In this article, the use of exceptional repeatability and rapid response times of on-line FT-NIR and other analyzers for offering complete real-time data for the optimization of naphtha steam-cracking furnaces has been discussed.
.jpg)
Refinery. Image Credit: ABB Ltd.
Firstly, it is essential to look at the background: why is real-time optimization of the steam-cracking furnace so essential, and what are the analytical tools available to help?
Ethylene production runs at nearly 175 M tons per year, the extensive mass of which is produced by steam-cracking light hydrocarbons — ethane where it is inexpensively and easily available, liquid feeds like naphtha or, less commonly, gas oil where it is more beneficial. The use of naphtha as a feedstock has important extra benefits where the end-user market is dynamic with respect to pricing and demand, as naphtha feedstocks also generate additional-value co-products such as butenes (for butadiene production), propylene, and a high aromatics content pygas product. This enables the operation of steam-cracker in campaign mode, the better to tune product spectrum to market opportunity.
Process Optimization
The steam-cracking process involves several stages such as, mainly, the cracking furnace, quench, downstream compression, and purification/recovery. The feed to the cracking furnace is pre-heated and mixed with steam at a controlled charge rate and steam-to-hydrocarbon ratio, and then passed quickly through the radiant section of the furnace. The cracking temperature is high (approximately 1382 °F to 1562 °F/750 °C to 850 °C) and the residence time is very short (of the order of 0.08 to 0.25 seconds). This produces a huge mass of cracked effluent gas consisting mainly of propylene and ethylene, but with other co-products as signified above.
This high-temperature gas flow passes primarily through transfer-line heat exchangers and through a main quench tower to instantaneously stop further reaction and prevent the formation of side-products. Eventually, the gas flow passes through a multi-stage compressor train and then to the cold section of steam-cracking unit for recovery, separation, and purification.
The crucial point is that the total profitability and efficiency of the steam-cracking unit is determined by the quality and yield of the furnace effluent gas. The downstream stages make the best of what has been produced, but cannot impact the furnace itself.
The crucial problem in furnace operation is to balance cracking extremity against throughput, ethylene/propylene selectivity, and yield, all of which can influence the gas-make, the capacity of the downstream separation and compression train, and the threat of unacceptable furnace tube coking. The perfect furnace set-point (for instance, measured as the coil outlet temperature [COT]) will be, among other factors, crucially dependent upon the composition of the liquid naphtha feed. Relatively light paraffinic naphtha will crack more readily and yield a higher volume of gas without the risk of furnace coking — consequently enabling a higher severity yield and setting, up to the limit of the downstream compressor train. A more aromatic naphtha at the same severity would intensely decrease furnace run-lengths by extreme coking.
.jpg)
The cracking, quenching, compression, and recovery stages of a steam-cracking unit. Image Credit: ABB Ltd.
Maintaining Ethylene Yield% Using Severity-Based Control Versus Operation at Constant COT for Variable Feed Quality
Measurement at a certain level is fundamental to process optimization. Measurement yields information, which enables the feasibility of control. The form taken by this measurement is a negligibly more open question, and one subject to great debate between those who dislike analyzers and like statistics (engineers mainly) , and those who do not believe anything which is not a directly traceable analytical result (chemists mainly).
.jpg)
The cycle of measurement and optimization. Image Credit: ABB Ltd.
.jpg)
Furnace severity control using dynamic COT set-point with feed composition and effluent analysis. Image Credit: ABB Ltd.
This results in several approaches to APC:
APC based on inferential models
- Usage of various basic mass-flow, temperature, and pressure transmitters
- Requires lab test data for calibrating and maintaining the inferential quality estimator
- Requires chemical engineering model of unit
APC based on physical analyzers
- Usage of various single-property physical analyzers for direct measurement
- Requires considerable training, calibration, maintenance, and spares stockholding
APC based on advanced analyzers
- Usage of a lesser number of multi-stream multi-property analyzers
- Requires calibration or calibration model development
- Generally provides significant enhancement in precision, reliability, and speed
Real-Time Analysis of Naphtha Feed Composition
APC on the basis of real process stream quality measurements from real analyzers is superficially attractive yet fraught with risk.
