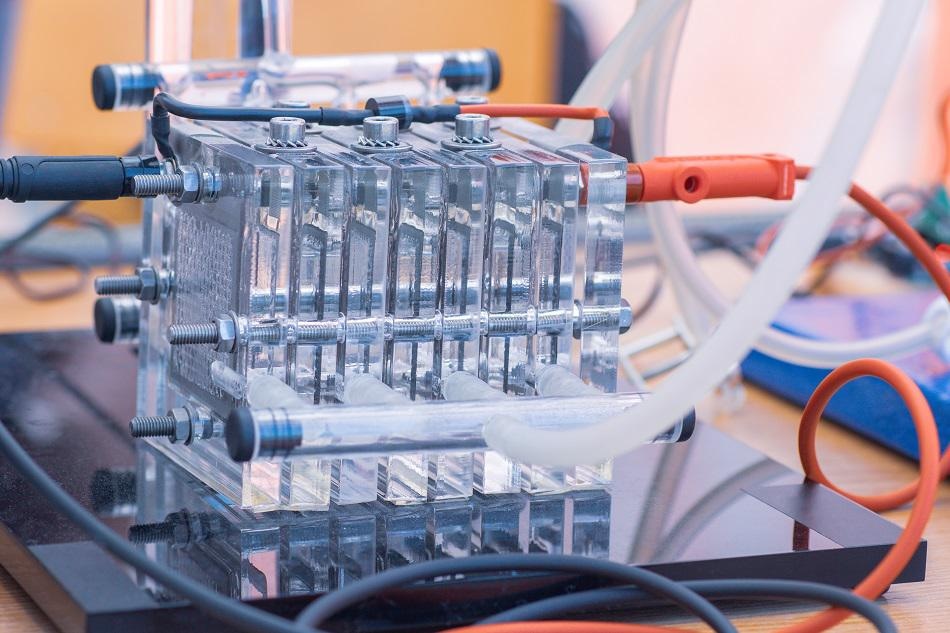
Image Credit: Kaca Skokanova/Shutterstock.com
Polymer electrolyte membrane fuel cells (PEFMCs), otherwise known as proton-exchange membrane fuel cells, have great potential for use as an energy-dense, efficient and portable power source. Fuel cell systems could be made a practical alternative to internal combustion engines running on non-renewable hydrocarbon fuel through the generation of hydrogen fuel.
Hot-pressing methods can produce PEMFCs that are demonstrably sensitive to temperature, pressure, and press-time during the manufacturing process. The range of precision-heated platens and laboratory hydraulic presses offered by Specac provide an affordable and compact solution for accurately controlling these parameters for optimal fuel cell performance.
With depleting global fossil fuel reserves, there is a pressing need for research into alternative fuels. Chemical fuels are relied upon by global power infrastructure for their energy density, ease of use, and, in the meantime, abundance. The transport sector, in particular, accounts for around 25% of global power consumption.1 The only way to meet future energy demands is to develop alternative fuel sources.
One promising alternative to petroleum-derived fueled combustion engines is fuel cells that run on hydrogen. Hydrogen is commonly produced through electrolysis of water (producing hydrogen and oxygen), and this requires an external power source.
Using renewable energy sources such as solar or wind to power hydrogen production has the potential to make hydrogen fuel cells an incredibly energy-dense and efficient store of completely renewable energy. Carbon oxide emissions would be removed from the equation of energy production entirely with an energy infrastructure based on hydrogen fuel cells. This would only emit water and water would be the primary precursor to fuel.
Proton-exchange membrane fuel cells (PEMFCs) show particular promise and offer several advantages.2 A membrane electrode assembly (MEA) is at the core of a PEMFC and contains an electrolytic polymer membrane that can conduct protons but, most importantly, not electrons.
The splitting of hydrogen into protons and electrons at the anode is facilitated using catalysts. The resulting protons are conducted through the polymer membrane – usually Nafion – to the cathode. At the same time, electrons are conducted through an external circuit to supply power (for example, an electric motor in a vehicle). Water is produced when electrons and protons recombine with protons and oxygen at the cathode.
