technique involves reducing the size of larger particles to nanoscale, for instance, with laboratory mills. Small particles are attracted to each other by their electrostatic charges because of their significantly expanded surface in relation to the volume. Nanoparticles are generated by colloidal grinding which involves dispersion of the particles in liquid in order to neutralize the surface charges. Depending on the sample material, both alcohol and water can be used as dispersion medium. In some cases, the neutralization of surface charges can be achieved through the addition of a buffer such as sodium phosphate or molecules with long, uncharged tails such as diaminopimelic acid (steric or electrostatic stabilization).
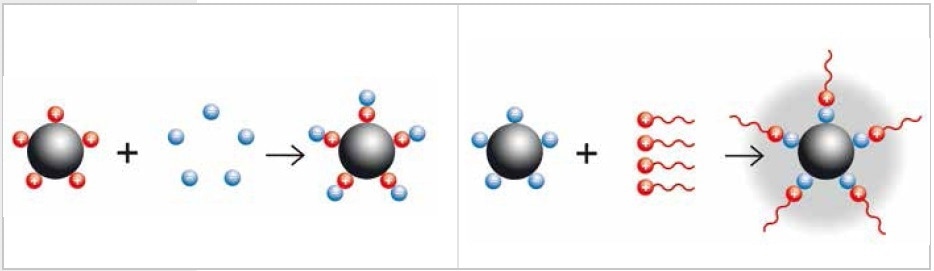
Figure 1. Neutralization of charged particles by adding a buffer (electrostatic stabilization, left) or by adding long-chained molecules (steric stabilization, right)
Several factors, including size reduction principle and energy input make ball mills the best option for the production of nanoparticles. The most important factors for choosing a mill and suitable accessories are:
- Material of the grinding tools
- Grinding balls/sample/dispersant ratio
- Grinding ball size
- Grinding time
- Energy input
Top-Down Method: Production of Nanoparticles with Ball Mills
Nanoparticles are produced with the Top-Down method by colloidal grinding employing a suitable dispersant in order to keep the particles from agglomerating. A high energy input is needed to reduce small particles with mechanical force to smaller sizes. The selection of the correct grinding jar filling and suitable grinding tools are other factors that need to be considered.
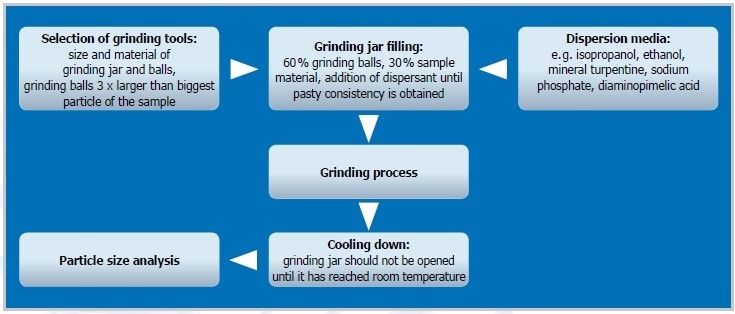
Figure 2. The steps of colloidal grinding
Preliminary Grinding
An initial size reduction step can be useful depending on the size of the original sample material and desired final fineness. A dry grinding method with grinding balls of >3 mm Ø is generally performed by filling one third of the jar with sample material and one third with grinding balls. The homogenized sample is then employed for the actual colloidal process.
Colloidal Grinding
With its planetary ball mills and the novel high-energy ball mill Emax, RETSCH provides two types of ball mills that offer the energy input necessary for colloidal grinding down to the nanometer range. Grinding balls and jars made up of an abrasion-resistant material such as zirconium oxide are well-suited for this kind of application. Here, 60% of the grinding jar level is filled with grinding balls ranging from 0.5 to 3 mm Ø, offering many frictional points. The actual sample fills about one third of the jar volume. The consistency of the sample should become pasty by adding an appropriate dispersant (e. g. buffer, isopropanol, or water), providing perfect conditions for colloidal grinding. If an extremely high final fineness is needed, it is advisable to continue with a second colloidal grinding step with grinding balls ranging from 0.1 to 0.5 mm Ø, particularly if 2 to 3 mm balls were employed in the initial process (the balls need to be 3 x bigger compared to the particle size of the initial material). In order to separate the sample from the grinding balls, both are placed on a sieve (with aperture sizes 20-50% smaller than the balls) with a collecting pan. 60% of the jar is filled with small beads for the subsequent colloidal grinding. The suspension from the earlier grinding is carefully mixed with the grinding beads until a pasty consistency is achieved.