Historically, this approach was hindered by:
- Large infrastructural requirements for installation
- High capital cost
- Complex operational needs (validation, calibration)
- High life-cycle costs, less reliability
Technical advances have led to:
- More powerful, simple, cost-effective analyzers
- Considerably reduced operational and installation demands
- Broader array of existing technologies
The low life-cycle costs and long maintenance intervals of Fourier-Transform Near IR (FT-NIR) analyzers have provided one way to handle a portion of the problem. Selected sensibly, they provide space-technology levels of reliability and uptime (quite literally because the technology is regularly employed in climate sensing satellites). Currently, on-line FT-NIR analyzers have a verified track record in consistent hydrocarbon stream property measurement over the entire range of petrochemical and refinery streams from crude distillation to heavy oil upgrading, naphtha conversion, and end-product blending.
In the current instance, on-line process FT-NIR analyzers provide an excellent match with the measurements needed for the monitoring of liquid naphtha feed real-time composition. On this application, they compare very well with process gas chromatographs which, for a complete PIONA analysis, are simply too slow for efficient APC update cycles in this fast-moving process. At the same time, GCs (or process mass spectrometers) are considerably appropriate for post-furnace gas effluent measurement. Both effluent gas composition and feed quality are essential inputs for the furnace RTO for a steam-cracker with variable naphtha feed quality, or using a recycle of C4+ back into the furnace feed.
The key compositional measurement necessary for the determination of feed naphtha quality is PIONA (percentage of total paraffins, iso-paraffins, olefins, naphthenes, and aromatics). This information is offered to a portion of the APC system that acts as an entire yield predictor and furnace simulation. This will usually estimate, for a given extremity, ethylene/propylene yield, coking index, the total gas-make, or analogously defined parameters. Depending on the specific setup, the yield estimator and furnace simulator may need input data as a simpler reduced data set (for instance, PIONA and main distillation parameters like T05, T95), or it may need a complete C-number-based breakdown of the entire hydrocarbon composition. Process FT-NIR analyzers are capable of meeting both of these requirements efficiently. The correct selection of analyzer platform can be chosen for achieving this in an optimal fashion.
In this article, both analyzer platforms signified are Ex zone certified, field-mountable process FT-NIR systems. The main dissimilarity is that the TALYS ASP400-Ex unit is a very concise, single-channel fiber-optic-based system perfectly suited to PIONA measurement with very easy installation requirements, while the HP360 unit is an extractive system with an embedded analysis sample flow-cell. This last arrangement does not require the use of fiber-optics and is capable of delivering a very exact full C-number breakdown of the naphtha feed composition when required by the furnace yield simulator.
.jpg)
ABB process FT-NIR analyzer TALYS ASP400-Ex. Image Credit: ABB Ltd.
.jpg)
ABB process FT-NIR analyzer FTPA2000-HP360. Image Credit: ABB Ltd.
Typical naphtha feed qualities provided by TALYS ASP400-Ex FT-NIR analyzer
Example Naphtha feed calibration data |
Property |
FTIR R |
FTIR r |
Range vol% |
Property |
FTIR R |
FTIR r |
Range (°C) |
P% |
0.74 |
0.14 |
18 - 53 |
IBP |
2.1 |
0.26 |
21 to 105 |
I% |
0.98 |
0.11 |
20 - 55 |
T10 |
1.2 |
0.17 |
35 to 81 |
O%(hi) |
0.17 |
0.03 |
0 - 12 |
T30 |
1.7 |
0.16 |
44 to 93 |
O%(lo) |
0.08 |
0.03 |
0 - 1.6 |
T50 |
2.4 |
0.2 |
50 to 125 |
N% |
0.83 |
0.13 |
8 - 40 |
T70 |
3.3 |
0.31 |
54 to 143 |
A%(lo) |
0.26 |
0.08 |
1 - 15 |
T90 |
4.9 |
0.32 |
67 to 165 |
A%(hi) |
0.57 |
0.08 |
0 - 35 |
T95 |
7.7 |
0.48 |
69 to 185 |
C4 Total |
0.17 |
0.09 |
1 - 6 |
FBP |
10.9 |
0.73 |
76 to 225 |
Measurements are made in the 4000 to 4800 cm-1 range of the NIR Combination Region for the FTPA2000-HP360 analyzer system. This enables precise isomer discrimination, and therefore a reliable carbon-number based breakdown of naphtha components.
.jpg)
PLS Regression calibration plots for PIONA in Naphtha feed typical naphtha feed qualities provided by TALYS ASP400-Ex FT-NIR analyzer. Image Credit: ABB Ltd.