In comparison to other fuel cell architectures, PEMFCs have a very short start-up time – usually a few seconds. They also work at much lower temperatures than most other fuel cell types, usually below 120 °C.3 PEMFCs are ideal for application in vehicles due to these two features.
Automobiles, buses, backup power systems and larger-scale power generation have all applied PEMFCs. However, widespread adoption is prevented due to issues with cost and deterioration.4,5,6,7 Research is on-going to optimize the performance of PEMFCs, with the end goal to produce a fuel source capable of replacing the internal combustion engine with a carbon-free renewable energy source.
Optimizing Proton Exchange Membrane Efficiency
The primary functional component in a fuel cell is the MEA. It is made up of a proton exchange membrane, catalyst layers, and gas diffusion layers (GDL). A hot press method is commonly used to assemble them and involves spreading a thin film of catalyst over either the GDL or the membrane. The two layers are then sandwiched together in a heated hydraulic press.
Researchers have isolated several ways in which the performance of PEMFCs can be affected by the manufacturing conditions of the membrane electrode assembly (MEA).8 It has been shown that the performance of the fuel cell is influenced by several factors, including temperature, pressure and time of press.
The IV characteristics and maximum power output of PEMFCs are all sensitive to these factors. The temperature used during manufacturing is particularly influential on the maximum power output. Researchers from the University of The Basque Country discovered that the maximum power output of a fuel cell nearly doubled with a change of just 10 °C during hot pressing.
In the construction of effective PEMFCs via hot pressing, it is evident that fine control over temperature, pressure and press time is critical. The range of benchtop hydraulic presses and heated platens from Specac provide a compact solution to tightly controlled hot-press manufacture of fuel cell MEAs.9,10
Specac hydraulic presses can be fitted with heated platens in order to press membrane materials at temperatures up to 300 °C and at loads up to 15 tonnes. Digital temperature controls are incorporated in Specac’s heated platens, providing exceptional temperature control, with stability of ±1 °C. Platens can be easily installed into Specac hydraulic presses. They feature water-cooling of the connecting blocks to isolate the press from any heating effects and enable efficient heating and cooling of the platens.
References and Further Reading
- International Energy Outlook 2016 | U.S. Energy Information Administration. Available at: https://web.archive.org/web/20170727110053/https://www.eia.gov/outlooks/ieo/pdf/0484(2016).pdf. (Accessed: 8th March 2019)
- Peighambardoust, S. J., Rowshanzamir, S. & Amjadi, M. Review of the proton exchange membranes for fuel cell applications. Int. J. Hydrogen Energy 35, 9349–9384 (2010).
- Reguera, G. et al. Biofilm and Nanowire Production Leads to Increased Current in Geobacter sulfurreducens Fuel Cells. Appl. Environ. Microbiol. 72, 7345–7348 (2006).
- AC Transit orders 4 more UTC Power fuel cell systems for public transport buses in California | News Center | News | United Technologies.
- Craven, W. B. Common Fuel Cell Project. 23, (2013).
- PEMFC Lifetime and Durability an overview.
- Stationary | Nedstack. Available at: http://www.nedstack.com. (Accessed: 15th March 2019)
- Barrio, A., Parrondo, J., Lombraña, J. I., Uresandi, M. & Mijangos, F. Influence of Manufacturing Parameters on MEA and PEMFC Performance. Int. J. Chem. React. Eng. 6, (2008).
- Hydraulic Press | Laboratory Presses - Specac. Available at: https://www.specac.com/en/products/sample-preparation/hydraulic-press. (Accessed: 18th March 2019)
- Heated Platens | Electrically Heated - Specac. Available at: https://www.specac.com/en/products/sample-prep/platens/electric/platens. (Accessed: 18th March 2019)
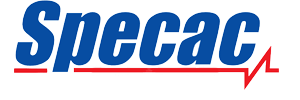
This information has been sourced, reviewed and adapted from materials provided by Specac Ltd.
For more information on this source, please visit Specac Ltd.