Consistency
During grinding, some materials tend to become very pasty, preventing the grinding balls from moving around in the suspension and thus making additional size reduction almost impossible. So, during the grinding process, it is recommended to check the consistency of unknown sample materials. If required, the sample/ball mixture can be diluted further by adding more dispersant. If a sample swells easily, the sample/dispersant ratio must be adapted accordingly. The addition of surfactant to stabilize the consistency is another option.
Removal of Grinding Jar
The grinding jar should be removed carefully as it may have a temperature of up to 150 °C, owing to the heat produced during the grinding process. Furthermore, pressure increases inside the grinding jar. Hence, it is recommended to use the optional safety closure for the “comfort” grinding jars used with RETSCH’s planetary ball mills to ensure safe handling. After the grinding process, the jar must cool down for a while. The Emax jar is equipped with an integrated safety closure. Furthermore, the mill’s effective cooling system prevents the jars from heating too much. Both jar types are provided with optional aeration covers for working under inert atmosphere.
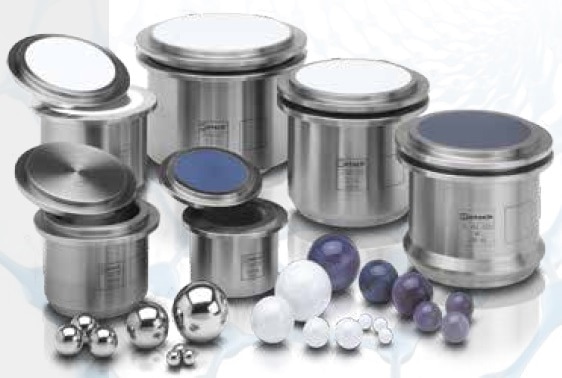
Suitable Ball Mills for the Production of Nanoparticles
With the high energy ball mill Emax and the planetary ball mills, RETSCH provides suitable mills for the production of nano particles and also has the required expertise.
Planetary Ball Mills
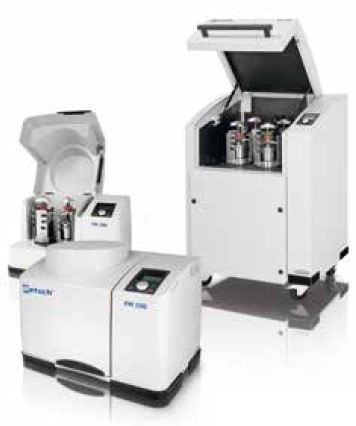
Figure 3. Planetary ball mills from RETSCH
Each grinding jar in the planetary ball mill represents a “planet”. This planet is placed on a circular platform, the so-called sun wheel. When the sun wheel rotates, every grinding jar turns around its own axis, but in the opposite direction. As a result, centrifugal and Coriolis forces are activated, causing rapid acceleration of the grinding balls (Figure 4). The outcome is very high pulverization energy that allows for the generation of very fine particles. The massive acceleration of the grinding balls from one wall of the jar to the other creates a strong impact effect on the sample material and causes additional grinding effects through friction. The ratio between the speed of the sun wheel and the speed of the grinding jar is 1:-2 for colloidal grinding and many other applications. This means that when the sun wheel rotates once, the grinding jars rotate twice in the opposite direction.
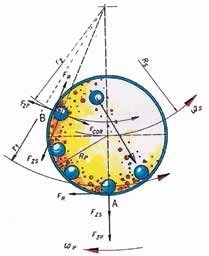
Figure 4. In the planetary ball mill, centrifugal and Coriolis forces permit grindings down to the submicron range.
The result of grinding of alumina (Al2O3) at 650 min-1 in the PM 100 is shown in Figure 5. The mean value of the particle size distribution is 200 nm after 1 hour of size reduction in water with 1 mm grinding balls; it is 100 nm after 4 hours. In a further test, the material was initially ground for 1 hour with 1 mm grinding balls and after that for 3 hours with 0.1 mm grinding balls (Figure 6). In this case, an average value of 76 nm was obtained. As demonstrated with these grinding results, the planetary ball mills can generate particle sizes in the nanometer range.