For instance, illustrated above are the spectra of various C6 isomers. The plot on the left demonstrates spectra of the individual compounds, which is observed to be evidently differentiated in the shape, position, and intensity of Near-IR Combination Region absorbance bands. The plot on the right demonstrates instances of gravimetrically prepared mixtures of the pure compounds. This matches relatively well with a usual naphtha-type hydrocarbon spectrum.
.jpg)
FT-NIR spectra of 2,3 dimethylbutane, 2-methylpentane, 3-methylpentane, and n-hexane methyl-cyclopentane. Image Credit: ABB Ltd.
.jpg)
FT-NIR spectra of analyzed samples for calibration set. Image Credit: ABB Ltd.
Detailed Analysis by C-Number
FT-NIR spectra in the NIR combination region 4000 to 4800 cm-1 for a range of C6 hydrocarbons and the related calibration plots demonstrate near-perfect analysis of the various C6 isomer compositions.
For this application, the use of Fourier-transform-based Near-IR analyzer platforms enables selection among a broad array of potential Near-IR spectral regions as it is an intrinsic feature of this technology that it covers the whole near-infrared range from 3700 cm-1 to more than 12,000 cm-1 without compromising the signal-to-noise ratio or resolution. Therefore, the TALYS ASP400-Ex is suitable for standard applications requiring PIONA feed to the yield estimator and furnace RTO, and the HP360 when complete C-number analysis is required (for instance, in an entire SPYROTM implementation).
.jpg)
Calibration plots for 2-methylpentane, methylcyclopentane, and 3-methylpentane by FT-NIR analysis. Image Credit: ABB Ltd.
.jpg)
ABB Process FT-NIR analyzer TALYS ASP400-Ex with fiber-optic link to sample flow cell cabinet. Image Credit: ABB Ltd.
.jpg)
ABB Process FT-NIR Analyzer FTPA2000-HP360 with fastloop sample conditioning system. Image Credit: ABB Ltd.
Conclusion
This article has examined the application of powerful on-line process FT-NIR analyzer technologies for the real-time analysis of liquid naphtha feed to steam-cracking units employed for universal scale production of propylene and ethylene. It is observed that different implementations of FT-NIR technology can be chosen as the application needs partial or complete feed quality characterization as feed-forward information to the cracking furnace yield estimator and real-time optimizer.
Properties including distillation, a complete C- number breakdown, and PIONA are available with an analysis cycle time of below 1 minute, comparing very well with alternative technologies. Other on-line analyzer technologies available within ABB Measurement & Analytics with equivalent application in ethylene units include process PGC5000 gas chromatographs for furnace effluent characterization and the LGR-ICOS off-axis tunable diode laser system for ultra-low-level acetylene and ammonia detection in the end product purified ethylene.
.jpg)
Calibration plots showing PIONA analysis by C-number for FTPA2000-HP360 system. Image Credit: ABB Ltd.
References
- Chambers, L.E.; Potter, W.S.; “Ethylene Furnace Design: Part One,” Hydrocarbon Processing, p. 121, January 1974.
- K. Keyvanloo, K.; Towfighi, J.; Sadrameli, S.M.; Mohamadalizadeh, A.; “Investigating the effect of key factors, their interactions and optimization of naphtha steam cracking by statistical design of experiments,” J. Anal. Appl. Pyrolysis 87, 224–230, 2010.
- Wysiekierski, A.G.; Fisher, G.; Schillmoller, C.M.; “Control coking for olefins plant,” Hydrocarbon Processing, p. 97, January 1999.
- Tecnip Engineering Solutions Briefing Note: “Steam Cracking for Ethylene Production,” Paris, 2008.
- ABB Application Note, “Model Based Severity Control for Olefins Plants,” PA Division, Oil Gas & Petrochemicals, 2011.
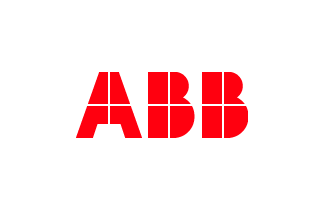
This information has been sourced, reviewed and adapted from materials provided by ABB Measurement & Analytics - Analytical Measurement Products.
For more information on this source, please visit ABB Measurement & Analytics - Analytical Measurement Products.