Colloidal grinding of aluminum oxide in the PM 100
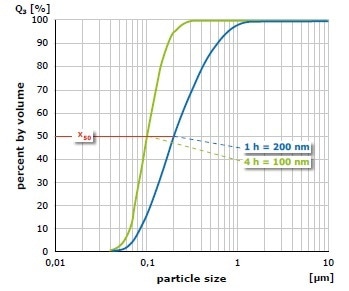
Figure 5. Grinding of alumina in water with 1 mm grinding balls (left) after 1 hour (blue) and after 4 hours (green)
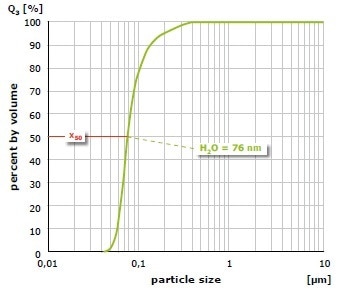
Figure 6. Grinding of alumina with a 1 mm grinding ball (1 hour) and then with 0.1 mm balls (3 hours) in water
High Energy Ball Mill Emax
The Emax is a new kind of ball mill designed specifically for high energy milling. The impressive speed of 2,000 min-1, thus far unrivaled in a ball mill, together with the special grinding jar design produces a huge amount of size reduction energy. The unique combination of friction, impact, and circulating grinding jar movement produces ultrafine particle sizes in a very short amount of time. Thanks to the novel liquid cooling system, excess thermal energy is rapidly discharged, thus preventing the sample from overheating, even after long grinding times.
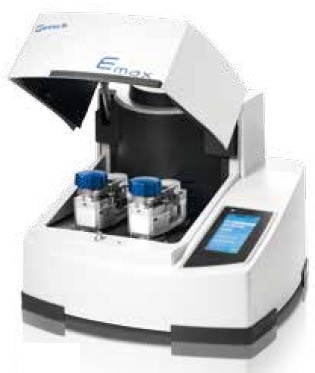
Figure 7. Emax
Functional Principle
The new size reduction mechanism of the Emax is characterized by intensive friction and high-frequency impact, resulting in unequaled grinding performance. This unique combination is produced by the oval shape and the movement of the grinding jars which do not turn around their own axis as seen in the case of planetary ball mills. The interaction of jar geometry and movement produces strong friction between jar walls, sample material, grinding balls, and rapid acceleration which allows the balls to impact with large force on the sample at the rounded corners of the jars. This considerably enhances the mixing of particles, resulting in a narrower particle size distribution and smaller grind sizes than obtained in traditional ball mills.
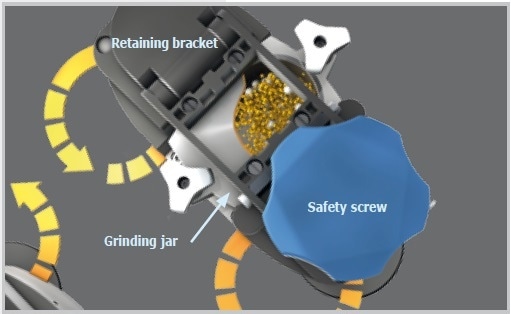
Figure 8. Functional principle Emax
The grinding energy ensuing from the friction of a large amount of small grinding balls is enhanced even more in the Emax by the high speed of 2,000 min-1. As the unique liquid cooling system rapidly discharges the frictional heat, the high energy input is fully exploited for the grinding process. Both sample and mill would overheat without effective cooling. Based on the grinding mode and the sample characteristics, cooling breaks of approximately 60% of the total grinding time are suggested for traditional planetary ball mills to prevent overheating. On the other hand, the Emax is suitable for continuous grinding without breaks, thanks to its effective liquid cooling system.
In a comparative test, the pigment titanium dioxide was pulverized in the Emax (50 ml grinding jar of zircomium oxide, 110 g matching grinding balls 0.1 mm Ø, 10 g sample, 15 ml 1 % sodium phosphate) and in the most powerful planetary ball mill. The d90 value of the Emax sample was 87 nm after 30 minutes. The planetary ball mill accomplished a grind size of only 476 nm after this time (excluding cooling breaks). As a result, the Emax provided a 5 times higher final fineness compared to the planetary ball mill (Figure 9).
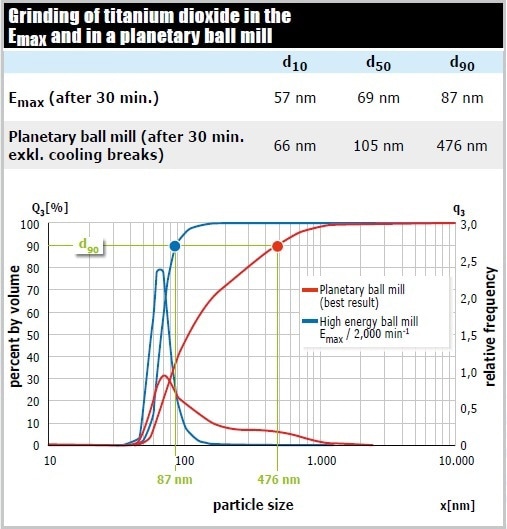
Figure 9. The Emax pulverizes the sample not only faster and to a finer size, it also produces a significantly narrower particle size distribution
Figure 10 displays the outcome of grinding graphite in the Emax at 2,000 min-1 (50 ml grinding jar of zirconium oxide, 110 g matching grinding balls 0.1 mm Ø, 5 g sample, 13 ml isopropanol) and in the most powerful planetary ball mill. Since graphite is a lubricant, it needs a particularly high energy input for size reduction. 90% of the Emax sample showed a fineness of 13 microns after just 1 hour of grinding, whereas the planetary ball mill achieved this grind size only after 8 hours of grinding (excluding cooling breaks). Regarding the final fineness obtained in the Emax after 8 hours of grinding, its excellent performance again becomes obvious: With a d90 value of 1.7 µm, the grind size is 7 times finer than the one obtained in the planetary ball mill (12.6 µm).
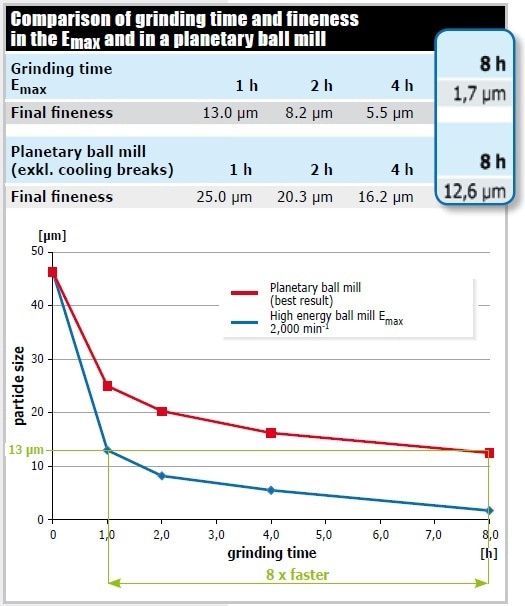
Figure 10. Pulverization of graphite. The water-cooled Emax is highly superior to the planetary ball mill without cooling system both in speed and achieved final fineness.
Highly Efficient Liquid Cooling
An integrated water cooling system cools the grinding jars of the Emax. The mill can be connected to the tap or a heat exchanger to further reduce the temperature. The cooling circuit of the Emax is shown in Figure 11. The grinding jars are cooled through the jar. The cooling system is extremely effective because heat is discharged more easily into water than into air. The Emax software enables users to perform the grinding process within a defined temperature range, that is, they can fix a minimum and a maximum temperature. The mill automatically stops when the maximum temperature is exceeded, and it starts again after reaching the minimum temperature.
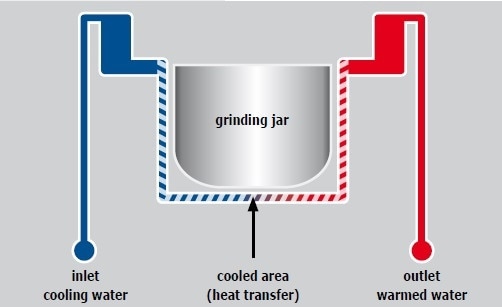
Figure 11. The grinding jar is cooled via the jar brackets.
Conclusion
For many years, nanoparticles (i. e., particles with a diameter of < 100 nm) have been the object of scientific research. There are different techniques to generate nanoparticles. The “Top-Down” technique involves size reduction of very large particles to the nanometer range. The best results are obtained using ball mills which provide the necessary energy input. Besides the planetary ball mills, including PM 100, PM 200 and PM 400, the new high energy ball mill Emax is particularly suitable for colloidal grindings down to the nanometer range due to the high energy input and innovative water cooling system.
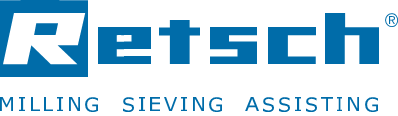
This information has been sourced, reviewed and adapted from materials provided by RETSCH GmbH.
For more information on this source, please visit RETSCH GmbH.